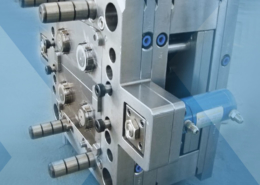
5 Things You Need to Know About Plastic Injection Molding - plastic molding
Author:gly Date: 2024-10-15
Aluminum mold can be polished or textured,it can be polished to a near SPI #2 finish,possible to get a Class A surface finish on an optical component. With few exceptions, any texture added to a steel mold can be added to any aluminum mold.Class A surface finish is usually used for optical components such as clear lenses, light pipes, light guides and prisms made from materials such as acrylic and polycarbonate. Even these clear plastic components with complex optical details and highest level of surface quality are not impossible to expect from aluminum tooling. For example, hard coating aluminum molds with electroless nickel adds additional hardness and corrosion resistance, polishes extremely well to a Class A surface finish, and protects the integrity and extends the life of the mold.
We combine traditional injection molding methods with aluminum tooling to deliver plastic molded parts in 3 weeks or less, with the same high precision, complex designs, custom surface finishes and textures.
Aluminum tools always play as a bridge to a faster product launch due to aluminum mold core/cavities and inserts being more flexible and easier to machine than steel, so iterative design changes or creating modifications are typically less burdensome and less cost impact.
Whether you have a simple design or very complex requirements, our engineering team and experienced craftsman will take you from initial concept through final production and packaging.
Usually, the weight of aluminum mold is one-third of the steel mold, which is easy to operate; fast and efficient machinability makes aluminum machining easier and tool loss lower; simplified cooling system and mold structure make the production efficiency much higher. These directly or indirectly reduce the overall production cost.
Have a complex part design, with tight tolerances, and various surface finishes and textures? Don’t worry. Our aluminum tooling process can handle it and we won’t ask you to change any things, and allow you to reach the market the fastest with the least amount of cost.
Aluminum offers excellent machinability with small chips, few burrs, fast CNC feeds, 5 to 10 times faster machining and EDM than steel, and the ability to provide faster finishing and polishing times, so molds can be built in less time.
Can you imagine making an aluminum mold and delivering hundreds of plastic parts in just three weeks? From mold design to mold built, our design team is devoted to developing a cost-effective and quick turn-around aluminum tooling approach:
Aluminum tooling cavities conduct heat nearly five times faster than P-20 tool steel. Quicker cooling generally means substantially reduced cycle time and faster parts and allows us to process without machining some cooling channels this also reduced mold building time.
Aluminum tooling can evenly dissipates heat, which offers a more consistent mold temperature, improve dimensional stability in tooling. This significantly reduces warpage and produces less waste during the production process.
Conventional steel tooling is normally used for producing millions of parts, however, what if production demands call for smaller quantities?As steel mold often takes months to manufacture and large initial capital investment, in the last few decades, pressures to shorten the cycle time for both making the mold cheaper and molding parts quicker to market has driven the interest in an aluminum injection mold to a new level. With today’s improved grades of aluminum outstanding hardness and strength for increased mold life, aluminum mold can be not just for a prototype or the bridge to a faster product launch, but also it can be a successful alternative to steel tooling with huge benefits that will continue to advance and influence the future of the plastics industry. If you don’t request millions of parts, if you need to produce parts on-demand in a quick turn, and if you want to avoid risky tooling investments until your part design is truly validated, low volume injection molding using aluminum molds may be a best approach.
Messenger specializes in high-tech, tight tolerance, precision mold design. As a full-service molder, we take pride in building relationships with our customers so your product is designed and built exactly to your specifications. Our team works with you one-on-one to be sure you are satisfied.
There are a variety of benefits of aluminum molds over steel molds, which translates to a critical advantage for our customers. Aluminum provides excellent machinability, faster machining, less cycle time, more readily adaptable to engineering changes, tight tolerances, and consistent process, and reduced production costs. Now, anything you do in a traditional P20 mold can be done in an aluminum mold.
For nearly 40 years and two generations, Messenger has been providing custom designed, high-quality, precision tooling and plastic injection molding to clients all over the world. Our proven track record and list of customers show we are committed to providing you the best quality in the industry.
We are committed to manufacturing high-performance aluminum injection molds, molded parts and continually improving our processes to build better molds faster and at a lower cost in order to provide high-value solutions to our customers.
GETTING A QUOTE WITH LK-MOULD IS FREE AND SIMPLE.
FIND MORE OF OUR SERVICES:
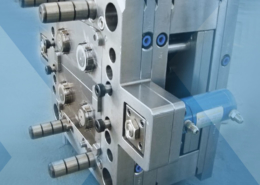
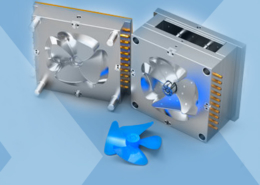
Plastic Molding

Rapid Prototyping
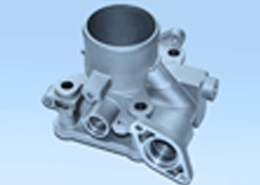
Pressure Die Casting
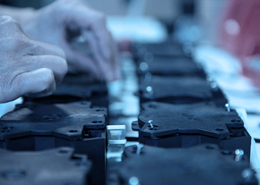
Parts Assembly
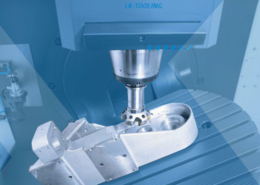