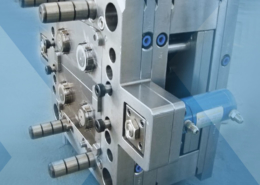
Components of an Injection Mold - injection molding tooling
Author:gly Date: 2024-10-15
All injection molding materials we offer are available for prototype mold applications. That said, abrasive materials such as glass-filled ones may result in increased wear on a prototype tool's life.
Depending on the needs of the finished products, a broad range of polymers can be utilized for injection molding. The cost involved when you buy plastic injection mold materials varies depending on the material selected. Thermoplastic pellets range in price from $1 to $5 per kilogram.
Material cost is determined by the design of a product, the material utilized, and the quantity of material needed to complete the injection molding process.
3D printers can manufacture basic low volume 3D printed molds for as cheap as $100. A metal mold for a mid-volume service life of 1,000-5,000 units costs between $2,000 and $5,000. Mold costs can range from $5,000 to $100,000 for molds with more complicated shapes and prepared for higher production runs of 10,000+ pieces.
3D printing is an excellent process for rapid prototyping! However, prototyping with injection molding enables a much more comprehensive range of materials, finishes, and textures that other processes do not offer. Prototyping with injection molding also paves the way for potential full-scale production in the future. You can iterate and tune the design to fit the same process used for production quantities. Many customers do initial prototyping using 3D printing but later move onto injection molding when preparing to scale production and bring their creation to its final vision.
Get your project off the ground with production quality parts in as few as 10 business days. Low-cost tooling, no minimums, and dozens of material and finishing options allow you to quickly validate your product and set you up for production runs.
Mold manufacturer location: This was also mentioned while researching how mold size may affect your total injection molding expenses. To have your mold wherever it needs to go, an off-site plastic injection mold maker will charge you extra for shipping and handling.
Typically, the cost of the mold, also referred to as the tooling cost, is the major cost driver in injection molding. Let’s take a look at some of the elements that influence the price of an injection mold.
With small desktop injection molding equipment and 3D printed molds, creating modest volumes of components with injection molding is the most cost-effective. Small-scale automated injection molding machines are viable options for medium-series manufacturing of small components.Large industrial injection molding machines can range in price from $50,000 to more than $200,000. These machines also have more strict facility requirements and the need for specialized staff for operations, upkeep, and monitoring. As a result, although injection molding is a core competency, most businesses outsource mass manufacturing to service providers and contract manufacturers, with equipment expenses included in the service prices.
Texturing and polishing of prototype molds can be performed; however, the effect is likely to wear out sooner due to the softer tooling used and may not justify the increased cost. Typically we recommend B to D SPI finishes for prototype molds.
All of our usual injection molding material offerings are available for prototype molding! Read more about choosing the right injection molded plastic.
Creating more sophisticated molds necessitates technical knowledge. As a result, companies typically outsource specific aspects of injection molding, for instance, mold design and production.
At Xometry, we help our customers bring their ideas to reality. While we offer an array of services, such as CNC Machining or 3D Printing which are used to prototype parts, many of our customers are looking to take their prototyping needs to the next level. Our prototype molding services can help you bridge the gap between initial prototypes to validating your product for full production runs.
When it comes to injection molding prices, basic plastic injection molds might range from $3,000 to $6,000. A big, more sophisticated high-production, cross-cavity mold can cost between $25,000 and $50,000 or more. Although it may seem obvious, several factors contribute to the cost of injection molding.
For injection molding, special-purpose equipment ranging from tiny personal molding machines that enterprises may use in-house to big industrial injection molding equipment primarily handled by providers, contractors, and major manufacturers is utilized.
Gates may be constrained to edge, direct & fan techniques. Gating that requires high shear or hot runners is better suited for Bridge or Production tooling.
We are ISO 9001:2015, ISO 13485, and AS9100D certified. Only the top shops that apply to become Suppliers make it through our qualification process.
After receiving the order, the statement of work is reviewed by one of our manufacturing engineers. A case manager is assigned, and an appropriate manufacturing supplier is identified. A comprehensive DFM/PEG report is created and provided for approval. Upon approval, tooling and mold production is commenced. T1 samples are produced and shipped for approval. Upon approval, the remaining parts are made.
Injection molding is used across various industries, including aerospace, medical devices, consumer goods, energy, electronics, automotive, robotics, toys, and more.
To a certain degree, asking for the costs of plastic injection molds cost is similar to questioning how much a car costs. Is your mold going to be a Pinto or a Porsche? Also, keep in mind that the cost of a mold is only the beginning. To calculate complete plastic injection molding costs for any projects, you must also include raw material, operating, and maintenance expenses in the future. These costs are a result of the aforementioned contributing factors.
A MUD (Master Unit Die) is a type of mold that uses a standard injection molding frame that utilizes inserts that define the shape of the internal cavity and thus the eventual part. Think of it as a quick-change system akin to swapping out the head of a disposable razor. Ultimately this type of tool helps drive lower-cost and lead time as most of the machining time will be focused on the core and cavity work, rather than all other aspects of a more complicated tooling setup. MUD tooling is often used with prototype molding applications. Learn more about injection molding tooling and processes.
Choose from millions of possible combinations of materials, finishes, tolerances, markings, and certifications for your order.
If a plastic injection mold factory has the tools and materials, creating molds in-house may be the most cost-effective option if the technical expertise is also accessible. If the tools required for injection molding are not easily accessible, outsourcing lowers the cost of developing a mold.
Our experts help get your parts delivered right to your door without the hassle of sourcing, project management, logistics, or shipping.
Our prototyping molding services are non-limiting. Take advantage of all the same technologies, materials, and finishing options Xometry offers within our plastic injection molding services to get the same quality of parts you can expect from a total production run with no minimums. Our project managers and engineers will work closely with you to understand your project's unique requirements and help you make informed decisions to optimize for the lowest costs and fastest lead times. Get started by uploading your files to the Xometry Instant Quoting Engine.
Tooling used for prototype molding applications is generally made of softer materials and thus will wear out sooner than molds made of tougher material.
Xometry can typically deliver a prototype injection mold component within 3 weeks. We can deliver in as few as 10 business days, depending on the specific requirements of your project!
Injection molding, the major cost driver is generally mold or tooling expenses. Molds for injection molding are typically created in one of three ways:
We do our best to cater to our customer's needs and desires. That said, there are considerations one should make when choosing any manufacturing process. When developing a prototype mold, there are a few key aspects. The table below may help you determine whether an injection molding prototype process is suitable or if you may need to explore higher-tier options such as our Bridge Tooling or Production Tooling services.
The SPI (Society of Plastic Engineers) developed mold classifications to standardize mold type definitions based on mold material, tool design, features, and production volume. Mold classes range from 101 (most advanced, highest volume production) to 105 (prototyping applications) to simplify the type of injection mold required for thermoplastic molding based on production needs. Mold classes are intended to be used as a guideline.
The simple answer is that plastic injection molds range in price from $100 for a 3D printed injection mold to $100,000 plus for a sophisticated multi-cavity steel mold for greater manufacturing loads, which is typically the most important fixed start-up cost in injection molding. However, because these expenses are spread across hundreds or thousands of components, injection molding is a suitable method for mass-producing plastic parts at a low cost.
Xometry offers both domestic (USA) and international molding options. US-based prototyping molding is typically the quickest, while international prototype tooling will be the most economical at the expense of a few extra days.
Class 105 & 104 molds are the most suitable for prototyping molding runs and are typically made of Aluminum or Mild Steel. Projects requiring class 103,102 or 101 molds may be better suited for other tiers of production and be made of higher tier materials.
Yes, multiple colors can be run even on the same order! When running multiple colors on the same order, a purge charge will be added.
Sometimes it can be challenging to determine whether or not you should start with Prototype Molding or jump straight into Production Molding. Xometry understands every project is unique, and our experts will work with you to make an informed decision. There are a few characteristics that Prototype Molding may be best suited for:
GETTING A QUOTE WITH LK-MOULD IS FREE AND SIMPLE.
FIND MORE OF OUR SERVICES:
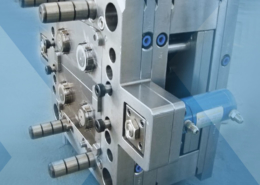
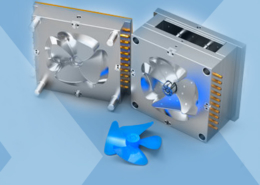
Plastic Molding

Rapid Prototyping
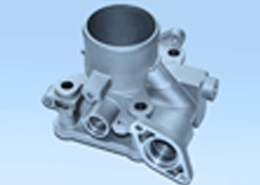
Pressure Die Casting
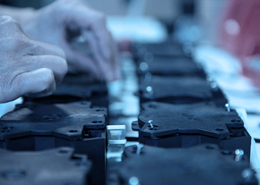
Parts Assembly
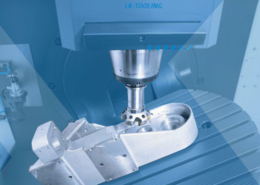