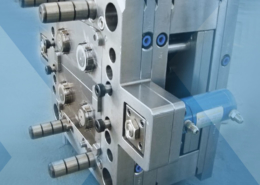
Unveiling the Dynamics of Injection Moulding Mould Cost: A Comprehensive Analysi
Author:gly Date: 2024-06-08
The realm of injection moulding mould cost stands as a critical factor influencing the feasibility, competitiveness, and profitability of manufacturing ventures worldwide. Delving into the intricacies of this essential component expenditure not only sheds light on the financial considerations of production but also unveils opportunities for optimization, innovation, and strategic decision-making. In this comprehensive exploration, we dissect the various facets of injection moulding mould cost, unraveling its significance, determinants, and implications for industry stakeholders.
The Significance of Injection Moulding Mould Cost
At the heart of every injection moulding operation lies the mould, serving as the cornerstone of production efficiency, product quality, and cost-effectiveness. The cost associated with acquiring, maintaining, and optimizing injection moulding moulds holds profound implications for businesses across diverse sectors, from automotive to consumer goods. Understanding the nuances of mould cost is essential for manufacturers seeking to maximize ROI, mitigate risks, and gain a competitive edge in the marketplace.
Factors Influencing Mould Cost
The cost of injection moulding moulds is shaped by a myriad of interrelated factors, ranging from material selection and design complexity to production volume and lead times. Material costs, including those of steel, aluminum, and specialized alloys, constitute a significant portion of mould expenses, with each material offering distinct advantages in terms of durability, machinability, and thermal conductivity. Moreover, the intricacy of mould design, such as the number of cavities, gating systems, and cooling channels, directly impacts manufacturing costs and cycle times.
Cost Optimization Strategies
In an era marked by fierce global competition and evolving consumer preferences, cost optimization emerges as a strategic imperative for manufacturers seeking sustainable growth and profitability. Adopting lean manufacturing principles, implementing design for manufacturability (DFM) guidelines, and leveraging advanced simulation and optimization tools can significantly reduce mould costs while enhancing production efficiency and product quality. Additionally, fostering collaboration with trusted mould suppliers and embracing agile manufacturing practices can yield substantial cost savings and operational agility in the long run.
Technological Innovations and Cost Trends
The landscape of injection moulding mould cost is continually evolving in response to technological advancements, market dynamics, and regulatory changes. Innovations such as additive manufacturing, rapid prototyping, and advanced mould coatings are revolutionizing traditional mould-making processes, offering cost-effective alternatives with shorter lead times and enhanced performance characteristics. Furthermore, shifting consumer preferences towards sustainable and eco-friendly manufacturing practices are driving investments in recyclable materials and energy-efficient production technologies, thereby influencing the cost dynamics of injection moulding moulds.
Market Dynamics and Competitive Landscape
The competitive landscape of injection moulding mould cost is shaped by a complex interplay of supply chain dynamics, global economic trends, and industry consolidation. Market volatility, geopolitical uncertainties, and raw material price fluctuations can significantly impact mould costs, necessitating proactive risk management and strategic planning by manufacturers. Additionally, the emergence of new market entrants, technological disruptors, and regional manufacturing hubs further intensifies competition, driving innovation and cost optimization efforts across the industry.
Conclusion: Navigating the Cost Maze
In conclusion, injection moulding mould cost represents a multifaceted challenge and opportunity for manufacturers seeking to thrive in today's competitive marketplace. By understanding the underlying drivers, adopting cost optimization strategies, and embracing technological innovations, businesses can effectively navigate the cost maze, unlocking new avenues for growth, efficiency, and profitability. Moreover, fostering collaboration and knowledge-sharing within the industry can facilitate the emergence of best practices and standards, driving continuous improvement and resilience in the face of evolving market dynamics.
As we chart a course towards a future characterized by innovation, sustainability, and resilience, the strategic management of injection moulding mould cost will remain a cornerstone of success for manufacturers worldwide. By embracing a proactive and holistic approach to cost management, industry stakeholders can not only enhance their competitiveness but also contribute to the advancement of the manufacturing ecosystem as a whole.
GETTING A QUOTE WITH LK-MOULD IS FREE AND SIMPLE.
FIND MORE OF OUR SERVICES:
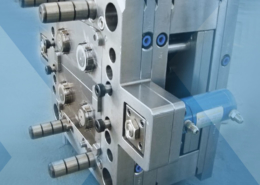
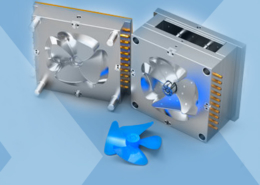
Plastic Molding

Rapid Prototyping
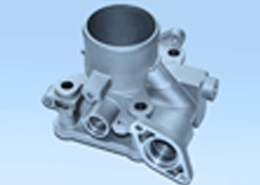
Pressure Die Casting
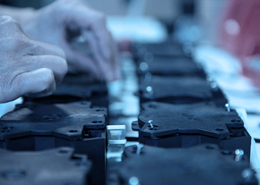
Parts Assembly
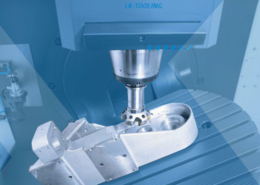