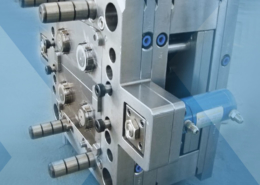
Automotive Injection Molding: How It is Used in Auto ... - automotive injection
Author:gly Date: 2024-10-15
Low Heat Distortion Temperature: ABS plastic has a low heat distortion temperature, making it prone to softening in high-temperature environments. The low softening and melting temperature of ABS means it is not ideal for applications near heat sources or hot machinery parts.
Food-grade ABS meets stringent FDA certification standards, ensuring its safety for direct contact with food. These ABS variants are free from harmful substances, making them ideal for food-related applications.
Standard ABS may lack resilience in high-temperature environments, readily deforming when exposed to heat sources like a hair dryer.
Notable grades include 757F, 737 (Chimei), 2802HD, 2802-TR (BASF), HP20, HP30 (Sabic), 920 (Toray), and SX-200 (Asahi). Food-grade ABS is essential for various culinary and food processing applications, guaranteeing the highest standards of safety and compliance.
ABS plastic is celebrated for its non-toxic and odorless nature, rendering it safe for various applications. Its visual appearance typically manifests as ivory translucent or transparent granules or powder.
2. Automotive Industry: The automotive sector extensively relies on ABS for an assortment of applications. ABS is commonly employed for crafting interior parts, contributing to the overall aesthetic appeal and structural integrity of various components. Additionally, it finds use in the production of engine peripheral parts, where its impact resistance and malleability are valuable assets.
Draft Angle: Reasonably designed draft angles are crucial to prevent surface strain. Inadequate draft angles can lead to cosmetic imperfections in the molded part.
At Fabrik Molded Plastics, Inc., we offer custom two-shot plastic injection molding capabilities. Other service offerings include precision plastic injection molding, insert molding, CT scanning, scientific plastic injection molding, automotive lighting, tooling transfers, and custom automation services.
While ABS plastic offers numerous advantages, understanding its disadvantages is crucial for appropriate application. Here’s a concise overview of the main disadvantages of ABS plastic:
With its diverse variants catering to specific application needs, ABS continues to demonstrate its adaptability and resilience, solidifying its position as a cornerstone in the world of plastic manufacturing.
Holding Pressure and Time: Inadequate holding pressure and a short holding time may result in poor density and gloss. To address this, it is important to increase both the holding pressure and holding time during the injection molding process.
In summary, ABS injection molding, with its diverse variants catering to specific application requirements, offers a versatile solution across various industries.
These flame-retardant ABS variants are engineered to adhere to stringent safety standards while maintaining the versatility and processability that ABS is renowned for, making them indispensable for applications where fire resistance is paramount.
Injection Speed: Optimal injection speed often falls within the medium to high range. Adjusting the injection speed within this range can help maintain the quality and integrity of the molded ABS parts.
Understanding the unique advantages and contexts of these materials is crucial for ensuring optimal performance and quality in various manufacturing processes.
Fabrik Molded Plastics, Inc. is a custom injection and insert molding provider of thermoplastic products. We use the latest molding technologies and automation equipment in our full-service offerings to ensure we compete at the global level. Because we use the latest molding technologies and a scientific approach in our molding processes, our clients can reap the benefits of our competitive advantage. Contact us today or request a free quote to start your custom project.
Cooling: For thick-walled plastic parts, inadequate cooling can lead to surface imperfections and reduced luster. Having a properly designed wall thickness and improving the cooling system is vital to maintaining product quality.
Importance of Drying: While some factories may skip this step for low-quality ABS products, it’s crucial to understand that ABS requires proper drying before injection molding.
Understanding the distinct characteristics and application-specific benefits of each ABS variant enables manufacturers to make informed decisions based on their particular production requirements.
Adhering to these recommendations for drying treatment and injection parameters is vital to produce ABS parts that meet quality standards and avoid common surface defects associated with moisture and incorrect injection conditions.
Varying the monomer ratios yields ABS with diverse physical properties, catering to specific application needs. Furthermore, incorporating additives like glass fibers bolsters strength, while flame retardants enhance fire resistance. These adjustments highlight the adaptability of ABS, enabling its utilization across various industries for an array of specialized purposes.
In addition to the previously mentioned ABS variants, there are several other specialized types to consider, such as glass fiber-reinforced ABS, anti-static ABS, and light-shielding ABS. The choice of ABS type should align with your specific requirements and intended applications.
Also called multi-shot or double-injection molding, two-shot injection molding is an over-molding process that adheres additional material—like thermoplastic elastomer (TPE)—to plastic substrates to improve the appearance, grip, handling, environmental resistance, or impact resistance of injection molded components. Two-shot injection molding is typically performed by multi-barrel injection molding machines, which add extra material shortly after forming the substrate to create strong bonds between the materials.
The two-shot injection molding process consists of two main phases. Similar to traditional injection molding, the first phase involves injecting resin into a mold, which is then cooled to form a solid part in the shape of the mold. The second phase involves overmolding the 1st shot by transferring it to a second cavity by robot or rotating platen. The two plastic resins will form a molecular bond and, once cooled and ejected, becomes a finished multi-resin molded part.
If you have specific material needs or require guidance in selecting the most suitable ABS variant for your project, please feel free to reach out to us. We are here to assist you in making informed decisions and ensuring the right material for your unique applications.
Notably, ordinary ABS plastics retain their toughness even at temperatures as low as -40℃ and can withstand a temperature range of -40℃ to 80℃.
Materials as Alternatives to ABS: While ABS holds a prominent position in the world of plastic manufacturing, other materials such as PP and PC/ABS also serve as viable alternatives for producing shell parts. While PP is a cost-effective alternative, its inferior gloss, hardness, and toughness compared to ABS may limit its application in certain contexts.
Mold Surface Quality: A paramount factor is ensuring the mold’s surface quality. The absence of scars, micropores, friction marks, or roughness is critical. Smoothing the cavity’s surface, and if necessary, utilizing chrome plating for polishing, can greatly enhance the final product’s appearance.
Based on the level of impact resistance, ABS can be classified into three categories. Each category has its own advantages and uses, and it’s not always the case that higher impact resistance is better.
The softening temperature (viscoelastic transition temperature) of ABS lies between 85 to 95°C, and its melting temperature (viscous flow temperature) is between 170-180°C. Therefore, its high-temperature resistance is not very good.
The two-shot molding process improves the final product in terms of feel, color, and functionality. There are many design opportunities to suit specific preferences. Examples of two-shot injection molded products include toothbrush handles, buttons, switches, caps and closures, and hand and power tools.
Poor Weather Resistance: A significant disadvantage of ABS plastic is its low weather resistance, especially when used outdoors for extended periods. It ages quickly under UV exposure, resulting in yellowing, powdering, and increased brittleness, which limits its outdoor use.
Recommended Drying Conditions: The recommended drying temperature for ABS is in the range of 80-90℃, and it’s advisable to maintain this temperature for a duration of at least 2-3 hours. This process ensures that the material’s humidity remains below 0.1%. Neglecting to dry ABS adequately can lead to issues such as water mist and silver streaks on the product’s surface.
Attention to mold quality, appropriate drying treatment, and meticulous control of injection parameters are vital for achieving superior surface quality and overall product performance.
Prominent brands that produce transparent ABS include 920 (Toray), TR558, 557 (LG Plastic), and Chimei’s PA-758 (Chimei Taiwan). This specialized ABS variant is favored for applications where transparency is a key requirement.
ABS, owing to its unique properties and processing capabilities, finds extensive applications across various industries.
Two-shot plastic injection molding is an injection molding process used to create multilayer, multicolor, or multi-material parts in a single process. This process is also sometimes referred to as two shot injection molding, 2-shot molding, 2K, multilayer, multi-shot injection molding, or multishot molding. Multi-shot manufactured products eliminate steps in the manufacturing process while creating a more cost-effective, enhanced finished product.
For bonding to occur, the two parts undergoing the two-shot molding process must be chemically compatible. Fabrik consults with customers and material suppliers to ensure proper material selection for the specific application.
Transparent ABS, also known as MABS or methyl methacrylate-acrylonitrile-butadiene-styrene plastic, is engineered by blending ABS with PMMA, resulting in a transparent and durable material.
ABS, a copolymer of acrylonitrile, butadiene, and styrene, derives its properties from these constituent materials. Acrylonitrile contributes strength, chemical resistance, and thermal stability, while butadiene enhances toughness and impact resistance. Styrene imparts high gloss, easy coloring, and smooth processing.
ABS, or Acrylonitrile-Butadiene-Styrene, is a versatile and widely used amorphous plastic material that results from the copolymerization of three key raw components. This remarkable material boasts an array of exceptional properties, making it a preferred choice for a diverse range of applications.
Injection Pressure: In typical ABS injection molding, the injection pressure generally falls within the range of 50-100MPa. This pressure range is often suitable for achieving the desired results.
These heat-resistant ABS variants have found wide-ranging applications in the fields of electronic appliances, home appliances, and automobile parts. Their ability to withstand elevated temperatures ensures product longevity and reliability in settings where heat tolerance is a prerequisite.
Commonly used materials for two-shot injection molding include thermoplastics, thermoplastic elastomers, and liquid silicone rubber.
In some scenarios, opting for modified ABS or alternatives such as PC (Polycarbonate), PC/ABS blends, or PP (Polypropylene) might be more suitable, as each material offers different advantages and disadvantages based on the application’s needs. The right choice of material is key to ensuring product performance and safety.
Gate Design: The type and location of the gate significantly influence surface quality. Inadequate gate design may complicate post-processing. Thoughtful gate placement is essential.
1. Home Appliances and Office Equipment: ABS is prominently used in the manufacturing of structural parts for a wide array of home appliances. These include juicers, rice cookers, kettles, and hair dryers, where the robustness and aesthetic appeal of ABS play a pivotal role. Similarly, in office equipment, ABS is often the material of choice for crafting typewriter casings, keyboards, and router casings, ensuring a balance of durability and design.
Acknowledging these disadvantages of ABS plastic is essential for its selection, taking into account the specific application environment, safety requirements, and cost-effectiveness.
Attention to these critical factors in the mold design and injection molding process will help ensure the production of high-quality ABS parts with the desired surface finish and physical properties.
Ordinary ABS can be susceptible to combustion, emitting strong flames, dark smoke, and a pungent odor during the burning process. It also produces harmful byproducts, including carbon monoxide and hydrogenated chlorine.
Chemical Stability Issues: ABS plastic’s resistance to certain chemicals like acids, alkalis, and oils is relatively weak, leading to potential corrosion or dissolution. This factor must be considered when ABS is used in environments exposed to harsh chemicals.
In contrast, heat-resistant ABS offers a solution with various grades capable of withstanding temperatures up to 120 ℃ without deformation or degradation. Notable examples include 777B, 777D, 777E from Chimei, HJ730 from Samsung and H2938 from Kumho. These grades are celebrated for their exceptional heat resistance, mechanical strength, and electrical insulation properties.
Injection Speed: In the ABS injection molding process, an overly low injection speed can result in insufficient plastic density and poor gloss on the injection molded part. Adjusting the injection speed to an appropriate level can enhance surface quality.
Molding temperature: Considering the melting temperature of ABS being 170 to 180 ℃, the injection temperatures typically range from 200 to 230°C for ABS, with variations among ABS types. Caution is needed to avoid excessive heat, which can lead to plastic decomposition. Mold temperatures generally range between 50 and 80°C, but for high glossy products, higher mold temperatures are necessary.
3. Toy Manufacturing: ABS is a staple material in the toy industry, renowned for its strength and versatility. Popular toys, including the iconic Lego building blocks, utilize ABS for its ability to withstand substantial impact and maintain intricate shapes.
ABS lends itself to various processing methods, including injection molding, extrusion, blow molding, and foam processing. Its surface is amenable to plating and painting, and the material is weldable, expanding its utility across diverse applications.
Flammability: A notable disadvantage of standard ABS plastic is its flammability. It tends to burn, producing a lot of black smoke, limiting its use in applications where high fire resistance is necessary.
With a density ranging between 1.05 to 1.18g/cm3, ABS exhibits a shrinkage rate of 0.4% to 0.9% and a hygroscopicity of less than 1%.
GETTING A QUOTE WITH LK-MOULD IS FREE AND SIMPLE.
FIND MORE OF OUR SERVICES:
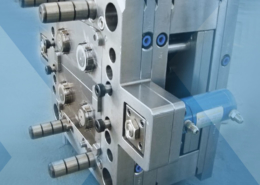
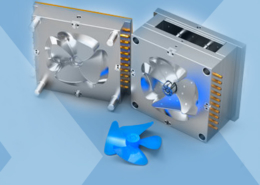
Plastic Molding

Rapid Prototyping
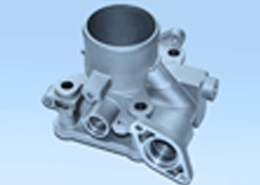
Pressure Die Casting
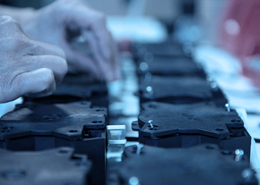
Parts Assembly
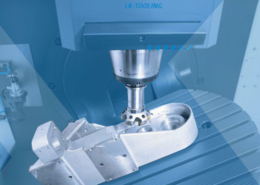