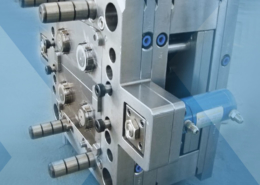
About rapid-acting insulin - rapid injection
Author:gly Date: 2024-10-15
You can build your molding tools using aluminum or steel. However, aluminum isn’t the best option when producing high-tolerance plastic parts. You should, therefore, use it when making low-tolerant components only.
Once a functioning, error-free mold has been created, the injection molding process is rather repetitious. It also has a low scrap rate when compared to other production processes such as CNC machine for mold making, which is a subtractive process that removes major chunks of the original material hollow.
Tools mold design, cavitation, and materials impact the plastic injection tooling tolerance. A simpler process is likely to get and maintain a tighter tolerance than complex parts because they can put tight tolerance at risk as there are other variables, such as the number of cavities, to consider.
Thousands of goods in the healthcare industry are manufactured using the injection molding technique. Because many of these product lines are single-use, disposable items used only to preserve sterility or stop the spread of pathogens or disease, the healthcare industry is dependent on multipurpose consumer products that must be produced in bulk. Plastic goods are widely used in the medical business. Medical plastic injection molding has enabled the production of considerably more productive, safe, and hygienic medical supplies and systems, such as syringes.
These are the most frequent products, with billions produced each year in a variety of forms and sizes. Because polyethylene terephthalate (PET) is both robust and light, it is commonly used to make plastic bottles that carry potable water and other beverages.
You may not realize it, but you are surrounded by injection molded materials in your automobile every day as you travel around. Car bumpers, dashboards, radio knobs, automated window switches, and cup holders are all built the same way, although performing distinct tasks.
Overmolding is the process through which the injection mold forms multiple layers around a single product. It does this by re-introducing the injection molded parts into the mold.
Because of the necessity of working with electrical parts, this sector needs perfect certainty and consistency. The polymers aid in encasing and protecting the wire, which can easily be damaged or cause injury to others.
Now that you know your mold qualifies, you can use it for mass production. This involves filling the various mold cavities with the molten plastics and giving it enough time to cool and solidify, taking the mold shape.
To understand how it works, you must have basic knowledge of the injection molds tools, what they are, how they work, where to find them, and which injection molding tools are best for specific tasks.
Injection molding is a popular production process for daily home products. Commercial, industrial, and consumer items are all covered by applicability. Injection molding allows for the creation of patterns with extensive detail or intricacy, as well as simpler shapes in a variety of sizes ranging from small to big things.
When the molten plastic molds, the clamping unit slides the B plate from the injection mold creating an exit point and pushing the plastic products out of the injection molds using ejector pins.
The next process in the injection molding tooling involves producing several test parts and measuring the properties and dimensions of the molded plastics to see if they meet the required specifications and standards.
The ejector mold or the B plate is the part of the injection molding tool that acts as the exit point through which plastic parts eject from the injection mold.
When we consider how many goods we use daily that are manufactured using the plastic injection molding technique, the list is infinite. Plastic is all around us and has become such an important part of our lives. They enable us to keep food safe, receive medical attention, and even perform simple tasks like brushing our teeth. We can see how essential the process is by examining how plastic impacts our lives.
Molded closures, jars, accessories, and kitchenware are just a few examples of typical home appliances that can be custom produced with injection molding.
Plastic injection molding, as complex as it may appear to a consumer, is a very common production method used to create a variety of everyday items. Plastic injection molding is used to assist in the creation of plastic products that we have adopted into our daily lives, regardless of how complex, excellently crafted, small or large they are.
Plastic products manufactured by mold making technology may be found everywhere around us. The injection molding method was used to create the bulk of the plastic goods and things we use daily. Injection molding is the most popular modern way of creating plastic components since it is perfect for generating large quantities of the same product in a short time.
The first stage in the injection molding process is the design creation and engineering. It involves creating a 3D CAD model of the injection mold and testing its performance, to see if it produces plastic parts with the desired shapes, sizes, and tolerance, using a simulation software.
Many people assume that plastic goods have only been in existence for a short period. However, molded plastic objects have been utilized in everyday life since the method was established in the 1870s. The method has been improved throughout time, and newer technologies have been developed to make it more efficient. Collar supports, buttons, and combs were created using the first plastic injection molding method.
Plastics are highly essential in the Medical and Life Science sectors since they are flexible, interchangeable, and hygienic for both clinical and lab use.
There are many types of injection mold you could use for your plastic injection molding process, but two-plate molding is the most used.
Another way to differentiate the plastic injection molding tools is through their feeding system, a collection of channels, including the runners, gates, and sprues, which direct the molten plastic into the mold cavity.
The process doesn’t end with a single production. You must maintain the injection molding to ensure it continues producing the high quality products. This means repairing worn parts, making needed adjustments, and cleaning it from time to time.
The overmolding process is simple. You start by molding the plastic products with a base-color material, ensuring you leave enough room to fit more plastic products with different colors.
One of the primary ways to differentiate injection molding is by the number of mold cavities. There are three different types of injection molds under this category. They include the following:
ACIS®, Autodesk Inventor®, CATIA® V5,Creo™ Parametric, IGES, Parasolid®, Pro/ENGINEER®,Siemens PLM Software’s NX™, SolidEdge®, SolidWorks®, STEP
The next step is to create a prototype mold to test the design. This helps you decide whether or not your model will give you the desired outcome. You can also use this stage to improve your mold design before it reaches the final stages.
To regulate the material flow flawlessly, injection molds have a highly accurate match between the two mold halves. The mold must be created to build a streamlined, precision commodity. Injection molds are generally made of steel or aluminum and carefully machined to produce the intended product’s characteristics.
Toys are one of the most popular injection-molded things seen in nearly every home. Plastic toy mold is ideal for producing children’s toys since it is considerably more resilient and can be bent, twisted, and frequently stamped on before major damage occurs. Another advantage of plastic toys is that they can be washed.
As mentioned, mold plates are one of the molding tools used to produce plastic containers. You can use the number of mold plates to differentiate various plastic injection tools. They include the following:
Tooling material selection is one of the most overlooked yet critical injection molding tooling designs. Your choice of material will significantly influence the lifespan of your injection mold tooling.
Now that you know how plastic injection molding tools work, you can start your project. It’s a pretty straightforward process to create plastic containers in large quantities within a reasonable time frame. It’s also affordable and will help you produce quality pieces within the shortest time possible.
The cavity image is an empty space in the injection mold that transforms the molten plastics to their desired shape and size.
Generally, this injection molding tool can have single or multiple cavities, depending on your production volume. Single-cavity molds are called single-impression cavity molds, while those with multiple cavities are called multiple-impression cavity molds.
The industry grew rapidly in the 1940s since World War II made a massive demand for low-cost, surplus-produced goods. James Watson Hendry, an American inventor, created the very first screw injection device in 1946. This enabled the materials to be blended before injection and offered more exact control of a uniform shot, assisting in the improvement of the quality of plastic goods produced.
Here’s where you produce the actual mold. You can use various materials, like aluminum and steel, and techniques, such as electrical discharge machining (EDM), CNC machining, or 3D printing to produce the molds.
There are plastics available in the market that are stronger than steel, more durable than nearly any substance on the planet, and reasonably affordable to make thousands of times over and over again: this is especially beneficial to the building and industrial industries.
Injection molding OEMs developing for the agricultural sector are shifting to plastic as a low-cost substitute for metal parts typically utilized in the industry. Plastics are more resistant to impacts during usage, humidity, and severe high and low temperatures. UV additives also aid in the protection of plastic parts against severe weather conditions and corrosive chemicals.
Generally, you’ll need sophisticated plastic injection molding tools to produce complex parts with added features like threads and undercuts. You may also require additional rotating mechanical gears in case of complex geometries.
Plastics have revolutionized the electronics we rely on every day, to the point where they have become an essential component of the electronics industry. When it relates to computers that are used by the majority of people daily, the displays, casing, keys, and other computer peripherals are all produced from injection molded plastics.
Finding the best manufacturing company for your custom injection molding process may be a little challenging. You must know the questions to ask and the response you need.
Plastic injection molding or injection molding is the production of plastic parts in large quantities using injection molding machines.
It’s the entry point that allows the melted plastic to pass through from the injection unit. The entrance of the injection mold is called the sprue bushing. They connect to runners, tunnels connecting the sprue to the cavity image.
This approach has resulted in the production of solid parts such as electronic enclosures, bottle caps, jars, computers, tv parts, patio furniture, agricultural goods, toys, industrial components, and many other items.
When using injection molding methods, electrical connectors and switches may be bulk manufactured. Almost your whole home’s electrical system is reliant on injection molded components to keep everything together.
The small opening created when a mold opens is called a gate. Plastic enters the mold cavities through these openings. There are two main gate types found in injection molds. They include:
The process for injection molding tooling isn’t that complicated. However, the process may vary depending on the products, materials, and specifications you want to meet.
An injection mold or A plate is a machined tool used in the plastic injection molding process. It molds the molten plastics into finished plastic goods.
GETTING A QUOTE WITH LK-MOULD IS FREE AND SIMPLE.
FIND MORE OF OUR SERVICES:
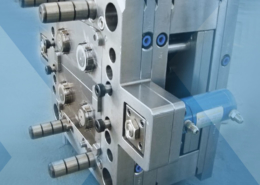
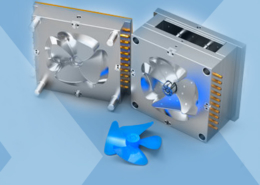
Plastic Molding

Rapid Prototyping
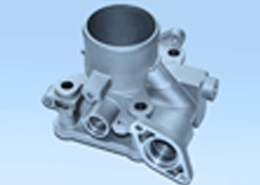
Pressure Die Casting
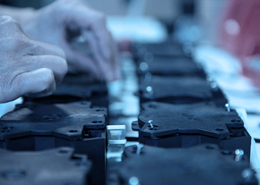
Parts Assembly
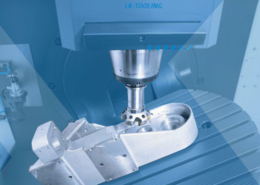