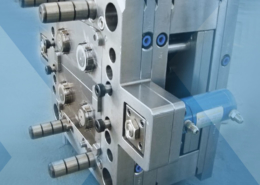
Creating a Realistic Plastic Prototype - plastic prototype manufacturing
Author:gly Date: 2024-10-15
● Melting temperature: 260 ~ 290 ℃. The products modified by glass are 275 ~ 280 ℃. Melting temperature should be avoided higher than 300 ℃.
Nylon 66 should be used if a high performing engineering plastic is required that will be exposed to higher temperatures. Additionally, its stiffness and good tensile and flexural modulus make it an ideal material for applications that need repeated long-term performance
Many industries use injection molding to produce their parts and products. The process enables them to create components of various shapes and sizes in high quantities (i.e., thousands or millions of pieces) quickly, consistently, and cost-effectively. While it can be used with a variety of other materials (e.g., glass, metal, and rubber), it is most commonly utilized for plastic. For example, clear plastic is often injection molded to form personal protective equipment (PPE), such as face shields and goggles, for industry professionals.
The plastic injection molding process involves heating plastic (in pellet or grain form) until it has melted. The molten material is then injected into a closed two-part mold under high pressure, where it cools and solidifies. Once the material has fully hardened, it maintains the shape of the mold cavity. At this point, the mold can be opened so the piece can be removed and sent for further processing as needed.
● Drying treatment: If the material is sealed before processing, then there is no need to dry. However, if the storage container is opened, drying in hot air at 85°C is recommended. If the humidity is higher than 0.2%, the vacuum drying at 105 ℃ for 12 hours is needed.
The following article provides an overview of plastic injection molding. It highlights what the process entails, key advantages of using it over other manufacturing methods, and challenges faced when conducting injection molding operations.
Nylon 66 (polyamide 6 or PA6) is a semi crystal crystal material. PA66 can also maintain strong strength and stiffness at higher temperature. PA66 is still hygroscopic after molding, the degree of which depends on the composition of the material, wall thickness and environmental conditions. In order to improve the mechanical properties of injection mold Nylon PA66, various modifiers are often added. Glass is the most common additive. Sometimes synthetic rubber is added to improve the impact resistance. PA66 is resistant to many solvents, but less resistant to acids and other Chlorinators.
● Runners and gates: Due to the short setting time of PA66, the gate position is very important. The hole diameter of the gate shall not be less than 0.5 * t. If a hot runner is used, the gate size should be smaller than using a conventional runner because the hot runner can help prevent premature solidification of the material. If a submerged gate is used, the minimum diameter of the gate shall be 0.75mm.
Nylon 6 (polyamide 6 or PA6) is a semitransparent polymer, which has excellent thermoplasticity and good chemical resistance and durability after modification. It is widely used in the manufacture of bearings, automobiles and tractors for various oil pipeline machinery and industrial equipment, such as zero fog material.
There are many benefits to using injection molding over other manufacturing methods to produce plastic components. For example:
The injection molding process can be used to produce parts and products for various industries. At Paulson Manufacturing, we leverage the technology to make high-quality, dependable safety equipment for industrial workers and fire responders. By carefully designing and building our own molds, we ensure we create solutions that surpass even the most rigorous safety standards. To learn more about injection molding in general or our capabilities, contact us today.
Nylon 6 should be used if a lightweight engineering plastic is required to withstand high impact and stress. It has better aesthetic appearance than Nylon 66 due to its lustrous finish and is easier to dye. It is an ideal choice for applications in the automotive, industrial and military industries. It is not ideal, however, for applications that are exposed to water at high temperatures due to its higher water absorption and lower heat deflection rate than Nylon 66, which would be a better choice.
● Mold temperature: 80 ℃. Mold temperature will affect the crystallinity, and crystallinity will affect the physical properties of the mold product. For thin-walled plastic injection mold parts, if the mold temperature is lower than 40 ℃, the crystallinity of the plastic parts will change with time. In order to maintain the geometric stability of the injection mold parts, annealing treatment is needed.
Nylon, usually referred to as “PA”, which is a synthetic thermoplastic polymer commonly used in injection molding applications. Nylon injection molding can be divided into PA6 and PA66. The chemical and physical properties of PA6 are very similar to PA66. PA6 has better impact resistance and solubility resistance than PA66, but its moisture absorption is also stronger. Then, what is the essential difference between PA6 and PA66 of Nylon injection molding? This article introduces the comparison of Nylon PA6 and PA66, covering features, advantages and all relevant properties of PA6 and PA66.
PA6 is a kind of material with good toughness, which is often used in climbing hands, automobile structural parts, etc. PA66 is a kind of material with toughness and hardness, which is used in industrial gears such as marine propellers.
● Runners and gates: Due to the short setting time of PA6, the gate position is very important. The hole diameter of the gate shall not be less than 0.5 * t. If a hot runner is used, the gate size should be smaller than using a conventional runner because the hot runner can help prevent premature solidification of the material. If a submerged gate is used, the minimum diameter of the gate shall be 0.75mm.
While injection molding offers a number of advantages over other manufacturing methods, it also comes with some challenges, such as:
● Drying treatment: Because PA6 is easy to absorb water, special attention should be paid to drying before processing. If the material is supplied in waterproof packaging, the container shall be kept closed. If the humidity is greater than 0.2%, it is recommended to dry in hot air above 80C for 16 hours. If the material has been exposed to air for more than 8 hours, it is recommended to dry it in vacuum at 105 ℃ for more than 8 hours.
● Mold temperature: 80 ~ 90 ℃. Mold temperature has a significant effect on the crystallinity, which in turn affects the mechanical properties of the plastic injection molded part. For structural parts, the crystallinity is very important, so it is recommended that the mold temperature is 80 ~ 90 ℃. For longer flow parts, higher mold temperature is also recommended. Increasing the mold temperature can improve the strength and rigidity of the plastic injection mold part, but reduce the toughness. If the wall thickness is more than 3mm, it is recommended to use a low-temperature mold of 20 ~ 40C. The mold temperature of glass reinforced material should be higher than 80 ℃.
GETTING A QUOTE WITH LK-MOULD IS FREE AND SIMPLE.
FIND MORE OF OUR SERVICES:
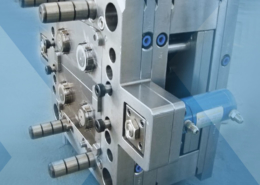
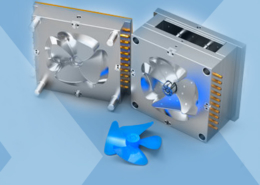
Plastic Molding

Rapid Prototyping
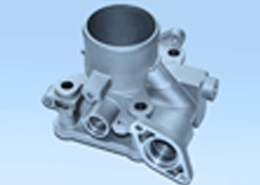
Pressure Die Casting
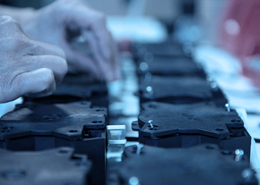
Parts Assembly
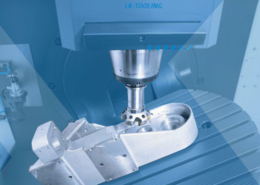