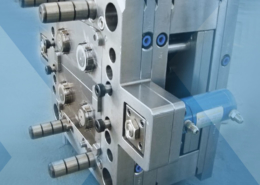
Exploring the World of Thin Wall Moulding
Author:gly Date: 2024-06-08
Thin wall moulding, a fascinating aspect of modern manufacturing, stands at the intersection of innovation and precision. Its importance lies in its ability to produce intricate and lightweight products efficiently. This article delves into the intricacies of thin wall moulding, exploring its techniques, applications, challenges, and future prospects.
Technological Advancements
Thin wall moulding has witnessed significant technological advancements in recent years. Injection moulding processes have evolved to accommodate thinner walls while maintaining structural integrity. The development of high-performance materials and additives has further expanded the possibilities in thin wall moulding. These advancements have revolutionized industries ranging from automotive to electronics, enabling the production of lighter, more durable components.
Material Selection
The choice of materials plays a crucial role in thin wall moulding. Polymers such as ABS, PC, and PP are commonly used for their lightweight properties and ease of mouldability. However, the demand for environmentally sustainable solutions has led to the exploration of biodegradable and recycled materials for thin wall applications. Material selection criteria include mechanical properties, thermal stability, and compatibility with the moulding process.
Challenges and Solutions
Despite its numerous advantages, thin wall moulding presents several challenges. Achieving uniform wall thickness, minimizing warpage, and preventing sink marks are among the key challenges faced by manufacturers. Advanced mould design, precise control of processing parameters, and the use of innovative cooling techniques are some of the solutions employed to address these challenges. Additionally, simulation tools have become invaluable for predicting and optimizing the moulding process.
Applications Across Industries
The versatility of thin wall moulding has led to its widespread adoption across various industries. In the automotive sector, it is used for manufacturing lightweight interior components, such as dashboard panels and door trims. In the consumer electronics industry, thin wall moulding enables the production of sleek and compact casings for electronic devices. Furthermore, in the packaging industry, it facilitates the creation of thin-walled containers that are both sturdy and cost-effective.
Future Directions
Looking ahead, the future of thin wall moulding holds promise for further innovation and refinement. Research efforts are focused on developing advanced materials with enhanced properties, as well as exploring novel moulding techniques to push the boundaries of what is achievable. The integration of digital technologies, such as artificial intelligence and machine learning, is expected to optimize the moulding process and improve product quality. Moreover, there is a growing emphasis on sustainability, driving the development of eco-friendly materials and recycling solutions in thin wall moulding.
In conclusion, thin wall moulding represents a pivotal advancement in manufacturing technology, enabling the production of lightweight and intricately designed components across various industries. While it poses challenges, technological advancements and innovative solutions continue to propel its evolution. As we look to the future, thin wall moulding will undoubtedly remain at the forefront of manufacturing innovation, shaping the way we design and produce products for years to come.
GETTING A QUOTE WITH LK-MOULD IS FREE AND SIMPLE.
FIND MORE OF OUR SERVICES:
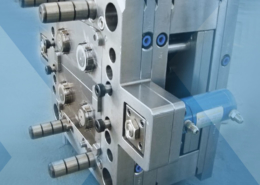
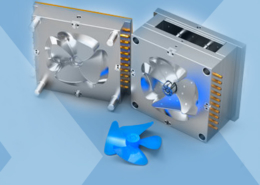
Plastic Molding

Rapid Prototyping
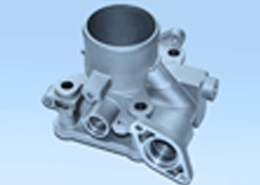
Pressure Die Casting
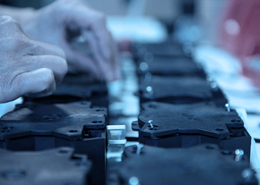
Parts Assembly
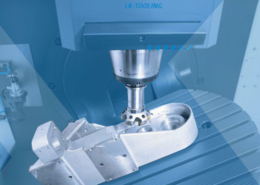