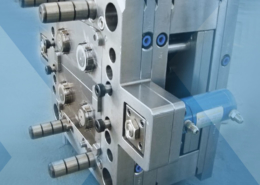
‘Mini’ Low-Pressure Injection Machine Makes Large, Thick Parts at Low Cost - sma
Author:gly Date: 2024-09-30
Luckily, the company’s quoting system quickly responds to enquiries within 24 hours by our allowing “On-time delivery — every time, no exceptions.” Request a quote from WayKen Rapid online now at WayKen.com.
As far as resolution is concerned, the accuracy of CNC machining at WayKen is typically higher than 3D printing, between 0.02mm and 0.05mm – 0.10mm depending on geometry. Turnaround time for 3D printing is typically faster at just 2-5 days versus 3 – 8 days for CNC. This does however come at a tradeoff with the volume of products than can be produced. A typical SLA/SLS run can create 1 – 10 parts, whereas CNC has a range of 1 – 50.
The rapid production time of 3D printing means it is finding increased uses throughout the medical industry. WayKen SLA & SLS 3D printing for medicine can be used to make hand held appliances, concept models, and new devices in low volume, e.g. diagnostic equipment, surgical instruments, electronic apparatus and ultrasonic systems. These devices are valuable for surgical planning, simulation and also to map dental correction procedures.
CNC operation is determined by computer aided design (CAD) or computer aided manufacturing (CAM) data translated into Gcode – as used by 3D printers. The precision tool path in a CNC system creates an excellent surface finish, and parts can be sanded and finished on the same machine.
WayKen specializes in an ability to machine a range of plastics (opaque and optically clear) and aluminum. In the CNC process, a toolhead gradually subtracts material from a solid block. As such, molecular stability of the base material remains constant producing a part with unparalleled tensile strength.
3D printing services at WayKen are primarily laser-powered, offering a high level of speed and accuracy. WayKen stereolithography (SLA) is a UV based curing process, and selective laser sintering (SLS) uses a carbon dioxide laser.
Often used as a reliable, lightweight, and cost-efficient way to manufacture parts that meet varying industry standards and FDA approval, sourcing activity for plastic injection molding services has increased more than 127% month-over-month on Thomasnet.com.
For example, when the staff at Fox Chase Cancer Center, a Philadelphia-based research hospital, realized their suppliers would not be able to scale to meet surging testing requirements, they turned to Araten and The Rodon Group for a solution. Although Rodon had never previously produced throat or nasal swabs, they quickly designed a custom swab for Fox Chase that allowed for better collection and release of patient samples.
The competitive price point for all services, according to the company’s website, is “normally 30%-50% less than the US/European prices, due to lower labor costs. Moreover allowing a quick project start compares to other rapid prototype companies.”
One of the main advantages of this process is material availability as virtually any material can be CNC machined. For this reason, and its use in industry since the 1940s, CNC machining remains the most common means of prototyping to date
In some cases, it may even be beneficial to combine both additive and subtractive manufacturing process to complete an end goal. As an example, SLA and SLS could be used as a preliminary stage before moving the CNC machining.
“By utilizing our high-volume plastic injection molding capabilities and applying our turnkey manufacturing solutions, our team produced a new fluid trap-tip swab that meets the strict requirements for use in the medical field,” explained Araten. “This swab makes the testing process more comfortable for patients and more effective for medical professionals.”
Established in Hong Kong and located in Shenzhen, WayKen is a contender for China’s most experienced prototype manufacturer. The WayKen Prototype shop operates across two sites, one for plastic and one for metal. In total, the facilities span 20,000 square feet, employing over 60 dedicated personnel. WayKen’s specialist prototyping services include 3D printing (particularly SLA and SLS), CNC milling and rapid tooling technology.As a service bureau operating within high value automotive, medical, and aerospace industries, WayKen Rapid’s expertise is in selecting the right technology for the specific application, and delivering results at a cost competitive with the west.
With COVID-19 still a global concern and healthcare facility testing needs still high, the demand for medical plastic injection molding services shows no signs of slowing down. In fact, plastic injection molding services were the fifth most-sourced service across the entire Thomas Network in Q3 2021.
SLS and SLA 3D printing are useful for fast response solutions. With digital operational tools like slicer software, the process does not require as much specialized training as CNC machining. With little labour involved, the manufacturing cost of 3D printing is priced based on the amount of materials. As larger parts cost more 3D printing is advantageous for small volumes and lightweight parts. Realtively simple structures, wth less demand for surface quality and precision parts, also benefit the most from WayKen’s 3D printing services. The technology is ideal for protoyping small medical devices, industrial tooling, and outer covering of electrical tools.
According to Thomas data, demand specifically for medical injection molded plastics has also risen more than 153% year-over-year and 106% quarter-over-quarter, most notably fueled by the COVID-19 pandemic. With more than 363,000,000 tests conducted in the U.S. alone since the beginning of the pandemic, the medical and pharmaceutical industries have been pushed to their limits and healthcare providers have had to find innovative solutions to meet the growing need for accurate and efficient testing swabs.
“Plastic injection molding offers several advantages that metal parts just can’t match, including less material waste, increased traceability, enhanced compliance with industry regulations, and high-temperature resistance and tolerances,” said Michael Araten, CEO of The Rodon Group, a U.S.-based, third-generation plastic injection molding business.
CNC machined parts at WayKen on the other hand can be used to make functional prototypes which are suitable for engineering evaluation and testing. In contrast to the SLA and SLS services offered, CNC machining requires specially trained engineers to pre-program the processing parameters and toolpaths, then machine according to the programs. Manufacturing costs are therefore quoted taking the extra labor into account. CNC’s advantage is for machining parts with special requirements such as dimensional tolerances and surface qualities.
This article was sponsored by The Rodon Group, an ISO 9001:2015 certified, high-volume custom plastic injection molder. To learn more about Rodon’s nasal testing swabs in their latest case study or to secure sample collection swabs for your testing needs, click here.
The question is – which technology should you choose? As a WayKen spokesperson states, “it is very difficult to get a standard answer to the cost comparison between 3D printing and CNC machining.” Instead, technology should be selected based on application.
With demand for plastic molded parts rising, driven in particular by major end-use industries, the plastic injection molding market is currently projected to reach over $513 billion by 2026.
“Traditional” processes at WayKen cover CNC plastic/metal parts machining, vacuum injection molding and rapid injection molding. In the case of CNC machining, a solid block of raw material can be used.
In automotive, WayKen applies a plethora of CNC prototyping and rapid tooling methods to the production of spare parts. The services are useful to car manufacturers running limited trials of a car/motorcycle, and allow volume customization. WayKen automotive rapid prototyping is delivered as a complete service, guiding customers through proof of concept design reviews and mechanical component engineering tests, to show car projects and exterior/interior prototypes.
With a turnaround time of only a few weeks, The Rodon Group now expects to produce as many as 50 million swabs per year. The swab is FDA registered and is anticipated to soon receive ISO 13485 certification.
With a predicted 4.6% annual growth rate over the next seven years, there is a clear expectation for sustained growth through Q4 2021 and beyond.
Approximations of the general parameters of each process are detailed on WayKen.com in the company’s Technology Selection Guide, and a supporting Materials Selection Guide.
The primary SLA material used by WayKen is an ABS-like photopolymer, suitable for use in the lost-wax method of casting favoured in jewelry making and dental industries. SLS uses powdered Nylon feedstock, which acts like a support material throughout 3D printing, cutting down post-processing times. Parts made using SLS also benefit from the potential of nesting meaning that more designs can be 3D printed within the same build.
GETTING A QUOTE WITH LK-MOULD IS FREE AND SIMPLE.
FIND MORE OF OUR SERVICES:
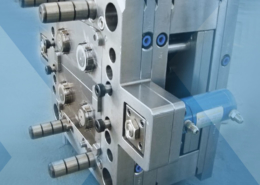
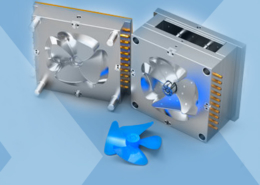
Plastic Molding

Rapid Prototyping
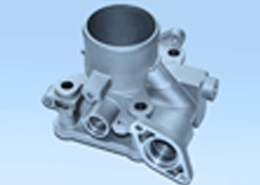
Pressure Die Casting
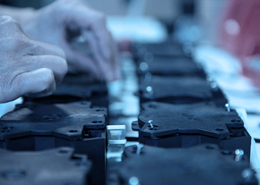
Parts Assembly
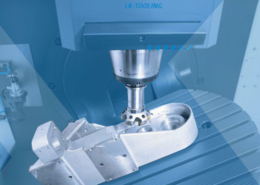