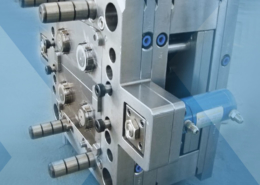
‘Historic’ Nebraska tornadoes, storms leave damage in their wake - strongest inj
Author:gly Date: 2024-09-30
This month’s resin pricing report includes PT’s quarterly check-in on select engineering resins, including nylon 6 and 66.
Say “manufacturing automation” and thoughts immediately go to the shop floor and specialized production equipment, robotics and material handling systems. But there is another realm of possible automation — the front office.
The biggest difference between 3D printed objects and 3D knitwear is the material. It is easy to see that much finer structures can be created with threads.
Furthermore, most 3D printers cannot produce fine enough details. Unlike 3D knitting, where the moving threads are processed by many small needles, the extruders of a 3D printer cannot produce anything comparable. The structure and texture of 3D-printed clothing is heavy and pitted, and the surface texture is likely to be quite cold and unpleasant. Gerard Rubio agrees, saying, “At this point, the materials are not developed enough. However, I strongly believe that 3D-printed clothing will be the future.”
Hi! We developed an innovative way to produce textiles with a 3D Printing device. In fact, we make a non-woven fabric, but you have the flexibility to use a wide variety of yarns and there are not gauge limitations. Furthermore, you get shaped pieces and textiles can be disassembled in order to re-use yarns again and again. We are currently at pre-launch phase, but you can get in touch visiting our website! L
One of the most eye-catching tooling exhibits at K 2019 was the debut of the Reversecube from moldmaker FOBOHA. This system divides the rotating cube mold in half horizontally, with the two halves turning by 90° increments in opposite directions. The first commercial system was running at the show, molding and assembling a PP socket and an acetal (POM) roller for a Bosch dishwasher. The innovative 24 + 24 cavity mold ran on a 290-metric-ton Arburg Allrounder Cube 2900.
Join Engel in exploring the future of battery molding technology. Discover advancements in thermoplastic composites for battery housings, innovative automation solutions and the latest in large-tonnage equipment designed for e-mobility — all with a focus on cost-efficient solutions. Agenda: Learn about cutting-edge thermoplastic composites for durable, sustainable and cost-efficient battery housings Explore advanced automation concepts for efficient and scalable production See the latest large-tonnage equipment and technology innovations for e-mobility solutions
Then, we have the woven fabric being sent back to be bleached or dyed at another factory. The harmful substances used in this process mostly end up in the wastewater, which in turn leads to the pollution of rivers and oceans. Lastly, the garment is sewn, knitted, and finished again in a different facility, with a large amount of material being wasted in the manufacturing process. The finished products are sent to the various branches around the world. The unbelievably long transport routes, which significantly increase Co2 emissions, rounds out the disadvantages of conventionally produced clothing. Although there are of course also smaller manufacturers who pay attention to sustainable, fair, and regional production, large-scale fashion producers that use traditional production channels still dominate the clothing market.
In recent years, 3D printing has become growingly everpresent. From medicine, aerospace, to design, and construction — every day there’s news about breakthroughs, innovations, and developments in the additive manufacturing industry. However, in one particular industry, it’s still pretty quiet regarding developments around 3D printing. We’re talking about the fashion industry. It cannot be denied that the first experiments and advances in 3D printed clothing have only been recorded relatively recently. Yet, if you have followed these developments in fashion a little more closely, you may have noticed that these are high-end fashion, i.e. clothing created for the runways and red carpet and not for everyday wear. The reason why the combination of 3D printing and clothing seems so difficult is quite simple: The materials used in 3D printing, mostly plastic, and metal, are not flexible enough. To counteract this problem, some fashion and 3D enthusiasts have been looking into suitable options and ultimately honed in on one solution: 3D knitwear. But, what exactly is 3D knitwear? How does its production method differ from additive manufacturing and conventional textile production? Will 3D knitwear be available as ready-to-wear for ordinary consumers in the near future? We got to the bottom of this topic in more detail and we clarify all of these questions with the help of various expert opinions from the industry.
The manufacturing process of 3D knitted fabrics is quite similar to other 3D objects. Both begin on a computer: CAD software is used to create the design and ultimately to obtain a programming language. The digital codes are then forwarded to the machine, which then begins the manufacturing process. However, the machine used is where knitwear and traditional 3D printing diverge. The primary difference from additive manufacturing is that the machine is not a 3D printer that processes filament or powder through extruders, rather, a knitting machine that can produce a three-dimensional garment in a single pass by uniting it thread by thread. Consequently, it should be noted that the principle is essentially the same both are based on software and are additively manufactured, but the material creates a big difference between the two methods.
I’m looking to do my first production run of urban style and college prep wear. From what I’ve seen you have a great reputation. I would like to see if we can work together. Do you do this garment category? Would you be interested in giving a quote?
Successfully starting or restarting an injection molding machine is less about ticking boxes on a rote checklist and more about individually assessing each processing scenario and its unique variables.
While the melting process does not provide perfect mixing, this study shows that mixing is indeed initiated during melting.
Join Wittmann for an engaging webinar on the transformative impact of manufacturing execution systems (MES) in the plastic injection molding industry. Discover how MES enhances production efficiency, quality control and real-time monitoring while also reducing downtime. It will explore the integration of MES with existing systems, emphasizing compliance and traceability for automotive and medical sectors. Learn about the latest advancements in IoT and AI technologies and how they drive innovation and continuous improvement in MES. Agenda: Overview of MES benefits What is MES? Definition, role and brief history Historical perspective and evolution Longevity and analytics Connectivity: importance, standards and integration Advantages of MES: efficiency, real-time data, traceability and cost savings Emerging technologies: IoT and AI in MES
In this three-part collection, veteran molder and moldmaker Jim Fattori brings to bear his 40+ years of on-the-job experience and provides molders his “from the trenches” perspective on on the why, where and how of venting injection molds. Take the trial-and-error out of the molding venting process.
In this collection of articles, two of the industry’s foremost authorities on screw design — Jim Frankand and Mark Spalding — offer their sage advice on screw design...what works, what doesn’t, and what to look for when things start going wrong.
This is still a touchy subject, with so few companies keeping their value chains and production methods transparent. Obvious and ongoing issues such as child labor, low wages, and inadequate protective measures in low-cost manufacturing countries are joined by the astronomically negative impact the industry has on the environment. From the cultivation of cotton, whereby both the use of pesticides and an enormous waste of water are recorded, to transit once the material has been broken down, and shipped to be processed into yarn and ultimately fabric in another country — this phase alone requires much examination for improvement.
Gifted with extraordinary technical know how and an authoritative yet plain English writing style, in this collection of articles Fattori offers his insights on a variety of molding-related topics that are bound to make your days on the production floor go a little bit better.
In this collection, which is part one of a series representing some of John’s finest work, we present you with five articles that we think you will refer to time and again as you look to solve problems, cut cycle times and improve the quality of the parts you mold.
Indeed, additive manufacturing of apparel faces a number of challenges. As mentioned earlier, the material is probably the biggest obstacle – which is why 3D knitwear is being resorted to. When a closer look is taken at previous projects involving 3D-printed clothing, such as products by fashion designer Danit Peleg, it quickly becomes apparent that the options are limited: The materials compatible with a 3D printer are mostly plastics such as ABS, PLA or the currently very popular and very flexible TPU. Although the latter can be used to create stretchy, movable 3D objects, it doesn’t begin to compare to the soft, comfortable texture of fabric. Although it could now be argued that the majority of conventionally produced clothing is also made of synthetic polymers, i.e. plastic, the problem lies with the texture. It makes a big difference what form the material is in: Fibers and threads have a filigree, elastic and flowing state, whereas filament has a comparatively thick, hard and rigid state.
While prices moved up for three of the five commodity resins, there was potential for a flat trajectory for the rest of the third quarter.
There are many problems with the conventional textile methods of large-scale fashion producers. These include the exploitation of workers in low-wage countries and the negative impact on the environment.
While prices moved up for three of the five commodity resins, there was potential for a flat trajectory for the rest of the third quarter.
For two-component molding, splitting the cube mold into halves that rotate in opposite directions provides thermal isolation and long cooling times for both materials.
While the major correction in PP prices was finally underway, generally stable pricing was anticipated for the other four commodity resins.
With regard to 3D knitwear, other problems are encountered. Rosanne van der Meer particularly emphasized here the difficulty of creating the digital codes for the knitting machine. That is why she relies on extensive databases, suitable non-fiction books and an open-source system. The latter should support New Industrial Order’s goal of creating a workflow that makes the codes for 3D knitwear accessible to all those who show interest. Gerard Rubio echoes this sentiment. He, too, describes developing the right parameters as a major challenge. The road from the prototype to the final, commercializable Kniterate machine, which is very complex, was long and difficult, according to him. Referring to the future, however, Rosanne van der Meer sees no problem in this regard: “The technology is already established and ready to function, but the current system works completely differently.”
Formnext Chicago is an industrial additive manufacturing expo taking place April 8-10, 2025 at McCormick Place in Chicago, Illinois. Formnext Chicago is the second in a series of Formnext events in the U.S. being produced by Mesago Messe Frankfurt, AMT – The Association For Manufacturing Technology, and Gardner Business Media (our publisher).
Plastics Technology’s Tech Days is back! Every Tuesday in October, a series of five online presentations will be given by industry supplier around the following topics: Injection Molding — New Technologies, Efficiencies Film Extrusion — New Technologies, Efficiencies Upstream/Downstream Operations Injection Molding — Sustainability Extrusion — Compounding Coming out of NPE2024, PT identified a variety of topics, technologies and trends that are driving and shaping the evolution of plastic products manufacturing — from recycling/recyclability and energy optimization to AI-based process control and automation implementation. PT Tech Days is designed to provide a robust, curated, accessible platform through which plastics professionals can explore these trends, have direct access to subject-matter experts and develop strategies for applying solutions in their operations.
Plastics Technology covers technical and business Information for Plastics Processors in Injection Molding, Extrusion, Blow Molding, Plastic Additives, Compounding, Plastic Materials, and Resin Pricing. About Us
Take a deep dive into all of the various aspects of part quoting to ensure you’ve got all the bases—as in costs—covered before preparing your customer’s quote for services.
Multiple speakers at Molding 2023 will address the ways simulation can impact material substitution decisions, process profitability and simplification of mold design.
In order to understand the principle of 3D knitwear and its differences and similarities to 3D printing, it is first necessary to take a look at the definitions. Gihan Amarasiriwardena, co-founder and CEO of the Ministry of Supply, defines 3D printing as follows: “In 3D printing, molded products (such as plastics) are produced by adding a layer of material (often plastic or synthetic) according to a given digital Design is ‘printed’.” Rosanne van der Meer, designer and founder of New Industrial Order, offers a broader definition: “3D printing is the production of a three-dimensional shape on the basis of a filament that is formed by a machine.“ In fact, 3D printing is all about computer-controlled machines creating three-dimensional objects and building them up layer by layer. The question now remains whether 3D knitwear is made according to the same principle.
After explaining the numerous advantages offered by 3D knitwear, the question now remains as to why it is not yet increasingly available in stores. What are the current challenges and what improvements may still need to be made? Will 3D printed clothing and especially 3D knitwear be the future of the fashion industry?
Now that the differences and similarities between 3D knitwear and 3D printing have been outlined, the question remains whether and, if so, why 3D knitwear should be preferred to traditionally manufactured clothing. In order to provide a reasonable answer to this, conventional textile production must first be examined more closely.
In this collection of content, we provide expert advice on welding from some of the leading authorities in the field, with tips on such matters as controls, as well as insights on how to solve common problems in welding.
Rosanne van der Meer also adds that she relies on high-quality yarn in order to achieve the best possible results and in order to not run the risk of the thread breaking in the middle of the knitting process and thus having to restart production. A special feature here: even if the thread were to break, the half-finished knitted part could be recycled since the knitwear is designed in such a way that it can be separated again. This means that the material used can be recovered — another sustainability factor. As far as the material is concerned, large savings can be made using 3D knitwear, as the machines produce additively In just one pass and therefore only requires the threads that will be used, thereby eliminating numerous production steps and saving a lot of time and costs. Gihan Amarasiriwardena confirms this statement: “With 3D-printed knitwear, only the required fabric is used. This results in approximately 30% less material waste”. Sustainability also plays a role at Kniterate. Gerard Rubio relies on plant-based yarns, which can be recycled, so items of clothing that are no longer wanted can be disposed of properly and not end up in a landfill.
Compare Desktop 3D Printers Compare Professional 3D Printers Compare 3D Scanners 3D Printing Directory Choose a 3D printer 3D Printing Directory Event Board Job Board Newsletter Advertising
Across all process types, sustainability was a big theme at NPE2024. But there was plenty to see in automation and artificial intelligence as well.
Across the show, sustainability ruled in new materials technology, from polyolefins and engineering resins to biobased materials.
Mold maintenance is critical, and with this collection of content we’ve bundled some of the very best advice we’ve published on repairing, maintaining, evaluating and even hanging molds on injection molding machines.
August 29-30 in Minneapolis all things injection molding and moldmaking will be happening at the Hyatt Regency — check out who’s speaking on what topics today.
Join KraussMaffei for an insightful webinar designed for industry professionals, engineers and anyone interested in the manufacturing processes of PVC pipes. This session will provide a comprehensive understanding of the technology behind the production of high-quality PVC pipes: from raw material preparation to final product testing. Agenda: Introduction to PVC extrusion: overview of the basic principles of PVC pipe extrusion — including the process of melting and shaping PVC resin into pipe forms Equipment and machinery: detailed explanation of the key equipment involved — such as extruders, dies and cooling systems — and their roles in the extrusion process Process parameters: insight into the critical process parameters like temperature, pressure and cooling rates that influence the quality and consistency of the final PVC pipes Energy efficiency: examination of ways to save material and energy use when extruding PVC pipe products
technotrans says climate protection, energy efficiency and customization will be key discussion topics at PTXPO as it displays its protemp flow 6 ultrasonic eco and the teco cs 90t 9.1 TCUs.
Mike Sepe has authored more than 25 ANTEC papers and more than 250 articles illustrating the importance of this interdisciplanary approach. In this collection, we present some of his best work during the years he has been contributing for Plastics Technology Magazine.
What do you think of 3D printed knitwear? Let us know in a comment below or on our Facebook and Twitter pages. Don’t forget to sign up for our free weekly newsletter, with all the latest news in 3D printing delivered straight to your inbox!
Resin drying is a crucial, but often-misunderstood area. This collection includes details on why and what you need to dry, how to specify a dryer, and best practices.
The result, says FOBOHA, is 20% higher output, up to 40% shorter cycle time, and around 40% less floorspace than a conventional system. The single machine system replaces four standard injection molding systems and two assembly lines. (See it in action at short.ptonline.com/RevCube).
Join this webinar to explore the transformative benefits of retrofitting your existing injection molding machines (IMMs). Engel will guide you through upgrading your equipment to enhance monitoring, control and adaptability — all while integrating digital technologies. You'll learn about the latest trends in IMM retrofitting (including Euromap interfaces and plasticizing retrofits) and discover how to future-proof your machines for a competitive edge. With insights from industry experts, it'll walk you through the decision-making process, ensuring you make informed choices that drive your business forward. Agenda: Maximize the value of your current IMMs through strategic retrofitting Learn how to integrate digital technologies to enhance monitoring and control Explore the benefits of Euromap interfaces and plasticizing retrofits Understand how retrofitting can help meet new product demands and improve adaptability Discover how Engel can support your retrofitting needs, from free consultations to execution
When, how, what and why to automate — leading robotics suppliers and forward-thinking moldmakers will share their insights on automating manufacturing at collocated event.
SPE Middle East Office N. ESO:14, Desk 34 Sheikh Rashid Tower, Seventh Floor Dubai World Trade Center P.O. Box 9204 Dubai, UAE
The aim of this presentation is to guide you through the factors and the numbers that will help you determine if a robot is a smart investment for your application. Agenda: Why are you considering automation? What problems are you trying to solve? How and why automation can help Crunch the numbers and determine the ROI
Since 3D knitwear is on-demand production, problems such as overproduction and inventory waste can also be avoided. Large-scale fashion producers are not able to react flexibly and quickly to changes in the market mainly due to long supply chains, which results in overproduction and overstocking. This is a fatal flaw in today’s fast fashion industry, where new collections and goods hit stores nearly every week. And where should the “old” items of clothing go that have not been bought? These resource and energy-intensive manufactured textiles mostly end up in the garbage or are partially incinerated. On-demand production that takes place on-site/in-house could be a solution here. Not only are transport costs and emissions saved as a result, but practically significantly less waste is produced.
However, the experts are confident that 3D printing will play a greater role in the fashion sector in the future and firmly believe that novel technologies will revolutionize it. Rosanne van der Meer summarizes: “Changes in the textile industry are slow. Yes: in the future we will find more additively manufactured clothing, but how far this progress is in the future cannot be said.”
Discover how artifical intelligence is revolutionizing plastics processing. Hear from industry experts on the future impact of AI on your operations and envision a fully interconnected plant.
These social and environmental problems are primary focuses for CEOs Gerard Rubio, Gihan Amarasiriwardena, and Rosanne van der Meer, which is why they all pay attention to sustainability in the development of their companies and in the manufacture of their products. Awareness begins with the procurement of materials: While more than half of all clothing is produced using man-made fibers, mainly polyester, but also nylon, elastane, and acrylic, which are obtained from fossil fuels and therefore have a negative environmental impact; new industrial methods use merino wool which is obtained sustainably and as a natural fiber which generally has a smaller footprint compared to synthetic fibers.
Processors with sustainability goals or mandates have a number of ways to reach their goals. Biopolymers are among them.
Second quarter started with price hikes in PE and the four volume engineering resins, but relatively stable pricing was largely expected by the quarter’s end.
3Dnatives is the largest international online media platform on 3D printing and its applications. With its in-depth analysis of the market, 3Dnatives gets over 1 million unique visitors per month and is currently available in English, French, Spanish, German, Italian. 3Dnatives works with key Additive Manufacturing market players and offers a variety of services such as a 3D printing price comparison engine, B2B consulting and B2B brand content, event management and much more!
Sustainability continues to dominate new additives technology, but upping performance is also evident. Most of the new additives have been targeted to commodity resins and particularly polyolefins.
This goes hand in hand with Rosanne van der Meer’s motto: “The starting point for a better climate balance in the fashion industry is less consumption. If you have timeless clothing that fits you really well, you will also consume less.” Thanks to 3D technologies, it is also possible to personalize 3D knitwear. Since the designs are created digitally and every needle stitch is equivalent to a pixel, patterns can easily be modified and adapted to customer requirements, which allows a lot of freedom. A special program from the start-up Shavatar also helped New Industrial Order to improve the accuracy of fit of their 3D knitwear without a 3D scanner – an essential aspect when it comes to buying clothes. With the help of the open-source system and the knitting machine from Kniterate, users are obviously also open to all creations and personalizations. Last but not least, the typical problems such as the exploitation of workers through in-house, regional productions are also eliminated.
Mixed in among thought leaders from leading suppliers to injection molders and mold makers at the 2023 Molding and MoldMaking conferences will be molders and toolmakers themselves.
This is because on-demand production, which is the principle of most current 3D knitwear manufacturers, completely contradicts the market flow. The current fashion market is based on mass production and mass consumption. Changing long-established systems and breaking habits is extremely difficult, which is why more sustainable companies specializing in on-demand production and customization face a major hurdle in entering the market. Also, in terms of production costs, 3D knitwear cannot compete with conventional clothing due to low market compatibility. Therefore, the current products from New Industrial Order and Ministry of Supply are still rather in the luxury segment in terms of price, within the framework of which customers are willing and able to spend a lot for personalization, sustainability and quality.
Additive technology creates air pockets in film during orientation, cutting down on the amount of resin needed while boosting opacity, mechanical properties and recyclability.
Core Technology Molding turned to Mold-Masters E-Multi auxiliary injection unit to help it win a job and dramatically change its process.
84 countries and 60k+ stakeholders strong, SPE unites plastics professionals worldwide – helping them succeed and strengthening their skills through networking, events, training, and knowledge sharing. For more information, visit www.4spe.org.
Introduced by Zeiger and Spark Industries at the PTXPO, the nozzle is designed for maximum heat transfer and uniformity with a continuous taper for self cleaning.
Despite price increase nominations going into second quarter, it appeared there was potential for generally flat pricing with the exception of a major downward correction for PP.
Thousands of people visit our Supplier Guide every day to source equipment and materials. Get in front of them with a free company profile.
New FOBOHA Compactcube is a simplified system that drastically reduces maintenance time and can be used in a standard machine with extended stroke.
Ultradent's entry of its Umbrella cheek retractor took home the awards for Technical Sophistication and Achievement in Economics and Efficiency at PTXPO.
In a time where sustainability is no longer just a buzzword, the food and beverage packaging industry is required to be at the forefront of this innovation. By adopting circular packaging processes and solutions, producers can meet regulatory requirements while also satisfying consumer demand and enhancing brand reputation. Join Husky to learn more about the broader implications of the circular economy — as well as how leading brands are leveraging this opportunity to reduce costs, increase design flexibility and boost product differentiation. Agenda: The cost and operational benefits of embracing circularity Key materials in circular packaging — including rPET and emerging bioplastics How to design a circular food and beverage package Strategies for selecting sustainable closures to future-proof packaging solutions Optimization and streamlining of production processes for enhanced efficiency How Husky Technologies can enable your sustainable success
We are considering purchasing a clothes-making machine with 3d printing. They are trying to produce clothes made by weaving them with threads, not plastic clothes. Please let me know the name of the machine, the price, and the time to make one top uniform. Please give me your phone number and e-mail address.
After successfully introducing a combined conference for moldmakers and injection molders in 2022, Plastics Technology and MoldMaking Technology are once again joining forces for a tooling/molding two-for-one.
Therefore, it is hardly surprising that industry experts agree in saying that 3D knitted goods are not manufactured using 3D printing, but rather, 3D knitting is a technology in its own right. Gerard Rubio, co-founder, and CEO of Kniterate, a company that sells 3D digital knitting machines, adds the following about his company’s machines and the use of the word 3D in connection with the production method: “These machines are capable of 3D knitting. But these machines are not necessarily 3D knitting machines.” This is because flat, single-layer garments like scarves can also be printed with a Kniterate machine, which eliminates the additive manufacturing aspect. Rosanne van der Meer adds that she deliberately uses the term ‘3D printed knitwear‘ for her products in order to make a clear distinction between 3D knitwear and conventionally produced knitwear.
Learn about sustainable scrap reprocessing—this resource offers a deep dive into everything from granulator types and options, to service tips, videos and technical articles.
FOBOHA also introduced its Compactcube, a simplified “plug-and-play” system for use on standard machines with extended stroke. The system is tailored for shorter runs, because it cuts the time for mold removal and maintenance from five days for a conventional cube mold to a single day. That’s because the Compactcube has no top and bottom shafts for media supply. Instead, there’s an integrated shaft and housing for media supply to the center block. This cube is mechanically driven, like a stack mold, rather than hydraulically or electrically driven like a standard cube. The new system is currently available for machines from 120 to 450 m.t.
The Plastics Industry Association (PLASTICS) has released final figures for NPE2024: The Plastics Show (May 6-10; Orlando) that officially make it the largest ever NPE in several key metrics.
The rationale for splitting the cube is to thermally isolate the two mold halves, one of which is molding PP at a mold temperature of 15-20 C (59-68 F) and the other molding acetal at 80-85 C (176-185 F). What’s more, the PP part is relatively thick, so the mold was designed to provide each component with two cooling stations after injection, with the fourth station reserved for assembly and ejection. With the two materials injected into mold faces 180° apart, the only way to provide two cooling stations for each, and to eject on the same side of the machine, was to split the mold into sections rotating in opposite directions. In the fourth mold station (on the non-operator side of the machine), a six-axis robot demolded the parts while assembling them with a snap fit. In this way, the same cavities and components are always combined, making it easier to track problem cavities.
This Knowledge Center provides an overview of the considerations needed to understand the purchase, operation, and maintenance of a process cooling system.
I’m Kim Kwan Sik in Korea. I’m going to make clothes with 3d printing. Among your products, 3D printing that makes clothes with cloth. If there’s a price, time to make a uniform, and the production period. I would be grateful.
Exhibitors and presenters at the plastics show emphasized 3D printing as a complement and aid to more traditional production processes.
Top half of the FOBOHA Reversecube molds an acetal part at a much higher mold temperature than the lower half, which molds a thick PP part. The two halves turn in opposite directions to give two cooling cycles to both parts and eject them at the same station on the back side of the machine.
GETTING A QUOTE WITH LK-MOULD IS FREE AND SIMPLE.
FIND MORE OF OUR SERVICES:
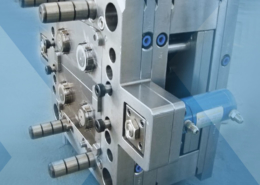
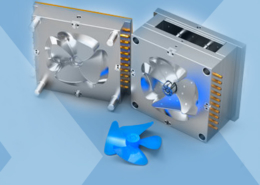
Plastic Molding

Rapid Prototyping
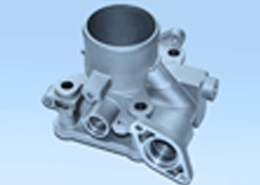
Pressure Die Casting
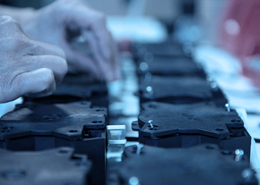
Parts Assembly
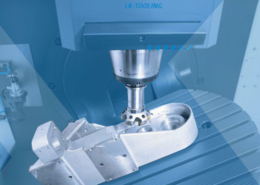