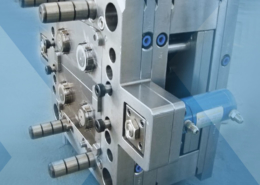
Weatherable PC Copolymer for In-Mold Exterior Automotive Components - pmma moldi
Author:gly Date: 2024-09-30
After investing in a test mold, Greiner Packaging is able to manufacture 500-milliliter thermoformed IML (T-IML) cups with a diameter of 95 millimeters. By switching from injection molding to thermoforming, the cup’s weight was reduced from 15 to 11.4 grams, a 25% reduction, Eisenhuber said.
President Director of Dynapack Asia, Tirtadjaja Hamball, commented: “To support our environmental responsibility, we have signed a global commitment with the Ellen McArthur Foundation to use at least 25% of recycled resin material in our packaging products by 2025. This recycled PET resin facility is another step closer to achieving our commitment.”
Bruce Adams is an experienced content creator and trade publishing veteran who has written extensively about the plastics, automotive aftermarket, hospitality, tire, rubber, mining, and construction industries.
Greiner Packaging has developed a technique for thermoforming cups with in-mold labels (IML) that requires less material, is lighter in weight, and is more recyclable than similar IML cups produced via injection molding.
Greiner Packaging is a leading European manufacturer of plastic packaging in the food and nonfood sectors. Its two business units include Packaging and Assistec. The Packaging unit focuses on packaging solutions and the Assistec unit is dedicated to producing custom technical parts. Greiner Packaging employs a workforce of almost 4,900 at more than 30 locations in 19 countries worldwide. In 2020, the company generated annual sales revenue of €692 million ($783 million), including joint ventures, which represents approximately 35% of Greiner’s total sales.
“Greiner Packaging offers various barrier solutions, which increase protection against oxygen or light and, thus, make food last longer,” Eisenhuber told PlasticsToday. “Our barrier solution of choice is a PP-EVOH-PP combination, which we call multi-barrier technology (MBT). It is hard to make a general statement about how barrier solutions will extend the shelf life of a product," Eisenhuber adds, “as this depends on many factors other than the packaging – such as the filling conditions and the type of filling itself.”
The company will develop packaging solutions based on the individual needs of its customers to achieve the best protection for its customers’ goods, Eisenhuber said.
President Director of Coca-Cola Amatil Indonesia, Kadir Gunduz, said the two companies have established a joint project team to leverage each company’s expertise in respective parts of the production and recycling process. “This joint venture represents a real environmental step-change in our move toward a more sustainable approach to plastic and a circular economy by bringing low-quality PET waste back to virgin-quality, food-grade PET, which also echoes the Coca-Cola Company’s ‘World Without Waste’ vision,” said Gunduz.
“It is a significant step toward Amatil becoming self-sustaining in the plastic materials we use, ensuring a closed loop for plastic beverage packaging in Indonesia as a whole,” he added.
Coca-Cola Amatil Indonesia (Amatil) has entered into a Heads of Agreement with long-term packaging partner Dynapack Asia to build what it calls the most sophisticated state-of-the-art bottle-to-bottle grade PET recycling facility in Indonesia.
IML typically is used in combination with injection molding technology. The thermoformed IML cups are more sustainable by several measures, according to Philipp Maurer, Key Account Manager at Greiner Packaging. Less plastic is required to produce thermoformed cups, which saves resources and makes the cups lighter and less costly to transfer. This requires fewer carbon dioxide emissions during transport.
In addition, the cup and label are made of polypropylene (PP), a mono-material construction that is very easy to recycle. Mono-material solutions also are possible with PET, Eisenhuber told PlasticsToday.
The use of recycled plastic could reduce the amount of new plastic resin the company uses by an estimated 25,000 tonnes each year by 2022. This aligns with a commitment through the National Plastic Action Partnership to support Indonesia’s National Action Plan in achieving a 70% reduction in the nation’s marine plastic debris by 2025.
During in-mold labeling, a label is inserted into the thermoforming mold that shapes the product and forms a solid bond with the finished product. Shaping and decoration are performed in a single, efficient process.
When possible, Greinier Packaging tries to use recycled material, although the use of mechanically recycled material for food applications is limited because of strict approval criteria. Currently, only rPET meets those requirements.
T- IML is an especially high-quality form of packaging decoration, the company said. Matte, rough, glossy, or soft-touch decorative effects can be applied, and the printed content is photo quality and “visually outstanding,” Maurer said. “IML packaging solutions are extremely effective at attracting consumers’ attention at the point of sale.
Dynapack Asia operates over 30 manufacturing sites across Southeast Asia and China and intends to collaborate with its customers to increase the use of recycled materials and products, strengthening the region’s recycling ecosystem and achieving a circular economy. The company specializes in extrusion blow molding and injection molding for the manufacture of bottles, jars, caps and closures as well as precision molded parts for the personal and baby care, food and beverage, home cleaning, lubricant, pharmaceuticals, automotive and other industries.
Greiner Packaging’s thermoformed cups with in-mold labels (IML) use less material, are lighter in weight, and easier to recycle than their injection molded counterparts.
Amatil and Dynapack will work together through a proof of concept phase, which is intended to consider a potential plant’s economic feasibility, size, scale, and location; end-to-end requirements; and potential integration into each company’s value chains.
Until she retired in September 2021, Clare Goldsberry reported on the plastics industry for more than 30 years. In addition to the 10,000+ articles she has written, by her own estimation, she is the author of several books, including The Business of Injection Molding: How to succeed as a custom molder and Purchasing Injection Molds: A buyers guide. Goldsberry is a member of the Plastics Pioneers Association. She reflected on her long career in "Time to Say Good-Bye."
“At Greiner Packaging, we are committed to a circular economy and want to take a broad-based approach to making that happen,” Maurer added. “With our new T-IML cups using less material and being readily recyclable, they encapsulate exactly what we hoped to achieve.”
In addition, the sheet used in the thermoforming process to make the cup can be embedded with barrier properties, which can extend the shelf life of packaged food and help reduce food waste, according to Sebastian Eisenhuber, Global Product Group Manager.
GETTING A QUOTE WITH LK-MOULD IS FREE AND SIMPLE.
FIND MORE OF OUR SERVICES:
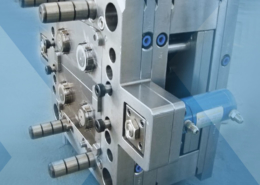
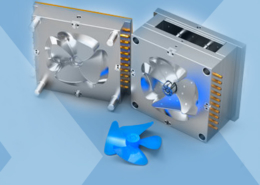
Plastic Molding

Rapid Prototyping
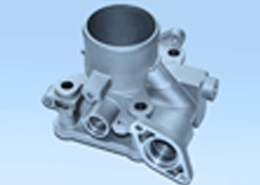
Pressure Die Casting
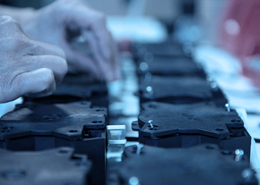
Parts Assembly
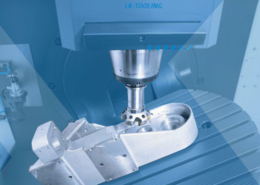