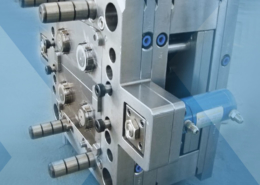
Components of an Injection Mold - injection molding tooling
Author:gly Date: 2024-10-15
Bioplastics represent a groundbreaking shift toward sustainability. Derived from renewable resources like corn starch, sugarcane, and even algae, these eco-friendly materials are rapidly gaining traction as viable alternatives to traditional plastics. Their adaptability and reduced environmental footprint make them a powerful ally in the fight against plastic pollution.
If you put a company on your watch list, we'll notify you on your email address when there are new publications regarding this company.
The future of sustainable manufacturing will be shaped by collaboration. By fostering partnerships between material suppliers, manufacturers, designers, and consumers, we can accelerate the adoption of bioplastics. This collective effort will drive innovation, lower costs, and increase demand for bioplastic products, ultimately reducing the environmental impact of manufacturing.
Despite these obstacles, the injection molding industry is rising to the challenge. This adaptable manufacturing process has proven its versatility by seamlessly integrating bioplastics into production lines. With just minor adjustments, such as fine-tuning temperatures, pressure settings, and mold designs, injection molding can efficiently produce high-quality bioplastic components.
The results are already visible in various applications: compostable packaging, disposable cutlery, and medical devices are just a few examples of products being efficiently produced using bioplastic injection molding. Advancements in molding technology, such as enhanced temperature control and innovative mold materials, further bolster the process, making bioplastic production more efficient and scalable.
In a world where over 300 million tons of plastic are produced annually, the environmental toll of plastic waste is impossible to ignore. This deluge of plastic waste is clogging our oceans, littering our landscapes, and threatening ecosystems worldwide. As awareness of these dire consequences grows, the urgency for sustainable manufacturing solutions has never been more pronounced.
Success stories abound, from eco-friendly packaging solutions to medical devices, all made possible through bioplastic injection molding. Ongoing innovations in molding technology continue to improve the compatibility and efficiency of bioplastic production, ensuring that the process remains at the cutting edge of sustainable manufacturing.
The potential of bioplastics to transform manufacturing and pave the way for a sustainable future is immense. As research and development in this field progress, we can expect to see a new generation of bioplastic materials with enhanced properties, opening up even more possibilities for their use across industries.
Injection molding, a versatile and widely used manufacturing process, is playing a pivotal role in the rise of bioplastics. Known for its ability to shape plastics into complex forms, injection molding is proving to be just as effective with bioplastics, with only minor adjustments needed. By tweaking temperatures, pressures, and mold designs, manufacturers can optimize injection molding to accommodate the unique properties of bioplastics.
The data on this page is generated by a fully automated algorithm. It may have errors, and is provided on an "as is" basis with no guarantees of completeness, accuracy, usefulness or timeliness.
However, challenges remain. The cost of bioplastics is still higher than that of traditional plastics, and in some cases, bioplastics may not yet match the performance standards required for specific applications. Additionally, the availability of bioplastics is still somewhat limited, which can slow their widespread adoption.
The path to a greener future in manufacturing is clear. With bioplastics and injection molding leading the way, we are on the brink of a world where products are not only functional and aesthetically pleasing but also environmentally responsible. The future of sustainable manufacturing is bright, and together, we have the opportunity to shape it.
The adoption of bioplastics is gaining momentum across multiple industries, including packaging, consumer goods, and even automotive manufacturing. This shift is driven by a combination of increasing consumer demand for environmentally responsible products, stricter regulations on conventional plastics, and corporations setting ambitious sustainability targets.
The dossier is a printable PDF file, summarizing information and publications for this company. The creation of dossiers is included in your subscription. After the creation of the dossier is completed, it will be sent to your email address .
Plastic&Chemical Trading (P&CT) was founded in 1989 by Roger Cockram, a veteran in the South African plastics industry. The company was initially established as a raw material trading operation that serviced the South African plastics industry.
The visualizations for "ABC Plastic Moulding Group GmbH, Rüsselsheim, Germany" are provided by North Data and may be reused under the terms of the Creative Commons CC-BY license.
GETTING A QUOTE WITH LK-MOULD IS FREE AND SIMPLE.
FIND MORE OF OUR SERVICES:
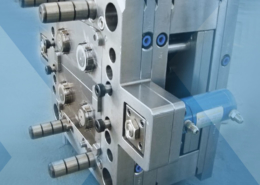
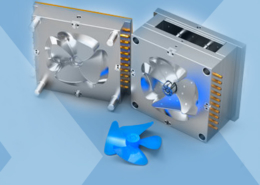
Plastic Molding

Rapid Prototyping
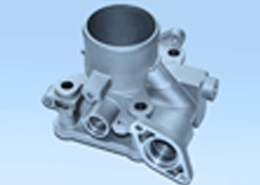
Pressure Die Casting
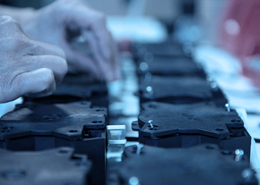
Parts Assembly
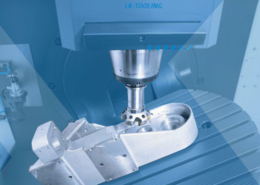