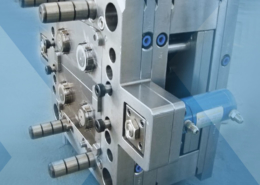
SEMI-FINISHED PRODUCTS: European market for plastic sheets: 10 percent of
Author:gly Date: 2024-09-30
New York, United States, March 12, 2024 (GLOBE NEWSWIRE) -- Injection molding is a mechanism that allows for the mass production of components. It operates by injecting molten materials into a mold. It is typically employed in mass production to manufacture thousands of similar things. Components produced by injection molding include metals, glassware, elastomers, and confections. Although thermoplastic and thermosetting polymers are the most common, other polymers exist. The real benefit of injection molding is its mass manufacturing capability. After initial costs are accounted for, the unit cost of injection-molded items is extraordinarily cheap. The ingredients, such as synthetic resins (plastics), are heated and melted before they are put into the mold and cooled to form the desired shape. This process is referred to as injection molding because it resembles the injection of fluids using a syringe. Materials are melted and poured into the mold, where they solidify before being removed and completed.
Known by its trade name Xarec, the plastic alternative is the first syndiotactic polystyrene (SPS) resin. The innovative structure allows for a variety of highly sought after characteristics. SPS is resistant to hydrolysis; chemically resistant to corrosion by various acids and alkalis, including automobile oil and antifreeze; and also resistant to heat. It also features a low specific gravity, reducing the weight and cost of parts. SPS is a fit for electronic components for various hybrid electric vehicles, as well as an essential component for everyday home appliances. Furthermore, it is viewed as a sound environmental choice.
Asia-Pacific's injection molding machines market share will grow at a CAGR of 6.3% during the forecast period. Due to the region's expanding demand for injection-molded plastics, it is projected that China, India, and Indonesia will contribute to expanding the Asia-Pacific injection molding machine market. This is due to the expansion of the packaging industry. In addition, significant companies such as NISSEI Plastic Industrial Co. Ltd. and Japan Steel Works Ltd. are employing various strategies, such as cooperation, acquisition, and others, to accelerate the expansion of the market.
PPO touts excellent tensile and impact strength while showing resistance to many chemicals, including steam and water; however, it is sensitive to stress cracking. PPO also poses a problem with melt processing because of its high glass-transition temperature. With that, it is often blended with high-impact polystyrene (HIPS) to be used in applications across the automotive and electronics industry, including pump parts, fan impellors, catalyst supports, and more.
Jack Rulander is a senior R&D engineer at Protolabs. He works on introducing new technologies to the company's digital manufacturing process for injection molding. Rulander has nearly 20 years of experience in the plastics engineering industry.
We know it’s frustrating when a material supply is low — especially when you’ve designed molded parts for a specific plastic — but hopefully these alternatives can help you bridge your part design and manufacturing past the material gap.
Supply-chain disruptions have left no part of our industry untouched over the last year. While there is light at the end of the tunnel in our fight against COVID-19, it is apparent the fallout will continue for some time. The impact is only heightened with the recent Suez Canal blockage and a shipping container shortage.
Advantage of Low Labour Cost and Mass Production Along with Material Flexibility and Low Production Waste to Drive the Global Injection Moulding Machines Market
During material shortages, substitution options are available based on desired material properties and the intended function of produced parts. (An extensive list is available on the Protolabs website.) Each lesser-known plastic could work as a replacement for commonly used plastics such as acrylonitrile butadiene styrene (ABS), polycarbonate (PC), and polypropylene (PP).
According to Straits Research, “The global injection molding machines market size had a market share of USD 10,724 million in 2021, expected to advance to USD 16,964 million with a CAGR of 5.9% during the forecast period.” Injection molding is an automated process in which an automatic tool operates efficiently on an injection molding machine. Machines and robots perform the majority of injection molding. These persons are solely accountable for overseeing and managing the process. This automation reduces the labor costs of the process. This drop in labor expenditure is predicted to reduce the cost of manufacturing plastic components. In addition, injection molding can make many identical components every hour.
Europe will hold the second largest market share and is expected to grow at a CAGR of 4.9% during the forecast period. Due to their high quality and energy efficiency, there has been a surge in the usage of all-electric injection molding machines in Europe. In addition, major market participants are spending considerable effort to deliver injection molding machines that fulfill the requirements of their clients by supplying customized and machine-type-based machines. Europe's economic expansion has led to a larger consumer market, indirectly benefiting the injection-molded plastics industry. In addition, the growth of the packaging, automotive, and electrical appliance industries is expected to increase the need for injection-molded plastics, boosting the market for injection molding equipment in Europe.
The disruptions have combined to create a significant material shortage, increasing prices or downright halting the production of plastic-based components. Fortunately, the tremendous innovation we have seen in material development provides options for product developers willing to explore alternatives for commonly used resins.
A vital characteristic of the injection-molding process is its capacity to use many types of plastic to make plastic things simultaneously. Manufacturers may use thermoplastics, thermosetting, or a combination of elastomers in injection molding to get the needed properties. This technique allows for producing more complicated objects with various forms and motifs. In addition, once the mold is prepared, the manufacturer can adjust the component's material and color. This factor is projected to drive the global market for injection molding machines. In addition, injection molding helps to reduce manufacturing waste. The majority of polymers produced by injection molding are recyclable.
Semi-aromatic polyamides like PPA are often a cost-effective alternative to the more expensive, fully aromatic aramids. Featuring a combination of aromatic and aliphatic groups, PPA greatly reduces moisture absorption, which results in few dimensional changes and more stable properties. The material is a great fit for products that must withstand prolonged exposure to harsher chemicals and higher temperatures. With that, common applications are motor parts, coolant pumps, bearing pads, resonators, and more.
This resin is an amorphous, transparent, and pale-amber high-performance thermoplastic that exhibits good melt stability, which permits fabrication by conventional thermoplastic processing methods. PSU also has outstanding mechanical, electrical, and thermophysical properties, as well as excellent chemical and hydrolytic stability. The characteristics come together to make the resin a tremendous fit for components that are exposed to steam and hot water, like plumbing components, sterilizable plastic parts for medical devices, and membranes for water treatment, gas separation, and more.
March 12, 2024 10:35 ET | Source: Straits Research Private Limited - Reed Intelligence Straits Research Private Limited - Reed Intelligence
Whether you are looking at business sectors in the next town or crosswise over continents, we understand the significance of being acquainted with the client’s purchase. We overcome our clients’ issues by recognizing and deciphering the target group and generating leads with utmost precision. We seek to collaborate with our clients to deliver a broad spectrum of results through a blend of market and business research approaches.
Straits Research is a market intelligence company providing global business information reports and services. Our exclusive blend of quantitative forecasting and trends analysis provides forward-looking insight for thousands of decision-makers. Straits Research Pvt. Ltd. provides actionable market research data, especially designed and presented for decision making and ROI.
PPS features a very high melting point and poor solubility, requiring special processing to manufacture parts out of the resin. But in the end, PPS has outstanding heat and chemical resistance, good dimensional stability, and high tensile and structural strength due to its aromatic ring structure. Parts made with PPS also feature flame-retardant capabilities and exceptional electrical properties, making it a widely used polythioether. Common applications include electrical and electronic parts, and mechanical parts in automobiles and precision engineering.
Utilizing injection molding machinery permits the actual mass production of injection-molded plastic components. The injection molding machine is the most effective and energy-efficient way of mass-producing plastic products. The rise of the global injection molding machines market is propelled by the multiple qualities of injection molding machines, such as their durability, user-friendliness, higher manufacturing rates and rapid production, and high quality. Rapidly increasing industrial investment and robust demand for injection-molded polymers in the automotive and healthcare industries are driving the expansion of the global injection molding machine market. In addition, industry leaders' manufacturing of energy-efficient, fully automated injection molding equipment stimulates the expansion of the injection molding market. Market participants provide injection molding machines in numerous sizes and designs to meet customers' needs.
A plastic resin shortage hasn't slowed down operations at Protolabs’ injection molding facility in Rosemount, MN. Image courtesy Protolabs.
Increasing production rates and rapid injection molding output are predicted to boost global injection molding machines market growth. In addition, injection molding allows for producing plastic components with various finishes, including light texture, medium texture, pad printed, smooth, and screen printed. Consequently, it is projected that cheap labor costs and mass manufacturing associated with injection molding machines will promote market growth.
GETTING A QUOTE WITH LK-MOULD IS FREE AND SIMPLE.
FIND MORE OF OUR SERVICES:
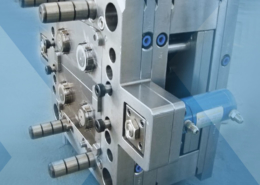
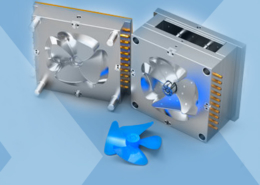
Plastic Molding

Rapid Prototyping
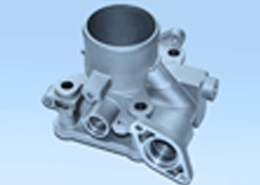
Pressure Die Casting
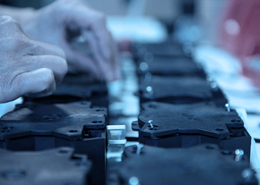
Parts Assembly
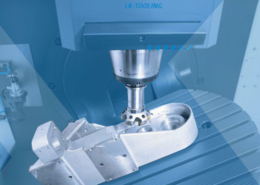