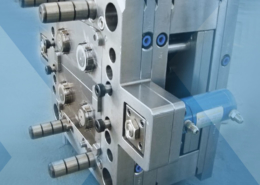
BILLION h 150/260-140 t Injection Moulding Machine - billion injection moulding
Author:gly Date: 2024-10-15
Schöttli molds have been renowned in the medical mold industry for their precision, speed, and excellent repeatability. Because of their compact cluster design, consistent wall thickness, and high-volume capacity, Schöttli medical molds have been the pre-eminent choice for use in medical and laboratory settings. Husky Technologies customers enjoy an enhanced level of technical expertise in the production of the highest-quality parts, additional capacity to increase speed-to-market, and improved responsiveness delivered by the industry’s largest global service and support network.
Do you have patients who suffer from certain chronic diseases or allergies? Husky molding systems enable you to produce auto-injectors that offer easy and intuitive use, especially in emergency situations. Whether you are injection molding empty or pre-filled syringes for single-use administration or cartridge-based (pen-injection) systems for single- or multiuse administration, Husky medical molding precision ensures the highest level of product quality for your drug delivery devices with the lowest level of risk.
In insert molding, a pre-formed component (known as the insert) is placed into the mold and molten plastic is injected to surround and bond with the insert. This insert is typically a distinct component, typically either a metal or a different plastic part. Insert molding is often used for adding discrete components within a single part.
Injection molding equipment that delivers just the right color, shape and shelf appeal are key to consumer trust and preference in healthcare packaging and retail display. So are protecting and sealing the products and their closures against damage, undesirable moisture, light, oxygen or temperature variations. Husky medical injection molding systems and solutions help you achieve all this and more—with high-volume throughput and low scrap rates, precise repeatability, and minimal maintenance.
Our systems approach harnesses the synergy of every component to deliver a smarter-built system. This not only produces better plastic medical injection parts, but also supports better management and response to unforeseen environmental influences—such as an unexpected temperature change in your plant. Husky systems can interact with data from different components, create connectivity between them and adapt internally to sudden changes. This puts greater control in the hands of your operator.
Husky medical injection molding systems produce pharmaceutical packaging that meets five important criteria: containment, accessibility, protection, integrity and stability. All are critical factors in the packaging of products and prescriptions sold behind or over the counter. Quality packaging also helps build brand identity and consumer preference while helping to prevent counterfeiting. Depend on our medical molding solutions to meet your exact cost/performance parameters in producing the following:
Husky is here for its customers, prospective customers, partners and communities—whatever you need, whenever you need it. Simply complete our form and we’ll do the rest. You can count on it.
If you’d like to acquire prototypes before going forward with your plastic molding projects, utilize Leech’s prototyping solutions to test parts before putting them through to full production. Contact us to find out more.
Reducing part variability and enhancing predictability are key in medical injection molding. Most injection molding manufacturers over-spec their machines, hot runners, molds and controllers to eliminate the high cost of producing a bad part. This generates waste. At Husky, we start with the end medical part you want and engineer the entire system to meet or exceed the current norm, enhance efficiencies and output on your shop floor, and eliminate waste.
While thermoset molding is an irreversible process due to the chemical reaction that occurs during the necessary curing process, thermoplastic molding is easily reversible. Thermoplastic parts can be re-melted and molded repeatedly without causing the material to deteriorate. At Leech Industries, we offer our customers the option to use recycled materials if this meets your needs.
A similar process, over-molding involves molding one material (usually a softer or different type of plastic) over another previously molded part to add new properties and enhance the appearance of the original part.
Thermoplastic components, produced through the thermoplastic injection molding process, possess several key characteristics that contribute to their versatility and widespread use in various industries. Here are some notable characteristics of thermoplastic components:
Among our comprehensive plastic molding services, thermoplastic injection molding produces precise molded parts that are suitable for a range of applications.
Trust ICHOR systems to get you to market fast with durable drug-delivery devices for diagnostic and laboratory applications. Your parts and products are formed with legendary Husky precision and repeatability, ready to meet all pertinent global regulatory requirements—so you can be certain about quality, performance and patient safety. Let Husky help you mold these and other medical products with maximum optical clarity and best-in-class operational performance.
We use cookies to personalise content, to provide social media features and to analyse our traffic. We also share information about your use of our site with our social media and analytics partners who may combine it with other information that you’ve provided to them or that they’ve collected from your use of their services. You consent to our cookies if you continue to use our website.
Insert molding and over-molding are additional processes that can be worked into both thermoplastic and thermoset parts.
GETTING A QUOTE WITH LK-MOULD IS FREE AND SIMPLE.
FIND MORE OF OUR SERVICES:
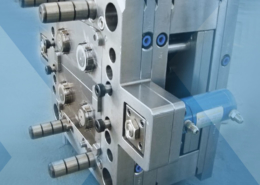
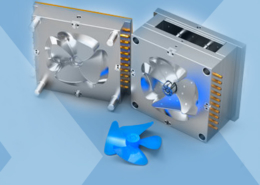
Plastic Molding

Rapid Prototyping
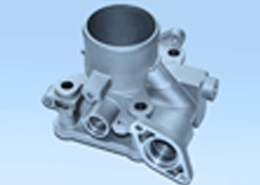
Pressure Die Casting
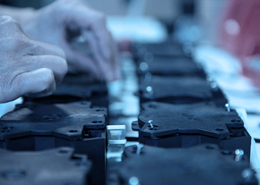
Parts Assembly
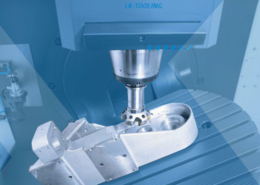