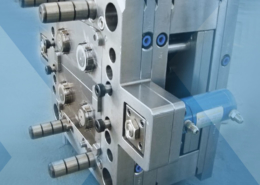
Atlanta Safti — Atlanta Industries Incorporated Logo - plastic molding for wire
Author:gly Date: 2024-10-15
The table below can be used to approximate the cost of plastic injection molding related to the most commonly used materials. These prices can vary, depending on the supplies and volume order.
Plastic injection molding is a process that many industries embrace and use widely thanks to its versatility. However, its popularity isn’t solely due to the quick production that’s possible with molding but also to the variability of the available materials. When manufacturers need to create products or parts with specific material properties, there are many injection molding materials to consider.
Mold setup costs include optimizing the process as well as physically setting up the materials and machinery to create your parts. These are part of the final price per part. The process will be optimized, and there may be some setup time that goes into preparations, which most companies will charge as its own flat fee. This may encompass processes like drying the resin, hanging the molds, arranging water lines, external troubles, and any type of sensors in the mold. It may also include any type of special cooling required or specific gating scheme that acts as a hot manifold system (which keeps runners hot enough to keep the plastic in them liquid).
Most common in industrial applications, TPU is a niche material that is best suited to molding heavy-duty products that will need to withstand a punishing environment. Despite its toughness, TPU molds easily and mold design is comparatively simple. TPU is also notable for its saltwater resistance.
As a manufacturer, it is preferable to maintain the cycle time to as low as a number as possible, since that translates into the production of more parts in a given time.
Trained personnel are required to validate the quality of the parts included in your order. Generally, however, if the part does not meet requirements (or expectations), the quality verification team of your provider is tasked with identifying the area and possible cause of the issue. This is, however, an internal process that is taken into account when you first make your order (no additional costs should be applied in this scenario).
Part packaging costs range depending on whether you require consumer-facing or just shipping packaging. Larger manufacturers can also make use of automatic packaging, which reduces the risk of error and damage.
You can either buy a ready-made injection mold or have one made for you. Ready-made mold use is a common practice and the less expensive option, especially in the electronics industry since standardization is quite prevalent. You can also have one produced for you, which is better for unique designs.
Mold cavitation cost, another factor in price per part rate, increases with the number of cavities. Cavitation is the amount of identical cavities that produce parts per mold. The injection mold itself can cost thousands of dollars.
The content appearing on this webpage is for informational purposes only. Xometry makes no representation or warranty of any kind, be it expressed or implied, as to the accuracy, completeness, or validity of the information. Any performance parameters, geometric tolerances, specific design features, quality and types of materials, or processes should not be inferred to represent what will be delivered by third-party suppliers or manufacturers through Xometryâs network. Buyers seeking quotes for parts are responsible for defining the specific requirements for those parts. Please refer to our terms and conditions for more information.
Plastic resins, which can range between $.90-$2+ per pound, are the primary material used in plastic injection molding, while additives can range from more expensive additives like heat stabilizers to cheaper plasticizers. When choosing a resin, take into account the following considerations:
TPR is a unique material that blends plastic polymers with rubbers, creating a material with the physical properties of both. TPR products exhibit a high degree of plasticity and can withstand long-term weathering. Also strong against chemicals, TPR is most common in hospital devices and tools.
Amorphous plastics have no order to the arrangement of their molecules. The random nature of the molecular structure means that these plastics soften gradually as the temperature rises rather than melting immediately. These types of plastics for injection molding produce results that are waterproof and highly receptive to bonding, and they are simple to form. Common examples include:
Part inspection requirements costs for quality can include standard inspection or specialized certification, though specialized certification will cost more. The injection molding process itself can introduce defects of various degrees to parts (from cosmetic to critical). Some of them may be acceptable, depending on industry standards.
Injection molding tooling cost increases exponentially if we are talking about a large custom-designed part. From the operator's perspective, it is preferable to use small (desktop) injection molding machines (and even 3D printers) in order to fulfill low-volume orders.
Saving money on injection molding can be helpful, but itâs important to be strategic around which areas you save money in. In order to maintain a cost-effective strategy for low cost injection molding, it is just as important to identify areas where trying to save money could cause bigger issues down the line as it is to find areas to lower the cost. The following tips will help you with both:
Set scrap rates will also go into the final cost of injection molding. These are for purging the plastic injection molding machines of previous plastics from the barrel and screws as well as reloading them with your plastic.
Injection molding cycle time takes up about 60% of final part cost. The part rate comes down partially to cycle time and partially to cavitation, which is covered in the next section. Generally, manufacturers will have set hourly rates they charge for their machines.
Injection molding tooling for a mid-level order (around 1000-2000 small parts), can cost up to $10,000. For more complex geometries and large orders, the cost can go up to $100,000.
Extra steps such as finishing or post-processing services, inspection, and packaging represent an additional cost to the price per part and setup fees.
POM is a material best suited for producing heavy-duty industrial plastic parts. It scores high marks in all categories, such as heat and chemical resistance, but it is also more difficult to work with at the molding stage. POM is in electrical devices, pumps and fan blades.
Mold cavitation is related to part size and design. If your part is relatively simple, single cavity molds are usually more affordable. However, if the part's geometry allows it, it is preferable to go for multiple-cavity molds to speed up the production process (making production less expensive over time). Larger parts may, however, not allow for this.
In this equation α is the thermal diffusivity coefficient and h max is the maximum wall thickness in millimeters. While the first is a material-specific constant, the latter is a design choice or requirement. As such, depending on the part's complexity, the cycle time can take up to two minutes.
Some parts may not need secondary services, while others do. The cheapest parts fall out of the machine and into a box, but others will form attached to the gate. Those require post-process machining to remove the gate, but they are used because gating makes the overall process more efficient and less wasteful.
Injection molding costs can vary depending on materials, equipment, mold cavitation, packaging, necessary certifications, and additional services employed. While your project may have strict requirements for the functionality of the desired part, there are multiple ways one can cut costs without sacrificing quality.
More commonly known as “polystyrene” or “PS,” HIPS contains materials beyond polystyrene. These materials, such as rubber, improve the impact resistance of a material that is otherwise very brittle. With its rigidity, some molding use cases for this substance include protective cases, such as those in use in hospital laboratories, medical devices or hardware tool chests.
Some companies offer the possibility of additional certification to your parts, at a cost. This implies the involvement of specialized engineers that are also licensed and are legally capable of offering these certifications.
With nearly a dozen different injection molding plastic types across three classes, there is an immense amount of variety to consider. Choosing the right injection molding materials is essential for product quality, budget planning and your long-term success. At Reliant Plastics, we leverage years of experience and an in-depth understanding of injection molding to assist your business.
One of the most durable plastic materials, polycarbonate can withstand significant deformation without breaking or even developing stress fractures. That trait made PC an obvious choice for the developers of the optical disc when CDs were first invented, but other uses include phone screens and eyeglass lenses.
The form impacts the cost of this material it is bought in, as not all polypropylenes are molding-ready. It is thus necessary to buy the plastic resin in pellet form. You may notice that engineering-grade plastics are generally more expensive (as with POM and PC). Overall though, the more materials you buy, the better your cost-effectiveness will become, as producers and distributors often have high-volume discounts which translate into better prices for your project.
Injection molding costs from $10,000 or less to $100,000, depending on order size, part complexity, and other factors. Injection molding can be expensive to set up, but is cheaper over the long run, so it works best for large production volumes. There is a range of factors affecting the final price you would pay for injection molded parts, including the cost of the resin itself, tooling, cycle time, mold cavitation, and other details.
What are the types of plastic used in injection molding? Understanding these options is a critical first step towards successful production planning. Learn about 11 of the most popular molding materials that comes from the three key types of plastic — crystalline, semi-crystalline and amorphous thermoplastics — and why manufacturers choose them.
Injection molded parts cost varies based on mold upkeep, the time to form a part, and factors around the plastic. These include the part rate, the estimated amount of scrap (usually 3-5%), the plastic weight, and sometimes a mold maintenance fee, which covers the cost of injection mold warranties. The quoted price should also include any setup costs for the molds.
If your provider is expected to deliver a ready or almost ready-to-use product, the packaging used may be the one your customers get to see directly. Some providers also offer personalized packaging services for this purpose.
Crystalline plastics get their name from the highly-ordered crystal structure that their polymers form. This dense structure gives crystalline plastics several key properties. They melt only at high temperatures, and typically, crystalline plastics have better chemical resistance properties and superior strength and stiffness, making them some of the most common plastics used in injection molding. Some of the most common crystalline plastics include:
A “semi-crystalline” plastic is a material in which a crystal structure is present, but it is not as rigid or as ordered as a true crystalline material. These solutions have many of the same properties as crystalline plastics but on a lesser level. A few typical semi-crystalline materials are:
If you want to impart special physical properties to the resin you're using, or simply defray the cost of using pure plastic resin, you can add additives. Commonly used materials like plasticizers and mineral fillers are among the cheapest that can be used, while products like lubricants and heat stabilizers can cost more than the polymer itself. There is a wide array of additives that impart a variety of properties, including glass fiber, ceramic fillers, pigments, UV stabilizers, plasticizers, and antioxidants. These materials can increase strength, impact resistance, durability, elasticity, and fatigue limit.
Let our team provide key insights to help you make critical decisions about materials, mold forms and more. Request a free quote on your project when you contact Reliant Plastics today.
Plastic weight cost includes both the plastic formed into parts and the hardened plastic left over in the mold. You'll also have to cover the cost of the plastic weight, not only in the parts but in the runner, sprue, and gate as well (the runner and sprue are channels molten plastic flows through to get into the mold, while the gate prevents plastic from flowing out once it's inside). For example, if you end up with 4lbs of parts, and 1lb of leftover plastic that hardens in the sprue and runner, you'll pay for 5 lbs.
Typically a part of applications such as tool housings, TV remote controls and other small, handheld tools or consumer products, ABS exhibits high strength and toughness without a correspondingly high material cost. ABS provides durability in products without adding a substantial amount of weight. The molding temperature of ABS influences its final characteristics.
However, to be able to do this, you should understand what exactly these areas are and how vital they are for your project. At Xometry, we offer the Xometry Quoting Engine to quickly get started on quoting your next injection molding project. Insert your requirements and designs into the Xometry's Quote Engine to get started and our experts will be in touch with you to start working out the details!
Tooling costs depend on how complex or large your parts will be. In other words, if your part is complex (for example, if it has intricate geometry or dense walls), the manufacturer may need to use a special (i.e. more expensive) machine to complete your order.
Sometimes referred to as high-density polyethylene, HDPE is highly resistant to both chemical exposure and temperature extremes. HDPE melts and molds very easily with excellent fidelity. HDPE is also well-known for how easy it is to recycle it. Many products made using injection molding use plastics such as HDPE.
Secondary services will range in cost, though often you can get a discount for ordering both injection molding and secondary services from the same provider (this also saves on shipping costs for another facility). These may come in the form of:
Commonly known as acrylic plastic, PMMA is not highly chemically resistant nor especially resistant to cracking. However, its brittleness is not a factor in its most common applications. Transparent and glass-like, acrylic appears in many applications, including in sports equipment, commercial food displays and lighted signs.
Besides physical properties, the color of the part can also be influenced, which is one of the most popular uses for additives. These providers will also sometimes establish partnerships with the thermoplastic producers to offer customers cheaper deals.
Another aspect to keep in mind is that for custom injection molds, the geometry has to be compatible with the machine used by the manufacturer. This constraint may affect your project (and possibly design), so it is best to make sure the company you are interested in can fulfill the order.
Also known as nylon plastic, polyamides exhibit high resistance to electricity and are heavily wear-resistant. Nylon parts are very suitable for high-stress environments, and in some cases, they can surpass comparable metal parts in performance.
Large, industrial plastic injection molding machines can cost over $200,000 and have additional costs that are related to skilled labor training, maintenance, monitoring, and even industry regulations. These types of machines are reserved for high-volume orders.
LDPE provides many of the benefits of PE/HDPE, but it is less stiff and more ductile. These traits make it well-suited to flexible plastic applications: consumers most commonly encounter LDPE in plastic bags or consumer-grade plastic water bottles. Like PE, it is easy to mold and cost-effective for appropriate projects.
Polypropylene is a common plastic in use in many industries, especially within commercial food applications due to its food-safe nature and for toys because of its affordability. PP does not perform as well in cold applications, but it does provide excellent hot water resistance for easy washing and sanitizing because of its high melting point. PP is not a very dense material.
GETTING A QUOTE WITH LK-MOULD IS FREE AND SIMPLE.
FIND MORE OF OUR SERVICES:
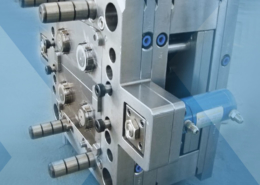
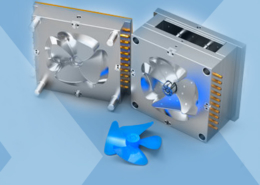
Plastic Molding

Rapid Prototyping
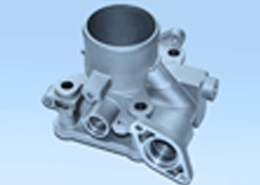
Pressure Die Casting
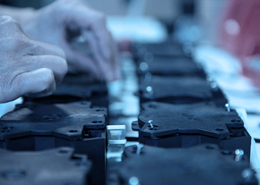
Parts Assembly
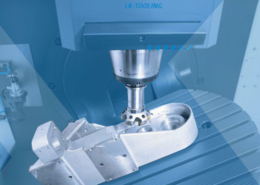