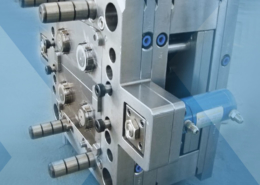
What biodegradable material possesses the hardness of conventional plastic? - bi
Author:gly Date: 2024-09-30
Cobots offer injection molders unique benefits over traditional gantry robots, Buse continued. For instance, manufacturers with more compact production floors and low ceilings can’t always accommodate tall gantry robots.
UR’s Injection Molding Machine Interface (IMMI) has provided a new level of automation connectivity to the plastics industry since its introduction in 2020, said Christopher Buse, application engineer for UR. Because of the pandemic hiatus, NPE2024 was the first time the IMMI was shown at an NPE.
The famous bowtie emblem of GM's Chevrolet brand has received a makeover with the application of in-mold decoration (IMD) in the 2013 Traverse model to generate a jewel effect. Processor Eimo Technologies (Vicksburg, MI) worked with fluoropolymer-based film supplier Soliant Films (Lancaster, SC) to perfect the process.
Further, because the cobot can operate without protective shielding, molders don’t have to sacrifice precious manufacturing space.
Universal Robots (UR) is giving injection molders an easy-to-use interface that seamlessly connects its cobots to injection molding machines (IMMs) — a capability made possible thanks to the standardization of IMMs through the Euromap 67 standard.
The famous bowtie emblem of GM's Chevrolet brand has received a makeover with the application of in-mold decoration (IMD) in the 2013 Traverse model to generate a jewel effect. Processor Eimo Technologies (Vicksburg, MI) worked with fluoropolymer-based film supplier Soliant Films (Lancaster, SC) to perfect the process.
“When you need to introduce a robot into that cycle, the robot needs to break into that molding process in order to go into the mold safely, extract the plastic parts, and then get out of there safely to allow the mold to shut again,” Buse explained. “That is what the Euromap 67 plug interface is doing. Users can control the sequence through the cobot’s teach pendant on the screen. The software is already embedded — all you have to do is turn it on when you install the line. When you get the inputs and outputs between both machines, you can start programming.”
The use of in-mold decoration (IMD) technology in the automotive sector has increased exponentially over the last few years and it is being used more and more in applications such as instrument panel trim, console/shifter trim, radio bezels, steering wheel trim, door spears, and switch plates in the interior, to exterior panels like window trim, pillars and rocker panels according to Gregg Greider, program manager at Eimo Technologies.
And, a cobot allows for “cageless automation” — taking parts out of the dangerous, guarded production environment, then reaching outside that area into an unguarded area like a conveyor belt. Users can also program the cobot to perform secondary operations like degating from the runner or presenting parts to a laser marker.
While UR’s UR10 cobot is the most popular among injection molders, Buse said, the IMMI is compatible with all UR cobots, including the UR20 and new UR30. UR’s newest generation of cobots offer more extensive reach into bigger presses up to 750 tons at least. More commonly, machines of 400 tons or less are automated with UR cobots, Buse noted.
The new emblems are much more robust; retaining jewel appearance throughout the life of the vehicle. Previously, emblems were made of translucent acrylic and were vacuum metalized. This process generates 6% more scrap than the new process, and the emblems are thicker, weighing 10% more than the new ones. Emblem sizes vary from ~2 x 6 inches (weighing 0.029 lb) to 3 x 9 inches (weighing 0.070 lb).
Geoff Giordano is a tech journalist with more than 30 years’ experience in all facets of publishing. He has reported extensively on the gamut of plastics manufacturing technologies and issues, including 3D printing materials and methods; injection, blow, micro and rotomolding; additives, colorants and nanomodifiers; blown and cast films; packaging; thermoforming; tooling; ancillary equipment; and the circular economy. Contact him at [email protected].
UR cobots are light enough to be wheeled from machine to machine, as required, Buse added, so users can “treat the cobot more as an operator.” And because UR cobots can be positioned flexibly simply by specifying an orientation through the control screen, users can bolt them to the platen of a press, on the side, or “in any orientation you can think of.”
When connected, the UR cobot is integrated with the IMM’s safety features, including emergency stop circuits and safety doors. As the injection molding machine is running, it tells the cobot exactly what’s going on in real time so the cobot can perform its functions safely at just the right time.
Integrating UR cobots with IMMs is as simple as installing the IMMI plug on the cobot’s controller and running a cable between the injection molder and the cobot, Buse explained. The Euromap 67 IO communication protocol means the IMMI runs on all brands of contemporary IMMs; some older machines can be retrofitted.
"While badging is just starting to gather momentum [with the Chevrolet exterior badging being perhaps the first example], body side moldings, rocker panels, chin spoilers, and even composite roof panels have all been made using IMD in the USA," he adds.
The process involves placement of thermoformed and trimmed IMD film inserts into an injection tool. Eimo worked Soliant to get the top coat of the 0.5-mm-thick film (i.e., the decorative layer that is are similar in thickness to a paint coating) so it would be flexible enough to "mold" to the textured cavity when the injected resin forces the inlay into the cavity of the tool, while ensuring enough durability to withstand the weather and stone impingement. The film itself is based on an alloy of the PVDF fluoropolymer and acrylic resin and boasts good chemical resistance. The casting process for the film also ensures minimized internal stresses.
GETTING A QUOTE WITH LK-MOULD IS FREE AND SIMPLE.
FIND MORE OF OUR SERVICES:
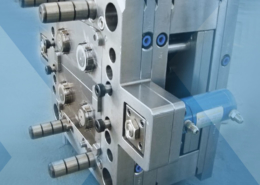
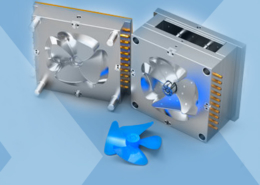
Plastic Molding

Rapid Prototyping
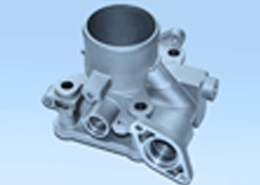
Pressure Die Casting
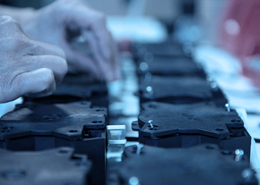
Parts Assembly
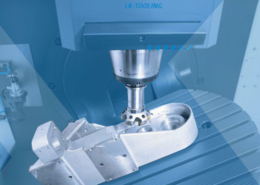