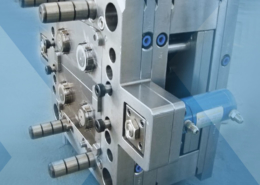
Australian Blowmoulding Corp Pty Ltd (ABC) - abc plastic moulding
Author:gly Date: 2024-10-15
PEEK can be processed through injection molding, extrusion, printing and compression molding. You should note that the processing conditions greatly influence the resin crystallinity thereby, also changing its mechanical properties. Let’s understand some of the processing guidelines for PEEK resins:
Plastech Corporation takes pride in serving the Midwest region as a trusted provider of injection molding solutions. With a strategic location and close proximity to major manufacturing sites in the upper Midwest, we offer a unique advantage to our customers in the midwest and central United States.
CF30 PEEK refers to a type of PEEK resin that has 30% of carbon fibers. The addition of carbon fibers greatly lowers its expansion rate and enhances the compressive strength and stiffness of PEEK. This grade provides greater thermal conductivity than natural PEEK thus, allowing for increased heat dissipation from surfaces.
GF30 PEEK refers to a type of PEEK resin that has 30% of glass fibers. The addition of glass fiber greatly reduces the expansion rate and increases the flexural modulus of the resin. GF30 PEEK is great for structural applications that require strength, stiffness, or stability, especially at temperatures higher than 148ºC / 300ºF.
The versatility and superior mechanical properties of PEEK resin make it an ideal choice for various industries such as medical, aerospace, mechanical, and automotive industries. In this article, we have conducted an in-depth analysis of PEEK injection molding material to help you understand whether it’s the best-suited material for your project.
PEEK plastic has distinct mechanical properties. It is thus a popular injection molding material It can be applied to a wide array of applications that include both, industrial and commercial industries. Let’s take a look at some of the sectors PEEK Plastic can be applied to:
At Plastech Corporation, we have extensive experience partnering with structural foam molding manufacturers and can help our customers obtain a range of foam molding services, from part design and mold fabrication to final production.
At Plastech Corporation, we understand the value of being geographically close to our customers. It allows us to build strong relationships, foster effective partnerships, and deliver exceptional service. Whether our clients are in the Midwest or beyond, we are committed to meeting their injection molding needs with quality, efficiency, and expertise. Contact Plastech Corporation today to experience the benefits of our Midwest presence and discover how we can serve as your reliable injection molding partner.
Plastic overmolding involves injecting molten plastic material onto a pre-existing metal part to create a composite part with enhanced features, such as improved grip or increased durability. The plastic material is molded onto the metal part by a second injection molding process, using a different mold than the one used for the initial metal part.
PEEK resins are very popular in the medical industry. PEEK is insoluble in most solvents. They also do not undergo hydrolysis, even at high temperatures. This property along with PEEK’s relative inertness to chemical reactions makes it a perfect resin for biomedical and dental applications.
Injection molding is a versatile manufacturing process that can produce a vast array of products across various industries. One of the key factors that contribute to the versatility of injection molding is the wide range of materials that can be utilized. At Plastech...
Unfilled PEEK is FDA-approved for food contact which is why it has a potential application in the food packaging industry.
This conversion process has applications in the automotive, electronics, aerospace, medical, and consumer goods industries. Metal to plastic conversion helps industries reduce costs, increase efficiency, and improve product performance. For example, plastic parts can be produced more quickly and at a lower cost than metal parts, leading to cost savings. Additionally, plastic parts can be designed with more complex shapes and features, resulting in improved functionality and performance.
Insert molding is an injection molding process that involves inserting a pre-formed component, typically metal or another plastic part, into a mold cavity and then injecting molten plastic around it to form an integrated part. The result is a part with a combination of materials and properties that cannot be achieved with traditional molding processes.
To better understand how VEM tooling can serve you for your PEEK injection molding project, contact us or request a quote today.
Client Profile A large manufacturer of dehumidifiers and air-handling equipment, used to control moisture and humidity in a wide range of commercial and industrial applications. Business Situation Demand for a specific client product line would surge following natural...
Our production capacity for injection molding varies depending on the project requirements. We have the flexibility to handle both small and large production runs, and our efficient processes allow us to deliver products in a timely manner.
Plastech Corporation is committed to serving customers around the world! We have planted out roots in the Midwest and have partners located throughout the United States. Globally, we are proud to serve customers in Canada, Mexico, South America, Europe, Africa and Asia.
Clear part molding is a specialized process that requires precision equipment and expertise to achieve the desired level of clarity and optical performance. The process involves careful control of the molding temperature, pressure, and speed to prevent the formation of defects such as bubbles, voids, or sink marks that can affect the optical properties of the part. The mold design and surface finish also play a crucial role in achieving a clear and smooth finish on the final part.
Plastech Corporation is a custom injection molder – but we actually do more than just mold parts. We are a full service contract manufacturer that collaborates with our customers to create customized project management solutions. That can include everything from engineering support to assembly, kitting, warehousing and order fulfillment, or as we call it, end-to-end manufacturing solutions. There are a lot of choices when you select a business partner, but when you choose Plastech, you get:
Plastech does much more than molding! We are here to be your partner from conceptual design all the way to mass production. To learn more, check out the additional services we offer:
In-mold labeling (IML) is a process where a pre-printed label or film is placed in the mold cavity before the plastic material is injected. The label is then fused with the plastic during the molding process, resulting in a seamless integration of the label and the plastic product.
PEEK is a very popular thermoplastic however, it is also not always suitable for every application. There are various considerations that one must take into account before applying PEEK resins to an application:
Tight tolerance molding is essential for producing high-precision parts, such as gears, bearings, sensors, and medical devices, which must function accurately and consistently under a range of conditions. We have the expertise and equipment necessary to perform tight tolerance molding to the highest standards, delivering parts that meet the most exacting specifications.
Natural PEEK is ideal for instrument components where aesthetics is a concern. In addition, it is also well-suited for plastic parts where ductility and inertness are important factors.
At Plastech Corporation, we have a wide range of capabilities in injection molding. We offer services such as design assistance, mold building, prototype development, production molding, assembly, and more. Our state-of-the-art equipment and experienced team enable us to handle projects of various sizes and complexities.
Both plastic and metal overmolding have various benefits, including increased product durability, improved grip and texture, and reduced production costs. These processes are commonly used in the automotive, medical, and consumer goods industries.
PEEK plastic exhibits excellent physical and mechanical properties. It is highly resistant to chemicals and thermal degradation. PEEK resins hold up well against high temperatures and long-term liquid submersion. In addition, they are also very durable in harsh environments.
PEEK polymers are manufactured through a chemical reaction known as step-growth polymerization. This is obtained through the dialkylation of bisphenol salts.
Injection molding can be used with a variety of materials, including various types of plastics, elastomers, thermosetting plastics, and even metals. The material selection depends on the specific requirements of the project.
Getting started with an injection molding project is easy. Simply reach out to our team at Plastech Corporation through our website or contact information. We will work closely with you to understand your project requirements, provide design assistance if needed, and guide you through the entire process from concept to production.
Most of our customers strategically source their products from nearby suppliers to reduce shipping costs and improve operational efficiency. Our close proximity to these industrial original equipment manufacturers (OEMs) within the upper Midwest has been a significant factor in our success. We have been awarded projects based on our ability to quickly respond to their needs and deliver high-quality products.
PEEK is a versatile injection molding material because the natural grade along with the reinforced varieties offers various properties that can be applied to a wide array of manufacturing projects. There are 4 major categories of PEEK:
Gas-assist plastic molding is useful for producing large, complex parts with thick sections or long flow lengths that are difficult to mold using conventional techniques. It is commonly used in industries such as automotive, appliance, furniture, and sporting goods, where lightweight, sturdy parts with complex shapes are required. Examples of parts produced using gas-assist plastic molding include automotive instrument panels, appliance handles, and furniture legs.
Clear part molding is a type of plastic injection molding process used to create transparent or translucent parts. It involves the injection of molten plastic material into a mold that has a polished cavity surface to create a part with a smooth and clear finish. The clarity of the part depends on the type of plastic material used, the mold design, and the molding conditions.
PEEK, abbreviated for Polyether ether ketone, is one of the most versatile and popular injection molding resins. PEEK is a high-performance thermoplastic that has an increased tolerance to gamma radiation exposure. It also demonstrates resistance to sterilization processes such as autoclaving which is why it’s ideal for manufacturing medical devices.
Tight tolerance molding is a type of injection molding process that is used to produce parts with exceptionally precise dimensions and tight tolerances. This process involves using advanced tooling and other specialized techniques to ensure that the final product meets the required specifications. Tight tolerance molding is useful in industries such as aerospace, automotive, medical, and electronics, where even the slightest deviation from the required tolerances can result in significant product defects, safety issues, or performance problems.
Mitigating costs is a major focus of our manufacturing processes at Plastech. If there are assembly, packaging, and testing operations that can occur during the cycle of the molding machine, we will always strive to complete them in process. This removes the need for a second cycle time which inflates the cost of your parts. Since our molding floor runs on a 24/7 basis, we can significantly increase output by moving secondary operations to occur beside the press during the cycle of the molding machine. Optimizing cycle times through manufacturing process improvements lead to lower costs for both Plastech and our end customers. Press side secondary operations is a win-win!
Clear part molding is commonly used in the manufacturing of products such as lenses, light diffusers, display screens, medical devices, packaging, and consumer goods, where the transparency or translucency of the part is required. The clear parts can be made from a variety of plastic materials, including acrylics, polycarbonates, and styrenics, among others.
At Plastech Corporation, we have extensive experience in insert molding and can provide our customers with a comprehensive range of services, from component sourcing and design to final part production. Our state-of-the-art facilities and experienced team enable us to deliver high-quality, precise parts with consistent accuracy and reliability.
Structural foam molding is commonly used in industries such as automotive, construction, and industrial, where large, complex parts with high strength and dimensional stability are required. Examples of parts produced using structural foam molding include automotive body panels, pallets, and shipping containers.
PEEK retains its mechanical properties at high temperatures which makes it an excellent electrical insulator. It thus can be applied to the manufacturing of electrical instruments that operate at high temperatures, such as soldering machines.
Structural foam molding is a specialized injection molding process that involves injecting a foaming agent into the molten plastic, which creates a cellular structure as the plastic cools and solidifies. This results in a part with a thicker, stiffer, and more rigid structure than traditional injection molded parts. Structural foam molding is useful for producing large parts with high strength-to-weight ratios, excellent dimensional stability, and reduced warpage, shrinkage, and sink marks.
At Plastech, we’re here to make your job easier. That’s why we offer a wide range of molding options, plus in-house value-added services to put the finishing touches on your project. We are proud to offer spin welding, sonic welding, hot plate welding, vibration welding, pad printing, hot stamping capabilities, plus kitting and assembly options. We also have a fully equipped tool shop to ensure your tooling investment is fully protected and well maintained.
This process eliminates the need for separate assembly processes and reduces the number of parts required, resulting in cost savings. Additionally, in-process welding and assembly can improve product quality by creating stronger, more durable products with fewer defects.
At Plastech Corporation, we specialize in gas-assist plastic molding and can provide our customers with a range of services, from part design and mold fabrication to final production. Our experienced team and advanced equipment enable us to deliver high-quality, precise parts with consistent accuracy and reliability, helping our customers improve their product performance and reduce their production costs.
PEEK (polyether ether ketone) is a part of the broader family of ketone polymers known as PAEK, abbreviated for polyarylether ketones.
Plastech Corporation serves a wide range of industries, including Outdoor Recreational, Appliance, Tier II Automotive, Agriculture, Industrial, and more. Our expertise in injection molding allows us to cater to the specific needs of each industry.
PEEK resins have extremely unique properties thus, 3D printing of PEEK allows the construction of almost any complex design geometry, which cannot be manufactured using other technologies.
Plastech provides a wide range of injection molding services to meet your specific needs. Our experienced team and state-of-the-art equipment gives us the ability to produce high-quality, precision parts for a variety of industries. At Plastech, we are committed to providing our customers with the highest level of quality and service in the injection molding industry. We operate on a 24/7 molding schedule that allows us to maximize capacity, complete high volume runs, and make a lot happen for you over the weekend.
VEM Tooling has the expertise for your PEEK injection molding project. At VEM Tooling, we offer dependable service and ensure that you have a great experience with a seamless manufacturing process.
The step-growth polymerization for the formation of PEEK polymers included reacting 4,4’-difluorobenzophenone or 1,4-bis(4-fluorobenzoyl) benzene with hydroquinone. This is done in the presence of alkali carbonates after which the PEEK polymer is isolated. The PEEK polymer is isolated by removing alkali metal fluoride and the polymerization solvent.
PEEK’s chemical name is Poly(oxy-1, 4-phenyleneoxy-1, 4-phenylenecarbonyl-1, 4-phenylene). The following diagram illustrates the chemical structure of PEEK:
Injection molding is a widely used manufacturing process for producing plastic parts and components. However, there are several misconceptions about injection molding that can prevent manufacturers from taking advantage of its many benefits. In this post, we will...
We have a rigorous quality control process in place to ensure the highest standards of quality for our injection-molded parts. This includes regular inspections, dimensional measurements, material testing, and adherence to industry standards and certifications.
Gas-assist plastic molding is a specialized injection molding process that involves injecting molten plastic into a mold cavity and then injecting pressurized gas into the center of the part to hollow out and pack the plastic against the mold walls. This results in a part with a hollow interior and thicker walls around the edges, which provides improved strength, rigidity, and dimensional stability while reducing weight, warpage, and sink marks.
Insert molding is useful for creating parts with complex geometries or assemblies that require multiple components to be combined into a single part. It is commonly used in industries such as powersports, automotive, aerospace, medical, and electronics, where the combination of different materials and components can improve performance, reduce weight, or simplify assembly. Examples of insert-molded parts include electronic connectors, automotive switches, and medical devices.
In-process welding and assembly is a manufacturing process used in plastics production where two or more plastic parts are welded or assembled together during the molding process. This process allows for the creation of complex plastic products with multiple components or parts. During the injection molding process, one or more plastic parts are assembled or welded together while still in the mold, either through heat or ultrasonic vibration. This helps reduce costs by minimizing the cycle time of the finished part. The result is a seamless integration of the various plastic parts, creating a single, unified product.
Our scientific molding approach can be flexible to the form, fit, and functional requirements of your parts. We process over 16 million pounds of thermoplastic resin each year across nearly 500 different grades. This experience has given us the knowledge to provide recommendations on material selection.
Injection molding offers several benefits, such as high production efficiency, the ability to produce complex shapes, cost-effectiveness for large production runs, and consistent quality and repeatability.
PEEK can be machined or injection molded to the nth degree of precision. As mentioned above, PEEK has several grades which makes it ideal for a number of applications in the automotive industry. For e.g. CF30 PEEK’s mechanical properties make it ideal to manufacture car components such as seals, washers, and bearings.
Yes, we understand that each project has unique requirements. We offer customization options such as color matching, texture selection, and material selection to ensure that the injection-molded parts meet the specific needs of our customers.
Metal overmolding, on the other hand, involves injecting molten metal material onto a pre-existing plastic part. This process can be used to create metal components such as inserts, connectors, or conductors, which are then integrated with plastic parts for improved functionality.
Standardization and quality are part of our companies core values. We deliver the best possible experience and product to our customers, every single time consistent. Take a look at our certificates!
Class A molding is a high-precision injection molding process that produces parts with a high-quality finish, smooth surface, and tight tolerances. This process is ideal for producing parts that require a premium aesthetic appearance, such as powersports and automotive exterior parts, consumer electronics, and medical devices. Class A molding requires advanced tooling, precise temperature control, and meticulous attention to detail to ensure that the finished product meets the desired specifications. At Plastech, we specialize in Class A molding and have the expertise and equipment necessary to deliver high-quality, visually appealing parts that meet our customers' exacting standards.
This process is commonly used for the production of plastic containers, such as food packaging and bottles, as well as other plastic products that require labeling or decoration. In-mold labeling provides several benefits over traditional labeling methods, including improved durability, increased efficiency, and the ability to produce more complex designs.
Yes, we have a team of experienced engineers who can assist with design and engineering aspects of injection molding projects. We offer design for manufacturability (DFM) services to optimize the design for efficient and cost-effective production.
PEEK resins meet safety and regulatory compliance and are thus an FDA-approved polymer. PEEK plastic can tolerate chemicals and exposure to extreme temperature ranges. Its often applied in the food packaging industry and in the production of oven parts.
PEEK Plastic is a popular injection material but we must note that it has advantages as well as disadvantages. Let’s understand them in-depth:
The IML process can also help reduce waste by eliminating the need for separate labeling and molding processes, and by allowing for the use of thinner plastic materials, which can reduce material costs and environmental impact.
PVX Black PEEK is reinforced with graphite and PTFE lubricants. This type of PEEK offers the lowest coefficient of friction and the best machinability of all PEEK grades. It is an excellent combination of low friction, low wear, high LPV, low mating part wear, and easy machining thus, making it ideal for plastic parts that are exposed to extreme environmental conditions.
Metal to plastic conversion involves replacing metal parts or components with plastic alternatives, which is becoming increasingly popular due to the numerous advantages of plastics over metals. Plastics are lightweight, durable, and cost-effective, making them suitable for a variety of applications in various industries.
Natural PEEK is an unreinforced general-purpose grade that is wear-resistant. As compared to the other PEEK grades, it exhibits the greatest elongation and toughness.
While we serve customers across the United States and even globally, our Midwest presence gives us a competitive edge when dealing with local businesses. Being nearby allows us to participate in competitive quoting opportunities more effectively. Our clients appreciate the convenience of having a trusted injection molding partner nearby, providing them with quicker response times, efficient communication, and streamlined collaboration.
GETTING A QUOTE WITH LK-MOULD IS FREE AND SIMPLE.
FIND MORE OF OUR SERVICES:
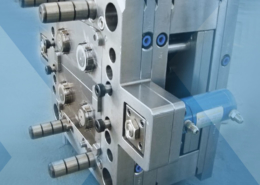
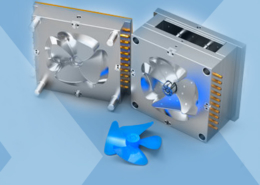
Plastic Molding

Rapid Prototyping
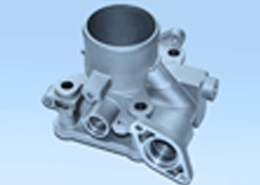
Pressure Die Casting
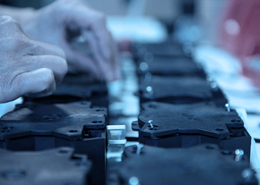
Parts Assembly
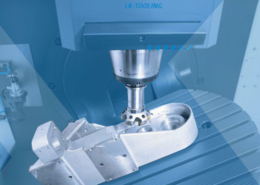