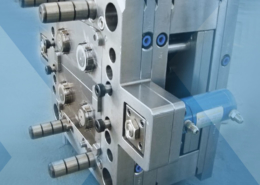
big pallet mould | Resinbyvu - Resin by Viyu - pallet mould
Author:gly Date: 2024-10-15
Please navigate to our online quotation platform and upload an injection molding CAD file to get a quick quotation. Our quotation process is comprehensive from start to finish and involves configuring different materials, finishes, quantities, etc. Furthermore, we will confirm the DFM analysis of the mold so that you get the most accurate part possible.
This category necessitates a straightforward mold, often crafted from cost-effective materials like aluminum or 3D-printed materials. Additionally, it requires minimal raw materials and less advanced machinery, resulting in an overall low injection molding cost. However, the cost per unit part tends to be higher in low-volume production scenarios.
An Installation qualification is essentially a documented Bill of Materials of all the intended equipment that will be needed to mold a product (i.e.: Machine type / tonnage, Robotics, dryer(s), chillers, eDART equipment, etc.).
Determining whether injection molding is expensive isn’t a straightforward answer. While the process proves cost-effective for mass production of plastic parts, the initial setup costs can be substantial due to high machine prices.
We employ a standardized approach when investing in new equipment such as: machines, software, auxiliary equipment, robotics, etc. We remain privately owned and operated and continue to reinvest in the future of our business to ensure long-term success for both our customers and employees. Furthermore, we remain completely dept-free, allowing us to quickly respond to growth opportunities with our clients, especially with new technologies or equipment.
Process Engineers are trained at Multiple RJG Master Molder Levels through their rigorous standards. Also, we routinely utilize cavity pressure sensors with process monitoring technology to achieve 100% monitoring and traceability on patient-critical-applications
Navigating the regulatory landscape for medical devices is complex, and at Plastikos, we pride ourselves on our rigorous compliance with specific regulations and industry standards. Our commitment ensures that the medical components we produce meet the highest levels of safety and quality.
Insert molding involves placing pre-formed components or inserts into the mold before injection. This technique allows for the integration of multiple parts into a single molding process, reducing the need for additional assembly steps. Naturally, a single-step process would mean a lower machine run-time and a lower number of repetitions and cycles. Furthermore, you won’t be assembling separately designed parts together as well and that again would save time. By consolidating manufacturing steps, insert molding can lead to time and cost savings.
Maximizing the lifespan of molds is a cost-effective approach in injection molding. Reusing molds for multiple production runs helps distribute tooling costs across a larger production volume, reducing the per-part cost. Regular maintenance and careful handling of molds can extend their life, providing long-term cost benefits for manufacturers.
In conjunction, Plastikos Medical was already expanding our ISO 7 cleanroom, a process that would take another year to complete. To expedite our customer’s urgent capacity needs, our leadership team devised a plan to address the immediate cleanroom molding requirements while accommodating long-term growth:
The extremely high level of precision needed within the aerospace industry makes CNC machining a suitable manufacturing process for the sector.
Larger mold cavities, capable of accommodating higher material volumes and producing more significant parts in each cycle, typically necessitate more substantial and, consequently, costlier molds.
Larger parts require more material, leading to higher raw material expenses. They also necessitate bigger, more energy-consuming machines with longer cycle times, reducing production efficiency. As part size increases, maintaining precision becomes more challenging, possibly requiring advanced, costlier processes. Additionally, larger parts can produce more waste, especially in the runner system where excess material is generated, further elevating costs.
During the peak of the COVID-19 pandemic, a prominent OEM specializing in fluid handling and liquid cooling for vaccine production partnered with Plastikos to help rapidly scale their growing Bio division. This initiative was driven by the urgent demand for COVID-19 vaccines in the United States and the broader pharmaceutical space. Plastikos, in collaboration with Micro Mold and several other reputable mold suppliers, spearheaded the project to meet the rigorous timelines to build and qualify more than 25 multi-cavity tools.
Instead of buying a machine, businesses outsource their project to injection molding service providers. So they no longer incur the heavy cost of purchasing the machine but are subject to the service provider’s service cost.
Part packaging costs depend on whether the packaging is consumer-facing (i.e., recognizable and short-span) or more costly shipping packaging. Consumer-facing packaging is suitable for products that are ready to use. However, larger manufacturers can use automatic packaging, which reduces damage and incurs fewer errors.
In contrast, high-volume production often demands molds made from robust materials like steel, incurring a higher initial cost but providing extended tool life and minimizing the cost per unit produced. The selection of mold material, therefore, becomes a strategic decision balancing short-term expenditure with long-term efficiency and cost-effectiveness in injection molding operations.
This is where much of the mold validation work / time is spent. Our process engineering team will develop a scientific molding process to target several key process variables. From there, a DOE is performed to test high / low limits of the process. During this time, extensive metrology work is performed on all key print variables. Measurement technique / correlation with our client is crucial during this stage.
A PQ is the final phase in the process development cycle. This is where an extended 8-24 hour production simulation run will occur on the mold to ensure we can move into full scale production. A metrology report on the critical dimensions is also performed as the last piece of confirmation with our clients.
Despite this, the overall manufacturing cost decreases as production scales up. Hence, plastic injection molding is widely considered a cost-effective solution for mass-producing plastic parts, with the price per part decreasing as quantities increase.
Our approach includes detailed planning and oversight at every stage, ensuring seamless execution and exceptional quality.
In contrast, simpler mold designs with fewer complex features result in lower tooling costs, making them a more cost-effective choice, especially for applications where intricate features are not essential. Striking a balance between design requirements and cost considerations is essential in optimizing injection molding expenses.
One stand-alone cleanroom with 8 medical molding machines ranging from 88T – 220T. Each ISO 8 cleanroom machine is equipped with its own 3-axis robot.
To effectively reduce unnecessary features, a thorough design review is essential, focusing on optimizing part geometry for both functionality and manufacturability. This might involve reevaluating the necessity of certain aesthetic elements, consolidating multiple components into a single, more efficient design, or modifying part dimensions to eliminate redundant or non-critical aspects. The goal is to achieve an optimal balance between the part’s functional requirements and the cost-effectiveness of its production.
If you want to produce high-quality machined parts with a sleek appearance, it’s essential to consider some critical factors related to CNC machining.
In some applications, the cosmetic appearance of a part may not be critical to its functionality. Choosing to forego intricate cosmetic details can result in faster production cycles and reduced tooling complexity, ultimately contributing to lower costs. This practice is particularly relevant for parts where aesthetics are secondary to functionality.
The equipment used in the molding process is unique. The cost of a machine depends on the size and its level of sophistication (often measured in terms of automation), and it ranges from $10000 (small) or less suitable for low-volume injection molding to $200,000 (large) suitable for high-volume injection molding. Medium molding machines ($50,000 or more) can also be tailored for medium-level molding. Also, you need to consider the following types of injection molding machines and how they affect the cost:
Part inspection costs can be specialized or standard. On the one hand, standard inspection is an internal process that requires trained personnel to check for part defects (cosmetic or critical) and a quality verification team to identify the probable cause. On the other hand, specialized inspection involves inviting specialized engineers to inspect the product. Thus, specialized certification costs more, and sometimes injection service providers offer the certification at a cost.
We have great confidence in Plastikos as a supplier and regard them as industry leaders in injection molding. Our confidence is so great that we trialed a supplier data program with Plastikos before any other supplier, relying on their measurement data to streamline the receiving inspection process on our end.
Complex designs often require intricate molds with finer details, increasing initial tooling expenses. They may also necessitate advanced machinery and tighter tolerances, leading to higher operational costs and longer production times. Complex plastic molded parts often result in increased cycle times due to additional cooling and setting requirements, reducing overall manufacturing efficiency. Furthermore, the potential for defects rises with complexity, leading to higher rates of waste and rework.
Two separate, state-of-the-art facilities with more than 50,000 square feet of combined cleanroom infrastructure with press tonnages ranging from 66T to 350T. All cleanroom machines are equipped with 3-Axis robotics to enable part handling and cavity separation.
Streamlined tool designs contribute to shorter cycle times in the molding process, enhancing production efficiency and reducing manufacturing costs. They also minimize material waste by lowering rejection rates and decreasing scrap material. Additionally, simpler molds are easier to maintain, which prolongs their lifespan and lessens the frequency and costs of repairs and replacements.
A well-designed part can reduce material usage, simplify mold design, and shorten cycle times, all of which lower manufacturing expenses. Optimizing wall thickness, incorporating uniformity, and minimizing undercuts can lead to more efficient production processes and less material waste. Conversely, complex geometries and poor DFM can lead to increased tooling adjustments, higher defect rates, and prolonged production cycles.
Today, Plastikos has become one of the largest suppliers to our pharmaceutical customer and continue to grow in other strategic markets they serve. Our debt-free, privately owned structure enabled our leadership team to make swift decisions and proactively invest in our customer’s rapid growth demands.
Injection molding costs are a focal point for plastic product manufacturers utilizing this process. This article delves into the intricacies of injection molding costs, shedding light on various factors that contribute to the overall expense. By unraveling these elements, you can gain valuable insights into optimizing costs for your specific project.
As the healthcare industry evolves, Plastikos is at the cutting edge, producing critical injection molded components for medical devices that meet today’s challenges and anticipate tomorrow’s needs. Our commitment to innovation and quality in our state-of-the-art facilities ensures we remain at the forefront of the injection molding industry. Everything we produce can be defined as “Patient Critical” devices ranging from insulin pumps, surgical eye care, respiratory equipment, enteral feeding devices, and much more. We are solely focused and committed to ensuring you produce life-saving devices that help patients get back to their everyday lives.
While high-performance plastics may offer specific advantages, they often come with a higher price tag. Analyzing the functional requirements of the part and selecting a cost-effective material that meets those needs can lead to substantial cost savings without compromising quality.
This holistic support system ensures that every project we undertake is positioned for success, with a focus on innovation, quality, and patient safety.
To simplify mold designs, it’s crucial to eliminate unnecessary features, optimize part geometry, and consider using standardized components. Utilizing CAD and CAM tools can help in identifying and removing superfluous elements, ensuring efficient mold design without compromising product quality.
Knowing about the injection molding cost can help in optimizing the manufacturing process. This is achievable by understanding different factors and elements, and this article discussed everything you need to know about costs in injection molding and how to use it. Looking for a quality-focused injection molding service provider? At RapidDirect, we offer the best at a competitive price.
Experienced Quality Engineering staff is trained on the latest IQ/OQ/PQ mold validation protocols consisting of: First Article Inspection, process DOE, Gauge R&R, CpK Analysis, etc.
Selecting specific materials, such as high-performance plastics, often results in increased expenses. However, optimizing designs and manufacturing processes to reduce material wastage can significantly lower overall costs. While incorporating recyclable materials might lead to a modest increase in initial expenses, it paves the way for more sustainable practices and could prove economically beneficial over time.
Furthermore, our Project Engineering team each holds a Plastics Engineering Degree and will help our clients to optimize their product design for manufacturing, material selection, process optimization, and on-going production support. Our clients are supported through weekly updates on the progress of the mold build through production approval.
The tooling cost incurred during injection molding depends on the machining process used in making the mold, the material used, mold complexity, and mold cavity size.
We have several plastic materials chosen using a stringent and streamlined selection process and an engineering team that can provide professional design suggestions and material selection. Our highly sophisticated manufacturing capabilities and network allow us to ensure high-quality molds and plastic parts. Upload your design today and get instant quotes and free DfM analysis at a competitive price.
Quality injection molded parts and a cost-effective process are achievable by trusting the right injection molding services. At RapidDirect, we offer custom plastic injection molding services to help you make different plastic prototypes or real parts based on your requirements.
On the other hand, smaller mold cavities are generally more cost-effective due to reduced material usage and simpler mold construction. The choice of mold cavity size should align with production requirements, as optimizing for the right balance between cavity size and part dimensions can result in cost savings in both material consumption and tooling expenses.
As an ISO 13485 certified facility, we continue to deliver the internationally recognized quality standard for the design and manufacture of Medical Devices. We are also ISO 14698 compliant and conduct routine bio-burden testing throughout the facilities.
Furthermore, our team of expert quality engineers will lead your IQ/OQ/PQ mold validation strategy whereby we conduct the following:
Several factors directly impact your costs, and understanding these key elements is crucial for optimizing your project’s financial aspect.
Note: not all parts will require surface finishing or other secondary services. As a result, you should ensure you need such services to increase overall production efficiency and less material wastage.
Each medical molding machine is equipped with its own multi-axis robotics system. Part handling and cavity separation are achieved utilizing integrated robotics. These systems are also tied into our process monitoring system to discard product that may drift outside our molding parameters, which are establish during our rigorous mold validation.
The production volume affects the amount of raw injection molding material required, the sophistication of the injection molding machine, and the injection mold’s strength/durability/other mechanical properties. The volume of production is divided into three major categories:
Recognizing the fluctuating nature of pricing and the vital role injection molding cost estimates play in projects, we have crafted an illustrative example to help better understand the cost estimation process.
More complex molds, characterized by intricate features, undercuts, or intricate geometries, generally involve higher tooling costs due to increased manufacturing complexity. These molds require specialized machining and longer production times, contributing to elevated upfront expenses.
This will require a strong injection mold made from steel due to its long life expectancy, many materials, and, if possible, a sophisticated machine. This should increase the injection molding cost. However, the high cost will be distributed among the parts, reducing the cost per part manufactured. It is important to note that there is a higher cost distribution per part in high-volume production than in medium-volume production. As a result, they have a lower cost per part manufactured.
The choice of mold material influences both the upfront investment and the overall efficiency of the manufacturing process. Mold materials vary in cost and durability, with aluminum and 3D-printed molds offering lower upfront expenses suitable for low-volume production.
This approach simplifies the mold design, leading to lower manufacturing costs as complex molds are more expensive to produce. Furthermore, reducing part complexity translates to decreased material usage, offering direct savings. Additionally, simpler designs can shorten the molding cycle, boosting productivity and cutting down on labor and energy expenses. This also results in molds that are less demanding in terms of maintenance. Importantly, such streamlined designs often yield parts with improved structural integrity and consistent quality, reducing the likelihood of defects.
Surface finishing includes processes such as annealing, sandblasting, powder coating, etc., in which the part is subjected to increase its aesthetic appeal or functionality. They are separate from the injection molding process itself. However, many service providers will give a discount to clients using them for both injection molding and surface finishing. Also, there are secondary services which can be manufacturing processes(e.g., machining and drilling), assembly services (e.g., sonic welding), and decorating (e.g., pad printing), which can increase the injection molding cost.
We strategically go-to-market as both a toolmaker, and precision molder. Our philosophy is that we design a mold around the product, whereby we consider critical items such as gating, maximum cooling, venting, wear & replacement components, and tool longevity. This customized approach to tool design and fabrication can often be overlooked unless your supplier has both tooling and molding capabilities.
There are several best practices to minimize injection molding costs without compromising quality. By strategically implementing these practices, businesses can achieve cost-effective production and enhance overall efficiency.
GETTING A QUOTE WITH LK-MOULD IS FREE AND SIMPLE.
FIND MORE OF OUR SERVICES:
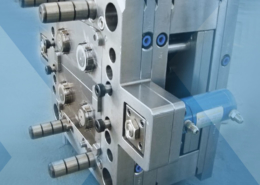
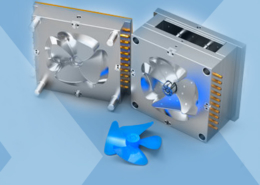
Plastic Molding

Rapid Prototyping
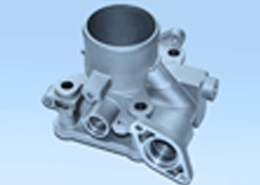
Pressure Die Casting
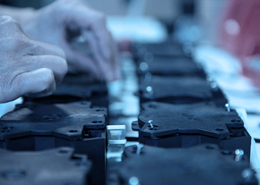
Parts Assembly
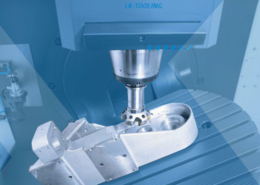