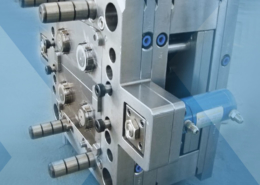
Virtual injection molding part II: Benefits of mold-analysis software for
Author:gly Date: 2024-09-30
As Euroform almost exclusively manufactures one-offs, pallet handling such as the PH Cell 2000 is the optimal solution. Operators set up jobs offline on several pallets using a zero-point clamping system while machining is in progress on another mould, so production downtime is minimal, even at night.
The modified rPET being processed at the K show comes from drinks bottles recycled in the plants of packaging and recycling specialists ALPLA Group, who are headquartered in Hard, Austria. The other collaborators involved with the project will also be at K 2022. This includes Brink (Harskamp, Netherlands) for the mould and IML automation and IPB Printing (Reusel, Netherlands) for the labels.
Euroform has been using machine tools from DMG MORI since 1995, latterly in a modern factory that it moved into in 2011 and expanded in 2016. Managing Director responsible for day-to-day business at Euroform, Krisztina Zwick, mentioned the supplier's broad machine portfolio and good service: "DMG MORI was one of the first machine tool manufacturers to open a subsidiary in Hungary, which meant that response times were always quick when service was required. Our latest investment in automation was necessary to utilise the machine during unattended shifts, giving us a competitive edge.”
When Euroform ordered the new DMU 100 P duoBLOCK, DMG MORI already had a large pallet handling system in development, based on the smaller, proven, modular PH Cell 300. The bigger capacity automation system handles pallets measuring up to 1,100 mm in diameter, so is able to deploy Euroform's 1,000 × 800 mm pallets. The PH Cell 2000 has twelve pallet positions on two levels and can accept workpieces up to 1,350 mm tall. (Other variants are available with three or four racks housing up to 17 or 21 pallets respectively.)
Another focus that accompanies business development at Euroform is digitalisation. The company has had a paperless working environment for many years, from design through to quality control. The mould maker is an enthusiastic adopter of the digital 'my DMG MORI' app when it comes to online service requests, which Zwick said significantly accelerates the process of calling in a service technician.
"The recent Corona pandemic, the war in Ukraine and high inflation have clearly shown us that we need to develop constantly in order to remain competitive.
Five-axis simultaneous machining of workpieces up to 1,100 mm in diameter by 1,600 mm and weighing 2,200 kg had already been carried out on a DMU 100 P duoBLOCK in the factory. Euroform's experience with the machining centre was consistently good, leading to the purchase in 2022 of a latest-generation model with a 1,000 × 1,250 × 1,000 mm working envelope.
The DMU 100 P duoBLOCK 5-axis machining centre with PH Cell 2000 pallet storage and handling system on the shop floor at Euroform, Budapest.
ENGEL will present solutions including a mould that can process different labels at the same time at K 2022 in Dusseldorf, running from the 19th to the 26th of October.
The companies say that up until now, it has only been possible to process PET in thick-walled parts such as bottle preforms in injection moulding. The final packaging format was apparently created in a second step of the process, for example, by blow moulding.
ENGEL, ALPLA Group, Brink and IPB Printing have collaborated to produce thin-walled containers made of PET and rPET in a single injection moulding process step.
Stefan Wolf, Euroform's managing partner said: "We play a pivotal role in automotive supply chains and our work begins in the early development phase of a new vehicle. Technical competence is crucial for exploiting the potential of innovative manufacturing solutions and CADCAM systems."
Wolf concluded: "Automated manufacturing and digital processes are essential, given the current challenges in the global marketplace.
PET offers the benefit of having a closed-loop recycling system already in place, the companies claim. They add that the innovation could remove the need to downcycle packaging into products other than bottles and provides an opportunity for bottle-to-bottle, bottle-to-cup, or even cup-to-bottle recycling.
The dyes used on in-mould labels for the American market can apparently be washed off before recycling, while ENGEL says that for the European market, the in-mould label floats off in the recycling process to allow for the dyes and the label to be separated from the PET.
ENGEL says that it specifically developed the e-speed 280/50 injection moulding machine with its electrical clamping unit and hydraulic injection unit for the high-performance requirements of thin-wall injection moulding. The new injection unit allegedly achieves injection speeds of up to 1400 mm per second at a maximum injection pressure of up to 2600 bar when processing small shot weights with an extreme wall-thickness to flow path ratio
According to the companies, an ENGEL e-speed injection moulding machine with a newly-developed and extremely powerful injection unit is being used to produce the thin-walled containers produced from recycled PET in a single step.
To process rPET, ENGEL adds that it combines the new injection unit with a plasticising unit from in-house development and production specifically designed for processing recycled material. During the plasticising and injection, the viscosity of the PET is configured for thin-wall injection moulding.
The companies add that the transparent, round containers feature a wall thickness of 0.32 and a volume of 125 ml. The containers are reportedly ready-for-filling as soon as they leave the production cell thanks to integrated in-mould labelling (IML).
Based in the Hungarian capital Budapest, Euroform was established in 1993 to provide a tool and mould making service from design to production and trialling. Approximately 70 employees fulfil innovative solutions for a range of different injection moulding processes, mainly for customers in the automotive industry.
"With targeted investment in technology and the training and further education of junior staff, we will continue to successfully meet these challenges.”
The firm currently uses eight machining centres from DMG MORI for tool production, including DMU monoBLOCKs, an HSC 75 linear and, most recently, a DMU 100 P duoBLOCK with PH Cell 2000 automation system for pallet handling to allow unattended production at night and during the weekends.
GETTING A QUOTE WITH LK-MOULD IS FREE AND SIMPLE.
FIND MORE OF OUR SERVICES:
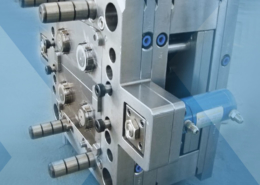
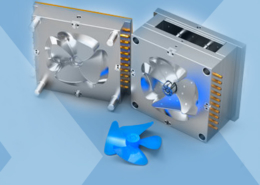
Plastic Molding

Rapid Prototyping
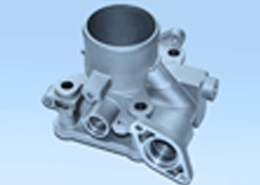
Pressure Die Casting
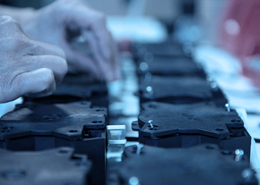
Parts Assembly
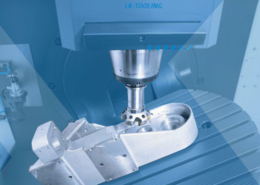