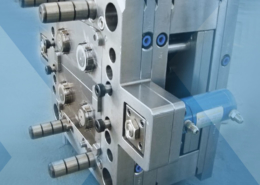
advantages of uhmw-pe compression molding - uhmw injection molding
Author:gly Date: 2024-10-15
At Enva we use cookies to provide an enhanced website experience, obtain audience insights, and customise adverts and content you see across websites and social media.
Prototype plastic injection molding can be done very quickly. The initial part will have the shape and functionality a plastic prototype part would need for testing form, fit, and function, but may not have fine details like color or surface finish preference. Prototype molds are built to handle minimum of 10,000 cycles.
ABS products produced by Enva customers include furniture fixtures and fittings, cable reels, pencil sharpeners, plastic drawers, under bonnet applications, automotive parts, cupholders, gear sticks, plastic container, kitchen unit feet, licence plate backing, TV housing, keyboards.
The current manufacturing trend is to use 3D printing to produce prototype parts. While 3D printing is a quick and efficient way to produce prototypes, it does have some serious drawbacks. Material choice is the biggest limitation when using 3D printing for prototypes. 3D printing can only use very specific materials that may not hold up to the demands of testing. Prototype injection molding will produce usable parts in the same material as the final part. This will allow designers to test the form, fit, and function of the part without worrying about differences in the material characteristics.
Fast Part Quote and Molding Low Cost, Quick Build, and Good Quality Online Project Management Trouble-Free Part Modifications No Size Limitations Any Commercially Available Material and most standard Surface Finishes
All projects are assigned a dedicated project manager and engineer to ensure your prototype injection molding project is done on time and in budget. For more information, please check out ICOMold’s Online Project Management System.
The use of recycled polymer provides injection moulders and other manufacturers with the ability to realise significant cost savings over the use of virgin material, whilst manufacturing a more environmentally friendly and highly marketable product.
PP polymers produced by Enva customers include pipe parts, school chairs, under bonnet applications, automotive parts, kitchen unit sockets, coat hangers, plastic drums, buckets, baskets.
PS & HIPS products produced by Enva customers include plant pots, coat hangers, mushroom trays, seed trays, planting troughs, footwear, wall plugs, cable caps, cable reels, storage contains, waterproof drums, fastening lips, identification tags, keyrings.
Prototype injection molding produces real injection molded parts for functional testing. Injection molding prototyping can also serve as bridge tooling to fill the manufacturing gap before production tooling or when production tooling goes down.
For manufacturers of commodity and technical products, the realisation of these benefits can be almost immediate. Recycled plastic has no impact on product quality and can be substituted into manufacturing processes without the need for additional process modifications or lengthy testing periods.
Prototype production is a necessary part of the injection molding industry because the costs associated with producing a prototype are significantly less than going straight to large scale production. Injection molding prototyping is a tried and true method for ensuring the mold is accurately designed prior to reproducing hundreds, thousands, or even millions of parts. Nothing can compare to the feeling of confidence that comes with holding a nearly finished version of your product before entering the production phase. This will ensure what you have designed and engineered will be exactly what you receive.
Cookies contain small amounts of information and are downloaded to your computer or other device (computer, smartphone, etc) by a server for this website. Your web browser then sends these cookies back to this Website on each subsequent visit so that it can recognise you and remember things like your user preferences. when you first visit a website. You can choose to not allow cookies used but blocking some cookies may impact your experience of the site.
A prototype mold is essentially the same as a production mold. It can produce the same parts as a production mold but is only warrantied for 10,000 cycles. Production molds will typically last for 100,000 cycles or more. The only real difference between prototype molds and production molds is the mold material. Prototype molds are made of softer steel that is easier to cut but does not last as long. ICOMold’s production molds are all made with high-strength steel and built to last.
Enva is one of the UK’s leading plastic recyclers, recycling around 80% of the plastic from mixed WEEE (waste electrical and electronic equipment) derived from Small domestic appliances such as toasters, kettles and vacuum cleaners. This consistent input material combined with the latest technologies enables Enva to produce extremely high-quality recycled polymers. All our material is REACH and RoHS compliant and material safety data sheets technical data sheets can be supplied on request.
Enva provides recycled Polypropylene (PP), Polystyrene (PS), High Impact Polystyrene (HIPS), and Acrylonitrile Butadiene Styrene (ABS) polymers to manufacturers across the UK. By purchasing directly from Enva customers can benefit from additional cost savings.
ICOMold’s fast-turn, low-cost, high-value injection molding enhanced by joining Fathom’s manufacturing platform. Learn More
GETTING A QUOTE WITH LK-MOULD IS FREE AND SIMPLE.
FIND MORE OF OUR SERVICES:
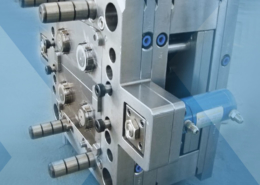
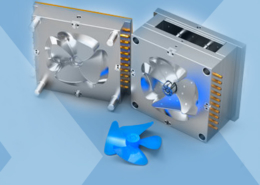
Plastic Molding

Rapid Prototyping
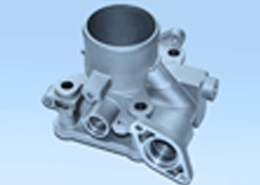
Pressure Die Casting
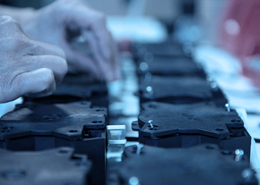
Parts Assembly
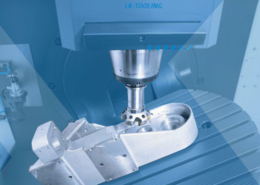