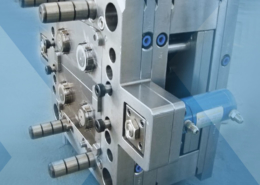
ABC Plastic Moulding Group GmbH, Rüsselsheim, Germany - abc plastic moulding
Author:gly Date: 2024-10-15
Heat deflection temperature under load varies from 75 C (167 F) for high flow materials to 100 C (212 F) for low flow (high molecular weight) materials.
Manufacturing elastomeric parts can be accomplished through injection molding, transfer molding, or compression molding. When getting a quote through Xometry, our team can help you decide the best method depending on the part geometry, estimated annual volume, and the type of material required.
Automotive (signal light devices, instrument panels, etc.), medical (blood cuvettes, etc.), industrial (video discs, lighting diffusers, display shelving, etc.), consumer (drinking tumblers, stationery accessories, etc.)
A variety of injection molding, liquid silicone molding, and compression molding options are available for an online quote. If you do not see the material stock you are looking for, please choose "Custom" under the material drop-down on your quote page and submit for an expert engineering review once you have specified features, tolerances, inspection needs, and quantities required. Below are the most common materials, and our injection molding services page offers a more comprehensive overview of our custom molding options, including insert molding and over-molding.
PMMA has excellent optical properties and weatherability. The white light transmittance is as high as 92%. Molded parts can have very low birefringence which makes it ideally suited as a material for video discs.
ABS (acrylonitrile butadiene styrene): High-strength general-purpose engineering plastic, used for many commercial products.
PMMA exhibits room temperature creep. The initial tensile strength is high but under long term, high stress loading, it exhibits stress craze. Impact strength is good but it does show some notch sensitivity.
PMMA injection molding processing condition Generic Class PMMA (Polymethyl methacrylate) Typical Applications Automotive (signal light devices, instrument panels, etc.), medical (blood cuvettes, etc.), industrial (video discs, lighting diffusers, display shelving, etc.), consumer (drinking tumblers, stationery accessories, etc.) Injection Molding Processing Conditions Drying PMMA is hygroscopic and must be dried prior to molding. Drying at 90 C (194 F) for 2-4 hours is recommended. Melt Temperature 240 - 280 C (460 - 536 F) Mold Temperature 35 - 80 C (90 - 176 F) Injection Speed Moderate If you need PMMA injection molding Pls contact us sales@viewmold.com If you need high quality injection mold tooling, Contact us. Chemical and Physical Properties Pellets for injection molding are made either by bulk polymerization of methyl methacrylate followed by extrusion and pelletization or by polymerization in an extruder. Formulations vary by molecular weight and physical properties such as flow rate, heat resistance, and toughness. Higher molecular weight grades are tougher than lower molecular weight grades. High flow formulations are generally preferred for molding. Heat deflection temperature under load varies from 75 C (167 F) for high flow materials to 100 C (212 F) for low flow (high molecular weight) materials. PMMA has excellent optical properties and weatherability. The white light transmittance is as high as 92%. Molded parts can have very low birefringence which makes it ideally suited as a material for video discs. PMMA exhibits room temperature creep. The initial tensile strength is high but under long term, high stress loading, it exhibits stress craze. Impact strength is good but it does show some notch sensitivity. If you need to look for more plastic resin injection molding processing condition, could you please click it. If you need high quality plastic extrusion services, Pls contact us sales@viewmold.com If you need high quality sheet metal parts, Pls contact us sales@viewmold.com The following is other plastic processing condition: ABS injection molding processing condition, HDPE injection molding processing condition, LDPE injection molding processing condition, PA12 injection molding processing condition, PA6 injection molding processing condition, PBT injection molding processing condition, PC-ABS injection molding processing condition, PC-PBT injection molding processing condition, PEI injection molding processing condition, PETG injection molding processing condition, PMMA injection molding processing condition, POM injection molding processing condition, PPE injection molding processing condition, HDPE injection molding processing condition, PP injection molding processing condition, PS injection molding processing condition, PVC injection molding processing condition, SAN injection molding processing condition,
Pellets for injection molding are made either by bulk polymerization of methyl methacrylate followed by extrusion and pelletization or by polymerization in an extruder. Formulations vary by molecular weight and physical properties such as flow rate, heat resistance, and toughness. Higher molecular weight grades are tougher than lower molecular weight grades. High flow formulations are generally preferred for molding.
GETTING A QUOTE WITH LK-MOULD IS FREE AND SIMPLE.
FIND MORE OF OUR SERVICES:
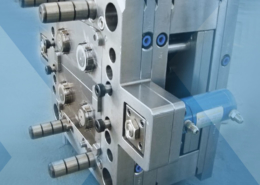
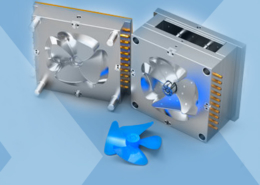
Plastic Molding

Rapid Prototyping
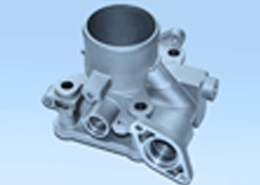
Pressure Die Casting
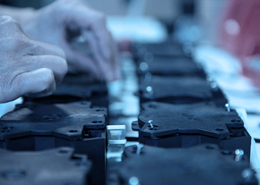
Parts Assembly
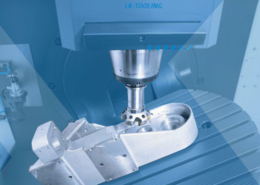