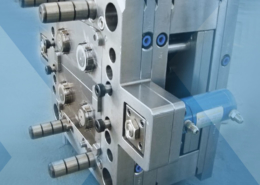
A Complete Guide to Overmolding vs Insert Molding - injection overmolding
Author:gly Date: 2024-10-15
As an innovator of on-demand digital manufacturing, Xcentric offers rapid injection molding, CNC machining, and additive manufacturing services from their Michigan facilities in the USA.
From rapid prototyping to product creation at scale, Xcentric, together with Quickparts, brings speed and scale to your prototype, parts, and production projects.
Whether it’s high-performance plastics or metals, gains are made when the right material is used in a product or part. A race car can save a few kilos in weight—and win! A coffee brewer product that was initially a no-go can become commercially viable. An inhaler’s sterilization capability can improve so much that hospitals adopt it quickly.
The properties of Delrin plastic can be measured across a range of characteristics. We further define what it means for material selection in your projects.
Our reputation as specialists stems from the millions of parts we’ve supplied in unfilled, glass, carbon fiber, bearing and wear grades of advanced polymer materials including:
Drake Plastics’ Quality Management System is certified to the worldwide aerospace industry’s AS9100D(2016) as well as ISO 9001:2015 standards. These stringent requirements apply to all products we manufacture. Our ability to meet these standards stems in large measure from our team’s experience and their commitment to achieving the highest attainable levels of quality. We also support our team by investing in the best inspection technology available, including:
Drake invests in the best available molding and process equipment and control technology for materials like Torlon PAI, PEEK, Ultem PEI and other high-performance polymers. Our production team also takes extreme measures to achieve the highest levels of quality and performance in molded parts.
One of the most fundamental questions asked in product performance is: Are we using the most optimal material for this application?
Drake offers a diverse menu of services and capabilities to meet customer-specific requirements and industry compliance standards for injection molded parts. They include:
At Xcentric, we offer the most popular grades of Delrin to help our customers choose the best application for their part or product. These include the Delrin 150 Homopolymer in Natural and Black, and Delrin 570 (20% Glass Filled) in Natural.
Drake’s process technology includes In-cavity pressure transducers and RJG Systems that monitor process parameters inside the mold cavities to maintain ideal conditions. This important control leads to high quality and exceptional repeatability in every Drake injection molded part equipped with RJG.
Overall, Delrin plastic offers strength, toughness, dimensional stability, and natural lubrication for good machining capabilities. But what makes a particular grade stand out?
Becoming part of Quickparts expands the capabilities and expertise Xcentric offers, delivering injection molding, CNC machining, and other critical services to customers across the globe.
Plastic injection molding is a viable substitute for metal in very demanding applications. If you’re considering a transition from metal to plastic components for your parts and projects, work with an Xcentric expert to understand how a high-performance plastic—like the Delrin plastic— can perform your desired function at an acceptable manufacturing cost in commercially meaningful volumes.
Delrin plastic is available in many grades—100, 500, 900, and 1700. The grades refer to their melt viscosity, with 100 the most viscous and 1700 the most fluid. Choosing the correct grade depends on your fill requirements and end-use function.
There is a strong case for Delrin plastic as the ideal solution for your parts and projects. In some cases, the reward is obvious. Like in the race car example mentioned earlier. But in other cases, the math becomes more complex. We help you weigh up Delrin plastic as an alternative in your material selection.
Annealing PEEK and other ultra-high performance thermoplastic parts: Drake has extensive experience in annealing to relieve internal stresses that can impair a part’s properties or cause it to deform over time. Residual stresses occur as an advanced polymer rapidly transitions from its hot melt phase to ambient temperature. This is especially problematic for parts with heavy or varying cross-section thicknesses that cool at different rates. Annealing under controlled conditions resolves this: by heating parts above the advanced polymer’s Tg or softening point, then cooling very slowly to a point below its Tg, the polymer chains relax uniformly, relieving residual stresses. Drake offers annealing on a custom basis. It is often utilized for injection molded parts that require exceptional dimensional stability or a crystallinity level that maximizes the polymer’s strength, toughness and chemical resistance.
The best production and quality practices deliver maximum value to customers only when backed up by consistently exceptional service. Drake’s customer-centric culture is evident in our rapid response to requests for information, support and problem-solving. Drake’s on-time delivery performance is 98% or better. Our team sets 100% customer satisfaction as the norm and sustaining it determines our ongoing service-based investments.
Certifications on all shipments: Drake Plastics provides a Certificate of Conformance with all products regardless of polymer composition at no charge. Special testing is also available at a reasonable cost.
As a combined company, Quickparts and Xcentric offer an in-house, end-to-end solution from first prototype to short-run production, offering more to capabilities and benefits to customers both domestically and worldwide.
Precision injection molding ultra high-performance plastics demands a solid understanding of each polymer’s unique behavior to avoid degradation and achieve optimum property and quality levels. Its melt characteristics and flow behavior must be factored into process conditions and hardware designs to preserve physical properties and achieve consistent quality in the high-pressure and high-temperature molding process.
Rapid prototyping involves the fast creation of parts. A material like Delrin plastic that is stable and has a high machinability rating makes it very suitable for rapid prototyping.
The merging of Quickparts and Xcentric helps support customers’ continued growth and proficiency through improved U.S.-based, in-house, and quick-turnaround production. From 3D printing to injection molding, we do it all.
Our production team’s ideas have a major impact on our reputation for superior quality. Among their initiatives: dedicated dryers for each resin to avoid cross-contamination. And they know purging can’t eliminate all residue after a run, so they do a full tear-down, polishing the screw and cleaning all components that contacted the melted polymer in the prior run before starting the next job.
Take Delrin plastic, for instance. Also known as PolyOxyMethylene (POM), Delrin is a brand name for Dupont’s acetal polymer. It has two distinguishing factors when compared to other acetal plastics:
In 3D Printing, a prototype is created layer by layer and therefore the material used needs to be wear-resistant. Delrin plastic filaments make a great selection.
In the numerous injection molding projects Xcentric has delivered for its clients, we know there are applications where high-performance plastics are not viable substitutes for metal alloys. But in many other applications, we have found that polymers do outperform metals.
Drake Plastics’ support capabilities can be especially beneficial to customers transitioning from a machined plastic or metal component to injection molding:
Delrin plastic is often used in CNC Machining, Injection Molding, and 3D Printing because it is durable and robust. It is hard—which helps when you’re working on a part that needs to be precise and accurate. It resists high temperatures. It is also wear-resistant, which makes it suitable for additive manufacturing. There are many more properties to Delrin and its different grades.
Founded in 1996, Xcentric Mold & Engineering is an innovator of on-demand digital manufacturing and continues to lead advances in injection molding and rapid prototyping. We know what it takes to deliver a high-quality product on time and on budget. Xcentric is engineered to be nimble, employs a team of experts in injection molding, and takes an engineer-centric approach to everything we do. Tens of thousands of product developers and engineers across North America trust Xcentric to bring their products to life.
With decades of experience in melt-processing ultra high-performance thermoplastics, injection molding specialists, Drake Plastics has fine-tuned process conditions, designed and built specialized components for our molding equipment and invested in the technology needed to produce consistently high-quality injection molded parts in Torlon PAI, PEEK and similar advanced polymers.
Post-curing Torlon PAI parts: Every Drake-produced Torlon PAI product goes through an engineered post-curing processes, a key factor in realizing the full performance potential of this advanced polymer. This final step before shipment achieves Torlon PAI’s typical core Tg (glass-transition temperature) midpoint value of 540°F (282°C). In our decades of experience with the material, we’ve optimized curing cycles to produce Torlon PAI parts to achieve maximum structural strength, toughness, and resistance to wear and chemicals.
Near-net shapes provide an efficient, economical bridge between machining low part quantities from stock shapes and molding high volumes that require a significant investment in tooling. These forms or blanks are molded in low-cost tools and approximate the part’s as-designed dimensions. They are then machined to exact part dimensions. Using near-net shapes when production requirements reach the right levels yields a major savings in material vs. machining from rod or plate.
Insert molding integrates functional metal components into injection molded parts during the molding process. The inserts are fixed in the mold cavity, and the polymer melt flows around the metal component as the molding process takes place. Electrical conductors, threaded fasteners, structural reinforcements and protective caps made from titanium, stainless steel and other metals are only a few of the possibilities for insert molding, and the technique is incorporated into many high-performance parts made from the advanced polymers Drake routinely molds. Other advantages include reduced assembly time in the customer’s operation and more secure integration of the molded-in metal component in the part.
If you have a project you need help with, submit your project here, and our team will be happy to provide expert advice.
Many customers describe our facility as the cleanest and most efficient they’ve experienced. Our all-electric injection presses yield precision parts from 0.03 to 20 oz. (0.85 to 570 grams). They use no hydraulics, adding to the cleanliness of our operation. Each machine is also equipped with a unique capability to compress or ‘coin’ parts during the molding cycle, enabling us to injection mold very heavy cross-sections without porosity or voids.
Drake’s extensive in-house molding and machining capabilities combine to offer customers molded parts with complex geometries and features not possible with injection molding alone. Precision finish-machining adds deep undercuts, side or angled holes or ports, zero or negative draft sidewalls and other design elements that are impossible or impractical to mold. Our CNC machining also yields tighter part tolerances than can be achieved in molding. For example, machined feature tolerances on a molded part can be held to +/-0.0005 inch (+/-0.02mm).
GETTING A QUOTE WITH LK-MOULD IS FREE AND SIMPLE.
FIND MORE OF OUR SERVICES:
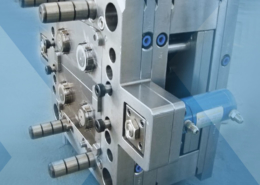
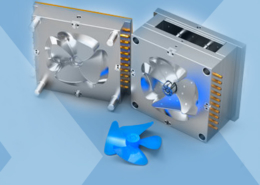
Plastic Molding

Rapid Prototyping
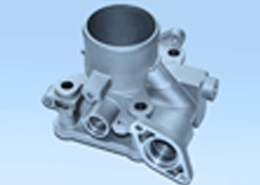
Pressure Die Casting
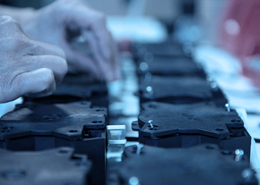
Parts Assembly
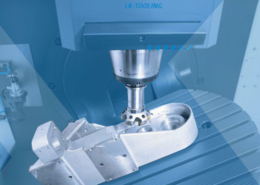