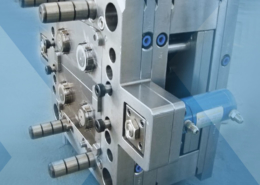
2 Shot Plastic Injection Molds - 2 shot molding
Author:gly Date: 2024-10-15
Prior to issuing a final acrylic molding design, Rebling’s team will review your part design and offer suggestions to ensure that the end product meets the design intent.
When adding text choose embossed text over engraved text as it is more economical when creating the mould. Raising the text 0.5mm above the part surface will ensure the letters are easy to read.
Commercially, injection moulding offers a flexible, consistent and cost-effective process of manufacturing that allows for rapid production of parts in a range of materials. Once the process has been set up and tested, machines can produce thousands of items per hour and once the mould is created (which is the most expensive element) the cost of production per component is relatively low.
Copolymerizing acrylic with other monomers can alter its properties. For example, the addition of ABS significantly improves impact strength. When acrylic is blended with polycarbonate, the resulting impact strength of the copolymer is higher than polycarbonate by itself. The impact strength of acrylic and its copolymers decreases, however, as the ambient temperature decreases.
Acrylic molding can sometimes be complicated. Acrylic is somewhat notch sensitive, so sharp edges should be avoided. Wherever possible, outside and inside corners should include a radius to minimize this notch sensitivity. The metal inserts used in insert molding should avoid sharp corners and edges to minimize the notch sensitivity of this material. Undercuts or entrapments should be avoided since they would break or fracture during part ejection. When necessary for part function, these features need to be incorporated through the use of slides in the mold which can increase the mold cost significantly.
When even the maximum recommended wall thickness is not enough to meet the functional requirements of a part, ribs can be used to improve the strength and stiffness of a part.
Here at UNSW we have 2 CR Clarke desktop injection moulders great for learning, testing and experimenting with the process!
Injection moulding is a manufacturing process that melts, injects and sets plastic into a metal mould. The plastics used by injection molding processes are relatively cheap and can be used to achieve a wide variety of properties, so injection molding is popular for creating many packaging and consumer products, like LEGO!
Draft angle is a taper applied to the vertical walls of the component to be moulded to assist with releasing the part. Walls without draft angle may become stuck in the mould and will have drag marks on their surface.
Injection moulding typically produces parts with tolerances of +/- 0.25mm. Tighter tolerances can be possible in certain situations but increase the cost of manufacture dramatically.
As the plastic shrinks, it applies pressure on the mold. During ejection, the walls of the part will slide and scrape against the mold, which can result to drag marks.
Undercuts refer to part features that cannot be manufactured with a simple 2-part mould because material is in the way while the mould opens or during the ejection of the part. Avoiding undercuts all together is usually the best options as they add cost, complexity and maintenance requirements to the mould.
In addition to the glass-like optical qualities of acrylic, the material is also noted for its resistance to ultraviolet and fluorescent lighting effects, excellent weatherability, and resistance to scratching. Several grades of acrylic material are suitable for food contact use, and because it is odorless and tasteless, it is used in applications such as refrigerator drawers and food storage containers. These molding compounds resist water, alkaline solutions, and weak acids but are dissolved by most organic solvents such as strong hydrocarbons, esters, and ketones.
Acrylic is one of the clear plastic molding materials the Rebling team is experienced at. Rebling has plastic injection molded acrylic for a variety of applications including lighting equipment, housewares and medical devices. If you are interested in acrylic molding, let’s first examine what acrylic material is. Acrylics are synthetic plastic materials that contain at least one derivative of acrylic acid. Acrylic material was first created in 1843 and patented nearly 100 years later by German chemist Otto Rohm The most common acrylic plastic is polymethyl methacrylate (PMMA).
For interior edges, use a radius of at least 0.5 x the wall thickness. For exterior edges add a radius equal to the interior radius plus the wall thickness to ensure constant thickness everywhere. This can also help to stop stress concentrating in the sharp corners which can cause weaker parts.
Trapped air in the mold can inhibit the flow of the material during injection, resulting in an incomplete part. Good design can improve the flowability of the melted plastic.
Redesigning the part to remove undercuts or moving the part line can be possible solutions to make the design more feasible.
When certain sections cool (and as a result shrink) faster than others, then the part can permanently bend due to internal stresses.
The uniform wall thickness limitations also applies to edges and corners; the transition must be as smooth as possible to ensure good material flow through the mould.
Acrylic material has a Tensile Strength in the range of 8000-10,000 psi; a Flexural Modulus in the range of 425,000 psi and a Heat Deflection Temperature of over 210°F for some heat resistant grades.
Belonging to the class of amorphous thermoplastics, Acrylic possesses predictable material shrinkage values. Close tolerances are readily achievable with this material when using the plastic injection molding process at Rebling. High flow formulations necessary for molding thin-walled, difficult to fill parts are utilized by Rebling.
When designing ribs, use a thickness equal to 0.5 x the main thickness, define a height smaller than 3 x the rib thickness and use a base fillet with a radius greater than 1/4 x the rib thickness. Also make sure to add draft angle!
Bosses consist of cylindrical projections with holes designed to receive screws and other fasteners and assembly hardware, they are very common in injection moulded parts as they are used as points of attachment or assembly.
To avoid warping and sink marks on the part as the melted material cools down it is important to have uniform wall thicknesses and avoid thick sections if possible.
Acrylic can be decorated using pad printing, hot stamping, and silk screening processes. Rebling has joined plastic injection moldings using both ultrasonic welding and solvent welding techniques. Machining operations; such as drilling, threading, tapping, routing, and turning; are additional services provided by Rebling on this material and other clear plastic injection molding materials.
If sections of different thicknesses are required, make the transition as smooth as possible using a chamfer or fillet. This will allow the material to flow more evenly through the mould.
Typical of part requirements for acrylic applications is the high degree of optical clarity and light transmittance afforded by these molding compounds. Light transmittance is 92%, which is comparable to optical quality glass. These optically clear plastics withstand exposure to UV radiation and will not discolor or fade when exposed to light. Acrylic material is also readily available in translucent and opaque colors that can be formed using the plastic injection molding process. Molding metal inserts into acrylic, commonly referred to as insert molding, is routinely performed at Rebling.
The outer diameter of the boss should be 2x the nominal diameter of the screw or insert and its inner diameter equal to the diameter of the core of the screw.
When 2 flows meet, small hair-like discolorations may develop. These knit lines affect the parts aesthetics, but also they generally decrease the strength of the part.
When the interior of a part solidifies before its surface, a small recess in an otherwise flat surface may appear, called a sink mark.
Thick sections can lead to various issues such as warping and sinking. Reducing the maximum thickness of the design can be achieved by making the thicker sections hollow is essential. To improve the strength of these sections, ribs can be used to create structures that are of equal strength and stiffness but with reduced wall thickness and weight.
GETTING A QUOTE WITH LK-MOULD IS FREE AND SIMPLE.
FIND MORE OF OUR SERVICES:
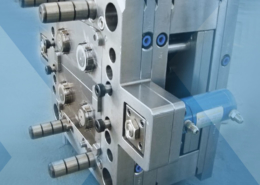
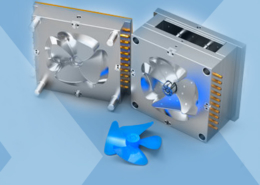
Plastic Molding

Rapid Prototyping
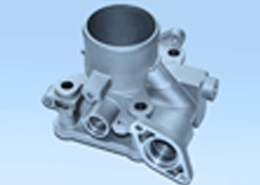
Pressure Die Casting
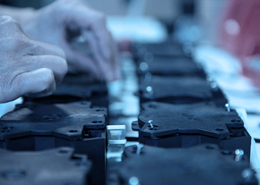
Parts Assembly
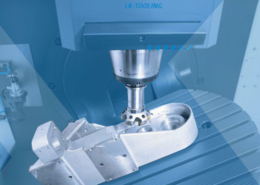