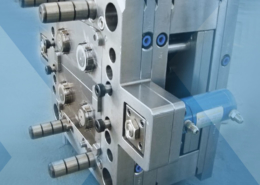
Exploring the Versatility of Injection Extrusion: Innovations in Plastic Manufac
Author:gly Date: 2024-06-08
Introduction
Injection extrusion, a cutting-edge process in plastic manufacturing, combines the principles of injection molding and extrusion to produce complex, high-quality components with precision and efficiency. This article delves into the intricacies of injection extrusion, shedding light on its mechanisms, applications, and potential for revolutionizing the industry.
Background Overview
Injection extrusion integrates the capabilities of injection molding and extrusion, allowing manufacturers to create parts with intricate geometries and varying cross-sections. This process involves injecting molten plastic into a preformed extrusion die, which shapes the plastic into the desired profile as it exits the die. With advancements in materials, machinery, and process control, injection extrusion has emerged as a preferred choice for producing components in automotive, construction, and packaging industries.
Mechanism and Operation
Injection Molding Phase
In the injection phase of injection extrusion, plastic pellets or granules are melted and injected into a preheated extrusion die using a reciprocating screw or plunger. The injection pressure and speed are carefully controlled to ensure uniform filling of the die cavity and prevent defects such as voids or air traps.
Extrusion Phase
Once the plastic is injected into the die, it undergoes a shaping process as it passes through the die channels. The die geometry determines the final shape and dimensions of the extruded profile, allowing for precise control over features such as thickness, width, and surface finish.
Cooling and Solidification
After exiting the die, the extruded profile undergoes cooling and solidification to maintain its shape and integrity. Cooling methods such as air or water quenching are employed to expedite the solidification process and minimize deformation or warping of the profile.
Advantages and Applications
Complex Geometry
Injection extrusion enables the production of components with complex geometries, including hollow sections, thin walls, and intricate features. This versatility allows manufacturers to meet the evolving demands of various industries, such as automotive fuel systems, window profiles, and medical tubing.
Material Compatibility
The compatibility of injection extrusion with a wide range of thermoplastic materials enhances its applicability across diverse applications. From commodity polymers like polyethylene to engineering plastics such as polycarbonate, manufacturers can select materials that offer the desired mechanical properties, chemical resistance, and aesthetic qualities for their specific needs.
Efficiency and Cost Savings
By combining injection molding and extrusion into a single process, injection extrusion offers significant efficiency gains and cost savings compared to traditional manufacturing methods. The elimination of secondary operations and the ability to produce complex parts in a single step reduce lead times, labor costs, and material waste, contributing to overall competitiveness and profitability.
Challenges and Future Directions
Process Optimization
Continued research and development efforts are focused on optimizing process parameters and die designs to enhance the quality and efficiency of injection extrusion. Advanced simulation tools, process monitoring systems, and material formulations enable manufacturers to fine-tune their processes and address challenges such as melt flow control and die swell.
Material Innovation
Advancements in material science play a crucial role in expanding the capabilities of injection extrusion and unlocking new applications. Research initiatives focus on developing specialized materials with tailored properties, such as enhanced melt strength, rheological behavior, and adhesion, to meet the evolving needs of high-performance industries.
Integration with Industry 4.0
The integration of injection extrusion with digital technologies, such as IoT, AI, and machine learning, holds promise for optimizing process control, predictive maintenance, and quality assurance. Smart manufacturing solutions enable real-time monitoring of process parameters, proactive identification of issues, and data-driven decision-making, leading to improved productivity and sustainability.
Conclusion
In conclusion, injection extrusion represents a paradigm shift in plastic manufacturing, offering unparalleled versatility, precision, and efficiency in producing complex components. By leveraging advancements in materials, machinery, and digital integration, manufacturers can unlock new possibilities for product design, functionality, and sustainability across diverse industries. Looking ahead, continued collaboration and innovation will drive further advancements in injection extrusion, shaping the future of plastic manufacturing and product development.
GETTING A QUOTE WITH LK-MOULD IS FREE AND SIMPLE.
FIND MORE OF OUR SERVICES:
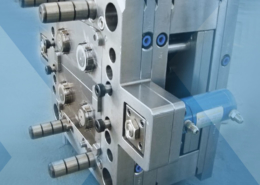
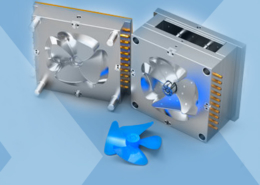
Plastic Molding

Rapid Prototyping
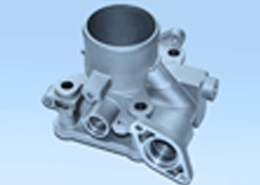
Pressure Die Casting
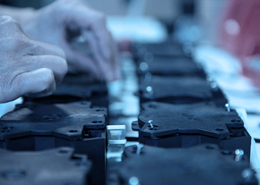
Parts Assembly
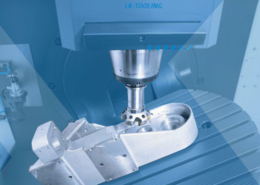