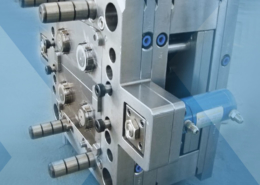
advantages of uhmw-pe compression molding - uhmw injection molding
Author:gly Date: 2024-10-15
Medical equipment. Overmolding is employed in medical device housings, enhancing durability and ergonomic design for instruments like handheld scanners and diagnostic tools.
Reduced assembly. Overmolding combines multiple components into a single piece, reducing the need for complex assembly processes, lowering labor costs, and minimizing the risk of assembly errors.
To get a quote for your overmolding project, start by uploading a part. You can also contact our injection molding experts with any questions or special requirements.Â
Venting. Integrate venting features in the design to allow air and gases to escape during injection, preventing voids and trapped air pockets.
In overmolding, a variety of materials can be used to achieve specific properties and functions. Several common combinations include:
Durability and protection. Overmolding can add a protective layer, such as a rubber coating, to shield delicate components from impact, moisture, or environmental factors, extending product lifespan.
What are the most common defects in the injection molding process and how do you avoid them? This article provides six essential design tips for avoid production defects while reducing the cost and lead time of your molded parts.
Overmolding involves placing an injection-molded part into a mold and injecting a second material to bond and create a single, integrated product.
Why is it important to design draft angles for injection molding custom parts? This article covers why draft angles are essential and how to design them better to get the most out of your injection molding designs.
Improved aesthetics. Different colors, textures, and finishes can be achieved through overmolding, enhancing the visual appeal of products and enabling branding opportunities.
Material compatibility. Choose materials that bond well together and have similar melting temperatures to ensure a strong and reliable bond between layers.
To obtain the desired surface finish and reduce residual stress, use a mold temperature in the range of 40-80°C, preferably as high within that range as possible. That said, using a higher mold temperature tends to lengthen molding cycle time, so use the mold temperature setting most appropriate for the individual product that is to be molded.
Ergonomic design. Overmolding enables the creation of ergonomic shapes and contours, enhancing user comfort and interaction, making products more user-friendly and intuitive to use.
Thermoplastic over thermoplastic. Using two different thermoplastic materials, such as a rigid plastic material like PC and a softer rubber-like material like TPU for improved grip or comfort.
Want to learn more about die casting? In this article, weâll take a look at the process, its history and current uses, advantages, design guidelines, and more.
Proper wall thickness. Maintain consistent and appropriate wall thickness to ensure even material flow and prevent defects like sink marks or voids.
A temperature setting in the range of 210-240°C is generally the most practical. Figure 3 shows the relationship between the cylinder temperature setting and the spiral flow length of TOYOLAC™.
Draft angles. Incorporate draft angles to aid in easy part ejection from the mold, reducing the risk of damage during demolding.
Limited material options. Material compatibility is crucial in overmolding, limiting the selection of suitable combinations â and potentially restricting the ability to achieve specific material properties.
Consider shrinkage. Account for material shrinkage differences between the injection-molded part and overmolded material to prevent warping or dimensional inconsistencies.
What are the common applications of injection molding? What sets it apart as a manufacturing process? This article covers the key benefits of injection molding and provides insight into whether injection molding is right for your industryâs applications.
Find out about the manufacturing technique used to injection mold a second material over or around a part to create a new one.
To reduce warpage and shrinkage, use sufficient injection pressure and holding time. Observe the appearance of the molded product to optimize injection pressure conditions.
Find out about the manufacturing technique used to injection mold a second material over or around a part to create a new one.
Applying the following best practices can help ensure successful overmolding, leading to high-quality products with optimal functionality and aesthetics.
Enhanced functionality. Overmolding allows the integration of different materials with distinct properties, resulting in improved grip, cushioning, insulation, or sealing, enhancing the overall functionality of the product.
Industrial tools. Overmolding improves ergonomics in handheld power tools, reducing operator fatigue and enhancing control during industrial use.
Ensuring proper material bonding, design intricacies, and quality control are challenges in achieving consistent overmolding results.
Tool design. Design molds with appropriate gating, runner systems, and cooling channels to ensure uniform material flow and efficient part production.
Thermoplastic over metal. Coating metal parts with a protective or cushioning plastic layer, such as encasing steel components with PP, to enhance corrosion resistance and reduce noise or vibration.
Construction. Safety equipment such as hard hats and tool handles benefit from overmolding, providing impact resistance and improved grip for construction workers.
Design for bonding. Create proper surface features, undercuts, and interlocking structures to facilitate mechanical bonding between the injection-molded part and the overmolded material.
Aerospace. Within aircraft interiors, overmolding enhances passenger comfort and cockpit functionality, seen in armrests, seat cushions, and control grips.
To obtain the desired ABS resin-molded product, preheat under appropriate conditions. Pellet water content should be no more than 0.1% (preferably no more than 0.05%) to obtain the desired molded product. When using a box-type hot-air dryer, dry at 80°C for 3-6 hours or 90°C for 2-3 hours. Figure 1 illustrates the drying curve for TOYOLAC™. Use higher drying temperatures than you would for standard grades to properly dry heat-resistant grade TOYOLAC™ or TOYOLACPAREL™.
In injection molding, âovermoldingâ refers to a process where multiple materials are used to create a cohesive, often multi-textured product with improved qualities and versatility. Hereâs a guide to using the technique, including how it works, its common industrial uses, and more.
Overmolding improves grip, durability, aesthetics, and reduces assembly steps, creating versatile and comfortable products.
What is Delrin and why is it unique among the many manufacturing materials available? Delrin, or POM-H (homopolymer acetal), is used in CNC machining, 3D printing and injection molding to create durable, precise components. This article explores Delrinâs properties and how to get the most out of the material.
Want to learn how to design undercuts that donât cause damage to your parts? Check out our article, which offers tips and tricks for DFM with undercuts, examples of when you might need them, and more. Undercuts in injection-molded parts present a host of challenges to designers and manufacturers. In this article, weâll take a look at the definition of undercuts, their purpose, applications, and tips for designing parts with them.
Level up your injection molding knowledge and find practical tips about selecting materials, working with draft angles, and reducing costs.
Various combinations include thermoplastics, elastomers, metals, and silicone, chosen for desired properties like grip, flexibility, or sealing.
Overmolded material placement. Position the overmolded material's injection points away from critical features and edges to avoid material entrapment or disruption.
To set molding conditions, consider such factors as the molding equipment being used, the size and shape of the molded product and the mold structure.
Silicone over plastic. Adding a silicone layer to a plastic material such as PC for water resistance, sealing, and enhanced tactile properties.
Thermoplastic over elastomer. Combining a rigid plastic such as ABS with a flexible elastomer for products requiring both durability and flexibility, like tool handles or medical devices.
 Overmolding offers versatile solutions to manufacturing challenges by combining different materials to enhance product functionality, durability, ergonomics, and aesthetics. The following are several of the advantages of overmolding.Â
Robotics. Overmolded grippers provide robotic systems with a balance of flexibility and rigidity, enabling secure handling of diverse objects.
Costly tooling and equipment. The need for specialized molds and injection molding equipment tailored to overmolding can lead to higher initial investment and tooling costs compared to traditional molding processes.
An ordinary resin mold can be used to form TOYOLAC™. Using a slightly larger gate and runner than what is ordinarily used to mold polyethylene or polypropylene resins produces even better results. Otherwise, no special measures need be taken as far as the mold is concerned. If the mold has a rough surface or an undercut structure, use a parting agent. Otherwise, a parting agent is unnecessary because TOYOLAC™ is relatively less prone to stick to the mold during molding. Mold shrinkage varies depending on molding conditions and product shape. Ordinarily, TOYOLAC™ mold shrinkage falls within the range of 0.4 to 0.6%. A draft angle within the range of 1/200 to 1/100 is preferred. See Table 2 for data on TOYOLAC™ mold shrinkage.
Learn what to consider when making a choice between 3D printing and injection molding, the benefits of each manufacturing method, and more.
Overmolding is a manufacturing process that is often used in injection molding, in which a part is encased or covered with a second material â typically a rubber or plastic â to create a single, integrated product. It enhances product durability, grip, aesthetics, and functionality.
In this article, weâll take a look at common factors that influence the cost of injection molding, including equipment, labor, and materials â as well as tips for reducing manufacturing costs.
Quality control. Ensuring consistent bonding between different materials can be challenging, and defects like delamination or inconsistent adhesion may arise, requiring meticulous quality control measures.
TOYOLAC™ possesses superb flowability and heat stability and is easily molded using ordinary injection molding equipment. Standard predrying and molding conditions are provided below.
Want to learn more about exactly how an injection molding machine functions, as well as its individual parts? This article puts injection molding machines under the microscope, with detailed descriptions of their components and an in-depth guide to the injection molding process.
Packaging. Overmolding contributes to the creation of ergonomic and comfortable grips on packaging machinery handles, improving operator experience and efficiency.
Complex design and engineering. Overmolding requires careful design considerations and engineering expertise to ensure proper material compatibility, bonding, and mold design, which can increase development time and costs.
Electronics. Overmolding ensures durability and strain relief for cable connectors, safeguarding cable connections in challenging environmental conditions.
Despite its advantages, overmolding presents challenges in terms of design complexity, material compatibility, production costs, quality control, and specialized tooling requirements. Learn more about the challenges in order to overcome them.Â
When producing parts with injection molding, understanding the range of materials that are available is crucial. Find out more about those materials, their properties, and factors to consider when choosing a material for injection molded parts.
Overmolding works by first placing the injection-molded part into a mold. Next, a second material is injected over or around the part. The two materials are then bonded together during the curing process.
Avoid sharp corners. Rounded edges and corners help prevent stress concentration and facilitate material flow during the overmolding process.
Process complexity. Overmolding involves multiple steps and material transitions, increasing the complexity of the manufacturing process and potentially leading to quality control challenges.
While tooling costs can be higher, overmolding often reduces assembly and enhances product lifespan, justifying the investment.
How do you optimize part design for injection molding? This complete guide to designing for injection molding provides basic and advanced design tips, including guidelines for creating snap-fits, living hinges and undercuts, and accounting for optimial surface finishes.
GETTING A QUOTE WITH LK-MOULD IS FREE AND SIMPLE.
FIND MORE OF OUR SERVICES:
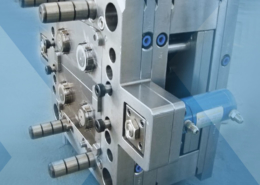
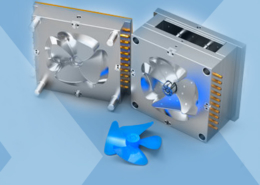
Plastic Molding

Rapid Prototyping
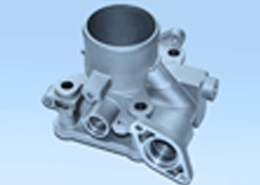
Pressure Die Casting
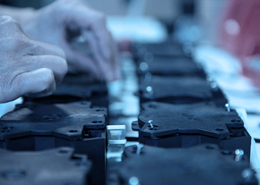
Parts Assembly
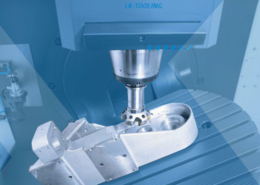