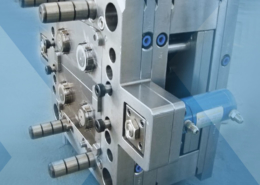
3 Tips for Calculating Press Size | Plastic Injection Mold - injection mold pres
Author:gly Date: 2024-10-15
Long-term resistance to X-rays and continuous operating temperatures of 260 °C, e.g. for computer tomography (CT), can be achieved with injection mouded components made of high-performance medical plastics.
All these applications place the highest demands on tolerances, feel and appearance of the medical plastic injection molded parts. The low weight of the plastic instruments contributes to gentle handling even during longer periods of use.
Overmolding, insert molding, multi-component injection molding, injection molding MuCell®-technology can offer flexible solutions for the integration of functions as well as the production of medical assemblies. Through various printing and marking technologies (e.g. laser marking), surface treatments, deburring technologies (e.g. blasting), custom requirements regarding haptics, optics and traceability are met.
We realise the complex shapes and design geometries required for this with high precision and efficiency using our injection molding technologies.
In medical technology, some components also require individual machining to achieve special contours and accuracies. Injection molding of blanks significantly increases the material variety and selection options. In addition, material losses and thus costs can be significantly reduced through near-net-shape injection molding.
We have many years of experience in the production of such blanks and can also reliably injection mold larger wall thicknesses without cavities.
Compared to instruments made of metal, such components allow X-ray transparency, are non-magnetic, lighter and can also be colour-coded. In addition to cutlery and applications in the operating theatre, such medical injection molded components are used in neurosurgery, e.g. for head mounts or also as trial implants.
FERROMATIK MILACRON EUROPE ELEKTRA 300 injection moulding machine was built in Germany in 2000. The machine produces high-quality plastic products using the injection moulding method. The plastic is fed into plate-mounted injection moulds with a height of 200 to 670 mm, and then welded with a force of 300 tonnes to produce items with the right shape and properties.
With our comprehensive portfolio of Medical Grade MT materials, we offer a very high variety of materials in injection molding in medical technology and thus excellent choices for individual applications. In addition, we offer extensive injection molding materials expertise for an application-specific material development with in-house compounding.
We can injection mold our own thermoplastic composites into medical components that are used, for example, in operating theatre robots.
The FERROMATIK MILACRON E300-S injection moulding machine is equipped with, among others, a large screw with a diameter of 60 mm and an operator panel located on the body of the machine with a FERROMATIK MILACRON IQT 33 CNC controller installed, allowing full control of all process parameters and programming of operating modes. The total weight of the FERROMATIK MILACRON ELEKTRA 300 S injection moulding machine is 17460 kg.
For decades, we have been developing and manufacturing durable medical and surgical instruments with specific requirements for cleaning, disinfection or sterilisation, chemical resistance and the necessary mechanical strength, surface quality and freedom from burrs using plastic injection molding and as assembled subassemblies.
Our injection molded medical products are used, among other things, in diagnostic and operating theatre equipment, where they take over important mechanical functions, such as dry lubrication, reduce wear and, of course, ensure the necessary mechanical strength.
GETTING A QUOTE WITH LK-MOULD IS FREE AND SIMPLE.
FIND MORE OF OUR SERVICES:
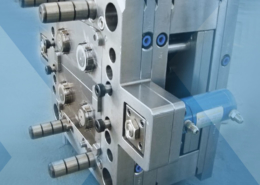
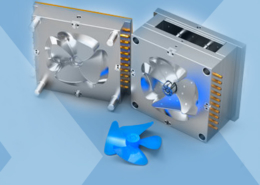
Plastic Molding

Rapid Prototyping
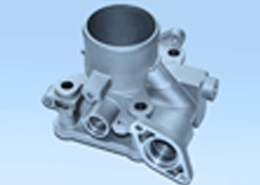
Pressure Die Casting
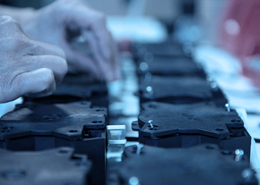
Parts Assembly
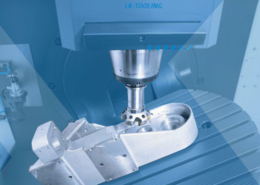