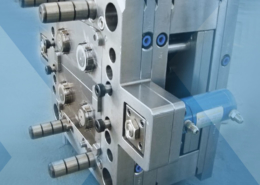
Exploring the Dynamics of Thermoplastic Molding
Author:gly Date: 2024-06-08
Introduction
Thermoplastic molding stands as an integral process in modern manufacturing, revolutionizing the production of various components across industries. By heating polymer resins to their melting point, molding enables the creation of complex shapes with precision and efficiency. This article delves into the intricacies of thermoplastic molding, exploring its mechanisms, applications, and future prospects.
Understanding Thermoplastic Molding
Thermoplastic molding involves the manipulation of polymers under controlled temperatures and pressures to achieve desired shapes. This process begins with the selection of suitable thermoplastic materials, which exhibit characteristics such as high moldability, strength, and chemical resistance. Subsequently, the chosen resin undergoes heating within a molding machine until it reaches a viscous state, allowing it to be injected or extruded into molds with precision.
Key Aspects of Thermoplastic Molding
Material Selection
The success of thermoplastic molding heavily relies on the careful selection of materials. Engineers consider factors such as the intended application, mechanical properties, and environmental conditions to choose the most appropriate resin. Common thermoplastics utilized in molding include polyethylene, polypropylene, polycarbonate, and acrylonitrile butadiene styrene (ABS), each offering unique advantages and limitations.
Processing Techniques
Thermoplastic molding encompasses various processing techniques tailored to specific applications. Injection molding, for instance, entails the injection of molten plastic into a mold cavity under high pressure, ideal for mass production of intricate components. Conversely, extrusion molding involves forcing heated plastic through a die to create continuous profiles, sheets, or films, suited for manufacturing pipes, tubes, and packaging materials.
Mold Design and Fabrication
The design and fabrication of molds play a pivotal role in thermoplastic molding. Engineers utilize advanced CAD software to design molds with precise dimensions and features, considering factors such as shrinkage, cooling rates, and part ejection mechanisms. Subsequently, molds undergo fabrication using techniques like CNC machining or additive manufacturing, ensuring accuracy and repeatability in the production process.
Applications and Impact
Automotive Industry
The automotive sector extensively relies on thermoplastic molding for the production of interior and exterior components. From dashboard panels to bumper fascias, thermoplastics offer lightweight, durable solutions that contribute to fuel efficiency and vehicle safety. Additionally, the ability to incorporate design flexibility enables automakers to meet aesthetic preferences and regulatory standards effectively.
Consumer Electronics
In the realm of consumer electronics, thermoplastic molding facilitates the manufacturing of sleek and compact devices. Enclosures for smartphones, laptops, and home appliances are commonly produced using injection molding, leveraging the inherent properties of thermoplastics such as electrical insulation, impact resistance, and thermal stability. Furthermore, rapid prototyping techniques empower designers to iterate quickly and bring innovative products to market faster.
Medical Devices
Thermoplastic molding plays a critical role in the medical device industry, where precision and biocompatibility are paramount. Components such as syringes, catheters, and surgical instruments benefit from the versatility of thermoplastics, which allow for sterilization, transparency, and dimensional accuracy. Moreover, the ability to manufacture custom implants and prosthetics tailored to individual patients underscores the transformative potential of thermoplastic molding in healthcare.
Challenges and Future Directions
Environmental Sustainability
While thermoplastic molding offers numerous advantages, concerns regarding its environmental impact persist. The reliance on fossil fuel-derived polymers and the generation of plastic waste pose significant challenges to sustainability. Future research endeavors aim to explore alternative biodegradable materials, recycling techniques, and closed-loop systems to mitigate the ecological footprint of thermoplastic molding processes.
Advanced Materials and Technologies
The evolution of thermoplastic materials and manufacturing technologies continues to drive innovation in the field. From carbon fiber-reinforced composites to 3D printing, advancements enable enhanced performance, reduced cycle times, and cost-effective production. Embracing emerging trends such as digital twin technology and machine learning holds the promise of optimizing process parameters and enhancing product quality in thermoplastic molding.
Conclusion
In conclusion, thermoplastic molding stands as a cornerstone of modern manufacturing, offering versatility, efficiency, and precision in the production of diverse components. By understanding the key aspects, applications, and challenges associated with thermoplastic molding, stakeholders can harness its potential to drive innovation across industries. Embracing sustainable practices and technological advancements will be pivotal in shaping the future landscape of thermoplastic molding and ensuring its continued relevance in the global manufacturing ecosystem.
GETTING A QUOTE WITH LK-MOULD IS FREE AND SIMPLE.
FIND MORE OF OUR SERVICES:
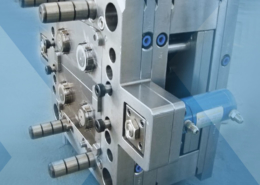
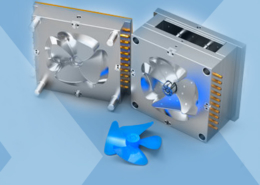
Plastic Molding

Rapid Prototyping
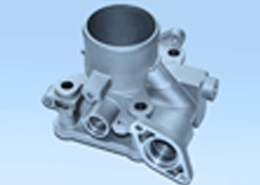
Pressure Die Casting
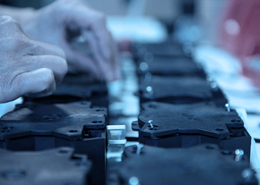
Parts Assembly
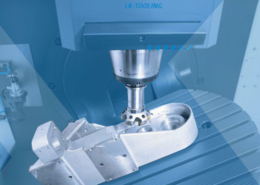