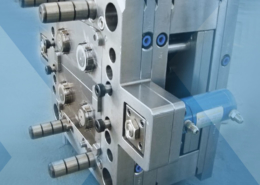
Unveiling the Potential of Injection Moulding Solutions
Author:gly Date: 2024-06-08
Injection moulding solutions represent a cornerstone in modern manufacturing, offering unparalleled versatility, precision, and efficiency. This article delves into the realm of injection moulding, exploring its applications, technological advancements, design considerations, sustainability aspects, and future prospects.
1. Introduction
Injection moulding stands as a pillar of contemporary manufacturing, revolutionizing the production of intricate parts and components across various industries. Its ability to produce complex geometries with high precision and repeatability has propelled its widespread adoption and continual innovation.
2. Applications
Injection moulding finds applications in diverse sectors, including:
Automotive:
From interior trims to under-the-hood components, injection moulding plays a crucial role in automotive manufacturing, offering lightweight, durable solutions.
Electronics:
The production of casings, connectors, and intricate parts for electronic devices relies heavily on injection moulding for its precision and scalability.
Medical:
Injection moulding facilitates the production of medical devices, equipment, and packaging with stringent requirements for quality, cleanliness, and biocompatibility.
3. Technological Advancements
Recent advancements in injection moulding technology include:
Industry 4.0 Integration:
The integration of IoT devices, automation, and data analytics into injection moulding processes enables real-time monitoring, predictive maintenance, and optimization of production parameters.
Advanced Materials:
The development of high-performance polymers, composites, and bio-based materials expands the capabilities and applications of injection moulding, catering to evolving market demands.
Additive Manufacturing Hybridization:
The fusion of additive manufacturing techniques with traditional injection moulding processes allows for the production of customized, on-demand parts with reduced lead times and tooling costs.
4. Design Considerations
Designing for injection moulding entails:
Draft Angles and Parting Lines:
Incorporating draft angles and minimizing parting lines in the design facilitates ejection and reduces the risk of defects such as flash and sink marks.
Gate Design:
Optimal gate design influences flow characteristics, part quality, and cycle time, necessitating careful consideration of gate location, size, and type.
Tooling Optimization:
Employing advanced tooling technologies, such as hot runners and multi-cavity molds, maximizes productivity, reduces cycle times, and enhances part consistency.
5. Sustainability
Addressing sustainability in injection moulding involves:
Material Selection:
Choosing recyclable, bio-based, or biodegradable materials minimizes environmental impact and promotes circularity within the supply chain.
Energy Efficiency:
Implementing energy-efficient equipment, processes, and resource management practices reduces carbon footprint and operating costs associated with injection moulding operations.
Waste Reduction:
Adopting lean manufacturing principles, regrinding scrap material, and optimizing part designs for minimal material usage contribute to waste reduction and resource conservation.
6. Challenges and Opportunities
Challenges in injection moulding include:
Material Innovation:
The quest for sustainable, high-performance materials that meet regulatory requirements and market demands poses challenges for material scientists and manufacturers.
Process Optimization:
Balancing speed, quality, and cost-effectiveness in injection moulding processes requires continuous optimization and adaptation to changing market dynamics.
Supply Chain Resilience:
Disruptions in the supply chain, whether due to natural disasters, geopolitical tensions, or pandemics, underscore the importance of building resilience and flexibility in injection moulding operations.
7. Future Outlook
The future of injection moulding hinges on:
Smart Manufacturing:
Leveraging artificial intelligence, machine learning, and digital twins to create autonomous, adaptive injection moulding systems that optimize performance and enable predictive maintenance.
Material Innovations:
Advancements in material science, including recyclable, bio-based, and self-healing polymers, will drive sustainability and performance improvements in injection moulding applications.
Circular Economy Initiatives:
Embracing circular economy principles, such as closed-loop recycling and remanufacturing, will foster a more sustainable and resilient injection moulding industry.
Conclusion
Injection moulding solutions epitomize the convergence of innovation, efficiency, and sustainability in modern manufacturing. By addressing design considerations, technological advancements, and sustainability challenges, the injection moulding industry can chart a path towards a more sustainable and prosperous future. Embracing innovation, collaboration, and continuous improvement will be paramount in unlocking the full potential of injection moulding solutions.
GETTING A QUOTE WITH LK-MOULD IS FREE AND SIMPLE.
FIND MORE OF OUR SERVICES:
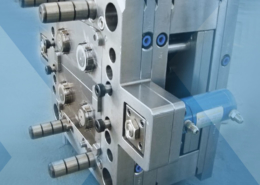
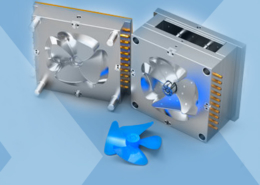
Plastic Molding

Rapid Prototyping
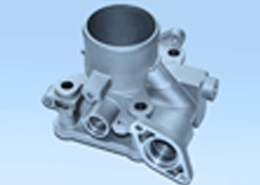
Pressure Die Casting
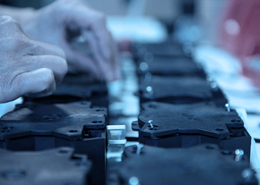
Parts Assembly
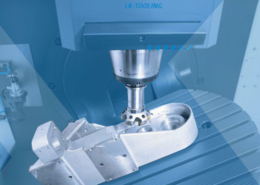