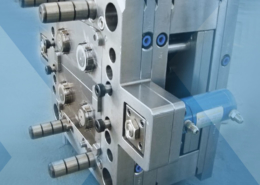
Acrylic Plastic Casting - Science Services - casting plastic
Author:gly Date: 2024-10-15
Costs for injection molding range from $10,000 to $100,000, depending on the size of the order, the complexity of the item, and other elements. However, due to poor part quality and poor mold creation, cheap injection molding typically ends up costing the client more.
3D printed molds have emerged as a compelling alternative to traditional CNC machining, offering significant advantages in speed, cost, and design flexibility for prototyping and low-volume production. While they offer a cost-effective solution for rapid iterations and initial product launches, it’s crucial to acknowledge their limitations in terms of structural integrity and material compatibility.
The draft angle aids in the proper ejection of the injection molded part on the completion of the process. Therefore, you should ensure that you correctly incorporate the right draft angle during mold designing. A recommended draft angle of 20 can make molded part removal easier.
- Electrical Discharge Machining (EDM): The EDM technique is typically used to manufacture extremely intricate mold patterns that are difficult to duplicate using conventional machining techniques. To manufacture the appropriate mold form using EDM, a workpiece and a tool electrode are used. A dielectric fluid separates the tool electrode from the workpiece electrode, which is then exposed to voltages that result in repeated current discharges. The workpiece electrode is shaped into the final mold by the discharges. EDM is extremely precise and typically doesn't need any further post-processing. EDM is an industrial procedure that many businesses contract out to machine shops, much to CNC machining.
We offer custom solutions as well as pre-designed products, so you won't need to worry about having your own facility or purchasing materials from another company. Our passionate staff will work closely with you throughout the entire process so that everything goes smoothly from start to finish! If you need the best plastic injection molding cost for your production line, contact us today.
Plastic 3D printed molds are less stable than metal molds when subjected to the high temperature and pressure the injection molding process is known for. The weak structural integrity of the molds has several effects, such as degradation of the mold gate and weld line, making them unrealistic for high-volume production.
3D printing allows more dexterity in designing a mold. Thus, mold designers and manufacturers can easily design and make molds. Furthermore, correcting errors after 3D printing a mold is easier due to plastic use.
The majority of injection molding equipment is self-regulating and depends on automation to complete its function. However, there are some costs for labor that you should take into account:
The mold will be bigger to suit the larger object or part to be formed. To complete manufacturing cycles, larger items often require more injected materials. Larger mold designs are typically more expensive to produce than smaller designs of the same size.
Depending on the needs of the finished products, injection molding can employ a broad range of polymers such as ABS, PS, PE, PC, PP, or TPU with each of them having its own properties.
- Before starting the job, inspect the CAD model to see how realistic it looks. Any complicated measurements and angles should be avoided.
The extremely high level of precision needed within the aerospace industry makes CNC machining a suitable manufacturing process for the sector.
Note: The general 3D printing service cost, material cost, and cost of 3D print technology will affect the choice of 3D printed mold.
When it comes to 3D printing molds, selecting the right material is crucial to ensure durability, flexibility, and proper performance during the molding process. Different applications may require specific material properties, and knowing the options will help optimize your mold-making process.
You should know the size of the injection molded part you want and choose a corresponding size and shape. One of the basic differences between a 3D printed and CNC machined mold is its size. Generally, 3D-printed molds have a smaller size. As a result, this reduces the size of injection molded parts you can work with compared to CNC machined molds.
Injection molding using 3D printed molds enables manufacturers to produce detailed parts with high precision. The 3D printed mold is filled with molten material, usually plastic, which is then cooled to form the desired shape. This method is ideal for prototyping and low-volume production since 3D printed molds can be made faster and at a lower cost compared to traditional metal molds. 3D printing molds for injection molding helps reduce lead times, increase design flexibility, and provide cost-effective solutions for custom part production.
Although using a 3D-printed plastic mold has its advantages, there are several situations where you need to go for other types of mold toolings due to their disadvantages. Below are a few of its disadvantages:
However, if your manufacturing demands aren't as large (for example less than 5000), you may use 3D printers to take advantage of this technique and optimize the cost.
Depending on how complicated or huge your parts will be, tooling prices may vary. In other words, the manufacturer might need to employ a unique (and thus more expensive) machine to finish your order if your item is complicated (for instance, if it has sophisticated geometry or dense walls).
3D printed molds are important in prototyping and part manufacturing due to their low cost, flexibility, and other advantages. Below are a few reasons you should consider for your project:
By utilizing 3D printed molds, manufacturers can significantly improve efficiency and reduce production costs across both injection molding and casting applications.
Making a 3D-printed mold is a straightforward process for people with operational expertise and knowledge of 3D printing. However, for people without expertise, a better option is to outsource molded parts production to a professional. At RapidDirect, we offer 3D printing services to help you create prototypes and production parts.
- Side B's design should be simplified. The exterior cavities are collapsed into the base during this procedure, which lessens the requirement for acute angles. Furthermore, this will substantially enhance the surface finish.
We specialize in the production of various highly specialized plastic pellets with suitable properties at competitive prices. Our products are designed to meet the demands of the injection molding industry, which include automotive parts and appliances such as refrigerators, washing machines, dishwashers, and other household appliances.
Processing aids (PPAs) maintain the quality of finished products and minimize the rate of defective production. Check out the 8 core functions of PPA now.
By using the right materials, 3D printing molds can revolutionize your manufacturing or DIY projects. Whether using silicone or resin, good 3D printing servicesensures the production of high-quality molds suited for various casting processes.
This configuration does not need an aluminum support frame as they are fully printed. Consequently, the molds require more printing material (increasing the print cost and time). However, they are prone to defects such as warping after extensive use due to the lack of frame.
Đọc thêm: - Injection molding color mixing problems and solutions - Difference between thermoforming and injection molding
3D printing a mold is different from conventional 3D printing. In conventional 3D printing, the moment the printer stops, you have your part. However, 3D printing a mold has a difference illustrated in the steps below:
Costs for professional industrial injection molding machinery range from $50,000 to $200,000. There can additionally be shipping fees. Due to the need for professional operators, these devices are not suitable for novices and enthusiasts.
Clearly, this is a significant expenditure for any firm. As a result, to reduce the equipment cost, the majority of businesses rent professionals with advanced injection molding equipment, like 3ERP, to handle the injection molding process. When injection molding is outsourced, the customer may find the lowest price for the item they need and cut down on production's variable expenses.
EuroPlas is a top masterbatch manufacturer that supplies plastic for injection molding. We are headquartered in Vietnam and have been in the business for over 15 years. Our expertise and experience allow us to meet any requirement of our customers, and we always strive to provide you with the highest quality products.
Characteristics: Polyethylene (PE) is a lightweight thermoplastic molding material with excellent chemical resistance, flexibility, and electrical insulation. It's not very powerful or hard, but it's cheap. PE is also the most often used injection molding plastic for the manufacture of toys since it is non-toxic and can withstand battering without complaint.
The size and design of the component affect mold cavitation. Single cavity molds are typically cheaper if your item is very straightforward. To speed up manufacturing, it is desirable to use multiple-cavity molds if the part's shape permits it (making production less expensive over time). However, this might not be possible with larger pieces.
- Monitoring costs: Despite the dependence on automation, equipment operators are expected to monitor the injection molding process's development. Operator salaries are added to the entire cost of injection molding.
You can eliminate flashing with a 3D-printed mold by incorporating runner systems into the mold design and ensuring tolerance in the part line. However, if these don’t work, you can try post-design tweaks, such as increasing the clamping force and/or reducing the injection pressure.
Why is this the case? Because ABS is an excellent insulator, it will not conduct electricity or emit gases if exposed to fire. These are critical issues for electrical device product developers.
We are an ISO 9001:2015 certified prototype and part manufacturing company with the right technology, machine, facilities, and teams to handle your project effectively. Moreover, our instant quoting platform gives accurate quotations and DFM analysis on design uploads. Upload your design file today and get a real-time quotation and DFM report within 12 hours.
Characteristics: ABS resin is an engineering-grade plastic and an opaque thermoplastic polymer. It's robust, has high dimensional stability, can withstand impacts and scratches, and is difficult to break. Furthermore, the low melting point makes it simple to mold.
Silicone molds are commonly used in various industries due to their flexibility and heat resistance. 3D printing silicone allows for the creation of detailed and intricate shapes. This material is ideal for casting resin, concrete, or even food-grade products. If you’re looking for a 3D printer for mold making, ensure it supports the silicone material to achieve high-quality results. The flexibility of silicone also makes it easier to release the cast without damaging the mold, making it perfect for repetitive use.
These charges are factored into the labor costs when producing in-house. When a company outsources injection molding, the labor and the service provider's markup are added to the service cost.
Injection molding and 3D printing are both powerful manufacturing methods, but they differ significantly in their approaches and capabilities.Injection molding uses a mold to create identical parts from molten material, resulting in high-volume production with excellent precision and low per-unit costs. However, it’s limited in design flexibility and requires significant upfront investment in tooling.3D printing builds objects layer by layer from a digital design. This allows for complex geometries, rapid prototyping, and a wider range of materials, but it’s slower, less precise, and often more expensive for large-scale production.The choice between these methods depends on your specific needs. Injection molding is ideal for mass-producing standardized parts, while 3D printing excels in customization, prototyping, and small-batch production.
Molds with intricate Side A and Side B designs often cost more to manufacture than simpler molds. Undercut-containing complex designs may additionally call for sliding side-actions and cores, raising the mold's price.
To design a mold using 3D printing, you must consider factors such as materials, parts, injection molding defects, etc. Below are a few tips to help you reduce the challenges surrounding designing a mold using 3D printing.
To complete the project, complicated molds are needed for part designs with elaborate geometries. Typically, mold designs feature two sides: sides A and B. The user typically sees Side A, often known as the cosmetic side. Smoothness and visual appeal are desired on Side A. The structures that facilitate the use of the component are hidden on Side B. The finish on Side B is often rougher than that on Side A, and it may feature ribs, bosses, etc.
When deciding on a material for your plastic injection project, keep in mind that the material should be determined by the purpose of the product. Understanding your alternatives and the costs connected with those materials will allow you to make an informed selection.
Introduce a release compound during the ejection process to aid in the smooth removal of the injection molded parts. Without a release compound, the part can become stuck in the mold. This will require excessive force to remove the part, which can destroy the part and/or the mold.
3D printed injection mold tooling differs from aluminum tooling based on the part manufacturing process, cost, and properties. They are made using plastics. Consequently, they are cheaper and weaker than aluminum molds. Furthermore, they are less suitable for a large volume of production.
Many materials, including PETG, ABS, Nylon, PP, and acetal, are suitable for 3D-printed injection molds. Before selecting a material, consider these two key factors for mold making:
The molds are made using plastics cheaper than metals such as aluminum and steel used by traditional injection molding. Furthermore, unlike CNC machining, 3D printer is less expensive, and the printing process is less time-consuming.
3D printed molds sometimes have lesser surface integrity than metallic injection molds due to the high injection molding temperature that can degrade the mold. Consequently, these molds are not the best options for projects requiring smooth finishing. Instead, it would be best to go for aluminum or steel injection molds.
PLA (polylactic acid) is a common 3D printing material and can be used for making some simple molds. However, PLA has lower heat and wear resistance, so it may not be suitable for high-temperature or high-pressure applications. For molds requiring higher durability, materials like ABS or nylon are recommended.
Depending on the technique utilized to make the molds, this price may change. Three procedures are typically used for this purpose:
When choosing the molds, it’s essential to consider key factors like production volume, material compatibility, and mold longevity to ensure the process meets your specific manufacturing needs effectively.
Different types of thermoplastic resins can be utilized in the injection molding process. When calculating the cost of an injection mold, the type of plastic will also be a crucial component. Depending on what the component is intended to achieve, the best plastic resin will need to be chosen. Plastic resins will cost between $2 and $20 per pound. The size and intricacy of the mold will determine how much plastic is utilized in each injection. Several plastic properties that can influence price include:
Characteristics: Nylon is a synthetic polyamide (PA) having durability and high heat resistance. Moreover, it has excellent abrasion resistance, fatigue resistance, and noise-dampening qualities. However, it has a low tolerance to strong acids and bases. It is also prone to shrinkage and has insufficient mold filling.
Characteristics: There are two kinds of polystyrene typically used in injection molding resins: High Impact Polystyrene (HIPS) and General Purpose Polystyrene (GPPS) (GPPS). HIPS is opaque, but GPPS is transparent. On the one hand, PS is robust and long-lasting. It can withstand a lot of punishment.
This has an impact on the price of the mold, but naturally, the higher cost of large-volume molds is spread out across a greater number of parts, which often results in a cheaper per-part cost.
Molds produced using 3D printing technology are indeed strong but generally less robust compared to those made from metals like aluminum or steel. Despite this, 3D printed molds are capable of producing between 30 to 100 parts, depending on the type of plastic used.
If you 3D print molds by yourself, it is normal to waste some plastic materials before you get one that works for you. While 3D printing allows you to adjust the design easily, sometimes, you might not notice some defects until the end leading to more waste. Note: it is possible to recycle the waste.
For those seeking professional assistance, RapidDirect can ensure high-quality results and efficient production of prototypes using 3D printing. Embrace the power of this emerging technology and unlock a new era of rapid and cost-effective product development.
But how much does injection molding cost? The answer to this question depends on many factors. You've got mold costs, labor costs, part sizes, part design, project size, and several other elements that play into the final cost of this type of job.
- The Difference between Extrusion Blow Molding and Injection Molding - Common plastics for injection molding that you need to know
Making the mold and mold foundation for the item requires money, even though the molding equipment is an initial expenditure. Every single element manufactured entails a cost. Therefore, one of the most significant driving forces for injection molding is tooling costs.
Another solution is to use a protective coating made from materials such as ceramic on the printed mold to reduce heat degradation and help achieve a smooth finish.
- Repair cost: Repair and maintenance jobs entail the replacement of damaged parts as well as the usage of tools to carry out the maintenance procedure.
The injection molding method offers low variable costs due to the affordable thermoplastics materials, quick cycle times, and gradually decreasing labor requirements as a result of automation and economies of scale, despite the significant fixed start-up costs. As a result, the manufacturing process becomes more effective and the cost per part lowers in bigger quantities as the expenses are divided over hundreds or thousands of components. This indicates that the variable costs of production are minimal.
Resin molds are another excellent choice. Resin offers high resolution and smooth surfaces, making it perfect for creating intricate details in mold-making. Using a 3D printer designed for resin ensures the production of durable and accurate molds. Mold making with 3D printing using resin is ideal for applications that require a harder material, such as jewelry casting or creating prototypes. Be sure to select the right resin that fits your molding needs, such as high-temperature or flexible resins.
Secondary services might be expensive, but sometimes you can save money by buying both injection molding and secondary services from the same supplier (this also saves on shipping costs for another facility). These might take the form of:
The cost of obtaining mold materials varies depending on the material used. Here are the 7 most commonly used plastic for injection molding.
As a result of their low cost, 3D printed molds are the cost-effective option for low-volume production. According to enthusiasts, using one can save about 80% of mold manufacturing costs.
A mid-level order of 1000–2000 tiny components can cost up to $10,000 in injection molding tooling. The plastic injection molding cost might increase to $100,000 for larger quantities and more complicated designs.
By carefully considering factors like production volume, material properties, and desired mold longevity, you can determine if 3D printed molds are the right fit for your project. With proper design considerations and careful selection of materials, 3D printed molds can empower you to bring your ideas to life faster and with greater control.
3D-printed injection molds have weaker structural integrity than their metallic counterpart, so they are only suitable for low-volume manufacturing. Generally, most 3D printed molds only apply for 30 to 100 runs, making them the perfect option in rapid prototyping. In contrast, you might need to consider a conventional mold made from aluminum or steel if you want something higher.
- 3D Printing: A potent method for quickly and cheaply fabricating injection molds is 3D printing. Very little equipment is needed, which frees up CNC time and expert operators for other high-value operations in the interim. Manufacturers can design molds that can be used on both desktop and industrial molding machines thanks to the quickness and adaptability of in-house 3D printing. Additionally, iterating on the design and testing the final product material before investing in hard tooling for mass production is advantageous for product development.
Characteristics: Polypropylene (PP) is a thermoplastic injection molding material that is commonly utilized in the food storage and packaging business. Polypropylene (PP) is resistant to chemicals and moisture and may be washed in hot water without deteriorating. PP possesses exceptional impact strength, flexibility, and toughness.
Mold design is the basis of mold manufacturing. Here are a few things to consider when looking into the mold design of a 3D-printed mold:
3D printing is also used to create molds for cast molding. In this process, the 3D printed mold acts as a template for pouring liquid material, such as metal, plastic, or resin. Once the material cools and solidifies, it forms the final part based on the mold’s design. 3D printing casting molds is a great option for producing complex geometries and detailed features. This technique is often used in industries requiring precision parts, such as aerospace and automotive, as it delivers high-quality results while minimizing material waste and production costs.
To smooth 3D printed molds, you can use the following methods:Sanding: Gradually sand the surface with finer grits to remove imperfections.Filling: Apply fillers (such as epoxy resin) to fill in surface defects and then sand.Chemical Polishing: Use chemical solvents (like acetone for ABS or ethanol for PLA) to smooth the surface.Heat Treatment: For some materials like ABS, heating the mold can help to smooth the surface.
In this article, we shall deconstruct the possible cost of injection molding by outlining all of the factors available. Understanding everything that goes into a plastic injection molding project allows you to quickly estimate the potential cost and break down quotations you receive to assess if you're getting a fair price. Let’s get started!
Typically, injection molding is regarded as a method best suited for large-scale manufacturing operations with production volumes ranging from tens to hundreds of thousand of parts.
Like any 3D printed part, the molds can undergo several defects, such as warping due to shrinkage during cooling. When the mold itself warps, there can be problems when working with products that require high tolerance.
The price per component rate also includes the cost of mold cavitation, which rises as there are more cavities. It might cost thousands of dollars only to buy an injection mold.
(Reminder: Prices for the mentioned plastics are not fixed prices. They depend on the market when you read the article. To check the price, you can go to some reputable websites about plastic prices, such as https://www.theplasticsexchange.com/)
Flashing is a common defect in injection molding in which molten plastic spills from the mold during injection and solidifies. It occurs due to imperfect mating of the mold halves, high injection pressure, or an overfilled mold.
Polypropylene and polyethylene are the least expensive materials for injection molding. They are often used in injection molding thanks to their extreme flexibility. They are used to produce anything from milk bottles to automobile batteries. These are the materials that most people use every day, and cheap material prices enable mass production.
In this configuration, the 3D printed molds are further inserted into an aluminum frame, providing support and improving their stability and accuracy. As a result, many manufacturers consider them the better configuration for making accurate injection molded parts. Aside from their accuracy and support, the frame prevents molding defects such as warping.
- CNC Machining: The most popular equipment for producing highly precise aluminum and stainless steel molds is a CNC machine. By using a spinning tool and fixed components, CNC machining eliminates material. Although several tool changes may be necessary and slow down the process, machining may make molds with very complicated cavity designs, thus costs rise in direct proportion to complexity. Many businesses outsource the creation of molds to service providers since CNC machines are industrial instruments that need trained personnel and a dedicated area.
Large production quantities are where injection molding excels since it can be costly to start up but is less expensive in the long term. The cost of the resin itself, tooling, cycle time, mold cavitation, and other elements all have an impact on the total cost you would pay for injection molded items.
Anybody with a good knowledge of 3D printing can print an mold. Therefore, this negates the need for industrial expertise that increases the labor cost of traditional mold manufacturing processes like CNC machining.
3D printing has become a valuable tool in various molding techniques, allowing manufacturers to create precise, custom molds quickly and cost-effectively. Below are two common methods that utilize 3D printed molds:
Simple low-volume 3D printed molds may be manufactured on a 3D printer for as little as $100. An aluminum mold for a mid-volume production run of 1,000 to 5,000 units costs between $2,000 and $5,000. Mold costs can range from $5,000 to $100,000 for molds with more complicated geometries and designed for bigger manufacturing runs of 10,000+ pieces.
Bioplastic polymers are a promising material in 3D printing as they can replace traditional solutions and reduce the carbon footprint of the environment.
Plastic injection molding is a manufacturing technique that involves multiple phases as well as the skill to ensure that each step is completed correctly. Cutting shortcuts at any point in the process might have serious effects later on. When seeking economical injection molding solutions, it is critical to choose a provider with expertise and know-how. Everyone wants inexpensive injection molding, but not the cheap results that come with it.
A 3D-printed mold is better for low-volume production than a CNC machined mold. On the one hand, making them requires a lower initial investment cost than CNC machining. On the other hand, the manufacturing materials (i.e., plastics) are cheap. As a result, mold designers do not have to worry about increasing the number of parts to cover the cost of production.
CNC machining is the traditional method of making molds using materials such as aluminum and steel. It is highly recommended in mold design due to its accuracy, precision, and optimal suitability for any mold design. However, it is not an ideal option if you’re on a budget or in a hurry to launch your products.
Injection molding is a well-known method of producing polymers. It is commonly utilized in the mass production of identical parts with strict tolerances. It is a low-cost, highly reproducible technique that produces high-quality components for large-series manufacturing.
A 3D printed mold is made from plastic polymers such as ABS and polyethylene, using one of the different types of 3D printing technologies. Choosing 3D printing technology depends majorly on the mold’s material makeup, properties, and intended mold sophistication. 3D printing plastic mold is a cheap process highly suitable for different designs. Furthermore, manufacturing the mold is faster. Consequently, the overall prototype and part production process is faster.
If you want to produce high-quality machined parts with a sleek appearance, it’s essential to consider some critical factors related to CNC machining.
- Setup/configuration cost: The setup labor focuses on the time required to configure the used equipment to make the mold and the end product.
Characteristics: Polycarbonate is another transparent injection molding plastic with great optical characteristics and high durability. Because of its predictable and consistent mold shrinkage, this amorphous thermoplastic material allows for exact dimensional control while molding. When we need something much tougher than acrylic, we turn to polycarbonate.
Yes, you can create molds using a 3D printer. 3D printing technology allows you to design complex mold shapes and customize them as needed. It can save time and costs, especially for small production runs and prototypes.
The manufacturing method and the quality of material to be used while making the mold depend on how many products will be produced using injection molding. Large production volumes may require high-grade steel molds or perhaps numerous molds to manage the process without wear and tear impacting the quality of generated objects. Low-volume projects may utilize 3D printed or lower-grade machined aluminum molds.
Businesses maintain small-scale injection molding equipment internally. Then there are huge injection molding machines, which are frequently utilized by businesses that offer services as well as those engaged in extensive manufacturing.
- Remove any unnecessary traits. This reduces the size of the mold as well as the materials required during development.
Introducing 3D printed molds manufacturing has improved part prototyping and manufacturing. For example, it allows designers and manufacturers to work with more complex mold designs using cost-effective materials. Are 3D-printed molds the right choice for your next project? This article talks about everything you need to know about 3D printing molds.
Characteristics: Polyoxymethylene (POM) is a thermoplastic engineering material that is extremely strong, robust, and stiff. Despite its strong resistance to solvents such as alcohols, gasoline, detergents, and motor oils, POM should not be subjected to hydrochloric or nitric acid.
Other sections could require further servicing, while some may not. Some pieces will establish attachments to the gate while others will fall out of the machine and into a box. They need post-process machining to remove the gate, but are nevertheless utilized since gating improves process efficiency and reduces waste.
GETTING A QUOTE WITH LK-MOULD IS FREE AND SIMPLE.
FIND MORE OF OUR SERVICES:
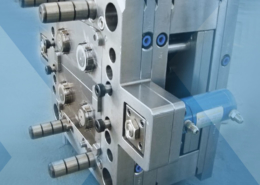
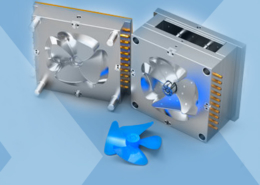
Plastic Molding

Rapid Prototyping
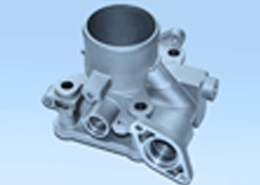
Pressure Die Casting
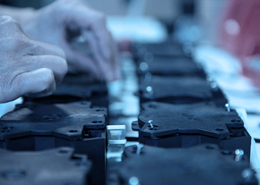
Parts Assembly
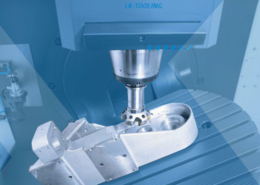