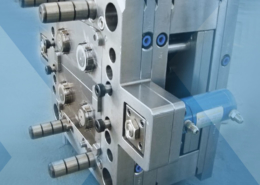
What can old clothes be made into right now? Puzzles, pillows and plastic
Author:gly Date: 2024-09-30
California materials company Checkerspot has launched a casting kit named Pollinator Kit that allows designers to experiment with making components from algae-based plastics.
News from Dezeen Events Guide, a listings guide covering the leading design-related events taking place around the world. Plus occasional updates and invitations to Dezeen events.
The N-SAPLI control system can also be applied to thermoset molding to precisely control the flow of the liquid polymer into the mold, thereby raising the precision of the final part to a tolerance of 0.3 mm compared with the 0.7 mm typically achievable. “We are targeting a precision of 0.2 mm by applying N-SAPLI to the injection-compression molding of a thermoset resin,” added Yoda.
Sent every Thursday and containing a selection of the most important news highlights. Plus occasional updates on Dezeen’s services and invitations to Dezeen events.
News from Dezeen Events Guide, a listings guide covering the leading design-related events taking place around the world. Plus occasional updates and invitations to Dezeen events.
"This strategy pigeonholes renewables, limits the scope of how they can be used and consequently narrows the impact they can have."
We will only use your email address to send you the newsletters you have requested. We will never give your details to anyone else without your consent. You can unsubscribe at any time by clicking on the unsubscribe link at the bottom of every email, or by emailing us at [email protected].
Other designers working on testing the material and process include Waves Not Plastic, a non-profit organization in California.
"This approach marries the efficiency of a highly productive, fast-growing, photosynthetic plant (sugarcane) with the efficiency of a highly productive, fast-growing, oil-producing microbe to make a very precise type of oil," said Checkerspot.
Speaking to PlasticsToday at the event in Japan, Nissei Plastic CEO Hozumi Yoda highlighted the fact that the “760” in the machine’s model name refers to the tie-bar clearance of 760 x 760 mm, rather than the clamping force of 3,540 kN (360 tons). “In general, we feel injection machines tend to be over-specified for the application at hand, with molders tending to ram the resin through the injection cylinder at high pressure and compensating for this with a higher clamping force in the case of thermoplastic molding,” he explained. “Our approach is to optimize injection pressure using our N-SAPLI low-pressure molding system and apply the minimal clamping force.”
"Access to the Pollinator Kit has provided our team at Waves Not Plastic with bio-based materials that have a beginning of life cycle consistent with our mission to reduce the world's reliance on petrochemicals," said founder Jeff Lenore.
Long perceived to be in decline, thermoset resin molding is being revived by two Japanese companies as a process with ample potential to contribute to lightweighting in electric vehicles (EVs). Injection machine builder Nissei Plastic and development partner Sumitomo Bakelite, a supplier of thermoset resins, held an in-house event at the Nagoya Congress Center on Aug. 2 to 4, 2023, in Aichi Prefecture, showcasing multiple thermoset molding solutions and more to 230 companies from the automotive industry, including OEMs and tiers. Home to Toyota Motor and Honda plants, Aichi is considered the capital of automobile manufacturing in Japan.
We will only use your email address to send you the newsletters you have requested. We will never give your details to anyone else without your consent. You can unsubscribe at any time by clicking on the unsubscribe link at the bottom of every email, or by emailing us at [email protected].
Rebeccah Pailes-Friedman, founder of Interwoven Design Group, told Dezeen that her studio has experimented with using the product for prototypes.
It can be used for making small and medium-sized products from jewellery and phone cases to surfboards and furniture and includes resin, a mixer as well as a choice of pigment, which is also made from algae.
"By 3D printing a mold and then casting it in urethane we can see the part, test its durability and function and make any adjustments in the design before sending a part out for vacuum casting or injection molding," said Pailes-Friedman.
Using biotechnology, Checkerspot has been able to create a production method that harvests the oil from algae to create "renewable building blocks" for use in product design.
A third thermoset resin in Nissei Plastic’s liquid silicone rubber (LSR) has potential for applications in battery cell spacers as well as high-voltage EV battery connectors that are water-resistant, to boot. The current material of choice for battery cell spacers, which compensate for cell expansion and contraction during charging and discharge, is EPDM rubber.
"Historically, product designers, hobbyists, and artists have been limited by the materials available to them from commodity-based suppliers," said Checkerspot founder Charles Dimmler
"Manufacturers of raw materials can often overlook these small but powerful groups, opting instead to bring their materials to market via well-known consumer brands."
According to the company, the material has a biomaterial content of 56 per cent and can be used in the same moulds used in fossil-based products. The rest of the mixture is made from fossil-derived isocyanate.
Our most popular newsletter, formerly known as Dezeen Weekly, is sent every Tuesday and features a selection of the best reader comments and most talked-about stories. Plus occasional updates on Dezeen’s services and breaking news.
Aware that someday in the future the emergence of solid-state batteries might transform the material requirements of EV drive systems, this writer suggested a potential alternative application for the battery cell spacers being molded in Nagoya. He duly accepted two samples to take back to his base in Singapore and currently uses them as heat-resistant placemats.
Other novel uses for algae include the limestone composites created from the material by researchers at the University of Colorado.
"The upshot is a lower land footprint, a far lower water footprint, and a low carbon use relative to other ways of making oil."
Microalgal oil is obtained from large industrial facilities, many of which are located in southern Brazil, where after mass fermentation, algae is mixed with sugars and then water is subtracted to produce the oil.
A quarterly newsletter rounding up a selection of recently launched products by designers and studios, published on Dezeen Showroom.
Before the release of the kits, Checkerspot launched a brand called WNDR Alpine that creates skis from a similar algae-based process.
Injection machine builder Nissei Plastic teams up with materials supplier Sumitomo Bakelite to expand adoption of EV components molded from phenolic and epoxy resins.
After mixing the two components users must cast the material within 15 minutes and the tack time is approximately eight hours.
Stephen has been with PlasticsToday and its preceding publications Modern Plastics and Injection Molding since 1992, throughout this time based in the Asia Pacific region, including stints in Japan, Australia, and his current location Singapore. His current beat focuses on automotive. Stephen is an avid folding bicycle rider, often taking his bike on overseas business trips, and is a proud dachshund owner.
Our most popular newsletter, formerly known as Dezeen Weekly, is sent every Tuesday and features a selection of the best reader comments and most talked-about stories. Plus occasional updates on Dezeen’s services and breaking news.
Traditionally, thermoset injection molding has been utilized in Japan to mold relatively small components for the electrical sector, typically weighing in at 150 g or less. Nissei Plastic and Sumitomo Bakelite, however, have their sights set on components tipping the scales at 1 kg or more for applications such as e-axle invertor covers. Prototype parts molded on a Nissei FWX760III-130BK thermoset injection molding press using biomass-derived phenolic resin tip the scales at 1.4 kg but nevertheless are reportedly 50 to 70% lighter than conventional steel covers and 20 to 50% lighter than aluminum versions.
Another area where Sumitomo Bakelite and Nissei Plastic are propelling innovation is in the encapsulation of circuit boards, which is conventionally carried out using the more costly and lower precision transfer molding process. Precision control of injection pressure at low levels is critical in this application to prevent damage to the circuit boards. “Typically, you need to limit injection pressure to less than 13 MPa and we have demonstrated on our FNX110III-18AK press that we can control pressure in the range of 6 to 10 MPa,” said Yoda.
At its in-house event, Nissei Plastic exhibited the 180-tonne clamping force NEX180III-5ELM all-electric press outfitted with a dosing system from Elmet and its own spiral plunger system that combines the first-in/first-out benefits of an inline screw with the dosing accuracy of a plunger system.
The Pollinator Kit is a direct-to-designer kit that allows producers to experiment with algae-based materials designed to replace traditional polyurethane resin – a fossil fuel-derived product found in many household items.
Checkerspot said that the kits were designed both for designers already using polyurethanes at scale as well as novices who want to begin working with resins.
A quarterly newsletter rounding up a selection of recently launched products by designers and studios, published on Dezeen Showroom.
Sent every Thursday and containing a selection of the most important news highlights. Plus occasional updates on Dezeen’s services and invitations to Dezeen events.
GETTING A QUOTE WITH LK-MOULD IS FREE AND SIMPLE.
FIND MORE OF OUR SERVICES:
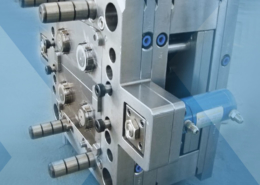
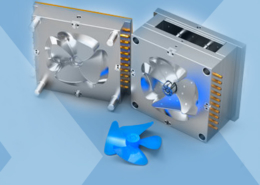
Plastic Molding

Rapid Prototyping
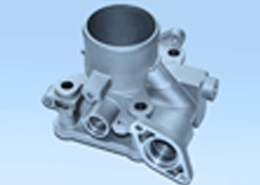
Pressure Die Casting
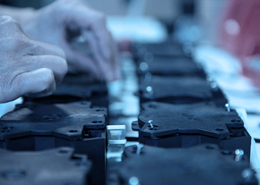
Parts Assembly
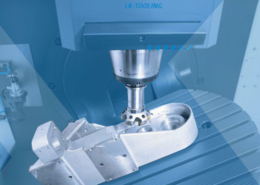