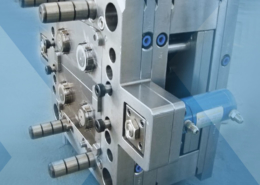
(2PCS x 4FT) BUILDMATE Royu PVC Electrical Moulding 1/2 - electrical plastic mol
Author:gly Date: 2024-10-15
Country Please selectAfghanistanAlbaniaAlgeriaAndorraAngolaAntigua & BarbudaArgentinaArmeniaAustraliaAustriaAzerbaijanBahamasBahrainBangladeshBarbadosBelarusBelgiumBelizeBeninBhutanBoliviaBosnia and HerzegovinaBotswanaBrazilBruneiBulgariaBurkina FasoBurundiCambodiaCameroonCanadaCape VerdeCentral African RepublicChadChileChinaColombiaComorosCongoCongo Democratic RepublicCosta RicaCote d'IvoireCroatiaCubaCyprusCzech RepublicDenmarkDjiboutiDominicaDominican RepublicEcuadorEast TimorEgyptEl SalvadorEquatorial GuineaEritreaEstoniaEthiopiaFijiFinlandFranceGabonGambiaGeorgiaGermanyGhanaGreeceGrenadaGuatemalaGuineaGuinea-BissauGuyanaHaitiHondurasHungaryIcelandIndiaIndonesiaIranIraqIrelandIsraelItalyJamaicaJapanJordanKazakhstanKenyaKiribatiKorea NorthKorea SouthKosovoKuwaitKyrgyzstanLaosLatviaLebanonLesothoLiberiaLibyaLiechtensteinLithuaniaLuxembourgMacedoniaMadagascarMalawiMalaysiaMaldivesMaliMaltaMarshall IslandsMauritaniaMauritiusMexicoMicronesiaMoldovaMonacoMongoliaMontenegroMoroccoMozambiqueMyanmar (Burma)NamibiaNauruNepalNetherlandsNew ZealandNicaraguaNigerNigeriaNorwayOmanPakistanPalauPalestinian State*PanamaPapua New GuineaParaguayPeruThe PhilippinesPolandPortugalQatarRomaniaRussiaRwandaSt. Kitts & NevisSt. LuciaSt. Vincent & The GrenadinesSamoaSan MarinoSao Tome & PrincipeSaudi ArabiaSenegalSerbiaSeychellesSierra LeoneSingaporeSlovakiaSloveniaSolomon IslandsSomaliaSouth AfricaSouth SudanSpainSri LankaSudanSurinameSwazilandSwedenSwitzerlandSyriaTaiwanTajikistanTanzaniaThailandTogoTongaTrinidad & TobagoTunisiaTurkeyTurkmenistanTuvaluUgandaUkraineUnited Arab EmiratesUnited KingdomUnited States of AmericaUruguayUzbekistanVanuatuVatican City (Holy See)VenezuelaVietnamYemenZambiaZimbabwe
Radii and fillets also aid in a part ejection as rounded corners are less likely to get stuck during ejection than sharp corners. Furthermore, sharp corners are also not structurally advisable as they lead to stress points that can fail. Radii help to smoothen out the stress on the corners.
How do I buy a machine?Send us an inquiry on the machine product page via the contact form and one of our sales managers will get in touch with you shortly. If you need help finding the right machine, please send us an email or call – we are happy to help you. Find more information about how to buy used machines down below.
Use our search bar to find the perfect machine for your needs. Explore recycling machines, extrusion lines, flexo printers, and more. Not sure of the name? Just search any requirement, and get relevant results.
We carefully streamline your machine’s data, ensuring it is primed for the sales spotlight. Our dedication extends to investigating transportation, shipping, and logistics, transforming the entire globe into your marketplace through our strategic efforts.
We’re excited to showcase the machine to you. Choose in-person or e-inspection via video. After inspection, we’ll negotiate for a complete agreement. Our services include logistics, dismantling, and potential machine replacement.
However, if not properly designed, this can lead to shrinkage. Shrinkage happens when the cooling rate of certain parts is much faster than others, resulting in the permanent bending of some sections. The warping can be effectively reduced by keeping the rib thickness between 50 – 60% of that of the wall it is attached to.
Bosses shouldn’t be freestanding. Always attach bosses to a side wall or to the floor with ribs or gussets. Their thickness should not exceed 60% of the overall part thickness to minimize visible sink marks on the outside of the part.
One key point for the tool maker to consider is the gate location. Gates are entry sections through which the molten material enters the mould. The tool maker has to choose the type of the gates and position them strategically to minimize potential quality issues.
These features slide in as the mould closes and slide out as it opens. The side cores must move perpendicularly and have appropriate draft angles.
How do I find the price of this machine?We are happy to provide you the price for the machine you’re interested in via email. Please use the contact form down below or email us at info@euro-machinery.com. Mention the machine reference number and one of our team members will reach out to you shortly.
You can also use stripping undercuts, also referred to as bump offs. However, only use this feature when the part is flexible enough to deform and expand during ejection from the mould.
Applying radii to parts, when possible, eliminates sharp corners, which improves the flow of material and the part’s structural integrity. Sharp corners cause weakness in the part as the molten material is made to flow through the corner or into the corner. The only places where sharp corners are unavoidable are the parting surfaces or shut-off surfaces.
How does transport work?Transport is a case by case basis and depends on the size and distance a machine should travel. We work together with the buyer and seller to facilitate transport when a machine is being bought. We have many partners for transport and can help find a supplier to suit your needs.
Snap fits are obtainable through undercuts. The straight-pull mould, which consists of two halves, and is the most straightforward design, is not suitable to manufacture parts with undercut features. This is due to the difficulty in machining such a mould with CNC and the tendency of the material to get stuck on ejection.
To inquire about a machine, click the ‘Request price’ button near the machine you’re interested in. We’ll promptly send you an offer with details and pricing.
Due to the high complexity, it creates in designing, the draft is usually added at the final stages of the part design. Different surfaces require varying drafts. Textured surfaces require the most draft. Some common surfaces found in injection molding and their minimum draft angles are as follows.
This is also referred to as a pass-through core. Another way is to adjust or move the parting line of the part. When doing this, also adjust the draft angle accordingly. Moving the parting lines is most suitable for undercuts that are on the outside of the part.
In order to properly design and manufacture your part using injection molding, it is important for the manufacturer to understand from the outset what your requirements are in terms of its appearance.
We deal in a variety of used machinery for the flexible converting industry, including extruders, recycling machines, granulators, shredders, bag making machines, printing machines, winders, slitters, laminating machines, and more. We facilitate factory-to-factory sales, allowing customers to inspect machinery in production, providing them the opportunity to see the origins and quality of the machines.
Where is the machine located?Most of our machines are located in Europe, but for specific details on this machine please contact us.
By submitting this form, you consent to Euro Machinery collecting, processing, and storing your information in accordance with our Privacy Policy.
Some of the factors that affect the injection molding design include: how the part will be used (singular product or for assembly), its dimensional and mechanical requirements, and its ability to withstand elements such as chemicals or pressure. Some vital tips to consider when designing for injection molding are explored below.
Tolerances are affected by the shrinkage that occurs during the cooling process. Amorphous materials like PLA generally have tighter tolerances than semi-crystaline materials like PEEK.
Many material removal processes such as CNC machining can produce vertical walls. However, creating a part’s design for injection molding with vertical walls will cause the part to get stuck, particularly at the core, as the part contracts on cooling.
Each sales journey is as unique as the machinery we trade. We pride ourselves on crafting personalized experiences that cater to your specific needs. Our commitment revolves around securing the optimal price for you swiftly and seamlessly.
Also, give enough clearance: bump-offs must have a lead angle of 30° to 45° for effective ejection. All these alternatives to expensive side cores require significant redesigning of the part. When the redesign of a part is not possible due to the possibility that it may affect the functionality of the part, then you have to employ sliding side-actions and cores to deal with undercuts.
For example, DIN 16901 contains a general tolerance table as a reference for different materials. If your supplier uses this standard and you need tighter tolerances or other standards, they will ask you to provide 2D drawings.
Bosses are cylindrical standoffs moulded into a plastic part to accept an insert, self-tapping screw, or pin for assembling or mounting parts.
Undercuts are usually created using side cores. However, side cores significantly increase tooling costs. Luckily there are some design tips to achieve the function of an undercut without using side cores. One way of doing this is by introducing a slot instead.
Also, including sharp corners in your part will exponentially increase the cost of production as this would require the mould to feature sharp corners that can only be achieved using very expensive manufacturing techniques.
Tight tolerances make production more expensive, but they may be necessary for your part to fit or function properly, especially if it is used in an assembly.
At Xometry Europe, we offer injection molding services with over 30 materials, such as plastics, synthetic and silicone rubber, and elastomers. Simply head over to our Quoting Engine to upload your model and select your part preferences to receive a 24h quote.
That’s why we recommend letting your supplier know about any aesthetic and functional requirements and defining where not to gate.
Thermoplastic resins can be broadly classified into amorphous and semi-crystalline. While semi-crystalline thermoplastics offer better chemical and electrical resistance, their amorphous counterparts are much more dimensionally stable and more resistant to impact. Material selection can affect the required tolerance level or certain features, like wall thickness.
The injection molding process is widely used in large volume production as it produces comparatively low scrap production and has high repeatability. The versatility of the injection molding process demands much broader design considerations. Most of the design considerations will be made on the mould after setting out the product requirements.
Different injection molding materials offer varying properties. For example, some injection molding materials provide more dimensional stability than others. Similarly, some bond better with adhesives than others. Material design considers the following: temperature, pressure, biological and chemical interactions.
Certain parts require ribs. Ribs and gussets give additional strength to parts and help to eliminate cosmetic defects like warping, sink and voids. These features are essential for structural components. Therefore, it is preferable to add them to parts rather than increase the thickness of parts to increase strength.
The outer diameter (OD) of the boss should be 2.5 times the diameter of the screw diameter for self-tapping applications.
If too much force is applied to eject the part, the risk of damaging the ejector pins and even the mould becomes very high. Design the walls of parts with a slight slant to avoid this problem. This slanting is called a draft.
GETTING A QUOTE WITH LK-MOULD IS FREE AND SIMPLE.
FIND MORE OF OUR SERVICES:
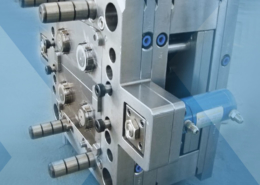
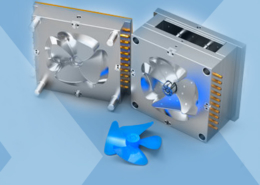
Plastic Molding

Rapid Prototyping
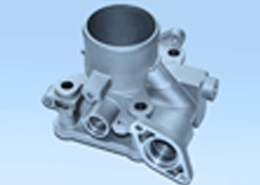
Pressure Die Casting
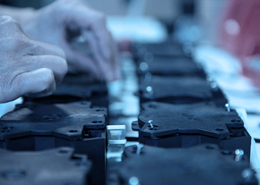
Parts Assembly
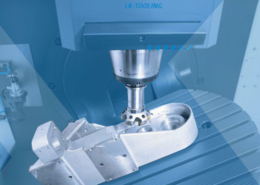