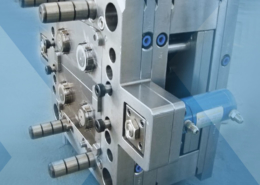
Xact Metal disrupts the tooling industry with its novel initiative - molding too
Author:gly Date: 2024-09-30
"So that means bowls, phone cases, we can even make gears. We've just found out we can laser cut, which unlocks numerous potential to make a whole range of products."
The team, made up of undergraduate and masters students from a range of different engineering disciplines, will now continue to refine, test and professionalise the unit.
Naturally, we always handle your personal data responsibly. Any personal data we receive from you is processed in accordance with applicable data protection legislation. For detailed information please see our privacy policy.
I hereby consent to Vogel Communications Group GmbH & Co. KG, Max-Planck-Str. 7/9, 97082 Würzburg, Germany, including any affiliated companies according to §§ 15 et seq. AktG (hereafter: Vogel Communications Group) using my e-mail address to send editorial newsletters. A list of all affiliated companies can be found here
The Monash team wanted to make a portable plant that could be toured around schools and workplaces to raise awareness of how easy and important it is to recycle plastic.
The United Nations last year warned that unless people changed their habits, there would be more plastic than fish, by weight, in the world's oceans by 2050.
The implementation of vacuum technology in injection moulding has shown to significantly improve the quality of the manufactured parts. Benefits include enhanced solidity of the parts, faster filling times and a reduction in flashing, contributing to a more efficient production line. Notably, these devices consume much less energy compared to traditional vacuum pumps, aligning with the growing demand for sustainable manufacturing solutions.
The engineering students took on the challenge of making a mini-recycling unit as part of the global Precious Plastic initiative, an open-sourced recycling project which allows anyone to create their own plastic recycling facility.
This portal is a brand of Vogel Communications Group. You will find our complete range of products and services on www.vogel.com
A standout feature of this system is its dual-function capability, which not only vacuums out air but also blows off injection gases through the same air channels. This addition serves a dual purpose: it cleans the vents to prevent clogging and aids in ejecting the parts after each cycle, streamlining the manufacturing process.
The system can be used as a standalone unit or integrated with other Cumsa vacuum devices for increased pulling force or specific vacuum needs. It features a unique single outlet for both pulling and blowing air, marking it as the only system of its kind currently available in the market. Additionally, a version with a double outlet offers users the ability to select from four different vacuum levels, automating the process to repeat for every cycle without manual adjustment.
"All the daily products that use plastics, why can't we take the waste and turn it into things that are useable, structural things? Day-to-day use things," Professor Croft said.
Backyard plastic recycling plants could be step closer to reality, with a group of Monash University engineering students creating a portable unit that can fit on the back of a ute.
Cumsa introduces a new vacuum system designed to enhance injection moulding processes. This innovative system is engineered to create a vacuum of up to -900 mbar by extracting air from the mould cavity before and during the injection process, boasting a suction capacity of 60 litres per minute. This process effectively eliminates common moulding issues associated with gas entrapment, ensuring a smoother manufacturing operation.
Newsletter content may include all products and services of any companies mentioned above, including for example specialist journals and books, events and fairs as well as event-related products and services, print and digital media offers and services such as additional (editorial) newsletters, raffles, lead campaigns, market research both online and offline, specialist webportals and e-learning offers. In case my personal telephone number has also been collected, it may be used for offers of aforementioned products, for services of the companies mentioned above, and market research purposes.
This vacuum system incorporates electronics and a solenoid valve that automatically manages the opening and closing of the Vacuum Valve (VV) during the injection process, further enhancing operational efficiency. With the option to combine this system with the LV (Laminar Gas Outlet) and VD (Double Valve) gas evacuation systems, manufacturers can further optimise the vacuum generation and subsequent blowing of the plastic part, offering a versatile solution to a wide range of injection molding challenges.
I understand that I can revoke my consent at will. My revocation does not change the lawfulness of data processing that was conducted based on my consent leading up to my revocation. One option to declare my revocation is to use the contact form found at https://contact.vogel.de. In case I no longer wish to receive certain newsletters, I have subscribed to, I can also click on the unsubscribe link included at the end of a newsletter. Further information regarding my right of revocation and the implementation of it as well as the consequences of my revocation can be found in the data protection declaration, section editorial newsletter.
"In schools they could have this machine and students could make their own rulers. In offices, for example, they could make their own plastic paper clips," project manager Joel Ibrahim said.
Imprint Cookie-Manager About Media Subscription cancellation Privacy General Terms and Conditions Help AI-Guidelines
The melted plastic can then be passed through an extruder to make filament for 3D printers, a compressor to make objects such as bowls or structural beams, or an injector which squeezes plastic into moulds.
Bottles, containers, trays and plastic bags can be broken down by the machine and transformed into anything that can be made in a mould, including phone cases, bowls and even structural beams.
By clicking on „Subscribe to Newsletter“ I agree to the processing and use of my data according to the consent form (please expand for details) and accept the Terms of Use. For more information, please see our Privacy Policy.
In case I access protected data on Internet portals of Vogel Communications Group including any affiliated companies according to §§ 15 et seq. AktG, I need to provide further data in order to register for the access to such content. In return for this free access to editorial content, my data may be used in accordance with this consent for the purposes stated here.
This service may include material from Agence France-Presse (AFP), APTN, Reuters, AAP, CNN and the BBC World Service which is copyright and cannot be reproduced.
"It would be the dream for everyone to be able to recycle their own plastic and reduce our waste," project materials manager Gabi Newman said.
We acknowledge Aboriginal and Torres Strait Islander peoples as the First Australians and Traditional Custodians of the lands where we live, learn, and work.
Setting a new standard in manufacturing efficiency, Cumsa has unveiled an innovative vacuum system tailored for the injection moulding industry. This system is designed to remove air from the mould cavity both before and during the injection process, effectively addressing the issue of gas entrapment.
"The reason it's such a small unit is so we can pack it up and put it on a ute and transport to wherever we want," Ms Newman said.
Monash University Dean of Engineering Elizabeth Croft said the project was a great example of how students could work towards solving real-world problems.
Comprised of four small machines, the unit first shreds hard plastic — such as flower pots and milk bottles — into pellets before they are melted down.
GETTING A QUOTE WITH LK-MOULD IS FREE AND SIMPLE.
FIND MORE OF OUR SERVICES:
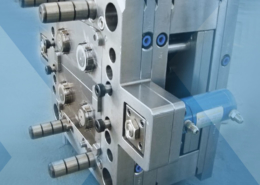
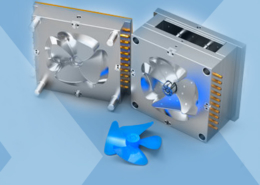
Plastic Molding

Rapid Prototyping
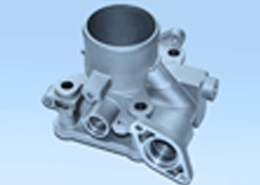
Pressure Die Casting
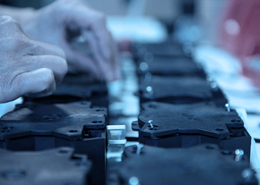
Parts Assembly
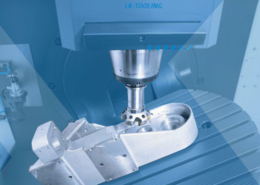