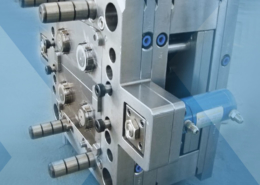
3 Tips for Calculating Press Size | Plastic Injection Mold - injection mold pres
Author:gly Date: 2024-10-15
We typically work with large customers such as automotive OEMs, Tier 1s, and Tier 2s. The majority of our accounts have volumes of at least 10,000 parts annually and have an annual buy over $100,000. If this sounds like you, we should connect.
Our expertise lies in two-shot overmolding and insert molding. In addition, we utilize in-house secondary processes and high levels of automation to lower labor costs and improve accuracy and lead times. Our team can determine the optimal processes for your part.
PEEK often outperforms metal when used in harsh environments. This makes it a popular choice when manufacturing aerospace and automotive components, medical devices, machinery parts, semiconductors, and electrical and electronic machinery.
From concept to production, our tailored design and engineering capabilities deliver cost-effective solutions for two-shot injection molded parts. We have the experience and confidence to take full design responsibility or serve as a design partner.
Two-shot injection molding eliminates the need for secondary processes such as welding and assembly. As such, piece prices tend to be lower for two-shot molded parts compared to multi-component single-shot assemblies. The tooling for two-shot, on the other hand, tends to be more complex and costly than single-shot. Therefore, two-shot injection molding is most cost-efficient for high-volume productions. Request a quote today to see if two-shot molding is the right solution for you.
While PEEK will enable you to make lighter, stronger, and more chemically resistant parts that will last longer, you need to evaluate how much of a return on your investment this material will get you, considering its additional cost. Talking to a material selection expert from Xcentric will help you decide. We will take you through an efficient design and manufacturing process that will bring even your most complex products to market in weeks.
With decades of experience in two-shot injection molding, we’ve optimized our processes to drive cost out and maximize value for our customers. Our rapid prototyping, advanced molding techniques, and material expertise streamlines the production process from conception to production.
Becoming part of Quickparts expands the capabilities and expertise Xcentric offers, delivering injection molding, CNC machining, and other critical services to customers across the globe.
Our two-shot injection molding company is ISO 14001:2004, ISO/TS 16949:2009, and WBENC certified. View our Certifications page.
As an innovator of on-demand digital manufacturing, Xcentric offers rapid injection molding, CNC machining, and additive manufacturing services from their Michigan facilities in the USA.
The merging of Quickparts and Xcentric helps support customers’ continued growth and proficiency through improved U.S.-based, in-house, and quick-turnaround production. From 3D printing to injection molding, we do it all.
Our two-shot injection molding company is located in Bad Axe, Michigan. You can drop us a note online, give us a call at 989-269-9791 or email us at plasticsales@geminigroup.net.
PEEK is a semi-crystalline, opaque material belonging to the PolyKetone family of polymers called PAEK, which comprises aryl, ether, and ketone molecule groups. The aryl and ketone portions of its build-up give PEEK rigidity and stiffness, which means good mechanical performance and a high melting point. The ether group in PEEK lends flexibility (making it tough) and renders it unreactive (providing resistance to chemical exposure).
This is what our experts at Xcentric think you should know about PEEK to help you decide whether it is the right material for your needs.
There are thousands of plastic variations available, from everyday commodity plastics to high-performance polymers used in very demanding operating environments. At Xcentric, we have more than 40 resins in stock to choose from and take particular care in advising our clients on material selection.
Founded in 1996, Xcentric Mold & Engineering is an innovator of on-demand digital manufacturing and continues to lead advances in injection molding and rapid prototyping. We know what it takes to deliver a high quality product on time and on budget. Xcentric is engineered to be nimble, employs a team of experts in injection molding, and takes an engineer centric approach to everything we do. Tens of thousands of product developers and engineers across North America trust Xcentric to bring their products to life.
Make informed decisions before full-scale production with our rapid prototyping capabilities. We evaluate the design and identify potential issues quickly and cost-effectively to speed up the product development process.
Here is why: Many high-performance polymers can stand up to one or two requirements, either the ability to withstand extreme temperature or chemical exposure. However, most of these fall below expectations when it comes to other demands, such as wear-resistance or mechanical strength.
Two-shot injection molding is the ideal process for complex parts. As such, part design often requires a high level of refinement and sophistication. That’s why we’ve developed a Two Shot Design Guide. It provides the foundation you’ll need to start designing for the two-shot molding process.
Among the small number of high-performance polymers, the PAEK (PolyArylEtherKetone) family leads the way, and, among these, PEEK (PolyEtherEtherKetone) is the most popular.
Our two-shot injection molded parts contribute to the success of major industrial sectors, including automotive, lawn & garden, heavy equipment, and consumer products. Explore the wide range of uses for our two-shot injection molding solutions.
If you are looking for an injection molding material solution that strikes a balance between your performance needs, budget, and environmental and sustainability goals, PEEK will top the shortlist (or come close!)
The two-shot injection molding process combines two different plastic resins in one machining cycle. To realize the full benefits of this process, you should choose two compatible materials that can form a molecular bond while simultaneously meeting the functional requirements of your part. Learn about the most common two-shot injection molding materials in our Two-Shot Design Guide, or contact us if you need help choosing compatible materials.
We’ve worked with hundreds of materials and additives, so we can accurately predict how processing will affect appearance. This expertise allows for precise color-matching and replication of design intent, enhancing visual appeal and brand identity.
There are hundreds of materials suitable for two-shot injection molding and thousands of ways to adjust, blend, and fine-tune them. Our material experts can help you choose compatible materials that will form a molecular bond while simultaneously meeting the requirements of your part.
From rapid prototyping to product creation at scale, Xcentric, together with Quickparts, brings speed and scale to your prototype, parts, and production projects.
PEEK comes in five grades based on composition and variances in properties that influence which applications it is best suited for:
We design and manufacture most trim and fabrication tooling, as well as assembly fixtures, in-house. We’ll occasionally build prototype and production molds in-house, but we’ve found it’s usually more cost-effective to design in-house and partner with a dedicated, US-based moldmaker for the manufacturing.
Two-shot design can deliver a competitive advantage far above other molding processes, especially for complex parts. Learn the benefits of the process and explore the special design requirements needed to make it work in this free guide created by engineers, for engineers.
Our specialized press-to-press transfer technique allows us to mold 360-degrees. It’s ideal when your application requires molding over metal inserts such as fasteners and magnets or other substrates such as structural reinforcements.
Product developers and engineers are often overwhelmed by the number of injection molding plastics they must choose from to find just the right material to manufacture with.
As a combined company, Quickparts and Xcentric offer an in-house, end-to-end solution from first prototype to short-run production, offering more to capabilities and benefits to customers both domestically and worldwide.
PEEK, however, possesses several of these properties: including mechanical strength, wear-resistance, heat resistance, and chemical resistance. It is easily processed and recyclable.
And because PEEK can be mass-produced by injection molding without involving the machining of metals and the curing of thermosets, there are fewer processing steps. This results in time and cost advantages.
This breadth of experience enables us to evaluate multiple processes and materials and recommend the optimal combination for your unique application.
GETTING A QUOTE WITH LK-MOULD IS FREE AND SIMPLE.
FIND MORE OF OUR SERVICES:
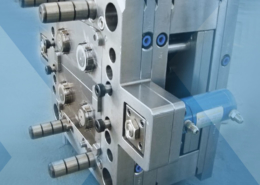
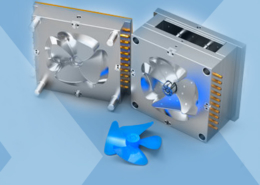
Plastic Molding

Rapid Prototyping
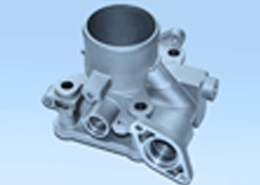
Pressure Die Casting
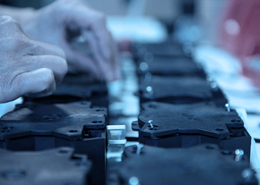
Parts Assembly
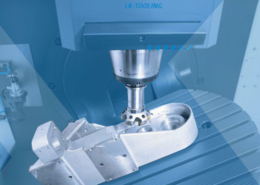