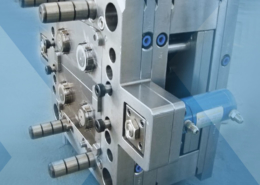
ABC Plastic Moulding Group GmbH, Rüsselsheim, Germany - abc plastic moulding
Author:gly Date: 2024-10-15
In essence, PETG injection molding transcends mere manufacturing processes, embodying a testament to human ingenuity and technological prowess. As we navigate the complexities of the modern world, PETG stands as a beacon of possibility, reshaping industries and driving progress towards a more sustainable future.
Fine-tuning injection molding parameters is paramount in achieving optimal results with PETG. Variables such as melt temperature, injection speed, and packing pressure significantly impact part quality and dimensional accuracy. By meticulously controlling these parameters, manufacturers can ensure uniformity across production batches while minimizing scrap and rework.
: Continuously refining injection molding processes through advanced modeling and simulation techniques to improve efficiency and reduce waste.
PETG boasts impressive mechanical properties, combining high tensile strength with impact resistance. This unique blend of strength and flexibility ensures that PETG components withstand rigorous handling and environmental stresses without compromising performance. Consequently, PETG finds widespread use in applications requiring durable and long-lasting solutions.
: Injection molding allows for intricate part geometries and customization, empowering designers to unleash their creativity.
PETG injection molding stands as a cornerstone in the realm of plastic manufacturing, captivating industries with its exceptional properties and adaptability. Originating from the polyester family, PETG exhibits remarkable clarity, durability, and chemical resistance, rendering it an ideal candidate for various applications.
Precision in molding PBT is heavily reliant on temperature control. Maintaining the appropriate melt temperature, mold temperature, and cooling rate is crucial for achieving the desired mechanical properties and surface finish. This meticulous temperature management ensures that PBT retains its dimensional stability and performance characteristics.
PBT blow molding is incredibly versatile and can be used in a variety of applications. For products like bottles, packaging containers, and complex automotive ducts, PBT is a great option because it can create hollow parts in a variety of forms and sizes. Because the material may be molded into various shapes, items can be customized to meet certain design specifications.
: PETG's recyclability aligns with growing sustainability concerns, offering eco-friendly alternatives to traditional plastics.
PBT's moisture sensitivity demands careful handling. Quality molding begins with thorough material drying to prevent defects like bubbles and voids. Preconditioning the material ensures a consistent and reliable melt, contributing to the overall quality of the final product.
In conclusion, PETG injection molding epitomizes the convergence of innovation and functionality, revolutionizing the manufacturing landscape. As industries continue to embrace sustainable practices and demand custom-tailored solutions, PETG's versatility and performance make it poised for sustained growth and adoption.
One particularly noticeable aspect of injection molding is its adaptability. It thrives in producing parts with complicated structures and detailed geometries, unrestricted by the simplicity of shapes. This adaptability is especially advantageous to the automobile sector since it makes it possible to produce complex parts like gears, connections, and housing sections with unmatched precision. Similarly, the electronics industry uses injection molding to create complex housings and parts that are essential to the smooth operation of electronic equipment.
The design and maintenance of molds play a pivotal role in achieving precision in PBT molding. Well-designed molds with proper venting, gating, and cooling systems contribute to the production of defect-free parts. Regular maintenance ensures prolonged mold life and consistent product quality.
PETG (Polyethylene Terephthalate Glycol) injection molding is a pivotal process in modern manufacturing, offering a versatile solution for producing a wide array of products. This article aims to delve into the intricacies of PETG injection molding, providing readers with a comprehensive understanding of its principles, applications, advantages, challenges, and future prospects.
: PETG's inherent shrinkage tendencies can lead to dimensional inaccuracies and warpage. Employing proper mold design and processing techniques helps mitigate these challenges.
One of PETG's distinguishing features is its exceptional transparency, rivaling that of glass. This property, coupled with its inherent clarity and gloss, makes PETG an attractive choice for products where aesthetics play a crucial role. From cosmetic packaging to display cases, PETG's ability to showcase contents with pristine clarity adds value to various consumer products.
The capacity of injection molding to produce consistency and homogeneity at scale is one of its distinguishing features. It is necessary to have parts that satisfy precise criteria in sectors like automotive manufacturing where accuracy is crucial. By removing differences and irregularities that can jeopardize performance or structural integrity, injection molding guarantees that every component produced is an exact replica of the mold.
One of the main advantages of blow molding is that it may be used to produce a wide range of products, including bottles, containers, and automotive ducts. The fact that PBT is so widely used in various applications is evidence of its specific benefits, particularly its ability to retain structural integrity even when molded into intricate patterns.
PETG's versatility enables it to accommodate diverse molding requirements, ranging from intricate designs to large-scale production. Its ability to maintain structural integrity under different temperatures and pressures makes it suitable for a broad spectrum of applications, including packaging, automotive parts, medical devices, and consumer goods.
By embracing these endeavors, stakeholders can propel PETG injection molding towards greater innovation, sustainability, and global relevance in the years to come.
After that, the molten PBT is pushed through a die that has been specially designed to produce continuous shapes that follow the die's edges. The final product's size, surface polish, and general characteristics are all determined by this shaping process. One of the unique qualities of extrusion molding is its capacity to produce continuous, lengthy lengths of a specific form, which is ideal for applications requiring a smooth, continuous profile.
Extrusion molding provides a variety of options that open up new avenues for PBT's adaptability. Using this process, PBT may create profiles for structural elements, pipes for fluid conveyance, and tubing for electrical conduits, among many other uses in a variety of sectors. Extrusion molding is a highly versatile material that is highly suitable for applications requiring a continuous length of a certain shape.
Nevertheless, the real secret to realizing PBT's full potential is found not only in its intrinsic properties but also in the highly skilled molding procedures used in the production process. We cordially invite you to join us on this investigation as we delve into the complex realm of PBT molding techniques, revealing the painstaking procedures that guarantee accuracy and caliber while satisfying the exacting requirements imposed by various industries.
: Compatibility issues with certain additives or colorants may arise, necessitating thorough compatibility testing to ensure product integrity.
The success of PETG injection molding hinges on meticulous mold design and optimization. Factors such as gate placement, cooling channel configuration, and part geometry profoundly influence the quality and efficiency of the molding process. Employing advanced simulation techniques aids in predicting and mitigating potential defects, thereby streamlining production and enhancing product consistency.
At the heart of precision molding with PBT lies a commitment to quality at every stage of the process. From material preparation to meticulous temperature control and tool design, each step contributes to the production of PBT-based products that meet the highest standards of precision and quality. As industries continue to rely on PBT for critical applications, the mastery of molding techniques ensures that this exceptional material continues to deliver on its promise of excellence.
Every reliable product review should start with an introductory paragraph. This is your chance to hook your readers right in and let them know what to expect. Are you reviewing one product or comparing a few? What is the full name of the product(s)? Share with your readers your expertise in this area; your frustration with products out in the market that haven’t met your needs; and why this review will offer them the ins and outs of the product’s benefits.
: Embracing circular economy principles by enhancing recycling infrastructure and promoting closed-loop material cycles to minimize environmental impact.
The process of turning solid PBT resin into a molten state is the core of extrusion molding. PBT pellets that are solid are first fed into the extruder, where they are heated and melted. The end product is a molten PBT mass that is prepared for shaping into continuous shapes.
: PETG's susceptibility to contamination necessitates stringent cleanliness protocols during mold preparation and maintenance.
ASEP Industries is a highly competitive company with its production facilities, as well as having deep R&D on products and applications. We have become an important supplier in many different markets
In the blow molding process, the molten PBT particle inside the mold is inflated under control. The precise control of this inflation assures that the material fits the intricate contours of the mold, producing hollow objects with exact shapes. To achieve uniform wall thickness and structural consistency, the inflating process must be managed.
In conclusion, the molding of PBT is a nuanced process that requires a harmonious interplay of technique, expertise, and quality assurance measures. Whether through injection molding for intricate parts, extrusion molding for versatile shapes, or blow molding for hollow structures, PBT showcases its adaptability in meeting diverse industry needs.
Within the broad field of polymer processing, extrusion molding is a critical procedure that is utilized to shape PBT (polybutylene terephthalate) into a variety of continuous shapes. This process demonstrates PBT's remarkable versatility and is preferred for producing a wide range of products, such as pipes, tubing, and profiles. Let's examine the complex process of extrusion molding in more detail and discover how it increases PBT's adaptability for a range of industrial uses.
Blow molding is a useful technique for showcasing PBT's ability to retain structural integrity even when shaped into intricate designs. This is especially important in situations where the finished product needs to be able to tolerate a variety of mechanical stresses and climatic conditions. The natural characteristics of PBT guarantee that the hollow structures created by blow molding maintain their performance and longevity.
It is impossible to overestimate the importance of accuracy and quality in manufacturing as sectors change and customer demands rise. PBT's remarkable characteristics, when combined with modern molding methods, accessible up the possibility to the production of goods that are unique in their use, durability, and aesthetic appeal. Manufacturers get a competitive edge when they choose ASEP Industries as their supplier of choice for high-quality PBT resin, guaranteeing that their products not only meet but surpass the demanding standards of the contemporary market. In the ever-changing world of plastics production, PBT and ASEP Industries' collaboration establishes a new benchmark for quality.
While injection molding yields near-net-shaped parts, post-molding operations may be necessary to refine surface finish or add secondary features. Techniques such as machining, polishing, and assembly complement the injection molding process, enabling manufacturers to meet stringent design specifications and functional requirements.
In the field of PBT (Polybutylene Terephthalate) processing, blow molding is a well-known and adaptable method for attaining the intended results of hollow constructions. This elaborate process consists of pumping a molten PBT parison—basically, a tube—through a precisely designed mold. As a result, complex hollow pieces are produced, which are used in a variety of sectors.
Few polymers in the ever-changing field of engineering plastics garner as much attention and respect as PBT (polybutylene terephthalate).
The secret to injection molding's superiority is its complex yet effective technique. PBT is first transformed from a solid into a molten state, which starts the voyage. After that, the melted PBT is pumped into a precisely designed mold cavity. When the molten material is inside the mold, it cools and solidifies to take on the shape of the cavity. This smooth transition guarantees that every completed product reflects the details of the mold, producing parts with perfect accuracy.
Acknowledged for its remarkable mechanical characteristics and superior electrical insulation, PBT has cemented its status as a flexible and desirable substance in an array of industrial uses.
GETTING A QUOTE WITH LK-MOULD IS FREE AND SIMPLE.
FIND MORE OF OUR SERVICES:
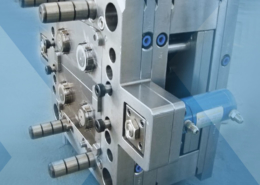
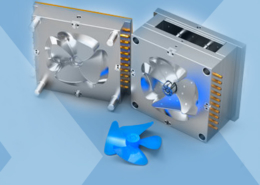
Plastic Molding

Rapid Prototyping
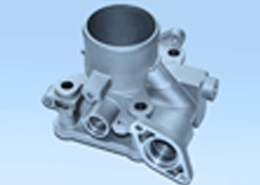
Pressure Die Casting
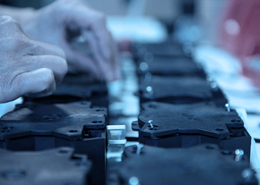
Parts Assembly
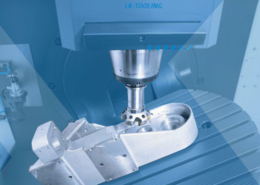