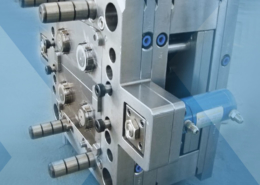
Virtual injection molding part II: Benefits of mold-analysis software for
Author:gly Date: 2024-09-30
The construction sector has witnessed an upward trend over recent years owing to the escalating rollouts of infrastructure development projects and the advent of several technological breakthroughs. Besides, the improving economic landscape and the significant rise in investments focused on building an energy-efficient infrastructure across numerous economies.
A stringent regulatory environment for medical-grade polymer use in healthcare industries is expected to fuel the injection molded plastics market growth. Over the forecast period, a growing preference for biodegradable polymers among medical device makers is expected to generate profitable opportunities in the medical industry. A significant shift in the automotive industry's trend towards replacing steel with plastics is anticipated to fuel product demand over the forecast period. In recent years, government rules have compelled automakers to use plastics instead of other materials such as iron and steel. Automobile makers have been concentrating on reducing vehicle weight in order to increase fuel efficiency.
Gerresheimer Medical Plastic Systems has installed a small-scale pilot production unit at its Technical Competence Centre in Wackersdorf, Germany.
Injection Molded Plastics Market size garnered over USD 300 billion in 2022. With the consistent expansion of the construction sector globally, the industry is set to witness 3.5% CAGR from 2023 to 2032.
In the initial phase, the production area will be 420m2 in size, with plans to expand this to 1,400m2 in 2016. It will include a 400m2 ISO Class 8 cleanroom to the DIN EN ISO 14644 standard, while integrated laminar flow hoods create an ISO Class 7 cleanroom environment in the injection moulding area. A gantry crane inside the cleanroom allows for fast and easy mould changes, the company says.
With respect to raw material, the injection molded plastics market is segregated into Acrylonitrile Butadiene Styrene (ABS), polypropylene (PP), High-Density Polyethylene (HDPE), Polystyrene (PS), and others. The Polypropylene segment is expected to expand at over 4% CAGR and exceed USD 160 billion by 2032. Because of the growing consumption of PP in automotive components, packaging applications, and household goods, the polypropylene (PP) segment held the biggest revenue share of more than 34% in 2021. Increasing PP-based product penetration in protective caps for electrical contacts and battery housings, as well as food packaging, is expected to fuel demand over the projection period.
The Injection molded plastics market research report includes in-depth coverage of the industry with estimates & forecasts in terms of volume in kilo tons & in terms of revenue in USD billion from 2018 to 2032 for the following segments: Click here to Buy Section of this Report
The control of the entire production process, including order management, production planning and scheduling, mould service, injection moulding/assembly, quality management and freight management, complies with the standards of large-scale production processes.
Regarding the application landscape, the packaging applications are expected to amass more than USD 135 billion by 2032, exhibiting a 3.5% growth rate throughout the projection period. To meet regulatory guidelines and end-user criteria, finished goods used in packaging go through several development stages. Plastics must satisfy several requirements for packaging applications, including improving food product shelf life, improved wear and tear resistance, and high durability. Plastic injection molding has enormous promise. Particularly in the medicinal and automotive fields. The medical devices and components sector is anticipated to grow the most in the industry. Product demand in the medical industry is anticipated to be driven by biocompatibility, optical clarity, and cost-effective manufacturing methods.
Asia Pacific injection molded plastics market is projected to be worth over USD 140 billion by 2032. The regional growth can be credited to the flourishing automotive and construction sectors owing to the increasing demand and uptake of autonomous high-end luxury vehicles and the rising infrastructural investments. In addition, the robust economic outlook across countries such as China and India, coupled with the rapid industrial growth, will create positive growth prospects for the injection molded plastics industry in the Asia Pacific.
Looking for more? Our expert team of researchers can create market analysis reports for any of your needs.
A Management Execution System (MES) guarantees efficient, fast and cost-efficient production processes. Automated quality checks are integrated into the process, while an end-to-end tracking system for individual subassemblies or batches ensures that all products comply with the required quality standards for pharmaceutical and medical technology products.
Players in the market have been widely integrating advanced technologies to develop state-of-the-art products to gain a competitive edge over their counterparts and expand their existing consumer base. For instance, in July 2022, Sabic introduced a specially personalized portfolio of new mineral-reinforced Sabic PP compounds, PPc F9015, PPc F9005, and PPc F9005 grades for foam injection molding (FIM). The newly introduced product range help provide stunning aesthetics for visible automotive interior parts with complicated geometries, such as seat and trunk cladding, door panels and trim, center consoles, and A/B/C/D pillar covers.
The pilot plant delivers laboratory prototypes, clinical test samples and small-scale production batches at any project stage. Potential weak points can be spotted at an early stage, optimised during the active project, and the acquired insights applied to large-scale production. Similarly, all intelligence gathered during the mould engineering and automation processes can be applied directly to the construction of moulds and technical equipment for large-scale production. The development and project teams supervise the entire product creation process right through to series production.
Because of their corrosion resistance and electrical insulation qualities, polypropylene components are widely used in food packaging and electrical contacts. Due to the aforementioned factors, the segment is anticipated to grow at the fastest rate during the forecast period. However, a reduction or cessation of manufacturing activities to fight the spread of the coronavirus has resulted in a decline in PP consumption and a negative impact on its demand in a variety of applications. Manufacturers are having difficulty operating their production units due to logistical constraints and limits on people's movement, which has impacted product demand.
Plastic injection molding is widely utilized across several industrial verticals ranging from electronics, automobiles, and construction to kitchen utensils and toys. The stringent government regulation pertaining to minimizing plastic pollution and the increased adoption of effective waste management techniques may restrict industry growth during the forecast period. On the other hand, the consolidated competitive landscape and the increasing strategic exchanges among leading product manufacturers will accelerate business growth through the ensuing years.
Even at this early pre-production stage, the pilot production unit complies with large-scale quality standards so that the acquired production intelligence can be applied directly to large-scale production processes at any Gerresheimer facility, the company says.
The pilot plant has been equipped 11 injection moulding machines with clamping forces of between 65t and 420t, two of which are equipped for two-component injection moulding with clamping forces of 120t and 200t, respectively. It also features project-specific assembly units such as joining machines, bonding units or ultrasound welding systems.
Home > Chemicals & Materials > Polymers > Industrial Polymers > Injection Molded Plastics Market
These trends, in covalence with the adoption of distinctive growth initiatives by premier product manufacturers and rising investments across the construction sector, will boost the industry revenue trajectory over the next ten years.
The injection molded plastics industry depicted a decent growth potential during the COVID-19 pandemic, owing to a remarkable rise in demand for gloves, masks, personal protective equipment, and associated packaging materials. Based on investigations by Frontline, plastic resin production in the U.S. increased by 0.9% compared to COVID-19 restrictions and industry closures. Besides, the strict movement restrictions and social distancing norms resulted in a transformer buyer behavior and caused a massive boom across the e-commerce industry, further pushing the demand for packaging boxes and containers.
Cleanroom Technology keeps decision-makers worldwide updated on contamination control via digital, live, and print platforms. Our articles span the cleanroom lifecycle, from design to maintenance, including monitoring and compliance. Editors deliver breaking news, product launches, and innovations, and also commission exclusives on technical trends from industry experts
Global Market Insights Inc. 4 North Main Street, Selbyville, Delaware 19975 USA Toll Free: +1-888-689-0688 USA: +1-302-846-7766 Europe: +44-742-759-8484 APAC: +65-3129-7718 Email: sales@gminsights.com
GETTING A QUOTE WITH LK-MOULD IS FREE AND SIMPLE.
FIND MORE OF OUR SERVICES:
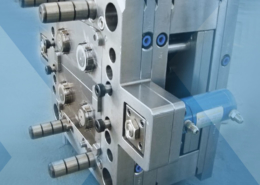
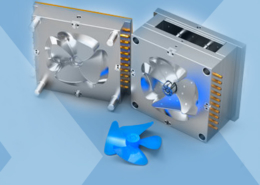
Plastic Molding

Rapid Prototyping
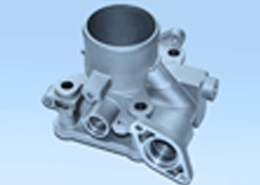
Pressure Die Casting
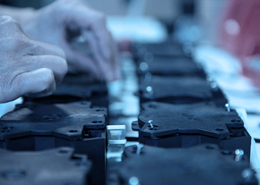
Parts Assembly
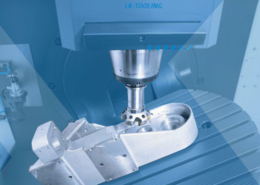