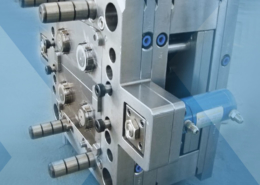
Exploring the World of Industrial Moulds
Author:gly Date: 2024-06-08
Industrial moulds are the unsung heroes of modern manufacturing, enabling the mass production of a vast array of products that we rely on every day. In this article, we delve into the fascinating world of industrial moulds, from their inception to their contemporary applications and future possibilities.
Introduction: Unlocking the Potential
Imagine a world without industrial moulds - a world where every product, from the simplest household item to the most complex automotive component, had to be painstakingly crafted by hand. Industrial moulds have revolutionized the manufacturing process, making it possible to produce high-quality, consistent parts with remarkable efficiency and precision. Join us as we explore the inner workings of these essential tools and their impact on modern industry.
Origins and Evolution
Early Beginnings
The origins of industrial moulding can be traced back to ancient civilizations, where rudimentary moulds made from clay, stone, and metal were used to shape objects such as pottery and metalwork. Over time, advancements in materials and techniques led to the development of more sophisticated moulding methods, laying the foundation for modern industrial moulding processes.
Technological Advancements
The industrial revolution marked a turning point in the evolution of industrial moulds, with the advent of mechanized production techniques and the introduction of materials such as cast iron and steel. The 20th century witnessed further advancements in mould design and fabrication, driven by innovations in materials science, engineering, and automation.
Digital Transformation
The dawn of the digital age brought about a revolution in industrial moulding, with the integration of computer-aided design (CAD), computer-aided manufacturing (CAM), and additive manufacturing technologies. These digital tools have revolutionized the design and fabrication process, allowing for greater precision, complexity, and customization in mould production.
Types of Industrial Moulds
Injection Moulds
Injection moulding is one of the most widely used manufacturing processes, employing precision-engineered moulds to produce plastic parts with high accuracy and repeatability. Injection moulds consist of two halves - the cavity and the core - which are precision-machined to form the desired shape of the final product.
Die Casting Moulds
Die casting is a process used to produce metal parts by forcing molten metal into a mould cavity under high pressure. Die casting moulds, also known as dies, are typically made from hardened steel and can withstand the high temperatures and pressures associated with the die casting process.
Compression Moulds
Compression moulding is a versatile manufacturing process used to produce parts from thermosetting plastics, rubber, and composites. Compression moulds consist of two halves - the upper and lower mould plates - which are brought together to compress and shape the material into the desired form.
Applications and Impact
Automotive Industry
Industrial moulds play a critical role in the automotive industry, where they are used to produce a wide range of components including engine parts, body panels, and interior trim. The ability to mass-produce complex parts with tight tolerances has revolutionized vehicle manufacturing, leading to greater efficiency, reliability, and cost-effectiveness.
Consumer Goods
From electronics and appliances to household products and packaging, industrial moulds are ubiquitous in the production of consumer goods. Moulded plastics, metals, and composites are used to create everything from smartphone cases and kitchen gadgets to food containers and toys, shaping the way we live, work, and play.
Aerospace and Defense
In the aerospace and defense industries, where precision and reliability are paramount, industrial moulds are used to produce critical components such as aircraft fuselage panels, engine parts, and missile casings. The ability to produce lightweight, high-strength parts with complex geometries has revolutionized aircraft design and manufacturing, leading to safer, more efficient, and more capable aircraft and weapons systems.
Conclusion: Shaping the Future of Manufacturing
In conclusion, industrial moulds are essential tools that have revolutionized the way we design, produce, and consume goods. From humble beginnings to cutting-edge digital technologies, the evolution of industrial moulding has been marked by innovation, ingenuity, and a relentless pursuit of excellence. As we look to the future, the possibilities are limitless, with advancements in materials, processes, and automation poised to further revolutionize the manufacturing industry. By embracing these innovations and leveraging the power of industrial moulds, we can continue to shape a future where anything is possible.
GETTING A QUOTE WITH LK-MOULD IS FREE AND SIMPLE.
FIND MORE OF OUR SERVICES:
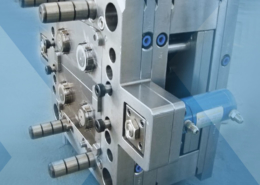
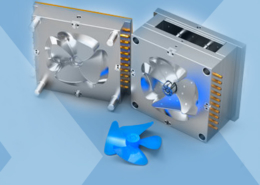
Plastic Molding

Rapid Prototyping
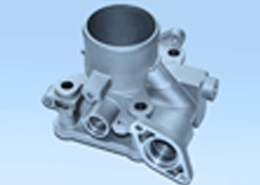
Pressure Die Casting
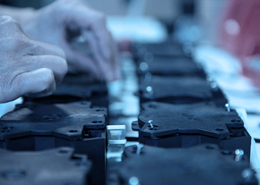
Parts Assembly
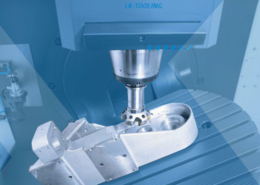