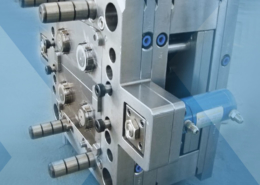
A Brief History of Plastic Injection Molding - plastic injection
Author:gly Date: 2024-10-15
If you are designing plastic parts and want to collaborate with professionals in plastic manufacturing, Aline Components is an excellent choice. Aline Components is a leading provider of plastic injection molding services located just outside Philadelphia, and we have an extensive range of services available for plastic manufacturing, as well as the different types of plastic and the expert knowledge of their application. If you are designing components for a particular industry we can help you select the appropriate material. Give us a call to discuss the details: (215) 368-0300.
At Advanced Plastiform, Inc. we design and manufacture custom plastics for industries and businesses across the Southeast and Mid-Atlantic. In order to ensure that we are producing highly-durable plastics that can fulfill the needs of our customers, we work with numerous thermoplastic materials to provide the best result. Due to its versatility and multitude of uses, we are a leading polypropylene plastic manufacturer.
Polypropylene is a thermoplastic polymer that is one of the most widely used plastics worldwide, second only to polyethylene. It was created in 1951 by petroleum chemists and was quickly used in large-scale commercial production.
Polypropylene injection molding is a method of manufacturing in which polypropylene is melted to its liquid state, then injected into a double-sided mold. Injection molding is ideal for small components and parts or plastic pieces that require intricate detailing and varying thickness throughout the item. While the up-front cost is more expensive and has a longer lead time than thermoforming, for high volume orders or orders that will be fulfilled regularly, the per-unit cost is actually very cost efficient.
In addition to its versatility, it’s also one of the lowest cost plastics, making it a popular option for mass producing plastics across the automotive, furniture, and material handling industries.
We are proud to be a leader in polypropylene plastics manufacturing, capable of providing custom plastics to customers across numerous industries. Our clients know we offer the durable, long-lasting products they need while providing competitive pricing and fast lead times. We work with businesses in North Carolina, South Carolina, Pennsylvania, Maryland, Tennessee, Georgia, and Virginia.
Often used as a less expensive alternative to polypropylene injection molding, pressure forming plastics allows us to achieve higher levels of detail and sharp edges than with vacuum forming. Once the polypropylene is fitted around the tool, the plastic is blasted at high pressure with air, pushing it against the tool and creating the sought after design and detail. Because it’s low electrical conductivity, polypropylene pressure forming is used for manufacturing scientific instruments and medical equipment.
Despite its name, Polylactic Acid is in the family of polyesters, composed of two main monomers: lactic acid and the cyclic di-ester, lactide. Widely known as PLA plastic, it is the second most commonly used bioplastic in the world. Formulated with specific attention to the environment, PLA plastic is derived from cornstarch or sugarcane and is designed to degrade back to its constituent components for a relatively benign environmental impact. As a biologically derived polymer, it is highly workable, and useful in situations where gradual dissolution is desirable. PLA plastic is often used for temporary fittings fasteners, plates, and other mechanical parts for the medical industry, and its biodegradable properties also make it useful for food packaging. The proliferation of its use in all types of industries is an indication of its effectiveness.
Since 1988, Advanced Plastiform, Inc., has been providing superior custom plastic molding and fabrication services to companies in North Carolina, South Carolina, Maryland, Georgia and Pennsylvania. Contact us to make an appointment Mon-Fri 8-5.
Polypropylene thermoforming is a lower-cost, efficient way to manufacture large plastic goods and components. We heat the polypropylene until it is malleable, then fit it around a custom tool and finish the product using one of three methods:
Elevate your projects with consistency, quality, precision, and efficiency in custom plastic manufacturing with parts made from polypropylene.
It’s not much of an exaggeration to say polypropylene is used for everything. It’s easy to customize, has a high melting point, high flexibility, and is water resistant so it’s most commonly used for:
Twin sheet forming is a complex method of polypropylene plastic manufacturing, requiring high levels of precision and care. It involves heating two plastic sheets at the same time, then fitting them together and fusing them. Because the plastic must be matched with pressed points where the fusion occurs, there’s no room for error or the integrity of the product is weakened. Twin sheet forming is ideal for manufacturing double-walled and hollow products, like air ducts, chutes used in material handling, and bed liners.
Vacuum forming is the simplest method of polypropylene thermoforming. Once the plastic is heated and fitted around the custom tool, a high-powered vacuum removes air and draws the plastic more tightly against the tool. This method is best for plastic components that don’t require sharp edges, defined corners, or intricate details, such as car dashboards and shipping trays.
As a low-temperature plastic, polylactic acid has a relatively lower melt point than high-performance plastics, and more research into the possibilities of increased temperature resistance is ongoing. In many respects, however, PLA plastic performs well in its dimensional stability and it can be crystallized to achieve more rigidity. While not designed for long life or high temperatures, the low cost and sustainability, combined with its ease of use, contribute to PLA plasticâs popularity.
GETTING A QUOTE WITH LK-MOULD IS FREE AND SIMPLE.
FIND MORE OF OUR SERVICES:
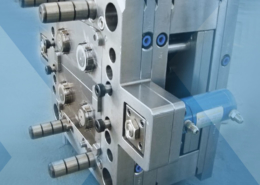
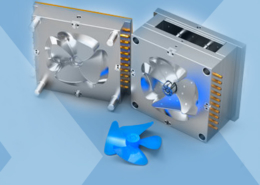
Plastic Molding

Rapid Prototyping
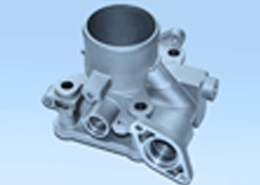
Pressure Die Casting
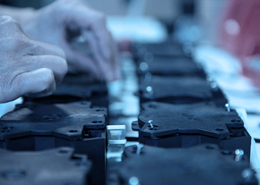
Parts Assembly
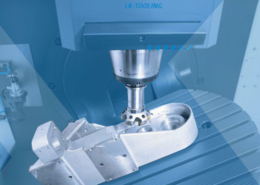