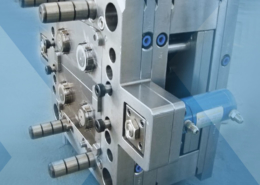
CNC Machining vs. Plastic Injection Molding - injection mold fabrication
Author:gly Date: 2024-10-15
And then closing the mold with the fixed side of the first set of molds, the first shot and the second shot simultaneously close the mold and open the mold, and then use a second set of nozzles to inject a colored material into the second set of molds, After the product is cooled and molded, the product is obtained by two-color molding, and then the product is taken out, as shown in the following picture.
- Careful consideration of surface finish in mold cavities influences the texture and appearance of the molded parts. The desired surface finish is designed to meet the specific requirements of the medical device.
- Regular handwashing, thorough gowning procedures, and adherence to hygiene practices are enforced to minimize the potential for human-generated contaminants.
- Applications: TPE molds are used for producing medical products like medical tubing, seals, gaskets, and grips requiring a balance of flexibility and durability.
Top ability of R&D team and mold design to efficiently complete any type of shape or surface. In addition, we can provide product development and complete solutions to mass production, which...
In essence, designing a plastic mold for a medical device demands meticulous attention to detail, collaboration between engineering and regulatory teams, and a deep understanding of both molding technology and medical device requirements. A well-designed mold is a cornerstone of producing safe, effective, and high-quality medical devices that meet the stringent standards of the healthcare industry.
FORESHOT has been offering customers high-quality plastic injection molding and electronics manufacturing services since 1985, both with advanced technology and 33 years of experience, FORESHOT ensures each customer's demands are met.
- Advantages: PE's flexibility and biocompatibility make it suitable for medical applications. It's used in devices requiring a wide range of mechanical properties and can be molded or extruded with relative ease.
- Data from post-market surveillance, production cycles, and quality control processes drive continuous improvement efforts. Any deviations or issues are thoroughly investigated, addressed, and used to refine mold designs and manufacturing processes.
- Advantages: PEN's barrier properties and resistance to chemicals make it suitable for medical packaging and devices requiring excellent moisture and gas barrier.
- Advantages: PC's impact resistance and transparency make it a top choice for medical devices requiring both durability and visibility.
- Rapid prototyping exposes design flaws in their infancy. Physical prototypes are examined for structural weaknesses, undercuts, interferences, and other geometry-related anomalies that might impede effective molding.
- The surface finish of implantable devices assumes critical importance. The choice of high-quality molds and meticulous production techniques contributes to achieving the desired surface texture, which is essential for preventing bacterial adhesion and promoting biocompatibility within the body.
- Applications: Medical bags, tubing, surgical drapes, joint replacements, and even implants benefit from PE's versatility and biocompatibility.
Plastic molds play a vital and intricate role in the production of implantable medical devices, serving as the linchpin that ensures these devices meet the highest standards of precision, quality, biocompatibility, and regulatory compliance. Implantable medical devices, ranging from orthopedic implants to cardiovascular stents, pacemakers, and intraocular lenses, have revolutionized modern healthcare by offering therapeutic, diagnostic, and supportive solutions that interact directly with the human body. The involvement of plastic molds in their production reflects the marriage of cutting-edge technology, materials science, engineering expertise, and healthcare innovation. Here's how plastic molds contribute to the production of implantable medical devices:
- Shortened development cycles allow designers to evaluate multiple design iterations within a condensed timeframe, enabling them to swiftly iterate on improvements and innovations.
- Personnel working in cleanroom environments receive extensive training in cleanliness protocols, gowning procedures, and contamination prevention measures. Regular training sessions reinforce the importance of maintaining a clean and hygienic environment.
Our comprehensive product design services ensure that we work with our clients from the beginning stages to make improvements on all technical drawings, including 2D and 3D files, to ensure the best possible outcome for each project.
- Ease of maintenance is integrated into the mold design. Features that facilitate mold disassembly, cleaning, replacement of components, and routine maintenance extend the mold's lifespan and ensure the sustained quality of molded parts.
- Compatibility assessments evaluate how the chosen materials will interact with the medical plastics, sterilization agents, and any chemicals used during production.
- By physically assessing rapid prototypes, designers identify opportunities for optimization. Cooling channel layouts, gate positions, and other critical features can be refined to maximize efficiency, part quality, and production throughput.
Plastic molds are indispensable tools in the production of disposable medical devices, playing a pivotal role in shaping the landscape of modern healthcare. Disposable medical devices are designed for single-use purposes to minimize the risk of cross-contamination, enhance patient safety, and simplify clinical procedures. The integration of plastic molds into the manufacturing process ensures that these devices are produced with precision, consistency, and adherence to stringent regulatory standards. Here's are how plastic molds are utilized in the production of disposable medical devices:
- The identification of these flaws at an early stage prevents their proliferation into full-scale production, mitigating costly rework and ensuring mold designs align with intended specifications.
- The mold design process is governed by strict design controls. Detailed design input requirements are established to ensure that the mold design aligns with the intended use and performance of the medical device.
- Sterilization: Many medical devices require sterilization to ensure they are free from pathogens. Sterilization methods can include gamma irradiation, ethylene oxide gas, autoclaving, or chemical sterilization.
Traditional plastic injection molding does often uneven surface gloss of products and floating or exposed fibers on the surface of the fiberglass reinforced plastic chassis、poor transferability、inject pressure excessive and inject pressure uneven that they make stress marks around the mold gate of the product.Therefore, it is necessary printing and painting process to cover these surface defects. For high gloss products, insufficient brightness and uneven brightness cannot be covered by painting.Therefore, FORESHOT develops and apply RHCM technology, not only solve the above problems but also solve traditional plastic injection molding in ultra-thin parts, thick parts and reduces the cycle time.RHCM (Rapid Heat Cycle Molding) is rapidly changing the temperature of mold in injection process.This process is not only vanish the welding lines of the surface, but also improve the rate of product gloss and higher mold transferability.High Gloss / Welding Line free Injection Molding with RHCM process is high-level technology, however, FORESHOT has been operated well in High Gloss / Welding Line free Injection Molding with RHCM process and invests many 250T ~ 1000T RHCM machines that they can do mass production and let customers satisfied.
- Mold materials are chosen based on their compatibility with medical-grade plastics, sterilization methods, and the device's intended use environment. Biocompatibility, chemical resistance, and sterilization resilience are meticulously considered.
- Applications: ABS molds are used for producing a variety of medical equipment parts, housings, and structural components.
- Post-sterilization, the disposable medical devices are ready for distribution to healthcare institutions. These devices are versatile, serving multifaceted roles ranging from medication administration to diagnostic testing, wound care, and beyond.
- The versatility of plastic molds facilitates the replication of these intricate designs, enabling the production of implantable devices that align perfectly with the intended anatomical or physiological requirements.
- The rapid prototyping of implantable devices and their molds enables testing, validation, and iteration before committing to full-scale production. This iterative approach refines designs, hones manufacturing processes, and fine-tunes device characteristics, ensuring that the final product meets the highest standards.
- Applications: Fluoropolymer molds are used for producing components like lab equipment, valves, and parts exposed to aggressive chemicals.
- Ensuring the quality of materials used in molds requires audits of material suppliers and meticulous traceability to meet regulatory requirements. This involves establishing a robust supply chain management process.
- Applications: PU is used in molds for producing catheters, medical tubing, wound dressings, medical gowns, and other devices requiring flexibility, durability, and comfort.
- Assembly: If the device consists of multiple components, they might be assembled using techniques like ultrasonic welding, adhesive bonding, or snap fits.
- Mold designers, engineers, and technicians are highly trained and experienced in the nuances of medical mold design and fabrication. Their expertise ensures that molds are designed, operated, and maintained to the highest standards.
- The foundation of the production process lies in the mold design, where meticulous plans are created to capture the complexity of the implantable device. These designs encompass cavity geometry, gating systems, cooling channels, and intricate features that are integral to the device's function.
- Airborne particulates are a major concern in cleanroom environments. High-efficiency particulate air (HEPA) filters are employed to trap particles as small as 0.3 micrometers, significantly reducing airborne contaminants and maintaining a controlled atmosphere.
- Properties: Polystyrene is a rigid, clear thermoplastic known for its transparency, hardness, and ease of molding. It can be either crystal clear or modified for impact resistance.
- Components that come into contact with molds, such as injection molding machines and auxiliary equipment, are also subjected to thorough cleaning and maintenance to prevent the transfer of contaminants.
- Advantages: PP's resistance to chemicals, heat, and impact makes it a valuable choice for medical applications. It is commonly used for devices requiring a balance between mechanical properties and affordability.
- Ethylene Oxide (EtO) Gas Sterilization: EtO gas sterilization is a low-temperature method that can penetrate packaging and reach complex geometries. Mold materials must be compatible with EtO exposure and not undergo significant degradation or changes in mechanical properties.
- The mold design goes beyond aesthetics; it meticulously replicates the intended shape, features, and dimensions of medical device components. Gate locations, cooling channels, ejection mechanisms, and venting are engineered to prevent defects, ensure uniform part quality, and maintain dimensional accuracy.
- Applications: Molds made from PS are commonly used for items like microscope slides, culture dishes, and clear diagnostic components that require visual inspection.
- Chemical Sterilization: Chemical methods like hydrogen peroxide vapor or peracetic acid vapor sterilization are used for heat-sensitive devices. Mold materials should resist chemical interactions with sterilizing agents and not undergo degradation or changes in properties.
- Applications: LSR molds are used for medical devices like silicone seals, gaskets, soft-touch grips, and wearable medical technology.
- Advantages: POM's low friction and mechanical properties make it suitable for producing precise moving parts in medical devices.
- Regulatory compliance is non-negotiable. Molds, like medical devices, must meet relevant standards such as ISO 13485, FDA regulations, and CE marking requirements. This ensures that molds contribute to the production of devices that meet the highest safety and quality standards.
In summation, plastic molds are indispensable in the production of implantable medical devices, serving as the conduits that transform innovation into tangible solutions for patients. The seamless integration of advanced mold design, precision manufacturing, biocompatible materials, and rigorous quality control culminates in the creation of implantable devices that offer unparalleled precision, therapeutic value, and patient well-being. These devices embody the convergence of medical science and technological prowess, shaping the landscape of modern healthcare through their role in restoring health, enhancing quality of life, and exemplifying the highest standards of safety and efficacy.
- Applications: In medical plastic molds, PP finds its place in producing items like syringes, medical bottles, laboratory containers, and packaging due to its durability, chemical resistance, and cost-effectiveness.
- The chosen medical-grade plastic resin, often PVC, polyethylene, or polypropylene, is subjected to a controlled heating process before being injected into the mold under precisely controlled pressure and temperature conditions.
- Autoclaving: Autoclaving involves exposing devices to high-pressure steam at elevated temperatures. The repeated heating and cooling cycles can put stress on mold materials. Materials that can withstand repeated thermal cycling and maintain their mechanical properties are preferred.
- Proper venting is incorporated into the mold design to allow air to escape as the plastic material flows into the cavities. Inadequate venting can lead to issues like air traps, where air is trapped within the mold, resulting in voids or incomplete filling of parts.
- Post-use, the disposable medical devices are safely and hygienically disposed of, aligning with healthcare waste management protocols. Their single-use nature circumvents the risk of cross-contamination and infection transmission, bolstering patient safety.
TDL Company, however, stands out in this field. Equipped with a 100,000 class (ISO8 level) dust-free injection molding workshop, TDL is well-positioned to assist medical manufacturers with production. Crucially, TDL supports the injection molding production of PVC plastic molded medical products in a clean room environment, demonstrating its commitment to meeting the highest industry standards.
FORESHOT is a renowned leader in the field of plastic injection molding and electronics manufacturing, specializing in producing a diverse range of high-quality finished goods, including advanced medical devices, sophisticated electronic components, durable automotive parts, and cutting-edge consumer electronics. Leveraging state-of-the-art manufacturing technologies such as RHCM, Double-Shot Injection Molding, and SMT, FORESHOT commits to delivering excellence and innovation in every product, from intricate medical appliances and robust vehicle accessories to the latest in communications and computing technologies.
In the realm of medical plastic molds, each material brings its unique set of properties and advantages to cater to specific device requirements. The selection process involves a meticulous evaluation of these properties, the intended application, regulatory compliance, and the desired performance of the final medical product. This comprehensive approach ensures that medical devices uphold the highest standards of safety, efficacy, and reliability.
- Proper cooling channels are strategically integrated into the mold design to ensure uniform temperature distribution during the molding process. Effective cooling minimizes cycle times, reduces the risk of warping, and enhances the consistency of molded parts.
- Raw materials used in mold fabrication, such as plastics and mold release agents, are carefully stored and handled within the cleanroom environment. These materials are sourced from reputable suppliers and undergo stringent quality checks.
- Mold fabrication is a testament to precision engineering, encompassing advanced manufacturing techniques such as CNC (computer numerical control) machining, EDM (electrical discharge machining), and intricate tooling. This results in mold components that mirror the intricacies of the design down to micron-level accuracy.
Image courtesy: https://www.healthcarepackaging.com/markets/medical-devices/-packaginig/news/21415536/aptar-csp-technologies-aptar-csp-technologies-earns-iso-quality-certifications-for-medical-device-production
FORESHOT founded in 1985 has more than 30 years in plastic injection industry. In order to give customers more comprehensive service, FORESHOT integration of OEM / ODM and continue develop...
- The mold design anticipates the need for post-market surveillance, enabling the monitoring of mold performance and its impact on device quality. Data collected during the device's lifecycle informs adjustments, updates, and enhancements to the mold design.
- The completion of the cooling process signals the activation of the mold's ejection mechanisms. These mechanisms, which might involve pins, plates, or other components, facilitate the seamless release of the molded device from the mold.
- Properties: Polyethylene, available in different densities (LDPE, HDPE), is a versatile thermoplastic with excellent chemical resistance, electrical insulation, and low friction properties.
- Many medical devices demand exceptionally tight tolerances for proper functionality and compatibility with other components. Designing molds that consistently produce parts within these narrow tolerances necessitates precision manufacturing techniques and stringent quality control measures.
- Enhanced communication minimizes misunderstandings and discrepancies, fostering a shared understanding of design intent and requirements.
- The gate type (e.g., edge gate, pin gate, hot runner gate) is selected based on material properties, part design, and aesthetic considerations.
- Cooling channels intricately woven into the mold structure govern the cooling rate of the injected plastic. This precision ensures that the plastic material solidifies uniformly, minimizing the risk of defects, deformities, or inconsistencies.
- Some sterilization methods involve temperature fluctuations, which can lead to thermal expansion and contraction. The mold material should exhibit good dimensional stability to prevent warping, distortion, or changes in mold dimensions.
- Advantages: PS's optical clarity and rigidity make it ideal for applications requiring transparency, such as laboratory equipment, petri dishes, and diagnostic components.
- The production of implantable devices requires a harmonious collaboration between diverse stakeholders, including designers, engineers, medical professionals, and regulatory experts. The collective expertise of mold designers, materials scientists, and manufacturing specialists ensures that devices are produced to exacting standards, prioritizing patient safety and clinical efficacy.
- Medical devices must be free from contaminants that could compromise patient safety. Ensuring that molds are manufactured in a controlled and clean environment to prevent potential contamination and maintain the quality of the final parts is a challenge that requires strict adherence to cleanroom protocols.
The Double-Shot Injection Molding process has two material tubes, which can respectively emit plastic materials of different materials. First, the mold is closed, and a material is injected into the first set mold by the first nozzle, and the obtained semi-finished product is cooled and opened.
- Suppliers providing mold materials and components are audited to ensure their quality and adherence to regulatory standards. Collaborating with reputable suppliers is paramount to upholding mold quality.
- The mold design should accommodate the optimal injection molding parameters for the chosen plastic material. Parameters such as injection pressure, temperature, and cooling time are meticulously calibrated to achieve consistent part quality and minimize defects.
- Properties: PVC is a versatile thermoplastic known for its flexibility, durability, and chemical resistance. However, it may require plasticizers to achieve certain properties.
- Advantages: PVC's flexibility makes it suitable for applications requiring pliability, such as medical tubing and bags.
- Properties: Polycarbonate is a strong, transparent thermoplastic known for its exceptional impact resistance, optical clarity, and high heat resistance.
- Molds and manufacturing equipment are regularly cleaned and maintained to prevent the buildup of contaminants. Cleaning routines involve using non-particulate-shedding cleaning agents and techniques that ensure no residues are left behind.
- Advantages: PMMA's transparency and optical properties make it suitable for applications requiring clear visibility and protection against UV radiation.
- The intricate ejection mechanisms within the mold are orchestrated to release the solidified implantable device smoothly. Quality control becomes paramount at this stage, with meticulous dimensional checks, visual inspections, and functional assessments carried out to ensure that the devices meet design specifications and regulatory standards.
In summary, the choice of mold material for a medical device is influenced by its compatibility with various sterilization methods. The material's ability to maintain its properties and structural integrity after exposure to sterilization conditions is essential for producing safe and reliable medical devices. Proper material selection ensures that the mold remains a robust and consistent tool throughout the medical device's lifecycle.
In summary, designing and manufacturing plastic molds for the medical industry is a multifaceted endeavor that requires a comprehensive understanding of engineering principles, medical device regulations, materials science, and manufacturing techniques. Overcoming these challenges demands collaboration between skilled professionals across multiple disciplines to ensure the production of safe, effective, and high-quality medical devices.
- Properties: Polyurethane is a versatile thermoplastic known for its flexibility, durability, and excellent abrasion resistance. It can be formulated to exhibit a wide range of properties.
- Just as medical devices are subject to post-market surveillance, molds are monitored for performance, wear, and maintenance needs. Continuous monitoring ensures molds consistently produce high-quality components.
FORESHOT has great experiences from mold design to assembly service including SMT, PCBA, EMS, plastic product injection, precision plastic parts manufacturing, metal stamping, glue dispense, Ultra Sonic Welding, Ultra Sonic Parts Cleaning, and Product Packaging, With its consistent manufacturing flow service, FORESHOT enables the perfect realization of producing products from scratch for clients.
- The parting line, where the mold separates into two halves, must be carefully determined to avoid flash or cosmetic imperfections. Precise mold alignment ensures uniform parting and prevents inaccuracies or defects at the parting line.
- Certain medical devices require molds capable of handling multiple materials or featuring multiple cavities for efficient production. Designing molds that accommodate these complexities while maintaining precision, consistency, and part quality can be intricate.
- Comprehensive maintenance and cleaning protocols are established and followed. Proper care not only prolongs mold life but also sustains the quality of the components they produce.
- Advantages: TPEs provide flexibility, comfort, and resistance to chemicals, making them suitable for medical applications requiring a combination of properties.
Double-Shot Injection Molding uses plastic polymers to mold plastic parts with multiple colors, materials or components with complex designs in one mold and machine. Double-Shot injection molding allows versatility, is simpler and more cost effective in comparison to other processes. Double-Shot Injection Molding requires attention that strengthen of joint is one of critical issue to be considered. FORESHOT could use this technology to shorten the cycle time, assembly cost, human resource and turnover rate. Double-Shot Injection Molding apply in keyboard、Computer / Communication / Consumer Electronics、Electronic Components、Precision Components and Vehicle Accessories etc.
- Rapid prototyping acts as a feasibility assessment platform for inventive mold designs involving complex geometries or unconventional cooling strategies. This evaluation process enables designers to ascertain the viability of innovative concepts before committing to full-scale production.
RHCM (Rapid Heat Cycle Molding) is not only vanish the weld line of the surface, but also lighten up the rate of gloss and higher mold replication. RHCM technology application like plastic parts in Network Communication equipments and Computers / Communications / Consumer electronics.
- Rapid prototyping bridges the gap between digital designs and tangible physical models. This visual representation aids stakeholders in comprehending the intricate mold structure, venting systems, gating locations, and other features that might otherwise remain abstract in the digital realm.
- Advantages: Fluoropolymers' unique properties make them suitable for medical applications requiring resistance to harsh chemicals and extreme temperatures.
- Conventional mold fabrication methods are often time-consuming and resource-intensive. Rapid prototyping techniques, such as 3D printing, dramatically reduce the time required to materialize mold prototypes, facilitating quick and comprehensive design validation.
- The mold design is systematically refined to reduce potential failures, ensuring patient safety and regulatory compliance.
- Achieving a balance between producing high-quality molds and managing costs can be challenging. The use of advanced materials and manufacturing processes required for high-quality molds may impact the overall production cost of medical devices.
- The medical industry is governed by strict regulatory standards to ensure patient safety. Designing and manufacturing molds that comply with standards such as ISO 13485, FDA regulations, and CE marking requirements necessitates meticulous documentation, validation, and quality control processes.
FORESHOT is using precise molds and advanced V-Line injection machine to produce and control each item in micro level. Precision Injection Molding is applied in Vehicle Accessories, Medical Appliances and Accessories, cameras, gears inside of CD player or printer, earphone components and LED etc which are required highly precise standard.
- Properties: PMMA is a transparent thermoplastic with good optical clarity, high UV resistance, and scratch resistance.
- Mold-making tools, machinery, and equipment are meticulously cleaned before use to prevent the transfer of contaminants to the molds. Cleaning processes involve the use of approved solvents and cleaning agents that leave no residue.
- The selection of mold materials is paramount, with a focus on biocompatibility and precision. Molds must be crafted from materials that are not only mechanically suitable but also biologically inert, ensuring that they do not introduce any harmful substances into the implantable devices.
- Adherence to regulatory standards, such as ISO 13485, FDA regulations, and CE marking requirements, is paramount. Regulatory compliance ensures that the mold and the resulting medical device meet safety, quality, and performance standards.
- Cooling channels intricately woven into the mold play a pivotal role in controlling the cooling rate of the injected plastic. This precision ensures that the device solidifies uniformly, mitigating deformities, warping, or structural flaws.
- Regulatory compliance forms the bedrock of implantable device production. The molds utilized adhere to stringent regulatory standards, thereby ensuring that the devices themselves meet the safety, quality, and performance benchmarks set by regulatory authorities.
In summary, maintaining cleanliness and hygiene in the production of medical plastic molds is a multi-faceted effort that involves a combination of controlled environments, strict protocols, personnel training, equipment maintenance, and stringent quality control. These measures collectively contribute to the creation of molds that uphold the highest standards of cleanliness, ensuring the safety, quality, and performance of the medical devices produced using them.
- Molds must withstand the stress of various sterilization methods without degrading, warping, or introducing contaminants that could impact part quality. Accommodating different sterilization techniques while maintaining mold integrity is a complex endeavor.
- Mold design incorporates features that allow for quality control checks during production. Dedicated areas for dimensional measurement, visual inspection, and other testing methods ensure that each molded part meets specifications.
- Computer-aided simulations and prototyping validate the mold design. Simulations predict how the mold will behave during production, helping identify potential issues like uneven cooling or defects.
- The mold's material is chosen carefully, taking into account biocompatibility, chemical resistance, and the compatibility with the chosen medical-grade plastic that the disposable device will be made from.
TDL uses cutting-edge 3D printing technologies to create high-quality, low-volume plastic parts for prototyping and production. Our printers can produce complex geometries, intricate details, and custom textures and finishes. We can work with a variety of 3D file formats and offer a range of materials to choose from.
- Properties: ABS is a thermoplastic known for its toughness, impact resistance, and ease of processing. It can be modified for different properties.
- Gate design and placement are critical to the overall part quality. The gate, where the plastic enters the mold, must be strategically positioned to minimize cosmetic defects, such as gate marks, and structural issues, such as weak points or weld lines.
- Properties: Polypropylene is a thermoplastic known for its exceptional chemical resistance, high melting point, and low density. It exhibits good impact strength and can be molded with ease.
Designing a plastic mold for a medical device is a multifaceted process that involves a comprehensive understanding of engineering principles, material science, regulatory requirements, and manufacturing considerations. Here is a detailed exploration of the key considerations when designing a plastic mold for a medical device:
- Some implantable devices, such as customized orthopedic implants or dental prosthetics, require molds that are tailored to individual patient anatomies. These molds are painstakingly designed to accommodate patient-specific variations, leading to devices that offer optimal fit, function, and patient satisfaction.
- The journey begins with the conceptualization and design of the disposable medical device. Engineers, designers, and medical professionals collaborate to create 3D models that consider the intended clinical application, ergonomic considerations, regulatory compliance, and user experience.
- Molds need to be fabricated from materials that are not only mechanically suitable but also biocompatible and chemically inert. Balancing these requirements while maintaining mold fabrication feasibility can be challenging due to limited material options that meet both criteria.
- Sterilization processes can expose mold materials to extreme temperatures, humidity, chemicals, and radiation. The material's resistance to these conditions is critical. Heat resistance, chemical resistance, and radiation resistance are properties to consider.
- The inclusion of draft angles in the mold design eases the ejection process and minimizes friction during part removal. Appropriate draft angles prevent damage to the part and mold, ensuring smooth operation.
The sterilization process has a significant impact on the choice of material for a medical plastic mold. Medical devices, including those produced using molds, must undergo sterilization to ensure they are free from pathogens and safe for use in clinical settings. The choice of mold material needs to consider how it will react to different sterilization methods while maintaining its structural integrity and functionality. Here's how the sterilization process affects the choice of material for a medical plastic mold:
- Biocompatible materials for the mold are essential to prevent contamination of the medical device. The choice of mold material should consider its potential interactions with the medical-grade plastics, chemicals, and sterilization methods involved in the molding process.
- During mold fabrication, strict quality control measures are implemented. Each component of the mold undergoes inspections to verify its dimensions, surface finish, and functionality. Quality control ensures that molds are precision-engineered.
- Some disposable medical devices undergo sterilization processes such as gamma irradiation, ethylene oxide gas, or other methodologies to guarantee their sterility, paving the way for distribution and use in clinical settings.
- Applications: Despite its wide use in medical tubing, blood bags, and IV bags, PVC is seeing a decline in some areas due to concerns about plasticizer leaching and efforts to find safer alternatives.
- The dynamic nature of the medical industry often leads to changes in device design, materials, or regulatory requirements after the launch of a product. Ensuring that molds can be adapted or modified without compromising regulatory compliance or device quality poses ongoing challenges.
- Involving clinicians and end-users is pivotal in medical device design. Rapid prototyping facilitates the creation of tangible prototypes that stakeholders can manipulate, leading to valuable insights that guide design adjustments for improved user experience.
- Sterilization processes should not compromise the structural integrity of the mold material. The material should maintain its strength, durability, and other mechanical properties after exposure to sterilization conditions.
- Applications: PEEK is used in medical molds for producing orthopedic implants, spinal fusion cages, and other components requiring a combination of mechanical strength and biocompatibility.
- In some cases, mold heating might be required to maintain optimal material flow and prevent premature cooling, particularly when molding high-temperature plastics.
- Compatibility extends beyond physical interactions to encompass potential leaching of harmful substances into the molded parts. Robust material selection mitigates risks associated with patient safety and device performance.
Special requirements also exist for mold maintenance, inspection, cleaning, and storage. The mold steel used in medical device production must be rust-resistant stainless steel. The risk assessment, validation, quality control, and product production of injection molds for medical and laboratory technology make them more costly than standard plastic molds.
- Durable, wear-resistant materials are chosen to withstand the demands of production cycles while minimizing the need for frequent replacements.
- Cleanroom environments are regularly monitored to ensure they adhere to specific cleanliness and contamination control standards. Particle counters and microbial monitors are used to assess the quality of the air and surfaces within the cleanroom.
TDL provides CPK (Process Capability Index) tests to ensure that the injection molding process is capable of producing products that meet the customer's specifications.
In conclusion, rapid prototyping is an indispensable tool that seamlessly integrates into the medical plastic mold design process. Its influence extends beyond visualization to encompass accelerated validation, stakeholder engagement, error reduction, and design optimization. By embracing rapid prototyping, designers can navigate the complexities of mold design with greater precision, confidence, and efficiency, ultimately contributing to the development of medical molds that uphold the highest standards of safety, quality, and innovation.
Double-Shot Injection Molding uses plastic polymers to mold plastic parts with multiple colors, materials or components with complex designs in one mold and machine. Double-Shot injection molding allows versatility, is simpler and more cost effective in comparison to other processes.Double-Shot Injection Molding requires attention that strengthen of joint is one of critical issue to be considered.FORESHOT could use this technology to shorten the cycle time, assembly cost, human resource and turnover rate.Double-Shot Injection Molding apply in keyboard、Computer / Communication / Consumer Electronics、Electronic Components、Precision Components and Vehicle Accessories etc. FORESHOT UL safety standards Double-Shot Injection Molding, Dual-Injection Molding, Two-Shot Molding, 2K Injection Molding manufacturing technologies from Taiwan since 1985. FORESHOT covers a wide range of manufacturing techniques, including Micro Injection Molding, Thin-wall Parts Injection Molding, and Double-Shot Injection Molding. These services are tailored to meet the needs of diverse applications in sectors like Medical Appliances, Optical Components, and Vehicle Accessories. Their innovative approach and advanced technology in areas like RHCM and LSR/LSM Injection Molding position them as a leader in the field, capable of handling complex and precision-based requirements in plastic injection molding.
- The chosen mold material must be compatible with the specific sterilization method used for the medical device. Materials that can withstand the sterilization process without significant changes in mechanical properties, dimensional stability, or surface finish are essential.
- Regulatory standards may require validation of the compatibility between mold materials and chosen sterilization methods. Proof that the mold materials do not negatively impact the quality or safety of the medical devices is crucial for regulatory compliance.
- Medical devices often have intricate and complex geometries to fulfill specific functions. Translating these complex shapes into mold designs that accurately reproduce them in molded parts while ensuring consistency, structural integrity, and dimensional accuracy requires advanced engineering and design expertise.
Designing and manufacturing plastic molds for the medical industry is a highly complex and exacting process, driven by the need for precision, safety, and adherence to stringent regulatory requirements. The challenges encompass various technical, regulatory, operational, and industry-specific aspects that demand careful consideration and expertise. Here's are some of the challenges associated with designing and manufacturing plastic molds for the medical industry:
- Applications: PET is commonly used in molds for producing medical packaging, containers, and disposable devices where maintaining the integrity of the contents is crucial.
- Rigorous risk assessments are conducted during the mold design phase to identify potential hazards and mitigate associated risks. Validation activities, such as simulations, prototyping, and testing, validate the mold's performance and its impact on the medical device.
- Advantages: ABS's impact resistance and versatility make it suitable for medical device components that require both strength and ease of molding.
- Physical prototypes produced through rapid prototyping facilitate practical testing of mold designs. These tangible models can be utilized to evaluate fit, form, functionality, and ergonomics using actual medical device components.
- Rigorous risk assessments are conducted to identify potential hazards, failure modes, and risks associated with the mold's design, fabrication, and use. Mitigation strategies are developed to address these risks and ensure patient safety.
- Complex geometries, undercuts, and intricate features must be faithfully replicated in the mold to achieve accurate and high-quality components.
Regulations and standards play a significant role in shaping the design and manufacturing processes of medical plastic molds. These guidelines are in place to ensure the safety, quality, and performance of medical devices, including those produced using molds. Here's how regulations and standards impact the design of medical plastic molds:
- Properties: PET is a strong, lightweight thermoplastic known for its excellent barrier properties, dimensional stability, and clarity.
- The tangibility of physical prototypes fosters efficient communication across interdisciplinary teams. Designers, engineers, medical professionals, and stakeholders can physically interact with prototypes, promoting clear and concise collaboration.
Medical and laboratory technology plastic molded parts necessitate stringent hygiene standards and advanced injection molding production techniques. The injection molds employed in production utilize only top-quality raw materials and mold components, leading to an increasing demand for innovative sliding coatings. Furthermore, most medical products, such as tips and luer tubes, necessitate clean room injection molding.
- Cleanrooms are equipped with specialized HVAC systems, air filtration units, and air pressure differentials that maintain a controlled and clean atmosphere. These measures prevent external pollutants from entering the cleanroom and safeguard the molds and equipment.
- Strict protocols govern the attire and personal hygiene of personnel working in cleanroom environments. Workers wear specialized cleanroom garments, including coveralls, gloves, hairnets, masks, and shoe covers, to prevent the introduction of particles and contaminants.
The choice of materials for medical plastic molds is crucial, as they must possess specific properties to withstand the demands of the molding process and produce high-quality medical device components. Common materials used for medical plastic molds include:
- The intricate cavities and channels within the mold outline the definitive shape of the disposable medical device. The injection molding process ensures uniform filling of the mold and subsequently cools the plastic to solidify, resulting in the final device form.
- Once the device design is finalized, mold design takes center stage. Mold designers intricately craft plans for the mold's structure, cavities, gating systems, cooling channels, ejection mechanisms, and other critical features.
- Incorporating medical-grade plastics into prototype molds enables simulation of the injection molding process. Designers can assess material flow, cooling efficiency, and part ejection dynamics, identifying potential enhancements or issues.
- Iterative design cycles are empowered by rapid prototyping. Designers can swiftly translate feedback into tangible modifications, accelerating the evolution of mold designs towards optimal outcomes.
In summary, plastic molds are at the epicenter of the production of disposable medical devices, orchestrating a symphony of precision, compliance, and innovation. Through meticulous mold design, adept fabrication techniques, injection molding mastery, stringent quality control, and strategic sterilization, plastic molds contribute to the creation of disposable medical devices that epitomize safety, effectiveness, and regulatory adherence. These devices, designed for a single-use journey, impact patient care across the healthcare continuum while embodying the principles of innovation and patient safety that underpin modern medical advancements.
- Implantable devices must endure sterilization processes without compromise. The mold materials, as well as the design's resilience to various sterilization methods, are meticulously evaluated to ensure that the devices remain sterile and structurally intact.
- Designing an efficient ejection system is crucial for consistent and damage-free removal of molded parts from the mold cavities. The ejection mechanism, often employing ejector pins, must be carefully planned to prevent cosmetic or structural defects.
In the medical field, the choice of plastic material, the molding technique, and adherence to regulatory standards (such as ISO 13485 for medical devices) are critical factors in ensuring the safety, efficacy, and quality of the devices produced. Plastic molding offers numerous advantages, including scalability, repeatability, and the ability to create intricate and customized designs, making it a cornerstone of medical device manufacturing.
- Gamma Irradiation: Gamma irradiation uses high-energy radiation to kill microorganisms. It's effective but can lead to polymer degradation over time. Mold materials should be radiation-resistant to maintain their structural integrity and dimensional stability.
- Prototyping allows for real-world testing of the mold's performance, ensuring that it can produce parts that meet specifications and withstand the stresses of molding.
- Advantages: PEEK's strength, stability, and biocompatibility make it ideal for implantable medical devices where exceptional performance and biocompatibility are paramount.
- The exquisite design of the mold, including gating systems, guarantees a controlled and uniform filling of the mold cavities, ensuring that the resulting implantable device faithfully represents the intended design.
- The virtual mold design transforms into a tangible mold through advanced manufacturing techniques. Precision machining, EDM (electrical discharge machining), CNC (computer numerical control) milling, and other state-of-the-art processes are harnessed to craft mold components with unparalleled precision.
- The surface finish of the mold can affect the release of the molded parts. Sterilization methods should not deteriorate the surface finish or introduce contaminants that could affect the quality of the molded medical device components.
Plastic molding plays a pivotal role in the efficient and precise manufacturing of medical equipment components. It combines engineering expertise, material science, and meticulous quality control to produce devices that meet the highest standards of performance and safety in healthcare settings.
- Properties: TPEs are flexible materials with rubber-like properties, combining the characteristics of both plastic and rubber.
- Properties: PEN is a high-performance thermoplastic with excellent barrier properties, chemical resistance, and heat stability.
Our expert team utilizes state-of-the-art technology and innovative strategies to deliver top-quality mold designs that are optimized for efficient and effective production.
Over the past few years, the demands for plastic injection products have seen considerable increase in consumer electronics products, transportation applications, medical supplies, etc. With the advanced development of precision machine and fast progress of plastic injection technique, progressing from general injection mold to micro injection mold manufacturing, the standards of precision and quality for the completed products of small Precision Components、Electronic Components、Computer / Communication / Consumer Electronics and Vehicle Accessories etc..FORESHOT is dedicated to the development of precision plastic technique and processing, improvement of precision mold, and advancement of plastic object measurement technique, to provide its clients the products with high added value and competitiveness.FORESHOT using precise molds and advanced Sodick V-Line injection machine and JSW high-speed injection machine to produce and control each item in micro level.
In order to provide high-quality products that satisfy customers, we have designed and developed a robotic intelligent production line dedicated to our customers' products.
- Advantages: PU's flexibility and durability are valued for medical applications that require comfort, resilience, and resistance to wear.
- Applications: PMMA molds are used for items like optical lenses, protective visors, and medical device covers requiring optical clarity.
- Quality control processes are in place to ensure that the molds meet the desired specifications and regulatory standards. Detailed documentation tracks the cleaning, maintenance, and quality control activities, providing a clear record of adherence to cleanliness protocols.
- Advantages: PET's strength and barrier properties make it suitable for preserving sterility in medical packaging and disposable medical devices.
- Rigorous risk assessments are essential to identify and mitigate potential hazards associated with mold design, manufacturing, and usage. Ensuring that these risks are appropriately addressed and minimized requires a deep understanding of both engineering and medical device regulations.
Plastic molds are essential tools in the production of various medical equipment. They enable the precise and efficient manufacturing of intricate components used in medical devices. The process involves several steps:
- Properties: PEEK is a high-performance thermoplastic known for its excellent mechanical properties, high heat resistance, and biocompatibility.
- The mold's design is meticulously engineered to replicate the precise geometry of the disposable medical device. Variables like material shrinkage during cooling are meticulously calculated to ensure that the molded parts align with the design specifications.
Maintaining cleanliness and hygiene in the production of medical plastic molds is of paramount importance to ensure the safety, quality, and integrity of the final medical devices. Contaminants, particulates, and impurities can compromise the functionality and biocompatibility of molds, which can subsequently affect the quality of the molded medical devices. Rigorous cleanliness protocols and cleanroom practices are essential to prevent contamination and uphold the stringent regulatory standards that govern the medical industry. Here's how cleanliness and hygiene are meticulously maintained in the production of medical plastic molds:
- The production of medical plastic molds often takes place within controlled cleanroom environments. Cleanrooms are designed to minimize airborne particles, microbes, and other contaminants that could settle on molds or components during the manufacturing process.
- Implantable devices often consist of medical-grade plastics that are compatible with the human body. During the injection molding process, these materials are heated and meticulously injected into the mold's cavities under precise pressure and temperature controls.
- Applications: Surgical instruments, connectors, transparent housings for medical electronics, and components that require impact resistance benefit from PC's properties.
In summary, regulations and standards significantly influence the design of medical plastic molds by ensuring the use of suitable materials, adherence to quality management systems, compliance with biocompatibility and safety requirements, and proper documentation of the design and manufacturing processes. Designers and manufacturers of medical molds must have a deep understanding of these regulations to produce molds that contribute to the production of safe and effective medical devices.
TDL uses medical grade plastic materials for molds that are used in medical applications, ensuring that all products meet the highest standards of safety and effectiveness.
- Mold materials should be chosen based on their ability to withstand repeated sterilization cycles over the mold's lifespan. Materials that maintain their properties and performance after multiple sterilizations contribute to consistent and reliable device production.
- The mold design should align with the intended use, classification, and regulatory pathway of the medical device. A clear understanding of regulatory guidelines influences every aspect of the mold's design and fabrication.
- Tangible prototypes generated through rapid prototyping can be included in documentation for regulatory submissions. These prototypes visually demonstrate design concepts, validations, and compliance with regulatory standards.
Then the plastic injection molding machine rotates the first set of molds to the position of the second set of nozzles, and then closes the mold with the fixed side of the second set of molds, and the second set of molds rotates to the position of the first set of nozzles.
- Inspection points aid in identifying and addressing deviations in real-time, contributing to the consistency and reliability of the medical device components.
- The mold's geometry must precisely mirror the intended shape, features, and dimensions of the medical device component. Meticulous attention to detail ensures that the molded parts meet stringent specifications and function as intended.
- The molded disposable medical devices undergo rigorous quality control procedures. These encompass dimensional assessments, meticulous visual inspections, exhaustive functional tests, and thorough evaluations to ensure that the devices adhere to specifications and meet stringent regulatory requisites.
- Rapid prototyping permits the isolated testing of individual mold components, such as ejector pins, cooling systems, and gating structures. This approach validates their functionality and compatibility before integrating them into the complete mold assembly.
In conclusion, the quality and safety of medical plastic molds are a culmination of meticulous attention to detail, regulatory adherence, validation, ongoing surveillance, and a commitment to continuous improvement. These molds are not merely tools for production; they play a vital role in upholding the highest standards of quality and safety in the medical device industry. By adhering to these principles, manufacturers ensure that molds contribute to the consistent production of medical devices that meet or exceed regulatory requirements and patient expectations.
Rapid prototyping is a transformative tool that holds significant value within the design process for medical plastic molds. This technology-driven approach offers numerous advantages that revolutionize how molds are conceptualized, tested, refined, and brought to fruition. Rapid prototyping empowers designers and engineers to expedite development cycles, enhance precision, and streamline collaboration, ultimately contributing to the production of safer and more effective medical devices. Here's how rapid prototyping fits into the design process for medical plastic molds:
- Successfully designing and manufacturing molds for the medical industry demands a workforce with specialized expertise in mold design, materials science, regulatory compliance, and precision manufacturing. Finding and training skilled professionals who understand both engineering principles and medical requirements can be challenging.
- Advantages: LSR's flexibility, biocompatibility, and resistance to heat make it suitable for producing medical components that require softness and comfort.
- Applications: PEN molds are used for producing medical packaging, containers, and devices where preserving the sterility of the contents is vital.
- The validation and verification process for medical molds is extensive to ensure consistent part production that meets specifications and regulatory standards. Comprehensive validation requires time, resources, and thorough testing to ensure mold performance.
Located in Taiwan since 1985, FORESHOT Industrial Corporation has over 30 years of industry experience, integrating OEM/ODM services and continuously developing new technologies. Their expertise covers a wide range of manufacturing techniques, including Double-Shot Injection Molding, micro injection molding, thin wall injection molding, and double shot injection molding. They serve various industries including computer, communications, consumer electronics, and medical devices.
Plastic molds are widely used in the manufacturing of various medical devices due to their versatility, precision, and cost-effectiveness. Some examples of medical devices that are commonly made using plastic molds include:
- Rigorous testing and inspection protocols are established for the molded components. Random and systematic checks are conducted to ensure that molds consistently produce parts that adhere to specifications and quality standards.
- Unveiling design issues during the rapid prototyping phase curtails the risk of expensive errors during full-scale mold fabrication. Modifications are rapidly executed during prototyping, reducing the potential for costly revisions in later stages.
- Surface Treatment: Components might undergo treatments like polishing, surface texturing, or printing of labels or identification marks.
With the development of science and technology, thin wall injection molding is becoming more and more important due mainly to the growth in telecommunications and portable electronic devices that require thinner and lighter plastic housings. Thin-wall molding offers the opportunity to reduce material part cost and to increase production output through faster cycle times.Thin wall injection molding requires new technology machines that have a multitude of control functions. FORESHOT has advanced V-Line injection machine to achieve the requirement of Thin wall parts and Micro Injection. The most thin thickness is 0.15mm.
- Thorough documentation of the mold design process is essential for accountability and traceability. Detailed records encompass design iterations, simulations, validation results, changes, and maintenance activities.
- Documentation supports post-market surveillance, facilitates recalls if necessary, and enables continuous improvement of the mold design and production process.
- Processes that generate higher levels of particles, such as machining or cutting, may be isolated from other processes within the cleanroom to prevent the spread of contaminants. Segregation ensures that processes with different cleanliness requirements do not interfere with each other.
Ensuring the quality and safety of medical plastic molds is an intricate and multifaceted process that requires a comprehensive approach across all stages of design, fabrication, validation, production, and maintenance. Molds are not only instrumental in shaping the medical device components but also directly influence the final product's performance, accuracy, and safety. Here's how the quality and safety of medical plastic molds are ensured:
- Every detail of the mold's journey is meticulously documented. From initial design iterations and material selection to maintenance records and changes, traceability ensures accountability and the ability to track the mold's history.
- The journey begins with the conceptualization and engineering of implantable devices, often tailored to the specific needs and anatomical variations of individual patients. Designers and engineers collaborate closely to develop 3D models that encompass intricate geometries and functional considerations.
- Following the quality control stage, the disposable medical devices are meticulously packaged within a sterile environment. The choice of packaging materials is meticulous, ensuring that the devices remain pristine, sterile, and safe until their designated use.
TDL utilizes rapid prototyping technologies such as 3D printing and CNC machining to create fast and accurate concept models, functional prototypes, and production-ready parts. Our team can work with a range of CAD files and produce parts in a variety of materials to suit your project needs.
GETTING A QUOTE WITH LK-MOULD IS FREE AND SIMPLE.
FIND MORE OF OUR SERVICES:
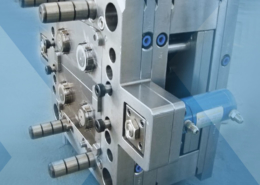
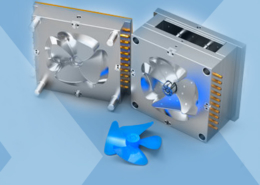
Plastic Molding

Rapid Prototyping
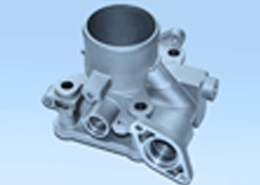
Pressure Die Casting
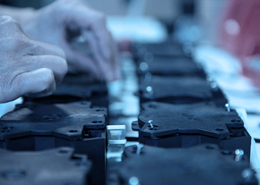
Parts Assembly
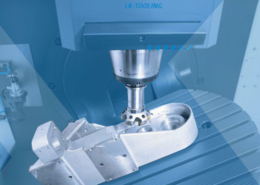