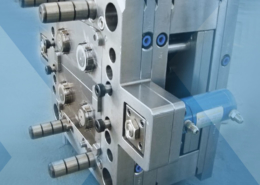
All About Short Run Plastic Injection Molding - The Toolroom Inc - short run pla
Author:gly Date: 2024-10-15
Our commitment to consistency has allowed us to serve manufacturers in the automotive, consumer goods, and electronics industries. As a seamless supply chain partner, we design and fabricate parts that meet your quality, lead time, and total cost needs.
Contact us today to learn more about polyethylene or any other commodity-grade material. If you’re ready to get started on your custom-made polyethylene components, request a quote. We’ll manufacture the mold you need to keep your application producing efficiently.
When you form a partnership with LMC Industries, our teams work to prevent problems proactively and create products that live up to your expectations as well as our own. Our engineers have nearly a century of combined experience with plastic overmolding and metal stamping services.
LLDPE shares many characteristics with LDPE but with several other benefits. Linear Low Density Polyethylene has an easy-to-adjust formula. This characteristic allows for lower energy usage during the overall production process.
Using a single supplier creates a leaner supply chain, making the entire workflow simpler and more predictable. Your job becomes more complicated every time you add another supplier to juggle, another contract to negotiate, and another invoice to process. Simplifying those workflows for your purchasing team boosts morale and can improve employee retention.
Combining multiple services eliminates at least one shipping step in your supply chain process, making room for dependent steps to move forward in the workflow. Optimizing your upstream operations will ultimately get finished products in the hands of your consumers that much earlier and more reliably. At the same time, you’re reducing your supply network’s carbon footprint and shipping costs.
By using a single supplier that is responsible for the end product, there’s zero diffusion of responsibility. There’s no chance of a blame game that has you and your team running back and forth looking for the root of a problem. Either you receive the correct parts and the quality is of an acceptable level, or you know exactly who is at fault. The increase in accountability dramatically reduces errors, and any problems that do occur are much easier to resolve.
LDPE is a highly flexible material. Its unique flow properties make it an excellent fit for shopping bags or other applications involving a thin plastic film. When strained, low density polyethylene will stretch, displaying this category’s high ductility and low tensile strength. LDPE melts between 110-130°C.
HDPE is an excellent option when you need a durable, stiff plastic that features a highly crystalline structure. HDPE is widely used and often chosen to manufacture milk cartons, laundry detergents, garbage bins, cutting boards, and more. High Density Polyethylene melts between 110-130°C.
As polyethylene is a thermoplastic, it responds to heat by becoming a liquid at its melting point. The specific temperature will vary depending on the chosen variety of polyethylene. Polyethylene materials can be melted multiple times, meaning that they are completely recyclable even after being used in an injection molding application. It is not recommended for applications requiring 3D printing.
At HiTech Plastics and Molds, we work with all the main types of polyethylene as an industry-leading injection molding manufacturer. As an ISO 9001:2008 certified company, we have the experience and knowledge to create high-quality custom plastic injection molded products that meet or exceed your strictest requirement.
HiTech Plastics and Mold is your go-to trusted injection molding manufacturer when you need polyethylene injection molded products. We work with all the main types of polyethylene as an industry-leading injection molding manufacturer. As an ISO 9001:2008 certified company, we have the experience and knowledge to create high-quality custom plastic injection molded products that meet or exceed your strictest requirement.
Finding a single company to handle sheet metal stamping and plastic overmolding services eliminates the need to transport parts between suppliers. A supply chain never benefits from the time spent shipping materials, even if everything ships and arrives on time. Once you start adding missed lead times and communication breakdowns, bottlenecks and delays become almost unavoidable.
With such a variety in polyethylene available for injection molding, the material can be altered and fit almost any industrial application. If you can imagine it, we can manufacture it. Common uses include:
There are three primary categories of polyethylene for injection molding: Linear Low Density Polyethylene (LLDPE), Low Density Polyethylene (LDPE), and High Density Polyethylene (HDPE). Each category has different characteristics, ranging from flexible to rigid, low impact to unbreakable. Which type is best suited for you will depend on your planned application.
Beyond the long-term benefits of reducing employee churn, there are immediate reductions in risk, administrative work, and expenses. When the process contains fewer steps and is easier to manage, the likelihood of costly mistakes is dramatically reduced. Even more immediately, the first visible benefit of working with a single profit center is often the associated cost reduction that comes with consolidating suppliers.
In addition to injection molding manufacturing, polyethylene is used in many of HiTech’s available services and secondary services. Molding processes that can take advantage of the different polyethylene varieties include:
Polyethylene is a semi-crystalline thermoplastic. As one of the most widely produced plastics in the world, it appears throughout virtually every industry. Polyethylene’s availability, versatility, and affordability make it a popular choice for injection molding manufacturers. PE is divided into categories based on density. In general, the higher the density, the higher the tensile strength, chemical resistance, and surface sturdiness. However, as polyethylene becomes denser, it also becomes more brittle in low temperatures. When solid, polyethylene is a non-toxic material.
Especially when combined with the superior quality that comes from increased accountability, enhanced ability to design for manufacturability yields clear enhancements to the finished product.
With more control over quality and more confidence in the manufacturability of parts, it becomes much easier for your team to focus on forward-facing projects.
Combining metal stamping services and plastic overmolding services is a win-win situation for manufacturing companies. When one partner can handle both plastic molding and sheet metal stamping, you’re able to streamline the supply chain and boost quality at the same time. Manufacturing companies often have to choose between superior products and faster workflows, but this is an opportunity to choose both, instead of sacrificing one for the other. These types of supply chain victories are made possible by selecting a supplier that can address multiple requirements simultaneously.
A single company that offers access to both metal stamping and plastic injection molding experts facilitates advanced design solutions to account for the nuances of both processes. For example, overmolded parts require tight tolerances to achieve a perfect fit. When the margin of error is measured in hundredths or thousandths of a millimeter, there’s no room for misunderstandings between teams.
Our team is involved from the ground up to create a molding solution to meet any requirement. We deliver high-quality products on time, every time. Read our case studies of past custom injection molded plastic projects to learn more about our work and what we can do for you.
Manufacturers may receive even more than these four benefits after combining sheet metal stamping and plastic overmolding. In many cases, meeting supplier optimization objectives opens doors to even more competitive advantages. By employing experts in the fields of plastic overmolding and metal stamping, you’re better able to earn the trust of your clients and their customers. If you’re ready to expedite your supply chain, eliminate lead time, and gain access to parts of a higher quality, it might be time to consolidate your suppliers.
Just as combining services under one roof boosts accountability, it also minimizes opportunities for communication breakdowns and the production of incompatible parts. Following the design for manufacturability (DFM) practice is one of the best ways to avoid wasting parts. Scrap parts are a waste of both time and resources, so eliminating them boosts the bottom line in two ways at once.
GETTING A QUOTE WITH LK-MOULD IS FREE AND SIMPLE.
FIND MORE OF OUR SERVICES:
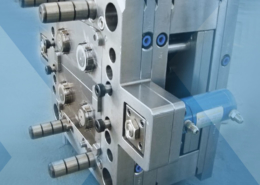
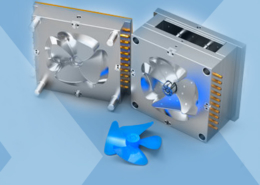
Plastic Molding

Rapid Prototyping
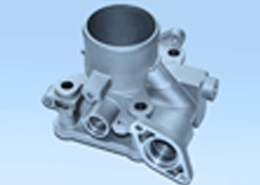
Pressure Die Casting
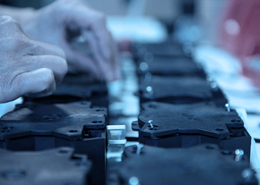
Parts Assembly
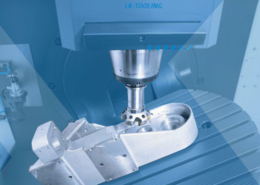