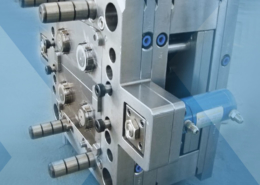
China Plastic Bottle Mould Companies - plastic bottle mould manufacturers
Author:gly Date: 2024-10-15
The cost of material for plastic resin pellets used in the injection molding process is from $1 per kg to $5 per kg. The final cost of injected material will depend on the amount used, which, in turn depends on the design required.
CNC machining is usually employed for metal molds. A stainless steel mold or an aluminum mold would be typical. For example, machining an aluminum mold uses cutting tools to remove material from an aluminum block. This method of machining creates aluminum molds with unmatchable preciseness.
The benefit of self-mating parts is that you can use a single half mold to create the entire part. It keeps the cost of the mold low, and the plastic injection mold size is half. This method increases the volume of production.
Several subprocesses fall under the general umbrella of injection molding, including insert molding and overmolding (a.k.a. multi-shot injection molding, two-shot injection molding, or double-injection molding). Keep reading to learn the differences and similarities between insert molding and overmolding, their applications, and how to figure out which type of multi-material molding is best suited for your project.
Are you considering using injection molding service for your next project? Then send a query to 3ERP at our contact email, and our team will reach out to you with the best price available for your requirements.
Overmolding involves injecting two shots of materials to form the substrate and the overmold. Insert molding only involves injecting one shot of molten plastic, though the metal insert needs to be purchased or created separately.
Repair Costs: Injection molding is a mechanical process requiring multiple types of equipment. Therefore, there are bound to be repair and maintenance processes that result in expenses.
Just like CNC machining, EDM also has high accuracy. However, while CNC machining can be used for materials other than metals, EDM is only suitable for metal molds.
Injection molding is one of the most widely applied manufacturing processes nowadays. Every day, you see and touch multiple parts created by this process, like bottle caps and plastic handles.
Every injection molding material has its specific benefits. The perfect material for your injection mold will depend on your requirements and budget constraints.
An example of this is the soft rubber grip that you see embedded into plastic and rubber products, such as toothbrushes.
Get in touch with 3ERP today to get an injection molding quote for your project. Whether it is a simple injection molding project or something that deals with inserts or overmolding, we handle it all!
Large volume production deals with hundreds of thousands of parts. For this comparison, let us assume we are producing 100,000 parts of the same type.
Professional industrial injection molding equipment costs between $50,000 and $200,000. There may also be shipping costs involved. These machines are not for hobbyists and amateurs as they require skilled operators.
This article examines the costs of injection molding. Understanding the factors that influence these costs will help you estimate your injection molding project costs.
In addition to a team of experts that will help you make your design reality, when you work with SyBridge, you also get access to a suite of online tools that makes designing and ordering parts easy. You can upload your part file, get DFM analysis, and start exploring production and material options, all without initiating a quote — and when the time comes, getting a rapid quote is simple. Contact us today to get the design and manufacturing insight you need to bring your next injection molding project to life.
Injection molding involves injecting molten plastic into a mold, cooling it, and ejecting it. Manufacturers can repeat the process to quickly and cost-efficiently to create thousands of identical parts.
Similarly, the labor costs per part also decrease for larger production volumes. While the final cost of production increases for higher production volumes, you will incur significantly lower per part expenses.
To get a better understanding of the plastic injection molding costs for a part for different production volumes, let’s examine a typical case.
The base cost of an injection mold is not a fixed number that will be the same for every application. It is a varying value that can fall between a couple of hundred to hundreds of thousands of dollars.
In this regard, you can eliminate any features that are just for the sake of cosmetic finishes. This will end up saving money.
There is small-scale injection molding equipment that businesses keep in-house. Then there are large injection molding machines typically used by service providers and those in the large-scale manufacturing industry with large production volumes.
Specialize in CNC machining, 3D printing, urethane casting, rapid tooling, injection molding, metal casting, sheet metal and extrusion
Overmolding is often used to make toothbrushes, medical instruments, disposable razors, and phone cases, or to enclose electronic circuit boards (e.g. USB flash drives).
For example, you can manufacture the top and bottom ends for a plastic container in a single-family cavity injection mold. This type of mold cavitation is a more expensive option in terms of mold cost. But they make the overall production process faster and cheaper.
This is the simplest type of injection molding process. The plastic is injected directly into the mold cavities to create the final piece. Of the three different molding processes, this one has the lowest cost.
After reading this article, you now have a better idea about the plastic injection molding cost and how it varies from project to project. You even know about the cost variations that occur due to the injection mold cost and injection mold tooling cost.
The entire production run for this volume takes about 3 days to manufacture the finished parts. For a 100-part run, let us assume the following parameters:
The size and design of the part will considerably affect the cost. Large injection molded parts require greater material costs and larger molds. Similarly, complex designs may require a multi-step molding process.
This cost can vary based on the process used to create the molds. Usually, three processes are employed for this purpose:
Generally speaking, to get an injection mold cost quote, you need to choose the manufacturer who can provide you with the best results at the cheapest rates. 3ERP is your answer in this regard.
Most steps involved in injection molding are automated and run by software systems. For instance, CNC machines are run by Computer Numerical Controlled software, 3D printers run on their own software, and injection molding also has automated processing.
Insert molding and overmolding can reduce assembly costs and accelerate production, helping companies simultaneously save on production costs and generate greater profits when producing large quantities of parts. However, overmolding is more expensive than insert molding, as it involves two steps. This is particularly true when it comes to prototype or small production runs, as overmolding requires manufacturing two tools — one for the substrate and one for the overmold.
While the process is cheap compared to its alternatives, you can further reduce the costs. For that purpose, here are some pointers that you need to take into account:
3ERP provides every injection molding service you might require, from low-cost injection molding to mass production parts. There are even material options, such as thermoplastic, thermoset silicone, and metal injection molding.
Many established brands such as BMW, Lamborghini, and Electrolux already use the injection molding services offered by 3ERP.
CNC machining has a little drawback in terms of the machine cycle for making molds. These machines require setup time for the tooling and changing the tools for different cut shapes.
DFM stands for Design For Manufacturing. DFM in injection molding refers to producing a part that serves the purpose of the customer and is within their stipulated budget.
This process creates plastic parts with metal inserts fused directly into them. An example of this is the metal fasteners that you see inserted in plastic components.
Family injection molds also have multiple cavities inside them. However, the part cavities are for different parts, so a family mold can simultaneously create different shapes of injection molded parts.
Complex features can call for complex molds and extra steps in the injection molding process. Therefore, eliminating unnecessary features results in a lower cost for injection molds.
Highly complex designs with more cavities and high mold polish result in extra costs. Such designs require research, development, and technical expertise. For this purpose, you can hire a professional or outsource the design process. Both options incur expenses.
Electrical Discharge Machining is also known as EDM. This technology is utilized for creating molds with intricate shapes. It is accomplished by using electrical discharges to melt and bend the metal workpiece and give it the desired shape.
You might have seen that manufacturing costs per part become less when the production takes place in large quantities. The same idea holds true for injection molding as well.
The second process creates Part 2, which contains Part 1. This process is similar to insert molding, with the difference that, instead of a metal insert, both parts are created with plastic injection molding.
Overmolding is also a little more complex than basic injection molding. In overmolding, an initial part is created using injection molding, let us say Part 1. Then, Part 1 is placed inside another mold, and another plastic injection molding process takes place.
What is the cost of injection molding? This is a commonly asked question by people wondering about adopting this technology.
Bigger parts are not always better parts. When the size of the parts increases, so does the expense of injection molds required for the parts. If the same process can be accomplished by reducing the part size, it is a good idea to opt for it.
Not at all. Injection molding is one of the cheapest manufacturing processes. Even so, you can still lower the injection molding costs per molding cycle by following the tips suggested in this guide.
Multi cavity molds have multiple cavities inside, so they can make more than one part simultaneously. Although this type of mold has a higher initial cost, it leads to significantly lower part costs. It is a cost-effective solution for large quantities.
This is, no doubt, a big expense for any business. Therefore, most manufacturers outsource the injection molding process to experts like 3ERP with high-end injection molding machinery. Outsourcing makes injection molding a cost-effective option, in which the client can source the lowest cost for the part required and minimize the variable costs of production.
After reading this guide, you can evaluate the exact manufacturing costs that injection molding will require for your particular requirements.
Medium volume production can range between five thousand to tens of thousands of parts. For this production scale, manufacturers usually outsource the mold production and molding processes.
On the other hand, insert molding is a popular option for connectors, dash panels, electric sockets and wires, dials, remote control coverings, handles, scissor grips, and surgical implements.
Using technologies like insert injection molding and overmolding helps save costs in the long run. For instance, insert molding eliminates the need to create threads on the plastic for attaching it to metal parts.
As stated in the plastic injection molds cost overview, higher volume means lower costs per part. This, combined with savings in mold size and number of molds, lead to significant savings in the final plastic injection mold costs.
Injection molding is a popular manufacturing process for creating many parts and components. As such, learning about the costs of producing an injection molded part is vital before considering this process for your manufacturing operation.
Multi-cavity molds and family molds allow you to multiply the production rate and reduce the cycle time. This can reduce the cost of the entire operation by a significant margin, especially in medium to large production runs.
Setup Costs: There are specific setup requirements for every step of injection molding. For instance, when making the molds, some setup of tooling is required. And setting up the mold and configuring the equipment during injection molding all involve an operator’s time.
Plastic injection molding offers a certain degree of versatility concerning the plastics you can use as the injection material. Some examples include ABS, PU, PE, PP, and PC.
Low volume production can be considered anything between a hundred to a couple of thousand parts. For these low-volume applications, manufacturers usually produce the molds in-house and do the molding themselves.
When you are fulfilling a large production volume, you will require a corresponding large number of molds. However, the cost of the molds does not increase linearly. For example, if the cost of a mold is $1 per part for 100 parts, the cost for 5000 parts can be about $0.5 per part, and for 100,000 molds it can be $0.25 per part.
Now that you know the various costs associated with injection molding, one vital question remains unanswered. What will be the cost of injection molding for my project?
The features of the final product also impact the injection mold cost. If the product has complex features, these might require small components made by a separate injection molding process. One way to lower costs is to eliminate unnecessary features during the design stage.
This is one of the most creative ways to save money on injection molds and simplify the design. Self-mating parts are the parts that attach to themselves when rotated 180 degrees.
The injection mold cost of 3ERP will come as an exact quote that matches your precise requirements. Therefore, you will not be paying extra for something you do not require.
As you can see, the injection molding costs per part decrease significantly for high-volume production. Therefore, high-volume projects have the best cost-effectiveness for injection molding costs.
While the molding equipment is a one-time investment, creating the mold and mold base for the part costs money. It is an expense for every different part produced. Therefore, tooling costs are one of the most important driving factors for injection molding.
For low production quantities, manufacturers create molds of 3D printed polymer resin since it is cheap and doesn’t have to go through a long production cycle.
This is a very wide price bracket. The exact value fluctuates based on several components involved in the injection molding process. These factors that influence the cost are:
Insert molding involves one shot while overmolding involves multiple, which means the insert molding cycle time is generally faster than the overmolding cycle time. However, that doesn’t necessarily mean that insert molding is always the fastest option for production. In some cases, manufacturers may be unable to find pre-made metal inserts that meet their requirements, meaning they’ll need to create a custom metal insert, which can lengthen production timelines.
The process results in a final assembly with greater strength than mechanically fixing the plastic and metal parts together.
The best thing is that you get your parts made by a world-class team of engineers using the most advanced equipment, without bearing any of the costs for the same.
Insert molding and overmolding are both types of multi-material injection molding, but they each have their own benefits and drawbacks and can’t be used interchangeably. To ensure you use the best process for your part, you’ll need to be familiar with each method. If you need some help selecting the best technique to use, contact us to get expert advice on your next injection molding project.
Make full use of the molds by reusing them for various applications. You can not only use the same mold for the same part but also for similar parts as well. This can be done by making adjustments or mold mods wherever possible.
Single cavity molds have one cavity inside. So they make one part per cycle time. While the cost of the mold is less, the production rate of parts is slower. This leads to higher part costs.
If the manufacturer needs additional services such as polishing or secondary finishing for the product, these represent an extra expense. While it is not a part of the injection molding cost, the service provider might consider it an added cost.
For DFM, analysts consider several factors based on art, science, and technology to find the most efficient design, resulting in reduced injection mold costs.
A single part can be approached through different CAD designs. However, not every design idea is ideal. Some designs for the same part may lead to time and resource wastage. Therefore, simplifying part complexity through efficient CAD design ensures the best utilization of resources.
Operator Costs: Regardless of the self-regulated machinery used, an operator must oversee the process. The cost of the operator is something to factor into the labor costs.
This is a little more complex process than basic injection molding. It involves positioning metal inserts in the mold. Once the metal inserts are in position, the plastic injection molding takes place.
Overmolding and insert molding enable manufacturers to create multi-material products without using adhesives, help eliminate secondary assembly steps, and improve the final product. However, it’s important to note the differences between insert molding and overmolding, including:
3D printing is one of the cheapest and fastest ways of making molds for injection molding. This process requires nothing but a 3D printer, so the expense is considerably less. Additionally, there is no need for skilled operators, saving labor costs.
The insert molding manufacturing process involves injecting molten plastic around pre-placed inserts (usually metal), forming a strong bond between the two materials and helping cut back on assembly operations and time. Common inserts include pins, blades, threaded nuts and knobs, sleeves, bushings, and the metal shanks of tools, such as screwdrivers.
Overmolding enables manufacturers to create parts from multiple materials using a manual two-stage process for small production runs or an automated two-stage process for large production runs. Regardless of production volume, the overmolding process works in the following way. First, a thermoplastic injection forms the rigid substrate. After the substrate forms, another shot (generally thinner and more pliable) is injected in, on, or around the substrate. As the materials cool, they bond together, creating a unified, strong, and durable part. Bonds can be chemical or mechanical, depending on the materials as well as the design of the part or product.
GETTING A QUOTE WITH LK-MOULD IS FREE AND SIMPLE.
FIND MORE OF OUR SERVICES:
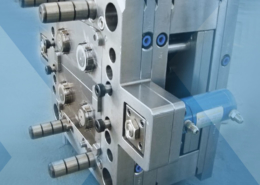
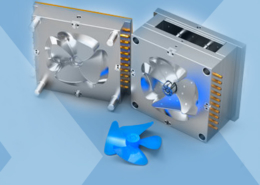
Plastic Molding

Rapid Prototyping
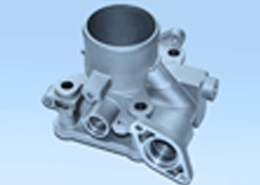
Pressure Die Casting
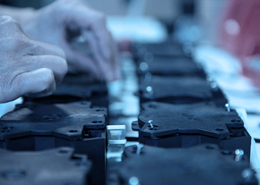
Parts Assembly
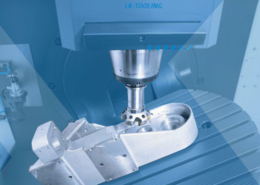