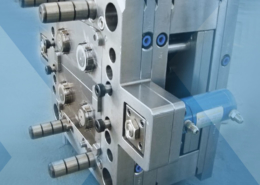
Clean Room Plastic Injection Molding with Class ... - JATCO, Inc - clean room in
Author:gly Date: 2024-10-15
KURZ has developed this world first together with its subsidiary SCHÖFER. SCHÖFER’s Spinstack Mold tool technology is ideal for manufacturing 2K components using the In-Mold Decoration process (IMD). This composition of the materials ABS/PC and the transparent PMMA enables precisely defined backlighting without undesired light diffusion. As a result, both three-dimensional component geometries and structures for 3D light effects and light barriers can be implemented in a single work step. Deformation, contouring, and decoration are all done in one step. Finishing via hot stamping, digital printing, or the integration of touch sensors are also possible. There are solutions for all customer-specific requirements. This is more than 2K plastic injection molding, this is the highly efficient 2K-IMD-process!
It is easy to brush over the basics of plastic injection molding and start talking about the benefits, especially when...
A groundbreaking innovation is the new machine and process technology, which was developed together with the KURZ subsidiary SCHÖFER. The complex technical application is based on SCHÖFER’S high-end tool technology, which is ideally suited to the production of immediately ready-to-install components with large dimensions and enables the use of In-Mold Decoration technology (IMD) in combination with the 2K material mix. This means that both three-dimensional component geometries and structures for 3D light effects and light barriers can be implemented in a single, efficient work step.
The rear-end-cover has a continuous closed surface and large-scale, seamless decoration. It consists of two different translucent plastics. The radar-permeable rear trim supports a wide range of assistance systems, including for autonomous driving. The component can be recycled as a whole and reused as a post-industrial compound.
Structural foam molding is an injection molding process that creates structurally sound and lightweight parts less likely to warp. Structural foam creates a cellular core and solid outer skin during molding, making it an ideal method for large, thick parts. It is widely used in medical, self-serve kiosk, and industrial markets. At Cadrex, we have injection molding and sheet metal fabrication experts that can help you convert sheet metal parts to structural foam or form the sheet metal base that supports the structural foam skins in-house.
Looking for plastic injection molding companies but don't know where to start? Here's why the highest quality, most cost-effective molded parts are usually sourced in North America...
When designing a product, it’s easy to create something that fits all requirements for the product's intent without any thought about the manufacturing process. Many times, it might not be clear what manufacturing process...
Structural foam molding is an injection molding process that creates structurally sound and lightweight parts less likely to warp. A foaming agent is mixed with part resin while still in pellet form. The plastic resin and foaming agent are heated by the barrel in the injection molding machine. Once injected into the mold, the foaming agent turns into gas. The gas bubbles created by the foaming agent expand until the cavity is filled. As the material pushes against the wall of the mold, it creates a thick skin while leaving the inside of the part with a cellular like structure. This not only creates a part that is much lighter than a traditional molded part but also uses less material because of the cellular-like structure. Due to the unpredictable nature of the gas, structural foam parts have an uneven surface color; you can see tints and shades of the chosen color in a swirl-like pattern. For parts that require high cosmetics, we offer in-house painting services.
When it comes to choosing the right plastic injection molding manufacturer, it can be hard to know what you don’t know. Who do you trust? How many questions should you ask? What questions, specifically, should you be asking? With so many variables at play, it’s a challenge to feel like you’re choosing the right manufacturer.
GETTING A QUOTE WITH LK-MOULD IS FREE AND SIMPLE.
FIND MORE OF OUR SERVICES:
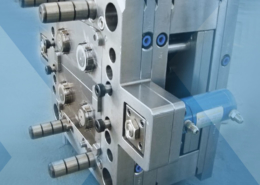
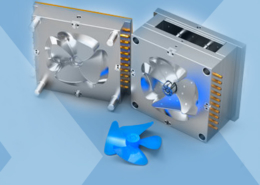
Plastic Molding

Rapid Prototyping
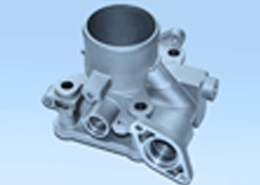
Pressure Die Casting
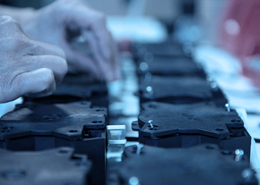
Parts Assembly
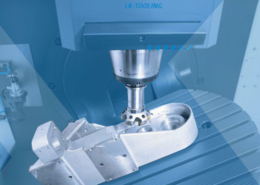