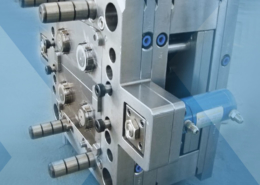
Alternatives to Molding with Teflon™ Thermoplastics - teflon injection molding
Author:gly Date: 2024-10-15
The mold is rotated first to a load station, then to a molding station, and ultimately to an unloading station on a rotary table vertical injection molding machine. Complex pieces can be manufactured on rotary tables, allowing for increased output.
A two-shot mold is a type of injection molding that allows different materials to be blended in one part. This technique can be used to provide durable plastic products with a softer feel, to color apart, or to create objects with varied performance characteristics.
TDLmould is one of China’s leading mold design and manufacturing companies established in 1995. TDL has established a strong presence in US. In collaboration with many local businesses, they offer top-of-the-line mold manufacturing solutions that are superior compared to other mold manufacturing companies in the region. The company specializes in mold design, manufacturing and injection molding with a strong commitment to providing high quality products and services to all its global customers. TDLmould uses a customer-oriented business approach with a team of experienced designers and engineers who take time to understand customer challenges, and come up with viable solutions tailor-made to each customer’s requirements. In developing their molds, the company uses steel sourced from reputable sources such as LKM, Gröditz, and ASSAB. TDLmould has the capacity of producing 570 mold sets annually, with 40% of the molds catering to the automotive industry and the remaining used in the medical and consumer electronics products. The company produces different types of molds depending on the applications. TDLmould leverages the expertise of their design team and the use of advanced mold manufacturing equipment to manufacture molds of utmost quality and reliability. The company has integrated a rigorous quality control system made up of modern testing equipment that ensures quality throughout the design and production of molds. TDLmould has earned several quality and standardization certifications including ISO 9001:2015, IATF 16049 and the POSI certificate for medical devices. In addition to mold manufacturing, this company offers other post-processing services including prototyping, surface finishing, CNC machining and components assembly. TDLmould is constantly improving its products and services through research and development to ensure customers get the best value for their money.
Understanding the changes and emerging trends in the mold manufacturing industry can help you determine the company that suits you best in your mold manufacturing projects. Each company uses different technology and offers different services. You should conduct deep research about each company for you to determine the company that best suits you.
MGS Manufacturing Group is a world class molding company that combines tooling, molding and automation to provide dependable molds worldwide. The company started as a small tooling shop in 1982. It has now grown and advanced in technology through its positive minded and ‘get it done’ attitude of its engineers and technicians to become a global mold manufacturing company. The company is guided by the values of teamwork, integrity and dedication which has enabled it to continually improve and deliver quality to its customers worldwide. The company’s mold manufacturing activities are carried out in one facility to reduce the costs and the risks associated with producing deformed molds, while ensuring quality assessment and control. The company has invested in sophisticated tooling, molding and automation technologies to ensure reliability and customer satisfaction.
3D printed custom injection molds are a time and cost-effective alternative for prototyping and low-volume production of about 10 to1000 components. They also offer a more agile production strategy, allowing engineers and designers to test mold design, readily tweak them, and then iterate on their designs far faster than traditional CNC machining, all while being orders of magnitude less expensive.
This method allows you to use two bottom mold halves with one top half. While one bottom half is molding with the top half, the other bottom half is available for insert loading. The bottom half of the press is filled with inserts and shuttles into position with the top half, while the bottom half molding shuttles out for part ejection and insert reloading when the press opens.
Knowing your application requirements which might change between prototyping and production is important when choosing the proper injection molding material. Any injection molding manufacturer will utilize a variety of plastics to achieve the finest results. Check them out below.
Pyramid Mold was established in 1987 as a tooling and mold manufacturing shop. The company grew overtime, attracting investors from different industries and getting mergers and acquisitions from different companies. With all these companies getting together, Pyramid Mold was rebranded and established as an advanced engineering and technology company called Synabridge Technologies in 2019. Sybridge Technologies is made up of more than 10 different companies that have merged to provide the best end-to-end manufacturing solutions. All the skills and talents combined under one umbrella, the company has the best equipment and latest technology in mold design and manufacturing, additive manufacturing, rapid prototyping, smart molding and custom parts manufacturing among others. The company has advanced engineering capabilities that integrate design, rapid prototyping and production on one platform to speed up the production cycle. Synabridge Technologies is ranked the top third mold manufacturer in North America with over 200 engineers and technicians, over 1000 employees in five countries and 18 production facilities. The company has many certifications such as ISO 9001, IATF and AIAG which reflect its excellence in top quality mold manufacturing.
Key advantages: Expertise in high-cavitation molds, advanced engineering capabilities, and top-quality mold manufacturing
R&D Tool and Engineering offers different services such as four slide tooling, automated machinery automation and assembly systems that increase your productivity by cutting the manual parts assembly time. Due to its expertise in complex molds and comprehensive mold design, and customer satisfaction R&D Tool and Engineering has secured several international companies as permanent clients.
Injection molding offers a wide range of manufacturing applications, particularly in the production of high-volume products. While tooling and molding can be costly, the cost of production after that is finished is inexpensive. Injection molding is utilized for parts made of a variety of materials since it allows for near-identical production. Bucket manufacturers use the same technique to come up with durable and strong products.
The mold manufacturing industry has been undergoing massive changes since the COVID-19 pandemic struck in 2020. There has been a growing gap in the need for mold manufacturing services because of the increased number of local manufactures and the demand for medical equipment in the country. Increased government budgets in healthcare has also made mold manufacturing a lucrative industry. This has led to many companies investing in mold manufacturing to cover the demand for these services. Apart from the medical industry, other industries such as construction, aerospace and the automotive sectors have also increased their demand for the mold manufacturing services and products.
Liquid injection molding entails the molding of stock materials into various components and products. It varies from traditional reaction injection molding in that it uses mechanical mixing instead of pressurized impingement mixing, and it concentrates on liquid silicone rubber and other elastomeric materials. Seals, o-rings, isolators, and electronic connections are just a few of the goods it can produce efficiently.
R&D Tool and Engineering is a family owned company that was established in 1972 in Cranston, Rhode Island. The company has been providing high quality molds for over 40 years with the goal of decreasing labor costs and increasing the profits. The company has an innovative leadership team that has invested in automation to minimize the costs associated with production. The company products are specialized in fourslide applications such as tail lights and door knobs. With its vast experience in the industry, R&D Tool and Engineering offers solutions that solve problems of its clients using locally available raw materials and quality automation. The company offers in-house turnkey molding systems and training sessions to help clients in the installation and operation of the molds and mold machines.
The primary purpose of tooling design is to provide a product that is easy to manufacture. To do so, a high-quality process that is simple and efficient, long-lasting, simple to operate and maintain, and capable of meeting all standards at the lowest possible cost is required.
It takes some money to set up a system for DIY injection molding. Getting the correct equipment and learning how to use it costs both money and time. However, because these prices are often less than the cost of a single metal mold, the time and money saved after you are up and running will readily compensate for the initial effort. You need:
The creation of the mold is the initial step done by most injection molding manufacturers. Most molds are finely machined from metal, usually aluminum or steel, to match the features of the product they will manufacture. The material for the part is fed into a heated barrel and combined using a helical curved screw after the mold has been made by the mold maker.
TechNH Inc is a family owned custom plastic injection molding company that was founded in 1995 in Nashua, NH. The company has now expanded to a team of 80 employees made up of engineers, technicians, mechanics and developers who are experts in plastic molding and technical engineering to help you design and materialize your ideas to plastic parts. TechNH Inc has partnered with other manufacturers who value compliance and cost-effectiveness in the production of plastic parts. TechNH Inc uses its team of experts to solve challenges that product designers face in molding complex parts. This team helps the client throughout the product life cycle from idea conceptualization, to the design, prototyping and production and marketing. TechNH Inc has precision mold manufacturing solutions that minimize your cost of production and deliver accurate and compliant molds quickly. The main services offered by TechNH Inc today are mold design, injection molding and mold making.
Injection molding machines are used by plastic injection molding service providers in the mass manufacture of complex-shaped plastic parts. Fast production speed, high efficiency, automatic operation, a wide range of colors, simple to complicated shapes, sizes ranging from large to small, and the injection molded part’s size is precise, the product is easy to replace, and injection molded parts with complex shapes can be molded are all advantages of injection molding machines. Let us go through the types of machines used in injection molding.
Extreme Tool & Engineering, Inc. is an innovative mold design and manufacturing company established in 1998. The company provides complete molding systems which include the mold design, product design and mold manufacturing. The company has a comprehensive mold process development that includes EOAT design, scientific molding and mold inspection to ensure that all molds manufactured meet the required specifications and standards. The company has heavily invested in the latest technology to boost its research & development creativity and expand its manufacturing capabilities. The company has very strict policies in commitment to quality and on-time delivery which earned the Leadtime Leader award in 2020. The company has employed automation in its manufacturing facilities helping it to stay on schedule in all its projects. Extreme Tool & Engineering, Inc. has an exceptional team that is fueled by a family-oriented but aggressive attitude which ensures that operations are made collectively with everyone hands-on.
When heated, a substance is squeezed or molded into a shape. Because the heating process alters the structure of certain materials, they cannot be reheated.
The names of the plastic injection molding materials sound like chemical words. Polyethylene rhymes with polypropylene, which has a similar acronym to polystyrene, which is challenging enough.
Horizontal injection molding machines are the workhorses of a wide range of plastics-based industries. Plastic parts created on injection molding machines ranging from 10 to 1000 tons are used in consumer products, electronics and telecommunications, food and beverage, medical, automotive, and other industries. Melted plastic is pumped into a mold to make a part in this manufacturing process.
Although vertical machines are used in a few specialty applications, such as insert molding, to make use of gravity, the majority of machines are horizontal. Plastic parts that can be affixed to or inserted into other materials are produced by vertical injection molding machines. A clamp is used on vertical injection molders to hold the mold from which the finished product will be manufactured.
Mold design and manufacturing is essential in most of the manufacturing industries because of its reliability and cost effectiveness regarding mass production and repeatability. In this post, we will explore the top ten companies offering the best high-quality mold manufacturing services.
Multi-shot molding is a procedure that involves injecting two or more plastic ingredients into a mold to make a part. This technique is commonly employed in the manufacture of toothbrushes. A two-shot technique in which two plastic components, usually a harder base material with a covering of softer material, are injected into a mold consecutively.
ACIS®, Autodesk Inventor®, CATIA® V5,Creo™ Parametric, IGES, Parasolid®, Pro/ENGINEER®,Siemens PLM Software’s NX™, SolidEdge®, SolidWorks®, STEP
By minimizing energy consumption, the electric press, also known as an Electric Injection Molding Machine, lowers operational expenses. It also addresses some of the hydraulic press’s environmental concerns. Manual presses are quieter, faster, and more accurate than electric presses, but they are also more expensive.
Key advantages: Comprehensive mold design and manufacturing services, expertise in complex molds, and a commitment to customer satisfaction
Mold-Tech Inc was founded in 1971 when mold manufacturing became popular as one of the most convenient and reliable methods of mass production. As technology advanced, the mold manufacturing industry became too competitive and through mergers and partnerships, the company was renamed to Standex Engraving. Mold-Tech now offers customized surface texturing and tooling performance for various industries which use molding machines. The company oversees the whole process from design and texturing to the production of molding tools. Mold-Tech uses advanced techniques of texturing such as chemical, laser and radar tech to ensure perfect end products. Mold-Tech has an excellent reputation of delivering quality through its team of experienced technicians and the wide variety of value addition services they offer.
Injection molding is a manufacturing technique that enables the large-scale production of items. Molten materials are injected into a mold to make it work. It is usually used to make thousands of identical things as part of a large production process. Metals, glasses, elastomers, and confections are all used in injection molding, although the most popular are thermoplastic and thermosetting polymers.
MSI Mold Builder was established in 1971 focusing on the design and manufacture of tailor-made molds for industries that make plastic products. The primary goal of the company was to manufacture plastic molds that are efficient, high-quality and low maintenance. Since its establishment, MSI Mold Builders have grown and diversified to manufacture molds from different products such as aluminum, steel and composite materials. The company has a team of experienced technicians and uses the latest technologies to ensure that it provides value for the customer. The main competitive advantage of MSI Mold Builders is dedication to customer satisfaction by building exceptionally durable and accurate molds and delivering within the shortest time possible. The company is committed to value addition by guiding and solving customer challenges in mold design to produce molds that exceed the customer expectations. MSI molding has invested heavily in the latest mold manufacturing machinery such as CNC mills, EDM machines, injection molding presses, milling machines, lathes, grinders and bridge cranes. MSI Molding Builders has also won a couple of awards such as Materials Handling Award in 2006, Best Overall Use Award and Lead Time Leader Award in 2011 and 2016
Many companies have ventured into mold manufacturing in America because of the increased demand in fast and cost-effective manufacturing of parts and components. Most of these companies have been evolving since the 1980s through technological change and advancement. You may be asking yourself “How do I choose the best mold manufacturing company?” Well, this article has highlighted some of the top companies that are reliable and dependable in mold manufacturing. Most of these companies have cutting-edge technologies and a team of engineers and technicians who are enthusiastic about their craft. You can visit this mold manufacturing homepage for more information.
Company Advantages: Provides customized mold design and production using a team of skilled engineers and state-of-the-art machinery. Known for producing quality and durable molds made from steel. Offers secondary services including prototyping, surface finishing and CNC machining.
Injection molding is a common manufacturing technique used to make the vast majority of plastic products on the market today. Traditional CNC machined metal molds have prohibitively high costs and long lead times for low-volume production, even though they are perfect for large-scale production needs.
The material in the barrel is melted by heating bands, and the molten metal or molten plastic is transported into the mold cavity, where it cools and solidifies to match the mold’s shape. Cooling lines that circulate water or oil from an external temperature controller aid in reducing the cooling time. Mold tools are installed on plate molds, which open once the material has solidified and removed the item from the mold using ejector pins.
Key advantages: Innovative mold design, commitment to quality and on-time delivery, and extensive manufacturing capabilities
Founded in 1993, StackTeck Systems Ltd is one of the top suppliers of complex plastic injection molding tools in America. StackTeck specializes in the design and development of injection molds and equipment to ensure reliable and dependable molding solutions to all its global customers. The team has an innovative research and development team which continually develops caps, PET preforms, thin wall packaging and medical molds for higher quality. The company takes time to understand the clients requirements and challenges to develop molds and molding systems that put them at a competitive advantage. All the molds and systems of the company are integrated for better control and quality assurance. The common services from StackTeck are part design, mold filling analysis, prototyping, refurbishment and repair of parts and service training.
The heart of injection molding is injection molding tooling. Plastic injection tooling, more particularly tooling design, impacts the quality of the injection molding process and the parts produced, whether it’s a complex application or a simple part.
GETTING A QUOTE WITH LK-MOULD IS FREE AND SIMPLE.
FIND MORE OF OUR SERVICES:
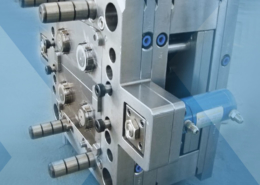
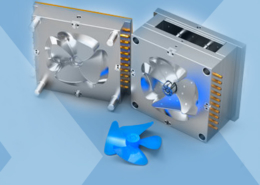
Plastic Molding

Rapid Prototyping
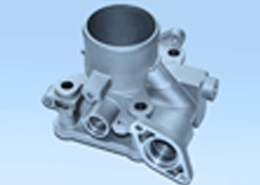
Pressure Die Casting
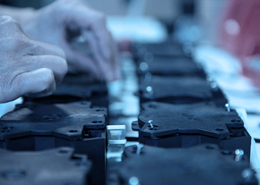
Parts Assembly
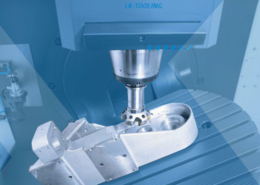