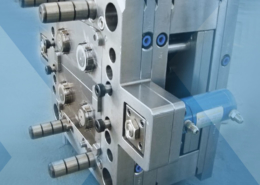
China Plastic Injection Mould & Plastic Cap Mould factories - plastic cap mould
Author:gly Date: 2024-10-15
Whether hydraulic, hybrid or fully electric: ENGEL injection moulding machines are among the most efficient on the market. Servo-hydraulic machines already consume less than 60% of a hydraulic injection moulding machine with a fixed displacement pump. With all-electric injection moulding machines, power consumption can even be more than halved on average.
We have developed hundreds of products, some with medical device injection molding, and manufactured millions of parts annually for the medical industry. Medical devices include point of care diagnostics, microfluidics, and pharmaceutical drug delivery applications.
Pharmaceutical and medical technology products such as syringes, pipettes or other products with high purity requirements,
We focus on forward-looking development and production of injection moulding machines and their automation. Innovative technologies, modern production facilities and sustainable service and support enable our customers to be competitive and successful.
Our precision injection molding options, including medical device injection molding, include scientific molding, R&D molding, high-cavitation molding, micro molding, over molding, and insert molding.
Ergonomics is the top priority for this injection moulding machine. The different clamping systems enable ergonomic overmoulding of inserts. Thanks to the wide range of options and the flexible machine concept, the machine can be adapted to your individual requirements.
Pharmaceutical and medical technology products such as syringes, pipettes or other products with high purity requirements,
Internet Explorer is no longer supported. Please switch to a current browser to be able to use engelglobal.com to its full extent.
When choosing the right machine, the customer's requirements are the most important factor. ENGEL therefore bases the classification of its machines on the following customer requirements:
All our injection molding presses are equipped with servo-driven robotics for high-speed automation and medical device injection molding production.
Our two-platen injection moulding machines are characterised by an extensive clamping force range on the smallest footprint. The range extends from 3,500 to 55,000 kN clamping force: from the entry-level t-win model to the individually adaptable duo tech and the fast duo speed. The duo series is among the most energy-efficient of its kind - with up to 55% less energy consumption compared to machines without servo hydraulics.
Ergonomics is the top priority for this injection moulding machine. The different clamping systems enable ergonomic overmoulding of inserts. Thanks to the wide range of options and the flexible machine concept, the machine can be adapted to your individual requirements.
Our assembly and joining capabilities include product filling, foil/heat sealing, ultrasonic welding, heat staking, mechanical assembly, pinning & UV/hot melt gluing, custom packaging/kitting, and pouching. And this includes medical device injection molding.
Our medical device injection molding product finishing capabilities include hot stamping, banding, pad printing, silk screening, flaw coating, conductive painting, cosmetic painting, metalizing, and plating.
With a precisely matched temperature control solution and our digital assistance systems, additional energy-saving potential of up to 67 % can be exploited.
Our mid to high-volume automated and semi-automated manufacturing of plastic, including medical device injection molding, injection-molded components and assemblies for single-use, metered-dose, and multi-use disposables for the drug delivery, consumer packaging and diagnostics industries offer high quality at economical value.
With a precisely matched temperature control solution and our digital assistance systems, additional energy-saving potential of up to 67 % can be exploited.
The production molds for medical device injection molding projects include high cavitation SPI Class 101 and 102 molds constructed from hardened steel. Cold, runner, hot sprue, and hot runner molds are designed with up to 128 cavities.
Everyday products such as household appliances, toys or furniture to underground tanks or pallets from the logistics sector
Whether hydraulic, hybrid or fully electric: ENGEL injection moulding machines are among the most efficient on the market. Servo-hydraulic machines already consume less than 60% of a hydraulic injection moulding machine with a fixed displacement pump. With all-electric injection moulding machines, power consumption can even be more than halved on average.
Everyday products such as household appliances, toys or furniture to underground tanks or pallets from the logistics sector
Lightweight plastic elements to reduce the weight and distortion of your plastic parts with foam injection moulding, for example.
Each development project requiring medical device injection molding services is managed by a Project Engineer who monitors and controls deliverables and provides regular status updates.
For the consumer market, including medical device injection molding, we specialize in the automated production of high-volume disposables, unit-dose packaging, caps and closures, and over-the counter diagnostics and drug delivery applications.
Internet Explorer is no longer supported. Please switch to a current browser to be able to use engelglobal.com to its full extent.
Our product portfolio ranges from 280 kN to 55,000 kN clamping force. It includes hydraulic, hybrid and electric or horizontal and vertical injection moulding machines. From quickly available stock machines to machines that can be customised to the maximum to high-precision systems with the shortest cycle times.
With over 20 market-proven injection moulding processes, ENGEL enables economical production despite ever-increasing product requirements.
The range extends from the standardised entry-level model e-mac fast track to the highly flexible e-mac and e-motion to the high-performance e-cap and e-speed, which are specially optimised for the packaging industry. The integrated encapsulated toggle of the injection moulding machines - in the clamping force range from 300 to 6,500 kN - is the optimal solution especially for applications in the cleanroom.
We focus on forward-looking development and production of injection moulding machines and their automation. Innovative technologies, modern production facilities and sustainable service and support enable our customers to be competitive and successful.
Our mold maintenance plans for projects that include medical device injection molding services ensure each mold undergoes regular cleaning and review at predefined intervals based upon the number of setups and cycles. Mold inspections, general mold maintenance, major mold maintenance and preventative maintenance are standard operating procedures.
Natech’s projects that include medical device injection molding services are supported by MoldFlow Analysis, a Viscosity Curve, a Cavity Balance Study, a Pressure Window Characterization, a Gate Seal Time Study, and a Cooling Time Study. Natech engineers are masters of insert configuration and design single-cavity R&D molds with steel inserted areas. Interchangeable plates, inserts, and sub-inserts allow for more rapid design iterations at LOWER cost than creating new molds for each feature variation. SPI Class 103 and 104 molds are constructed from P20 steel and aluminum with hot runners and cold runners.
We know how diverse the requirements of our customers and the products they produce are. At ENGEL, we see ourselves as a total solution provider. We support our customers in their challenges. Our injection moulding machines stand for efficiency, quality and reliability.
Compact, energy-efficient and consistently high part quality: the victory series - from 280 to 5,000 kN clamping force - offers you the perfect modular system for the production of diverse technical parts. The patented force dividers, which distribute the clamping force evenly over the entire clamping surface, guarantee consistently high part quality, even with multi-cavity moulds. In addition, the proven tie-bar-less technology allows the use of a relatively small injection moulding machine even with large moulds. In this way, you only invest in the clamping force that is actually required and save valuable production space in the process.
In the electronics market we draw upon deep experience in comprehensive analysis and testing for evaluation and verification to design and build lighter, more durable electronics components.
We are an ISO-certified, family-owned provider of engineering, custom injection molding, and contract manufacturing. Our clients bring demanding applications requiring medical device injection molding services and best served by expert engineers.
Compact, energy-efficient and consistently high part quality: the victory series - from 280 to 5,000 kN clamping force - offers you the perfect modular system for the production of diverse technical parts. The patented force dividers, which distribute the clamping force evenly over the entire clamping surface, guarantee consistently high part quality, even with multi-cavity moulds. In addition, the proven tie-bar-less technology allows the use of a relatively small injection moulding machine even with large moulds. In this way, you only invest in the clamping force that is actually required and save valuable production space in the process.
Clients trust Natech to be the medical device injection molding experts in engineering and manufacturing. Our engineers’ experience includes mold qualifications in medical IQ/OQ/PQ, high volume automation in consumer packaging, and engineering-grade resins and ultra-polymers in electronics.
With over 20 market-proven injection moulding processes, ENGEL enables economical production despite ever-increasing product requirements.
We provide medical device injection molding services in New York, New Jersey, Connecticut, Pennsylvania, Florida, California, Illinois, Oregon, Maryland, Massachusetts, Colorado, and Michigan and other regions.
Lightweight plastic elements to reduce the weight and distortion of your plastic parts with foam injection moulding, for example.
The range extends from the standardised entry-level model e-mac fast track to the highly flexible e-mac and e-motion to the high-performance e-cap and e-speed, which are specially optimised for the packaging industry. The integrated encapsulated toggle of the injection moulding machines - in the clamping force range from 300 to 6,500 kN - is the optimal solution especially for applications in the cleanroom.
We take pride in the workmanship of our medical device injection molding services. All Natech tools and production parts are made in the USA. We run three shifts per day, five days per week, and weekends are run on an as-needed basis.
Our two-platen injection moulding machines are characterised by an extensive clamping force range on the smallest footprint. The range extends from 3,500 to 55,000 kN clamping force: from the entry-level t-win model to the individually adaptable duo tech and the fast duo speed. The duo series is among the most energy-efficient of its kind - with up to 55% less energy consumption compared to machines without servo hydraulics.
GETTING A QUOTE WITH LK-MOULD IS FREE AND SIMPLE.
FIND MORE OF OUR SERVICES:
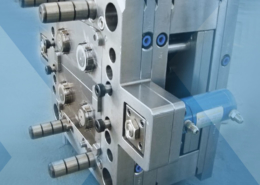
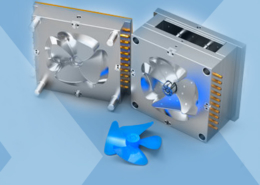
Plastic Molding

Rapid Prototyping
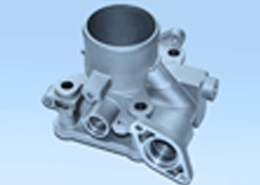
Pressure Die Casting
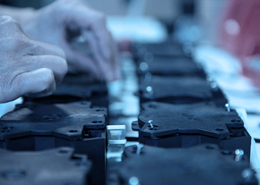
Parts Assembly
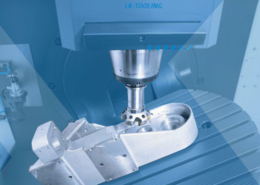