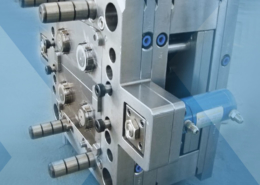
2 Shot Injection Molding: Advantages, Process, and ... - two shot moulding
Author:gly Date: 2024-10-15
This tough, impact-resistant plastic is widely used across industry. With good resistance to acids and bases, ABS also offers low shrinkage rates and high dimensional stability.
Moulds can be made of single or multiple cavities. Multiple cavity moulds can have identical parts in each cavity or can be unique to create parts of different geometries. Aluminium moulds are not best suited to high volume production or parts with narrow dimensional tolerances since they have inferior mechanical properties and can be prone to wear, deformation and damage due to the injection and clamping forces. While steel moulds are more durable they are also more expensive than aluminium moulds.
PMMA, also known as acrylic, provides good optical properties, high gloss and scratch resistance. It also offers low shrinkage and less sink for geometries with thin and think sections.
Good electrical properties makes PBT ideal for power components as well as automotive applications. The strength ranges from moderate to high depending on glass fill, with unfilled grades being tough and flexible. PBT also shows fuels, oils, fats and many solvents, and it also doesn’t absorb flavours.
Injection moulding has a great many applications for manufacturing, particularly for producing high volume parts. While the tooling and moulding can be expensive, the cost of production once this is completed is low. Providing the ability to produce near-identical parts, injection moulding is used for parts in a variety of material types.
Mold life affects mainly the tooling cost. Prototype molds use regular steels such as P20 or 718H. For production molds at higher volume, hardened steel would be required, like NAK 80 or H13.
Injection moulding is mainly used where there is a need to manufacture many thousands or millions of identical parts from a mould.
Advancements in modern injection moulding machinery mean that they now use between 20 and 50% less energy as compared to ten years ago.
The final advantage of injection moulding is that it allows for the production of many identical parts, which allows for part reliability and consistency in high volume production.
“How much does the China injection molding cost to make my product?”; “Is there any way to lower the mold cost in China?”. These are the most common questions we hear from our customers, especially start-ups. It’s quite understandable that the injection molding cost of a new plastic part is critical and sensitive, particularly when your budget is tight for a new design.
The entry cost for injection moulding manufacture can be high – given the cost of the machinery and the moulds themselves.
The part color is the factor that designers and product engineers will neglect, as they assume piece pricing of all colors is the same.
A dimensionally stable material with high toughness, temperature and heat resistance, PPSU is also resistant to radiation sterilisation, alkalis and weak acids.
Injection moulding is a manufacturing process that allows for parts to be produced in large volumes. It works by injecting molten materials into a mould (or ‘mold’ in the United States). It is typically used as a mass production process to manufacture thousands of identical items. Injection moulding materials include metals, glasses, elastomers and confections, although it is most commonly used with thermoplastic and thermosetting polymers.
The main advantage of injection moulding is being able to scale up production to produce a large number of parts. Once the initial costs of the design and the moulds have been covered, the price of manufacturing is very low. The cost of production drops as more parts are produced.
Up-front costs can be high for injection moulding, particularly with regard to tooling. Before you can produce any parts, a prototype part needs to be created. Once this has been completed, a prototype mould tool needs to be created and tested. This all takes time and money to complete and can be a costly process.
Once the mould has been created by the mould-maker, the material for the part is fed into a heated barrel and mixed using a helical shaped screw. Heating bands melt the material in the barrel and the molten metal or molten plastic material is then fed into the mould cavity where it cools and hardens, matching the shape of the mould. The cooling time can be reduced through the use of cooling lines that circulate water or oil from an external temperature controller. Mould tools are mounted on plate moulds (or ‘platens’), which open once the material has solidified so that ejector pins can eject the part from the mould.
The first stage of injection moulding is to create the mould itself. Most moulds are made from metal, usually aluminium or steel, and precision machined to match the features of the product they are to produce.
Minimising the cycle time will aid production as will using machines with hot runner moulds and well thought-out tooling. Such small changes and use of hot runner systems can equal production savings for your parts. There will also be cost savings from minimising assembly requirements, especially if you are producing many thousands of even millions of parts.
There are many factors that can affect the cost on making an mold and running molding production. Here we show you three examples how the various pricing might have. Please note that the price can vary depending on your parts size, weight and complexity.
With over 85,000 commercial plastic material option available and 45 polymer families, there is a wealth of different plastics that can be used for injection moulding. Of these, the polymers can be broadly placed into two groups; thermosets and thermoplastics.
However, if your part is white or transparent, the molding price will be higher than other regular colors. A cleaner molding condition adds cost for molding factories.
Mirror polishing adds cost to injection molding, which requires hardened steels (NAK 80 Steel) to create the molds and cleaner injection molding condition. Also, a higher texturing requirement is another reason to cost increases.
The most common types of plastic used are high-density polyethylene (HDPE) and low-density polyethylene (LDPE). Polyethylene offers a number of advantages including high ductility levels, good tensile strength, strong impact resistance, resistance to moisture absorption, and recyclability.
Injection moulding is used for a range of applications where a repeatable manufacturing process is required. This includes manufacturing items such as wire spools, packaging, bottle tops, toys, combs, musical instruments (and components), chairs, small tables, storage containers, mechanical parts, and automotive parts and components.
Bearing these factors in mind, a small single cavity injection mould costs between $1,000 and $5,000. Larger or more complex moulds can cost $80,000 or more. However, on average, a typical mould costs around $12,000.
Injection moulding is also not ideal for producing large parts as a single piece. This is because of the size limitations of injection mould machines and the mould tools. Items that are too large for an injection moulding machine’s capability need to be created as multiple parts and joined together later.
Injection moulding also produces minimal wastage when compared to traditional manufacturing processes like CNC machining, which cuts away excess materials. Despite this, injection moulding does produce some waste, mainly from the sprue, the runners, the gate locations, and any overflow material that leaks out of the part cavity (also called ‘flash’).
The final disadvantage is that large undercuts require experienced design to avoid and can add even more expense to your project.
Commonly known as acetal, this plastic has high hardness, stiffness, strength and toughness. It also has good lubricity and is resistant to hydrocarbons and organic solvents. Good elasticity and slipperiness also provide advantages for some applications.
PEI (or Ultem) offers high temperature resistance and flame retardancy, along with excellent strength, dimensional stability and chemical resistance.
This strong, impact resistant plastic has low shrinkage and good dimensional stability. A transparent plastic that is available in different optically clear grades, PC can provide a high cosmetic finish and good heat resistance.
It is important to determine how many parts you wish to manufacture so as to decide whether injection moulding is the most cost-effective production method.
This inexpensive resin material delivers high impact resistance in certain grades but can be brittle in cold temperatures (in the case of propylene homopolymer). Copolymers offer greater resistance to impact while PP is also wear-resistant, flexible and can provide very high elongation, as well as being resistant to acids and bases.
Injection moulding can be performed with a variety of different materials including metals, glass, elastomers, confections and, most commonly, thermoplastic and thermosetting polymers.
Complexity plays a vital role in molding costs. It adds extra works to mold making and more steps on molding production. Tolerance requirements, fine detailing, or the number of undercuts are the main reasons.
There are many different types of PPA (or nylons), each of which has its own advantages. Generally-speaking, nylons offer high strength and temperature resistance as well as being chemically resistant, apart from against strong acids and bases. Some nylons are abrasion resistant and offer good hardness and stiffness with good impact strength.
Injection moulding is used to make a range of widely used products, including common plastic items like bottle tops as well as remote control casings, syringes and more. It is also commonly used for manufacturing larger items such as car body panels.
Injection moulding is becoming more environmentally friendly as machinery becomes more efficient and materials such as thermosetting polymers are capable of withstanding extreme temperatures and conditions.
3D printing and injection moulding are both techniques for producing plastic parts and components, but each manufacturing process has its own advantages and can be used together as complementary manufacturing methods.
The most cost-effective type of injection moulding is rubber injection moulding, which produces a high yield of durable products. In addition, consistent vulcanisation processes with precise temperature controls can lower costs by reducing waste material.
The plastic molding material you selected will affect both tooling cost and piece pricing, which varies from different types of materials.
Injection moulding can be an expensive process, but there are several ways in which you can reduce mould costs, including:
The injection moulding process requires careful design, including the shape and features of the part, the materials for the part and the mould and the properties of the moulding machine. As a result, there are various considerations that need to be taken into account when injection moulding.
Minimising the number of parts and simplifying the geometry of your items will make injection moulding easier. In addition, the design of the mould tool is important to prevent defects during production.
Separate materials can be combined in one part in a type of injection moulding called a two-shot mould. This technique can be used to add a soft touch to plastic products, add colours to a part or produce items with different performance characteristics.
This high temperature, high-performance resin provides heat resistance and flame retardancy, excellent strength and dimensional stability, as well as good chemical resistance.
Moulding costs correlate with the number of cavities in a mould. Fewer cavities require less tooling work, which lowers the manufacturing costs to create an injection mould. The complexity of a part’s design also impact the cost, including factors such as surface finishing, tolerance, threads, detailing and the number of undercuts. Added details such as these will increase the cost, as they require more tooling.
Although there is some material waste with injection moulding it is less than with many other manufacturing processes. Of course, the exact materials used also have a bearing on the environment in relation to how long they last, if they can come from recycled materials and how they are disposed of. There are also considerations around the carbon footprint of the lifetime of the products that are created, including during manufacture.
3D printing, also known as additive manufacturing, is a method of creating a three dimensional object layer-by-layer using a computer created design.
GETTING A QUOTE WITH LK-MOULD IS FREE AND SIMPLE.
FIND MORE OF OUR SERVICES:
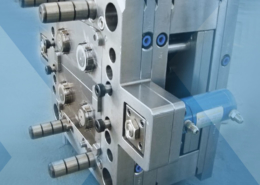
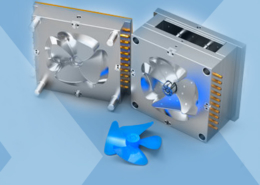
Plastic Molding

Rapid Prototyping
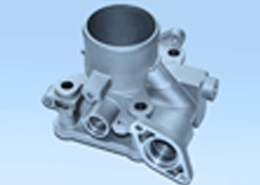
Pressure Die Casting
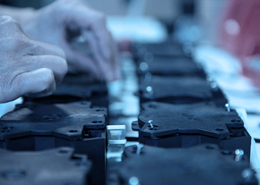
Parts Assembly
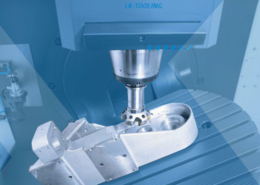