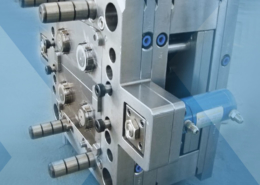
A Beginner's Guide to Injection Molding - plastic mold fabrication
Author:gly Date: 2024-10-15
Cavity and core mold halves are insured to be in proper alignment during mold close by the use of guide pins (or pillars) and guide bushings (or sleeves).
Overall, careful consideration of these factors is critical to the successful molding of PEEK and the production of high-quality parts with the desired properties.
PVX Black PEEK is a type of PEEK that is reinforced with graphite and PTFE lubricants. This grade of PEEK offers the lowest coefficient of friction and the best machinability out of all PEEK grades. It is an excellent choice for plastic parts that are exposed to extreme environmental conditions, as it offers a combination of low friction, low wear, high LPV, low mating part wear, and ease of machining.
CF30 PEEK is a PEEK resin that contains 30% carbon fibers. The inclusion of carbon fibers significantly reduces its expansion rate and improves the compressive strength and stiffness of PEEK. This grade of PEEK is particularly advantageous as it offers enhanced thermal conductivity compared to natural PEEK, allowing for greater heat dissipation from surfaces.
Plastic is injected hot and is cooled by cooling channels that allow conduction to cool the part. Working fluid is typically water, although oil can be used in high temp applications.
PEEK’s combination of high temperature and chemical resistance, excellent mechanical properties, biocompatibility, and electrical insulation makes it a versatile material that can be used in various industries, including aerospace, medical, oil and gas, automotive, and electronics.
PEEK is a versatile material for injection molding, as it offers a range of properties that can be applied to diverse manufacturing projects. PEEK is available in four major categories, which include the natural grade and reinforced varieties. These categories offer a broad range of properties that can be tailored to meet specific project requirements.
Sungplastic is a plastic product manufacturer with rich experience in injection molding. According to the different product development requirements, we flexibly adjust the manufacturing process to achieve high quality, high efficiency and more economical.
If you're up for an even deeper dive in the world of plastic injection molding, check out this video from a previous blog post. In it, one of our capable engineers explains the ins and outs of injection molding. The video is about 12 minutes long, and packed with great information.
Proper mold design, processing parameters, material handling, and maintenance are critical to successfully overcome the challenges of molding PEEK and produce high-quality parts.
Cavities are areas of the mold where the part is formed into desired shape. Molds must be balanced, so there are typically only a certain number of cavitations allowed (1,2,4,8, etc...)
So you've designed a product. You've gone through the RFQ process, sharing your CAD drawings with engineers who probably made even more tweaks. The part is going to be made of plastic using the injection molding process. But you've never made a plastic injected part before. There are a lot of new words and phrases being tossed around and you don't really know what they all mean.
East West is a global manufacturing services company focused on the realization of products, from design through distribution. As specialists in onshore, nearshore and offshore manufacturing, we offer a seamless path to scale and an exceptional speed-to-market strategy while driving down costs and adhering to the highest quality standards. We are one integrated family, working together to support our customers throughout the entire product lifecycle. Our vision is to make the world a better place – cleaner, safer, healthier and smarter.
A:Design considerations for PEEK parts include the part geometry, wall thickness, draft angles, and gating and venting. Proper design can help ensure successful molding and high-quality parts.
Mold halves are attached to the molding platens by the clamp plates. Mold clamps use large bolts to hold them in place; other machines hold the mold onto the platen with magnets.
Plastic Mold Manufacturing Plastic Injection MoldingRapid PrototypingCNC MachiningSheet Metal StampingPressure Die CastingSilicone & Rubber PartsSurface Finishing
Filed Under: Plastic Injection Molding, Injection Molding
PEEK(Polyether Ether Ketone) is a high-performance thermoplastic material that is known for its exceptional mechanical, thermal, and chemical properties. It is a semi-crystalline polymer commonly used in applications where extreme conditions exist, such as high temperature, high pressure and exposure to harsh chemicals. PEEK has a high strength-to-weight ratio, excellent dimensional stability, wear resistance and fatigue resistance. It is also biocompatible and has been approved for use in medical implants and devices. PEEK is used in various industries such as aerospace, medical, oil and gas, automotive, and electronics, and is processed using various techniques such as injection molding, extrusion, and machining.
Sungplastic is a PEEK injection molding service manufacturer that can provide a range of services to help with PEEK parts manufacturing. Our company has many years of experience in the plastic molding industry, specializing in the production of high-precision complex parts. We offer a range of injection molding services including design, engineering, tooling, and production. Here are some ways Sungplastic can help:
No one would blame you for looking for a glossary of terms right about now. Fear not. Below, we break down the components of an injection mold in simple, easy-to-understand language. It even includes labeled cutaway drawings. I promise, if you didn't understand how an injection mold worked before, you will after reading this.
An injection mold is a tool comprised of a series of parts that allows molten plastic to be formed and cooled in such a way as to create a discrete part shape.
We offer a variety of manufacturing services: Rapid Prototyping, Tool Making, Injection Molding, Product Design and Development, CNC Machining and Metal Stamping. You can choose from a variety of plastics, silicone rubber, or metal for your product. Regardless of mass production or small batch customization, Sungplastic has always been committed to providing assured, efficient and more economical one-stop processing services for your projects.
A:Post-processing techniques for PEEK parts can include machining, polishing, and coating. These techniques can be used to achieve the desired dimensions, surface finish, and functionality of the part.
Plastic flows through the sprue bushing in a sprue, then to individual runners which take the material to the gates - the entry point of the material to the individual cavities.
PEEK (Polyether Ether Ketone) is a high-performance thermoplastic material that possesses several exceptional properties, which make it well-suited for use in demanding industrial applications. Some of the key properties of PEEK material include:
Natural PEEK is an unreinforced general-purpose grade that is highly wear-resistant and has the highest levels of elongation and toughness of all PEEK grades. This makes it an excellent choice for instrument components that require aesthetic appeal. Additionally, Natural PEEK is well-suited for plastic parts that require high levels of ductility and inertness.
GF30 PEEK is a type of PEEK resin that contains 30% glass fibers. The addition of glass fibers significantly reduces the expansion rate and increases the flexural modulus of the resin. This makes GF30 PEEK an excellent choice for structural applications that require high levels of strength, stiffness, and dimensional stability, particularly at temperatures exceeding 148ºC / 300ºF.
Liquified plastic is pushed through the nozzle of the barrel of the molding machine. The nozzle seats against a surface on the mold called the sprue bushing and locating ring, which help center the nozzle to the mold.
A: Yes, such as ABS, PP, PC, Nylon, PMMA, etc. To better understand how Sungplastic can serve you for your injection molding project, contact us or request a quote today.
PEEK injection molding is used in applications where high performance, reliability, and durability are required. Its unique combination of mechanical, thermal, and chemical properties make it suitable for use in a wide range of industries and applications.
The ejector pins are mounted in an ejector plate. The motion of the ejector plate forward allows the pins to move forward, pushing the part off the core. The ejector retaining plate holds the pins into the ejector plate.
Sungplastic’s expertise and capabilities in plastic injection molding help ensure the successful manufacture of PEEK parts, from material selection to final delivery. At Sungplastic, we offer dependable service and ensure that you have a great experience with a seamless manufacturing process. When choosing a PEEK manufacturer, Sungplastic can be a great choice for you.
The PEEK injection molding process requires precision and skill to produce high-quality parts consistently. The process parameters, such as temperature, pressure, and cooling time, must be carefully controlled to ensure the part meets the required specifications.
GETTING A QUOTE WITH LK-MOULD IS FREE AND SIMPLE.
FIND MORE OF OUR SERVICES:
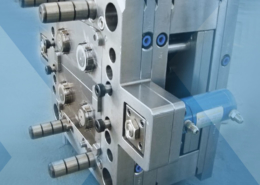
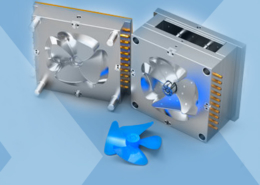
Plastic Molding

Rapid Prototyping
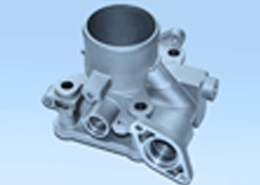
Pressure Die Casting
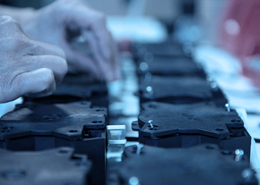
Parts Assembly
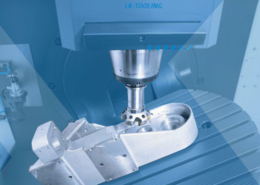