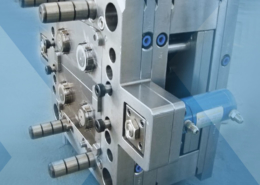
Automotive Injection Molding: How It is Used in Auto ... - automotive injection
Author:gly Date: 2024-10-15
3D Printing is an additive manufacturing method that builds a part layer-by-layer from a digital model. LVIM, on the other hand, is an injection molding process that injects molten material into a mold to create a part. 3D Printing can produce complex geometries, but the components may have poor mechanical properties. LVIM, on the other hand, can produce high-quality parts with excellent mechanical properties, but it could be more suitable for making large parts or parts with highly complex geometries.
Keyflex contact information: Australia Head OfficeAddress: U4/ 15 Rosslyn Street, West Leederville Western Australia 6007Phone: +61 (8) 9388 7366Email: sales@keyflex.com.auKeyflex contact information: Hong Kong office502 Golden Gate Commercial Building 136-138 Austin Road KowloonPhone: +852 8120 7299Email: info@keyflex.com.hk
The first step in the LVIM process is to design a mold that matches the part’s specifications. During production, manufacturers typically clamp together two halves of the mold. Designers create the mold to fit the part’s shape, forming a cavity filled with molten plastic material.
For more about a comprehensive guide of low volume injection molding for contract manufacturing low volume,you can pay a visit to Djmolding at https://www.djmolding.com/low-volume-injection-molding/ for more info.
LVIM is used in the consumer products industry to produce small batches of custom-made parts, such as smartphone cases, game controllers, and kitchen appliances.
Low Volume Injection Molding (LVIM) is a manufacturing process used to produce small quantities of high-quality parts. The process involves injecting molten plastic material into a mold cavity under high pressure, which cools and solidifies to form the desired amount. Manufacturers use LVIM for small production runs, prototypes, and custom-made parts. It is a cost-effective solution for producing parts that require high accuracy, intricate geometries, and tight tolerances.
CNC Machining is a subtractive manufacturing method that removes material from a block to create a part. LVIM, on the other hand, is an additive manufacturing method that injects molten material into a mold to make a part. CNC Machining can produce high-quality parts with excellent surface finish, but it’s more suitable for large batches. LVIM, on the other hand, is ideal for making small batches of high-quality parts quickly and cost-effectively.
Thermosets are materials cured through a chemical reaction, resulting in a rigid and durable part. They offer high strength, heat resistance, and dimensional stability, making them ideal for applications that require high-performance features. Examples of thermoset materials used in LVIM include epoxy, phenolic, and melamine.
LVIM offers the flexibility to use various materials, including thermoplastics, thermosets, elastomers, and composites. The choice of material depends on the specific application, performance requirements, and part complexity.
All plastic injection moulding items come in a wide range of colour options including most Pantone colours or silver-plating for a chrome look. Like all our products, plastic moulding can be created for a wide range of flexible designs and we can accept IGES, STEP, PARASOLID and other 3D formats or we can design the part to suit your requirements. When designing a keypad and plastic housing for your product, the ability to have the tooling and production of both parts done in one production plant eliminates problems created when one part does not fit correctly with the other, as the parts are carefully checked together during production, ensuring correct operation in the finished product.
Keyflex is a leading provider of high-quality plastic injection moulding solutions, offering a range of customised services for a variety of industries. Our team of experts in plastic moulding technology utilise state-of-the-art equipment and technology to ensure that each product is manufactured to the highest standards of quality and performance.
The part requires draft angles to eject it from the mold, and low draft angles may cause the part and mold to become stuck, resulting in damage.
1. Draft Angle2. Undercut3. Wall Thickness (too thick or too thin)4. Sharp Steel5. Draft angle of shut off area, the texture6. Shrinkage7. Miscellaneous Issues
LVIM is used in the automotive industry to produce small batches of custom-made parts, such as dashboard components, interior trim, and door handles.
LVIM is used in the medical industry to produce small batches of custom-made parts, such as surgical instruments, drug delivery devices, and prosthetics.
In conclusion, LVIM is an excellent solution for companies that need to produce small quantities of custom-made parts. Whether for prototypes, testing purposes, or low-volume production runs, LVIM offers many advantages over other manufacturing methods. With its ability to produce high-quality parts quickly and efficiently, LVIM will play a vital role in the manufacturing industry in the coming years.
The LVIM production process begins with the injection unit heating and melting the plastic material. The molten material is then injected into the mold cavity under high pressure, filling it and taking on the shape of the part. Afterward, the mold is cooled, and someone removes the piece.
The design should consider tolerances to ensure that the final part meets the required dimensions and tolerances. Tight tolerances may increase the cost of production, while looser tolerances may lead to elements that do not meet the required specifications.
When creating high-quality LVIM parts, it is essential to consider several design factors that impact the overall quality, functionality, and cost. Some of the critical design considerations for LVIM include the following:
Elastomers are materials that exhibit rubber-like properties, including high elasticity, flexibility, and resistance to deformation. Manufacturers commonly use them in applications that require seals, gaskets, and other flexible components. Examples of elastomers used in LVIM include silicone, natural rubber, and nitrile rubber.
Manufacturers combine two or more materials to form composites, creating a more robust and durable fabric. They offer excellent strength-to-weight ratios, resistance to impact, and other desirable properties. Examples of composites used in LVIM include fiberglass, carbon fiber, and Kevlar.
LVIM is used in the aerospace industry to produce small batches of custom-made parts, such as air ducts, interior trim, and control panels.
Cost-effective: LVIM is an economical solution for producing small batches of parts, requiring low tooling costs and minimal setup time. High accuracy: The precision of LVIM makes it an ideal solution for features that require high accuracy and tight tolerances. Flexibility: LVIM can accommodate a wide range of part geometries and shapes, making it a flexible solution for producing complex parts. Quick turnaround: LVIM has a short production time, which allows manufacturers to create pieces quickly and efficiently.
Designers should design the part geometry to minimize stress concentrations, minimize undercuts, and avoid sharp corners. These design features can lead to voids, sink marks, and other defects.
At Keyflex, we understand that each project is unique and requires a tailored approach. Our plastic injection moulding solutions are designed to meet the specific needs of our clients, providing them with the flexibility and reliability they need to achieve their goals. Whether you're looking for a one-of-a-kind solution or need to order in bulk, we have the expertise and resources to meet your needs. Browse our website today to learn more about our plastic injection moulding services and how we can help you bring your ideas to life
The next step is to select the appropriate material for the part. The choice of material depends on several factors, such as the part’s function, the operating environment, and the desired mechanical properties. LVIM can use various materials, including thermoplastics, thermosets, elastomers, and composites.
One of the key components of our plastic injection moulding process is our commitment to exceptional tooling. Our in-house tooling capabilities include the design, manufacturing, and maintenance of moulds, ensuring that each product is made to precise specifications. Our tooling is designed to be durable and efficient, reducing production time and improving the overall quality of each product.
Keyflex manufactures parts and tooling for a wide range of thermoplastic materials such as Polycarbonate, ABS, Polyester and blends. Our expertise means that we are able to advise which material is best suited to your requirements. Over-moulding with TPR gives a rubber feel and impact resistance while our high quality precision parts also have a tight tolerance.
LVIM has found applications in various industries, including automotive, medical, aerospace, and consumer products. Some notable examples of LVIM applications include:
Once the mold design and material selection are complete, the next step is to set up the injection molding machine. The machine consists of three parts: the injection unit, the clamping unit, and the control system. The injection unit heats and melts the plastic material while the clamping team holds the mold during production. The control system regulates the temperature, pressure, and other parameters during production.
The wall thickness of a part should be uniform to avoid warping, sink marks, and other defects. Thicker walls can also result in longer cooling times and higher cycle times, increasing production costs.
Thermoplastics are the most commonly used materials in LVIM, known for their excellent mechanical properties, durability, and ease of processing. Some common thermoplastics used in LVIM include polypropylene, polyethylene, ABS, and polycarbonate.
Article Original From: https://www.djmolding.com/a-comprehensive-guide-of-low-volume-injection-molding-for-contract-manufacturing-low-volume/
LVIM offers several advantages over other manufacturing methods, such as CNC machining and 3D Printing. CNC machining is a subtractive manufacturing process that involves removing material from a block of raw material to create a desired shape. While CNC machining can produce high-quality parts, it is unsuitable for making small batches due to high tooling and setup costs. 3D Printing, on the other hand, is an additive manufacturing process that builds up a part layer by layer. While 3D Printing is suitable for quickly producing small quantities of parts, it is not as accurate as LVIM and cannot deliver parts with the same level of precision.
GETTING A QUOTE WITH LK-MOULD IS FREE AND SIMPLE.
FIND MORE OF OUR SERVICES:
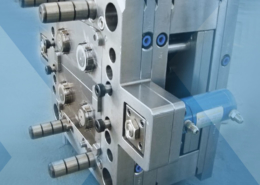
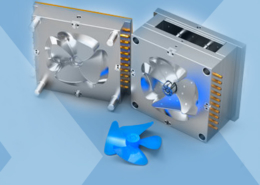
Plastic Molding

Rapid Prototyping
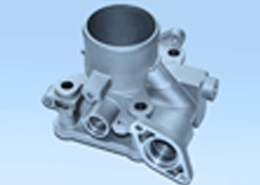
Pressure Die Casting
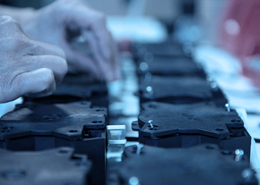
Parts Assembly
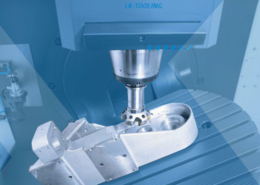