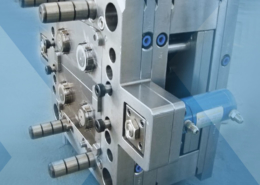
A Complete Guide to Overmolding vs Insert Molding - molding over molding
Author:gly Date: 2024-10-15
Nevertheless, the process starts with determining the design of CAD model. It merely revolves around choosing the color, texture and resin.
Sink marks – Usually occurs when due to solidification of interior parts before its surface, causing a small recess on a flat surface.
Secondly, we inspect the surface quality of the product to ensure there are no obvious defects or flaws. This includes checking whether the surface is smooth and free from scratches, dents, or other signs of imperfection.
Flexibility – It is advisable to determine how versatile the specific material you select is. It makes it easier to create a wide range of complex parts and reduces tooling costs.
Our Plastic Mini Desktop Injection Molding Machine features small size, cost-effective quality, and ease of maintenance.
FirstMold’s ABS injection molding services have several advantages. First, we have an experienced technical team with extensive injection molding experience and professional skills. They are capable of selecting suitable injection molding materials based on customer requirements and product characteristics, and use advanced injection molding processes and technologies. Secondly, we focus on details and quality, maintaining strict quality standards at every stage from raw materials to the production process. Additionally, we prioritize communication with clients, responding quickly to their needs, and providing professional advice and solutions.
When choosing the right mini injection molding machine, you need to factor in some fundamental elements such as the following;
Our integrated approach includes in-house mold design and fabrication, advanced finishing techniques, and rigorous quality control, ensuring precision, aesthetic excellence, and unmatched quality in every ABS plastic fabricated part.
As a professional manufacturer and supplier, we serve various industries like medical injection molding, university school labs, electronic, automotive, and more. Here in Inox Cast, we are committed to making innovation and continuous improvements so we can exceed your expectations.
Our plastic injection molding process uses different high-quality plastic materials with different sizes, shapes, and design.
Additionally, we test the material properties of the product. We check the hardness and toughness of the ABS material to ensure they meet our requirements and do not negatively affect the performance of the product.
Create smaller injection molded parts – It is easier to mold smaller parts faster, leading to higher production volume and lowering cost per part.
A simple case of mass production of portable ECG monitor buttons with a wide range of injection molding applications in the medical industry.
Allows repetition and consistency – This process leverages repetition and consistency; thus, you can produce a second part identical to the first one.
Small Plastic Injection Molding Machines is manufactured to produce different kinds of plastic parts and components for different industries.
ABS plastic molding might exhibit some molding defects, such as color variation. First, we recommend that clients choose standard colors or conduct color tests before production to ensure color consistency of the products. Then, we improve and optimize the mold design and injection molding process based on the experience of our engineers to ensure your products fully meet delivery standards.
Explore FirstMold's manufacturing service in producing calculator housings with injection molding ro discover how the parts be made.
Custom ABS molding demands meticulous drying and process control to mitigate moisture-related defects, warping, and shrinkage, alongside precise mold design to ensure quality finishes and part integrity. Accordingly, engineering and technology that possess the necessary engineering and advanced machinery skills are required.
We specifically offer mini injection molding services for cable overmolding, seismic cable repair, low volume injection molding, low run production parts, ASTM test specimen, and more applications. At Inox Cast, rest assured that you can get the best services fitted for your applications.
It is a combination of plastic and aluminum materials that are processed through injection molding and mold-making processes. One of the most important factors in the production of Interior LED Lamp is the design and manufacture of its components, particularly the reflector and lens.
Our mini custom plastic injection molding features polishing, chroming, brushing, silk screening, laser cutting, and other surface treatments.
Cost – Figure out the price of specific material you are selecting and establish whether it guarantees the return on investment.
We manufacture Mini Plastic Injection Molding Machine with different color variations like white, black, blue, red, and more.
What follows is DFM analysis, which aims to understand all potential risks or issues by updating CAD design to prevent future tooling modifications.
Inox Cast mini manual plastic inject molding is manufactured using outstanding quality materials, reliable performance, and optimized performance.
4. Tax and fee costs: This includes potential costs such as tariffs, tax, and freight charges, as well as other government taxes and transportation expenses.
Steel cutting is the next stage, and it involves CNC machining, EDM and wire cutting to make core, cavity, filters and inserts.
Thus, to keep production on a budget, it would be ideal to avoid using in-mold mechanisms and side-action cores unless where necessary.
Recognizing the diverse needs of our clients, we specialize in modified ABS injection molding. By altering material properties such as impact resistance, flame retardancy, or UV stability, we tailor ABS to your specific application requirements.
Our Mini Small Plastic Injection Molding Machine is made with single and multi cavities. It comes with high polish and EDM surface treatment.
Some parts hardly require such operations; thus, you can use them right away from injection molding, and this reduces cost.
The next stage is reviewing tooling design for approval. Here, you need to address all concerns and ensure you are satisfied with the design.
Of course, production of most molds is through EDM or CNC milling; thus, they can be simple or complex depending on design demands.
Custom Design Mini Plastic Injection for Mould Making is manufactured using CNC milling, prototype, plastic mould/tooling, 3D printing, etc.
2. Processing costs: This includes the production and maintenance costs of injection molds, as well as the energy, labor, and equipment depreciation costs required for the injection molding process.
3. Packaging costs: This includes the costs of packaging materials, such as plastic bags, foam, etc., as well as the labor costs for packaging.
Products made from injection molding can indeed undergo surface treatment. Common surface treatment methods include silk printing, painting, electroplating, anodizing, surface hardening, etc., to enhance the appearance and wear resistance of the products. The specific treatment method depends on the product’s application scenario and requirements. Before surface treatment, it may be necessary to clean the ABS products to ensure that the surface is free from impurities. The treated products should meet relevant quality standards and requirements to ensure their performance and service life.
We accept drawings for Mini Machine Service Injection Molding design using SolidWorks, PDF, Pro/E, Auto CAD, and more software.
Overmolding a visually stunning and functionally precise perfume cap presented a unique challenge. Let's check a case of the cometics.
Selecting the most suitable material for mini injection molding saves resources and ensures optimal product efficiency and manufacturability.
We supply wide range of mini injection molding services to different industries. For more than 20 years, Inox Cast has been recognized internationally because of our excellent quality products and unmatched services. For you business or project, you can surely trust Inox Cast to provide you mini injection molding services.
Durability – Determine the overall tensile strength of the material and its resistance to numerous environmental factors. It helps in establishing the longevity of the final part product.
What follows is samples’ first trial happening once fitting is done to resolve as many issues as possible before sending them out to the customer.
Inox Cast has a diverse and rich experience in the industry since its establishment in 1997. We are a manufacturer that covers around 32,000 square meter plant area and factory. Inox Cast also have 1000 employees including our expert engineers and designers. For more than 20 years, we are the trusted manufacturer of different industries including automotive, electronics, aerospace, medical, and so on. Message us for more information.
Easily automated – Depending on the machine you are using, you can fully automate the mini injection molding process, further reducing parts’ cost.
In the recent past, this manufacturing process is becoming popular since it somewhat reduces cost per unit of the parts.
Different resins have varied amounts and rates of shrinkage; thus, material selection for the final part is vital during design phase.
In a nutshell, mini injection molding is easily attainable with the help of multiple auxiliary equipment before, during and after the manufacturing process.
The underlining essence of using mini injection molding instead of the traditional injection molding process is to reduce cost and wastage significantly.
In mini injection molding, auxiliary equipment used for material, ingredient and batch storage include; surge bins, hoppers and silos.
Once part is ejected, it is dispensed on a conveyor belt and ready to use right away with little or no post-processing operations.
At FirstMold, our advanced facility is equipped with a comprehensive array of injection molding machines, perfectly suited for ABS plastic production. This infrastructure underpins our commitment to precision and flexibility in our ABS molding services. Our team’s deep expertise in ABS allows us to harness the latest technologies to create robust and top-tier components for a wide range of applications.
It features plastic injection mold shaping mode, single/multi cavity, DME/HASCO/LKM mold base, +/-0.02mm tolerance, and more advanced features. features.
On the other hand, others, due to performance and aesthetics, require such post-molding procedures, which increase the overall cost.
FirstMold places a high emphasis on environmental protection. All our raw materials and products comply with environmental standards. We can provide third-party test reports for the Acrylonitrile Butadiene Styrene raw materials we purchase, or we can buy materials from suppliers you specify and provide proof of raw material purchase. We are also prepared to collaborate with you on any reports or certifications needed for your products to pass various tests.
Material conveying process is facilitated by pumps, conveying controls, material selection tables, mobile conveying systems, vacuum conveying systems, conveying lines etc.
Moreover, this process offers high repeatability and ideal design flexibility, allowing you to produce the particular volume of parts you need.
Inox Cast is a popular manufacturer in different industries by providing customers’ most preferred choice and solution. We offer OEM services at a competitive price.
In addition to these, the injection molding quotation may also include other costs, such as design fees, mold modification fees, testing fees for new molds, quality inspection fees, and after-sales service fees. The specific costs may vary depending on the manufacturer, region, and complexity of the product. When determining the injection molding quotation, it is advisable to communicate in detail with the specific manufacturer or supplier to understand the specific cost structure and pricing strategy.
Our mini injection molding can generate up to 12tons huge clamping force through mechanical advantage. It only uses minimal effort maintained by the injection cycle. For our mini injection molding, we use single hydraulic cylinder for carriage and clamping. Thus, minimizing the manufacturing cost.
We offer ABS plastic fabrication services, and we can use CNC machining of ABS materials to replace some injection molding processes. ABS has excellent physical, mechanical, and processing properties, making it suitable for substituting some injection molding processes. However, due to the characteristics of ABS material, CNC machining cannot completely replace injection molding, especially in cases where large-scale mass production is required and precision demands are not high. Therefore, when considering using CNC machining as a substitute for injection molding, it is important to consider the specific application and requirements, and consult our professionals.
Scaling down production en masse – Once you determine the initial costs per unit, this manufacturing process becomes exceptionally cost-effective.
Material weighing, ingredient dispensing, and batch blending are facilitated by feeders, blenders, mixers and weighing scales.
If a product is non-conforming, FirstMold will immediately rework or scrap it and analyze the cause to prevent similar issues from recurring. We also provide clients with detailed reports and analyses of the non-conforming products to help them understand the issues. Additionally, FirstMold actively communicates with clients to seek solutions and ensure client satisfaction.
Irrespective of the material you are using for mini injection molding based on your product demands, this process offers several advantages such as follows;
On the other hand, thicker walls tend to be more expensive because of greater material usage and longer machine cycle times.
First, we use internationally accepted measurement standards to measure and inspect the dimensional accuracy and surface quality. This means we precisely measure all critical dimensions of the product to ensure they meet our design and customer requirements.
Warping – It happens when certain sections cool faster than others leading to bending on the part due to internal stresses.
Often, customized parts are a bit expensive to produce because they involve several small details, unlike standard parts.
Plastic shrinks as it cools, and properly designed molds account for such shrinkage to ensure the final product has right dimensions.
We manufacture mini injection molding machine that is easy to operate and easy to maintain. It is manufactured using copper, aluminum, brass, etc.
Besides, thorough consideration of uniform wall thickness relieves you from costly delays in your schedule arising from molding issues and mold modifications.
Inox Cast mini plastic part injection moulding features film gate, pinpoint gate, open gate, +/-0.001mm tolerance, and 50k-1.5million shots mold life.
It is a critical phase in mini injection molding process since part modifications here take a few minutes and several days after tooling is complete.
Drying, pre-heating or dehumidifying material is done by drying systems, dehumidification systems, machine sides and mini-systems.
Our ABS composite molding is used for a lot of different industries, for example, automotive, healthcare, consumer electronics, and so on. These include automotive components, medical devices and products that have good aesthetic and functionality.
Drag marks – These arise from part walls sliding and scraping against mold during ejection since it applies pressure on the mold.
You can use this method to create plastic parts of various sizes and complexity, making it ideal for a wide range of applications.
Also, the specific surface finishing and post-molding operations you need for your part influence the full cost of the process.
Optimizing the ABS plastic molding process can be approached from several angles, such as increasing injection speed, reducing mold temperature, and optimizing barrel temperature. These measures can effectively improve production efficiency while ensuring product quality. Additionally, further efficiency gains can be achieved by improving mold design and optimizing raw material formulations. The key is to enhance production efficiency without sacrificing product quality, including appearance and performance.
Unique properties – Ideally, check all the special attributes of the material such as temperature resistance, dimensional stability, weatherability, machinability and impact resistance etc.
Reduce wall thickness – To obtain a smaller part volume, it is necessary to reduce wall thickness. It implies use of less material and an accelerated mini injection molding process.
Consider secondary processes – Mini injection molding for low volume parts may be cost-effective to use secondary operations to complete.
Through the various features of ABS injection molded parts, we can easily understand the multiple advantages of ABS injection molding.
Most defects in mini injection molding are connected to melted material flow or non-uniform cooling rate during solidification.
Finally, we conduct additional tests to assess the durability and stability of the product. This includes long-term usability tests of the product under various environmental conditions to evaluate whether they can withstand the expected loads and conditions.
At FirstMold, we bring precision to life with our expert ABS injection molding services. Whether it’s a sleek gadget or a durable household item, we craft every piece to perfection, ensuring quality that lasts. Trust us to turn your design into reality with accuracy and care.
Weight – Lightweight materials are preferable as far as mini injection molding is concerned. Such materials make it easy to create both complex and simple designs.
Minimal waste – Mini injection molding features properly designed molds and processing, enabling it to produce little waste, if any.
Inox Cast is a division of SunOn Industrial Group and a Hong Kong Limited Liability Company with a diverse experience of more than 20 years. We supply products and services to customers around the world.
Knit lines – Small hair-like discolorations often develop when two flows meet, causing knit lines. These lines affect parts’ aesthetics and reduce overall strength.
Customization – Mechanical features of resins in mini injection molding can easily be engineered to meet particular design requirements by using coolants, additives and fillers.
Avoid small details – Usually, small details need longer machining and finishing times and avoiding them would enable you to cut costs significantly.
Ordinarily, unlike the normal injection molding used in mass-production processes, mini injection molding creates a few similar parts in succession.
Short shots – It usually arises due to trapped air in the mold inhibiting material flow during injection hence an incomplete part.
Essentially, basic understanding enables you to establish features to consider when designing parts for this process and forecasting production schedules.
In the acrylonitrile butadiene styrene injection molding process, we prevent product deformation by precisely controlling mold temperature, injection speed, and injection pressure. We adjust these parameters based on the characteristics and requirements of the product to ensure accuracy and consistency. Additionally, we have a temperature control system that continuously monitors and controls the temperature of the mold and materials, ensuring accuracy and stability.
GETTING A QUOTE WITH LK-MOULD IS FREE AND SIMPLE.
FIND MORE OF OUR SERVICES:
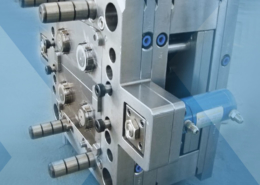
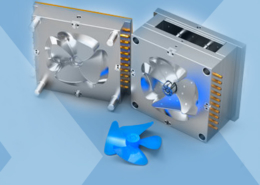
Plastic Molding

Rapid Prototyping
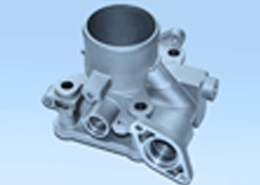
Pressure Die Casting
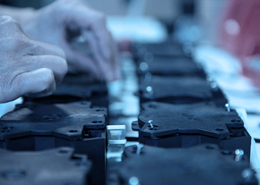
Parts Assembly
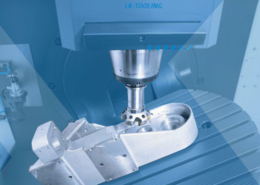