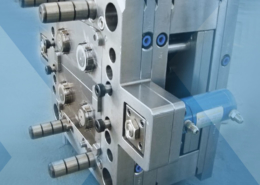
Bio-Flex® S 5514 - bioplastic injection molding
Author:gly Date: 2024-10-15
Make the move from prototyping to on-demand manufacturing for affordable, high-quality molded parts within days. Better yet, your prototyping tool is free once you shift to an on-demand manufacturing tool. Working with a single supplier that provides free design consultation services also massively speeds up the manufacturing process, allowing for greater supply chain flexibility, more consistent parts, and making qualification a breeze.
Overmolding and insert molding are two-part injection molding processes where one material is overlaid onto a second substrate part or metal insert to create a single component.
Design for Manufacturing FeedbackEvery quote includes real-time pricing and design analysis. We evaluate your 3D CAD and help identify any features that may pose challenges during the molding process such as difficult to machine undercuts and insufficient draft.
No one ever said that designing and manufacturing molded parts was easy. Our goal is to get you through it quickly and with quality parts. A good starting point is our Design for Moldability Toolkit.
Injection Molding ExpertiseWe'll work with you throughout the course of your project to help you quickly move from prototyping to production, including finishing options and inspection reporting.
Plastic injection molding is a manufacturing process where resin in a barrel is heated to a molten state, then shot into a mold to form a final production-grade thermoplastic part.
Our digital factories create prototypes and low-volume parts fast, while our manufacturing network, offers advanced capabilities and volume pricing.
Tough Black (Loctite Henkel 3843) and Ceramic-Filled (BASF 3280) are two new advanced photopolymer materials now available for 3D printing.
Injection molding is plastic manufacturing process that can produce high quality parts at scale. It's typically used for low- to high-volume production but our aluminum tooling can also make prototyping runs economical.
Aluminum moldsStandard lead times as fast as 7 daysTolerances of +/-0.003 in. plus resin tolerance (in./in.)Set-up fees apply to each run Consultative Design Services (CDS)Finishing OptionsNo minimum order quantities (MOQ)Quick-turn shipping in as fast as 1 day
Aline Components serves customers in Pennsylvania, New Jersey, Delaware, New York, and beyond. Conveniently located just outside Philadelphia, its state-of-the-art facility employs the latest injection molding equipment and offers plastic parts with all of the most advanced features, such as insert molding, sandwich molding, stack molding for large production runs, and more. Alineâs services range from CAD/CAM documentation support, rapid prototyping, and short-run processes for rush delivery. If you are looking for experienced plastic injection molding company with a detailed knowledge of the most current plastic manufacturing techniques, including composite/core-back molding, contact Aline Components today.
This complete reference guide walks you through everything from quoting, design analysis, and shipment to best practices that ensure your model is optimized for molding.
In most cases, we can maintain a machining tolerance of +/- 0.003 in. (0.08mm) with an included resin tolerance that can be greater than but no less than +/- 0.002 in./in. (0.002mm/mm).
Get machined parts anodized and chromate plated with our quick-turn finishing option. Eligible materials include aluminum 6061/6082 and 7075.
At Aline Components, we work with you to determine if insert molding is right for your plastic part or component, and if so, what material is best suited for the application. We take pride in helping our customers obtain the solutions they need for their product or system to perform to the highest level.
Proto Labs, Inc. 5540 Pioneer Creek Dr. Maple Plain, MN 55359 United States P: 877-479-3680 F: 763-479-2679 E: [email protected]
Our helpful design aid demonstrates part features that are too thin or too thick, bad bosses, right and wrong ribs, and other considerations to be mindful of while designing parts for injection molding.
Because of the initial capital investment in tooling, injection molding makes sense for higher volumes of parts. Our mold cost starts at $1,495 and will vary depending on part geometry and complexity. Other factors that will impact injection molding cost are lead times and material.
Yes, we offer a production tooling option called on-demand manufacturing. This tooling option provides several benefits: lower piece part price, multi-cavity capabilities, guaranteed tooling for the life of the project (we will cut a new tool if it wears out), and first article inspections.
We have two unique offers to meet your needs wherever you are in the product lifecycle. Our prototype injection molding process helps you cut product development cycles by weeks—sometimes months—and bridge to production with injection-molded parts within days. Our On-demand Manufacturing process is designed to meet your production needs, and helps you qualify parts quickly to seamlessly transition into production with scientific molding, in-process CMM inspections with GD&T, and a full suite of secondary operations to make sure that your parts show up and perform as expected.
Unmatched Lead TimesReduce your product development cycle by weeks—sometimes months—and bridge to production with injection-molded parts within days. Some injection molding orders can ship in as fast as 1 day.
No Minimum Order Quantities (MOQs)Procuring parts on demand, without MOQs, helps you manage market or demand volatility and provides a cost-effective source for bridge production, line-down emergencies, end-of-life production, or product customization.
Injection molding is widely used for plastic part production in medical, consumer, and automotive industries. Typical parts include:
Plastic manufacturing and the evolution of thermoplastic injection molding technology has continued to develop with a range of innovative options that add potential savings and performance. Aline Components is a leading plastic injection molding company serving the Tri-State area with the finest plastic parts and employing the most advanced custom plastic injection molding equipment and expertise. Composite molding, also known as core-back molding, is a relatively recent thermoplastic injection molding technique that makes use of innovations in material science to enhance new products and components.
We combine scientific (or decoupled) molding techniques, which optimize and lock in processing parameters to ensure part consistency—with extra attention paid to critical-to-quality dimensions using our proprietary automated CMM process. Plus, with every order you'll get:
We have wide selection of more than 100 thermoplastic and thermoset materials. And if you're looking for alternative material options, check out our guide to resin substitutes for ABS, PC, PP, and other commonly molded plastics.
Liquid silicone rubber molding is a thermoset process that mixes a two-component compound together, which is then heat cured in the mold with a platinum catalyst to produce a final part.
Composite molding uses a two-shot molding technology to add a layer of high performance composite material onto another molded element made from a more rigid plastic. The rigid component acts as a substrate for the composite material. The composite has expansion properties during the curing process, and, after cooling, the final component now has a thick layer of composite firmly affixed to the rigid substrate. Core-back molding has the capability to add more structural strength to components with little added weight, making it an ideal choice for many types of applications where this structural efficiency is desired. New products using core-back molding can also provide this greater strength at a reduced cost to the consumer.
We do quoting a little differently. When you request an injection molding quote, you'll not only receive accurate pricing, but also a manufacturing analysis—within just a few hours. Our online quoting platform also provides you with gate and ejector pin layouts and a price curve tool to help select the best tooling option for your project.
GETTING A QUOTE WITH LK-MOULD IS FREE AND SIMPLE.
FIND MORE OF OUR SERVICES:
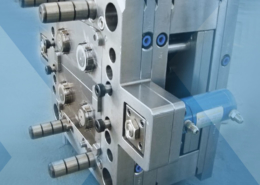
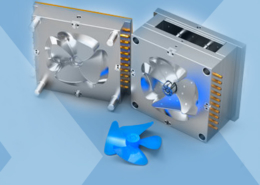
Plastic Molding

Rapid Prototyping
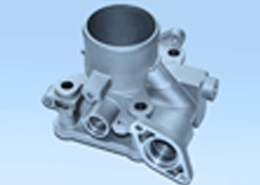
Pressure Die Casting
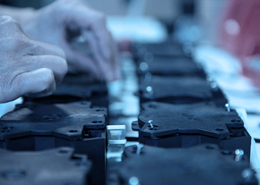
Parts Assembly
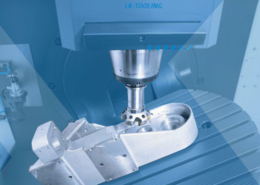