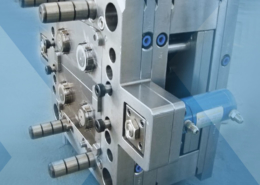
Two-Shot Molding: The Advantages, Considerations and Real-World Applications - i
Author:gly Date: 2024-09-30
In this collection of articles, two of the industry’s foremost authorities on screw design — Jim Frankand and Mark Spalding — offer their sage advice on screw design...what works, what doesn’t, and what to look for when things start going wrong.
Say “manufacturing automation” and thoughts immediately go to the shop floor and specialized production equipment, robotics and material handling systems. But there is another realm of possible automation — the front office.
PLA looks and performs similiarly to the polyethlene used in plastic films, packing materials and bottles, and it can also be used as a substitute for the polystyrene used in foam food plates and containers and plastic cutlery. But unlike conventional petroleum-based plastics, PLA has some big advantages. For one, since it's made from plants that absorb carbon dioxide as they grow, there's no net increase in carbon dioxide from its raw materials. A 2017 study found that switching from conventional plastic to PLA would cut U.S. greenhouse gas emissions by 25 percent [source: Cho].
Second quarter started with price hikes in PE and the four volume engineering resins, but relatively stable pricing was largely expected by the quarter’s end.
While some people are busy developing plastic substitutes, others are bent on making conventional thermoplastics biodegradable. How? By throwing in additives called prodegradant concentrates (PDCs). PDCs are usually metal compounds, such as cobalt stearate or manganese stearate. They promote oxidation processes that break the plastic down into brittle, low-molecular-weight fragments. Microorganisms gobble up the fragments as they disintegrate, turning them into carbon dioxide, water and biomass, which reportedly contains no harmful residues.
Gifted with extraordinary technical know how and an authoritative yet plain English writing style, in this collection of articles Fattori offers his insights on a variety of molding-related topics that are bound to make your days on the production floor go a little bit better.
Across all process types, sustainability was a big theme at NPE2024. But there was plenty to see in automation and artificial intelligence as well.
•Do a preliminary test. To get a good idea of how well your substrate material will bond to a particular LSR grade, it’s a good idea to send a representative part or sample plaque of the substrate material to the LSR supplier for testing.
Back in 1907, Leo Baekeland invented a new material, Bakelite, that was the first true synthetic plastic, composed of molecules not found in the natural world. It was an amazing breakthrough. Bakelite was durable and heat resistant and could be molded into almost any shape. People called it "the material of a thousand uses" [source: Science History Institute].
When single-use plastic bags first hit the scene, we had a choice: paper or plastic. Today, it's pretty much all plastic. And if you're not that hypervigilant person at the checkout, you'll find yourself walking home with a bag for each item.
The KE2090 Select-Hesive LIMS silicone comes in 10 to 70 Shore A hardness. It bonds to PC, PBT, PPO alloys, PEEK, and polyphenylsulfone, according to Shin-Etsu’s Eric Bishop.
Mixed in among thought leaders from leading suppliers to injection molders and mold makers at the 2023 Molding and MoldMaking conferences will be molders and toolmakers themselves.
Take polycaprolactone (PCL), a synthetic aliphatic polyester that isn't made from renewable resources but does completely degrade after six weeks of composting. It's easily processed but hasn't been used in significant quantities because of manufacturing costs. However, blending PCL with cornstarch reduces cost.
When, how, what and why to automate — leading robotics suppliers and forward-thinking moldmakers will share their insights on automating manufacturing at collocated event.
Once upon a time, both moms and milkmen filled glass bottles with milk. Now look around your kitchen and you'll probably see many plastics — water bottles, soda bottles, food storage containers. Times have changed.
Producing plastic from processed corn may seem like a pipe dream, but it's happening every day. Polylactic acid, or PLA, is another aliphatic polyester and one that can be made from lactic acid, which is produced via starch fermentation during corn wet milling. Although most often generated from corn, PLA can be made from wheat or sugarcane as well.
Next up is a promising bioplastic, or biopolymer, called liquid wood. Biopolymers fake it; these materials look, feel and act just like plastic but, unlike petroleum-based plastic, they're biodegradable. This particular biopolymer comes from pulp-based lignin, a renewable resource.
Production costs have mostly put PHA in the shadow of cheaper, petroleum-based plastics, but a little creativeness in sourcing inexpensive raw materials may make it a top choice soon. Corn-steeped liquor, molasses and even activated sludge could all supply the sugar the bacteria need to produce the plastic.
That turned out to be an understatement. Today, plastics are one of the cornerstones of modern technological civilization — tough, flexible durable, impervious to corrosion, and seemingly endlessly versatile. However, there are downsides to its prevalence. That's why plastic alternatives are worth finding.
Glass bottles and jars potentially are 100 percent recyclable, and the glass in them can be reused endlessly, without any loss in quality and purity. Glass manufacturers welcome recycled glass, because when it's used as an ingredient in making new glass, it requires less energy in furnaces. Container manufacturers and the fiberglass industry (which also uses recycled glass) together purchase 3.35 million tons (3.03 million metric tons) of recycled glass annually [source: Glass Packaging Institute].
All newborn mammals survive on it. Without it, there would be no ice cream. There's really no denying the value — or pleasure — of milk.
In fact, it's tough to make a purchase without it promptly being thrown into plastic. No wonder plastic bags seem omnipresent. The U.S. produced an astonishing 4.13 million tons (3.75 million metric tons) of plastic bags in 2015 and only 530,000 tons (481,000 metric tons) of those were recycled [source: EPA]. The rest end up as litter in cities and towns — and too many find their way to the ocean, where they kill millions of sea turtles, birds and ocean mammals each year. But you have to lug those groceries home somehow. So what do you do? Reusable grocery bags, for starters.
The Plastics Industry Association (PLASTICS) has released final figures for NPE2024: The Plastics Show (May 6-10; Orlando) that officially make it the largest ever NPE in several key metrics.
Join this webinar to explore the transformative benefits of retrofitting your existing injection molding machines (IMMs). Engel will guide you through upgrading your equipment to enhance monitoring, control and adaptability — all while integrating digital technologies. You'll learn about the latest trends in IMM retrofitting (including Euromap interfaces and plasticizing retrofits) and discover how to future-proof your machines for a competitive edge. With insights from industry experts, it'll walk you through the decision-making process, ensuring you make informed choices that drive your business forward. Agenda: Maximize the value of your current IMMs through strategic retrofitting Learn how to integrate digital technologies to enhance monitoring and control Explore the benefits of Euromap interfaces and plasticizing retrofits Understand how retrofitting can help meet new product demands and improve adaptability Discover how Engel can support your retrofitting needs, from free consultations to execution
But an Italian company, Vegea, is using the grape waste to make a synthetic leather that could replace vinyl imitation leather, and also into fabric for clothing. Vegea is now in the process of scaling up its production capacity to manufacture the grape-waste apparel items for sale to clothing stores, so you can add grape waste to your wardrobe [source: Stella McCartney].
Hard/soft overmolding has become a fundamental technique for injection molders in recent years, and a growing number of molders are extending that technology thermoset/thermoplastic combinations.
Thousands of people visit our Supplier Guide every day to source equipment and materials. Get in front of them with a free company profile.
Plastics Technology’s Tech Days is back! Every Tuesday in October, a series of five online presentations will be given by industry supplier around the following topics: Injection Molding — New Technologies, Efficiencies Film Extrusion — New Technologies, Efficiencies Upstream/Downstream Operations Injection Molding — Sustainability Extrusion — Compounding Coming out of NPE2024, PT identified a variety of topics, technologies and trends that are driving and shaping the evolution of plastic products manufacturing — from recycling/recyclability and energy optimization to AI-based process control and automation implementation. PT Tech Days is designed to provide a robust, curated, accessible platform through which plastics professionals can explore these trends, have direct access to subject-matter experts and develop strategies for applying solutions in their operations.
Casein-based plastic has been around since the 1880s, when a French chemist treated casein with formaldehyde to produce a material that could substitute for ivory or tortoiseshell. But although it's ideal for jewelry that even Queen Mary admired, casein-based plastic is too brittle for much more than adornment.
The future of casein plastic isn't certain, but swapping it for petroleum-based polystyrene would certainly give us another reason to love milk.
•Watch out for additives, mold releases. Bishop advises against usin thermoplastic substrates with internal mold releases or “self-lubricating” additives, though they do not always create an adhesion problem. External mold releases are a definite no-no. And avoid any additives containing sulfur or amines, which inhibit cure of LSR. That means amine-based antistats can be a problem.
•Consistency counts. If you follow all the advice above, you should get good results with self-adhesive LSR regardless of whether you use two-shot molding in one machine or separate molding in two machines. But with two machines, it definitely helps to use automated (robotic) transfer from one to the other, Bishop says. That way ensures a consistent substrate temperature for overmolding and also avoids any contamination from a human operator handling parts.
NPE2024: Absolute Haitian says Generation 5 of the servo-hydraulic Haitian and electric Zhafir machines lines emphasize efficiency, performance and intelligence.
In a time where sustainability is no longer just a buzzword, the food and beverage packaging industry is required to be at the forefront of this innovation. By adopting circular packaging processes and solutions, producers can meet regulatory requirements while also satisfying consumer demand and enhancing brand reputation. Join Husky to learn more about the broader implications of the circular economy — as well as how leading brands are leveraging this opportunity to reduce costs, increase design flexibility and boost product differentiation. Agenda: The cost and operational benefits of embracing circularity Key materials in circular packaging — including rPET and emerging bioplastics How to design a circular food and beverage package Strategies for selecting sustainable closures to future-proof packaging solutions Optimization and streamlining of production processes for enhanced efficiency How Husky Technologies can enable your sustainable success
Mike Sepe has authored more than 25 ANTEC papers and more than 250 articles illustrating the importance of this interdisciplanary approach. In this collection, we present some of his best work during the years he has been contributing for Plastics Technology Magazine.
But we could do a lot better job of recycling glass. In 2015, the most recent year for which the U.S. Environmental Protection Association (EPA) has statistics, Americans only recycled 26.4 percent of the glass containers that they used.
When added to polyethylene (the standard plastic bag material) at levels of 3 percent, PDCs can promote nearly complete degradation; 95 percent of the plastic is in bacteria-friendly fragments within four weeks [source: Nolan-ITU Pty]. While not strictly biodegradable ('bioerodable' is more like it), PDC-containing polymers are more environmentally friendly than their purer polymer cousins, which sit in landfills for hundreds of years.
After successfully introducing a combined conference for moldmakers and injection molders in 2022, Plastics Technology and MoldMaking Technology are once again joining forces for a tooling/molding two-for-one.
What one of the hottest trends in biodegradable plastic development can do is make polymer composites more biodegradable. You name it, and starch has probably been combined with it, albeit with varying degrees of success.
Join Engel in exploring the future of battery molding technology. Discover advancements in thermoplastic composites for battery housings, innovative automation solutions and the latest in large-tonnage equipment designed for e-mobility — all with a focus on cost-efficient solutions. Agenda: Learn about cutting-edge thermoplastic composites for durable, sustainable and cost-efficient battery housings Explore advanced automation concepts for efficient and scalable production See the latest large-tonnage equipment and technology innovations for e-mobility solutions
The aim of this presentation is to guide you through the factors and the numbers that will help you determine if a robot is a smart investment for your application. Agenda: Why are you considering automation? What problems are you trying to solve? How and why automation can help Crunch the numbers and determine the ROI
As a totally biodegradable, low-cost, renewable and natural polymer, starch has been receiving lots of attention for developing sustainable materials. When it comes to replacing plastic, however, starch can't cut the mustard; its poor mechanical properties mean it has limited use for the sturdy products that plastics generate.
Sustainability continues to dominate new additives technology, but upping performance is also evident. Most of the new additives have been targeted to commodity resins and particularly polyolefins.
The next three entries on this list are all biodegradable plastics called aliphatic polyesters. Overall, they aren't as versatile as aromatic polyesters such as polyethylene terephthalate (PET), which is commonly used to make water bottles. But since aromatic polyesters are completely resistant to microbial breakdown, a lot of time and effort is being pumped into finding viable alternatives in aliphatic polyesters.
Plastics Technology covers technical and business Information for Plastics Processors in Injection Molding, Extrusion, Blow Molding, Plastic Additives, Compounding, Plastic Materials, and Resin Pricing. About Us
While prices moved up for three of the five commodity resins, there was potential for a flat trajectory for the rest of the third quarter.
•Serve it up hot. “It is vital for substrate parts to be hot,” Bishop states. “The bonding of LSR to the thermoplastic is a chemical reaction. It needs a combination of time, temperature, and pressure. In general, he says, hotter is better. Typical mold temperatures for LSR are 300 to 400 F and the minimum is 250 F. The LSR has to achieve at least that internal temperature to cure adequately. Hotter is also faster—meaning shorter cure cycles.
In this collection, which is part one of a series representing some of John’s finest work, we present you with five articles that we think you will refer to time and again as you look to solve problems, cut cycle times and improve the quality of the parts you mold.
Ultradent's entry of its Umbrella cheek retractor took home the awards for Technical Sophistication and Achievement in Economics and Efficiency at PTXPO.
This Knowledge Center provides an overview of the considerations needed to understand the purchase, operation, and maintenance of a process cooling system.
•Mechanical interlock helps. Even with self-bonding LSR, it’s good insurance to incorporate some form of mechanical interlock between the materials into the part design. Allowing LSR to penetrate through-holes onto the back side of the part is a good example. A rough finish on the overmolding interface area can help, but isn’t required with a good self-bonding material.
Preparing the substrate surface with chemical primers or plasma or UV treatment has been one approach to the adhesion challenge. To minimize processing steps, LSR suppliers have come out with newer “primerless” or “self-adhesive” grades that bond well on their own with thermoplastics (see accompanying case history). Even so, there are some rules to observe in order to obtain good results. Here are some key points of advice offered by Eric Bishop, North American marketing manager for Shin-Etsu Silicones of America, Inc. in Akron, Ohio (shinetsusilicones.com). Shin-Etsu supplies Select-Hesive LIMS for primerless adhesion to thermoplastics.
A collaboration between show organizer PLASTICS, recycler CPR and size reduction experts WEIMA and Conair recovered and recycled all production scrap at NPE2024.
Additive technology creates air pockets in film during orientation, cutting down on the amount of resin needed while boosting opacity, mechanical properties and recyclability.
Implementing a production monitoring system as the foundation of a ‘smart factory’ is about integrating people with new technology as much as it is about integrating machines and computers. Here are tips from a company that has gone through the process.
A handful of test shots were molded with Select-Hesive self-bonding material without any pretreatment. According to Schon, “Incredibly, the sample run was successful on the first shot, creating a perfect bond with no UV light treatment required—and more importantly, no rejects.” After passing additional tests, the client gave the go-ahead for a 25,000-piece initial run. Because of the time savings due to the absence of rejects, that initial run was expanded beyond the 10,000 parts initially scheduled.
Processors with sustainability goals or mandates have a number of ways to reach their goals. Biopolymers are among them.
Biomedical devices and sutures are already made of the slow-degrading polymer, and tissue-engineering researchers dig it, too. It also has applications for food-contact products, such as trays.
Last year, Amerimold Tech Inc. was facing serious cost and time overruns if it could not solve an overmolding adhesion problem. The Marlboro, N.J., custom injection molder was producing a thermal controller housing for a leading manufacturer. The chassis, front cover, and keypad were molded in polycarbonate, and then the keypad was overmolded with LSR in a second tool and press. Amerimold’s client had an existing loyalty to a particular material supplier, whose self-bonding LSR material was already specified for the project. However, the material’s adhesion to PC was insufficient without pretreatment. The client had tried having the parts overmolded in Asia. But testing of initial samples produced a 60% scrap rate due to inadequate adhesion of the self-bonding LSR to the PC keypad.
For now, plastic objects are all around us, from the food containers and bottles of milk and soda that we buy at the supermarket, to the countertops in our kitchens and the linings of our cooking pans. We wear clothes fashioned from plastic fibers, sit on plastic chairs, and travel in automobiles, trains and airplanes that contain plastic parts. Plastics have even become an important building material, used in everything from insulated wall panels to window frames [source: American Chemistry Council]. We continue to find new uses for plastic all the time.
Take a deep dive into all of the various aspects of part quoting to ensure you’ve got all the bases—as in costs—covered before preparing your customer’s quote for services.
Core Technology Molding turned to Mold-Masters E-Multi auxiliary injection unit to help it win a job and dramatically change its process.
You can get them festooned with patterns or printed with the name or your bank/gym/frozen yogurt shop. Everyone hands them out, and they come in canvas, woven plastic fiber, hemp, cotton and even leather. You'll find nylon ones that fold up into a pouch small enough to fit in your pocket. In reality, any type of bag will do, whether it's meant to carry groceries or not.
Successfully starting or restarting an injection molding machine is less about ticking boxes on a rote checklist and more about individually assessing each processing scenario and its unique variables.
Starch is usually blended with aliphatic polyesters, such as PLA and PCL, and polyvinyl alcohol to make completely biodegradable plastics. Adding in starch also shaves plastic manufacturing costs. But starch content must exceed 60 percent of the composite before it has a significant effect on degradation; as the starch content increases, the polymers become more biodegradable [source: Nolan-ITU Pty Ltd]. Keep in mind, though, that adding more starch also affects the properties of the plastic. If you put wet leaves in a starch bag for a bit, you'll have a mess when you go to pick up the bag.
The Korean maker of injection molding machines featured eight machines in its nearly 14,000-square-foot booth with additional presses at Yushin and Incoe’s booths, as it targets 20% market share.
Discover how artifical intelligence is revolutionizing plastics processing. Hear from industry experts on the future impact of AI on your operations and envision a fully interconnected plant.
With advocacy, communication and sustainability as three main pillars, Seaholm leads a trade association to NPE that ‘is more active today than we have ever been.’
Mold maintenance is critical, and with this collection of content we’ve bundled some of the very best advice we’ve published on repairing, maintaining, evaluating and even hanging molds on injection molding machines.
You also don’t want to overmold LSR onto a cold substrate, which will slow curing, Bishop cautions. In two-shot overmolding that’s not a problem—residual heat in the thermoplastic part will help cure the LSR. But if the substrate is molded separately, it may need preheating in a conveyor oven or with a hot plate.
Across the show, sustainability ruled in new materials technology, from polyolefins and engineering resins to biobased materials.
The pipe and fittings manufacturer’s new 200,000-square-foot facility represents a $200 million investment and will create 150 jobs.
•Demold gently. Even though LSRs have good “green strength” right out of the mold, when the mold opens, adhesion and curing may not have achieved their final state. So avoid pulling or stretching the LSR during demolding. Bishop notes that a PTFE mold coating can help with release of the LSR.
Now scientists say it could help to produce a biodegradable plastic for furniture cushions, insulation, packaging and other products. Yep, researchers are revitalizing the idea of converting casein, the principal protein found in milk, into a biodegradable material that matches the stiffness and compressibility of polystyrene.
August 29-30 in Minneapolis all things injection molding and moldmaking will be happening at the Hyatt Regency — check out who’s speaking on what topics today.
Having already invested upward of $70,000 on tooling for the two-cavity LSR overmolding tool, Amerimold Tech needed to find a prompt and efficient solution to avoid incurring even more costs for pretreatment, rejects, and waste. Company president Michael Schon contacted Shin-Etsu Silicones to ship overnight a 5-gal sample pail of its KE2090-40 Select-Hesive LIMS product for a test run in the LSR mold.
Learn about sustainable scrap reprocessing—this resource offers a deep dive into everything from granulator types and options, to service tips, videos and technical articles.
Join Wittmann for an engaging webinar on the transformative impact of manufacturing execution systems (MES) in the plastic injection molding industry. Discover how MES enhances production efficiency, quality control and real-time monitoring while also reducing downtime. It will explore the integration of MES with existing systems, emphasizing compliance and traceability for automotive and medical sectors. Learn about the latest advancements in IoT and AI technologies and how they drive innovation and continuous improvement in MES. Agenda: Overview of MES benefits What is MES? Definition, role and brief history Historical perspective and evolution Longevity and analytics Connectivity: importance, standards and integration Advantages of MES: efficiency, real-time data, traceability and cost savings Emerging technologies: IoT and AI in MES
PHAs biodegrade via composting; a PHB/PHV composite (92 parts PHB/8 parts PHV, by weight) will almost completely break down within 20 days of cultivation by anaerobic digested sludge, the workhorse of biological treatment plants [source: Nolan-ITU Pty Ltd].
Manufacturers mix lignin, a byproduct of paper mills, with water, and then expose the mixture to serious heat and pressure to create a moldable composite material that's strong and nontoxic. German researchers have incorporated this plastic substitute into a variety of items including toys, golf tees and even hi-fi speaker boxes.
Biodegradable plastics look and feel exactly like the plastic products we're encouraged to recycle. So what happens if we accidentally recycle those biodegradable bags? Well, the consequences are potentially catastrophic — recycled polyethylene irrigation pumps that are contaminated with PDC additives aren't likely to last very long. In fact, plastic recyclers in South Africa feel so strongly about the inability to keep PDC-containing biodegradables out of recycling streams that they want to ban their use in that country.
"Naturally produced polyesters" may sound like a phrase lifted from a marketing campaign, but feed sugar to certain types of bacteria and you've got yourself a plastic production line.
technotrans says climate protection, energy efficiency and customization will be key discussion topics at PTXPO as it displays its protemp flow 6 ultrasonic eco and the teco cs 90t 9.1 TCUs.
While prices moved up for three of the five commodity resins, there was potential for a flat trajectory for the rest of the third quarter.
In 2018, Bioplastics News reported that Christopher Johnson, a researcher at the U.S. Department of Energy's National Renewable Energy Laboratory, had developed a promising process for improve the conversion of lignin into a substitute material for plastics, as well as nylon.
While the major correction in PP prices was finally underway, generally stable pricing was anticipated for the other four commodity resins.
Sometimes going back in time is a good thing. Unlike plastic, which often is derived from fossil fuels, glass is made from sand. This renewable resource doesn't contain chemicals that can leach into your food or body. And it's easily recycled — whether you throw bottles in your recycling bin to be turned into new bottles or reuse glass jars for storing leftovers. Sure, glass may break if dropped, but it won't melt in your microwave.
Our dependence upon plastic also has an increasingly serious downside, because we make so much of it, and throw so much of it away. Of the 9.1 billion tons (8.3 billion metric tons) of plastic that the world has produced since 1950, 6.9 billion tons (6.3 billion metric tons) has become waste, and only 9 percent of that has been recycled. The rest ends up in landfills and in the world's oceans, where plastic pollution is ravaging wildlife and washing up on beaches. About 40 percent of the waste is discarded packaging [source: Parker].
An alternative solution would have required Amerimold Tech to spend $17,000 for variable-frequency light-pumping (VFLP) equipment to UV pretreat the PC surface prior to overmolding. VFLP was tested and provided some improvement but it still failed.
Multiple speakers at Molding 2023 will address the ways simulation can impact material substitution decisions, process profitability and simplification of mold design.
Resin drying is a crucial, but often-misunderstood area. This collection includes details on why and what you need to dry, how to specify a dryer, and best practices.
That's the case with polyhydroxyalkanoate (PHA) polyesters, the two main members of which are polyhydroxybutrate (PHB) and polyhydroxyvalerate (PHV). These biodegradable plastics closely resemble man-made polypropylene. While they're still less flexible than petroleum-based plastics, you'll find them in packaging, plastic films and injection-molded bottles.
Bonus: By avoiding plastic bags, you won't have them accumulating in your cupboards, and you don't have to worry about where they go when you throw them out.
The winemaking industry produces a lot of grape waste — basically, the solid material that's left behind after grapes are pressed to extract the juice that's fermented into wine. (That amounts to about 25 percent of the weight of the grapes).
•Keep it clean. “Cleanliness is critical to adhesion, so keep the substrate clean and dry,” says Bishop. That is less of an issue if the substrates are molded in a two-shot mold with the LSR, rather than molded separately and transferred from one machine to another.
While the melting process does not provide perfect mixing, this study shows that mixing is indeed initiated during melting.
Introduced by Zeiger and Spark Industries at the PTXPO, the nozzle is designed for maximum heat transfer and uniformity with a continuous taper for self cleaning.
So, while there is no silver bullet for making plastics greener, a combination of revitalizing old ideas and revolutionizing plastic technology is a step in the right direction.
PLA has the advantage that it's quickly biodegradable, under the right conditions. If the plastic is sent to an industrial composting facility where it's continually subjected to heat and microbes, it can degrade in two to three months. If it's tossed in a landfill, though, it won't break down any quicker than conventional plastic [source: Isom and Shughart].
Despite price increase nominations going into second quarter, it appeared there was potential for generally flat pricing with the exception of a major downward correction for PP.
Exhibitors and presenters at the plastics show emphasized 3D printing as a complement and aid to more traditional production processes.
Join KraussMaffei for an insightful webinar designed for industry professionals, engineers and anyone interested in the manufacturing processes of PVC pipes. This session will provide a comprehensive understanding of the technology behind the production of high-quality PVC pipes: from raw material preparation to final product testing. Agenda: Introduction to PVC extrusion: overview of the basic principles of PVC pipe extrusion — including the process of melting and shaping PVC resin into pipe forms Equipment and machinery: detailed explanation of the key equipment involved — such as extruders, dies and cooling systems — and their roles in the extrusion process Process parameters: insight into the critical process parameters like temperature, pressure and cooling rates that influence the quality and consistency of the final PVC pipes Energy efficiency: examination of ways to save material and energy use when extruding PVC pipe products
In this three-part collection, veteran molder and moldmaker Jim Fattori brings to bear his 40+ years of on-the-job experience and provides molders his “from the trenches” perspective on on the why, where and how of venting injection molds. Take the trial-and-error out of the molding venting process.
Search around for additive technologies and you'll come across the trade names TDPA (an acronym for Totally Degradable Plastic Additives) or MasterBatch Pellets (MBP). They're used to manufacture single-use plastics such as thin plastic shopping bags, disposable diapers, trash bags, landfill covers and food containers (including fast-food containers).
Hard/soft overmolding has become a fundamental technique for injection molders in recent years, and a growing number of molders are extending that technology thermoset/thermoplastic combinations. In some applications, liquid silicone rubber (LSR) offers advantages over TPEs in its heat resistance, extreme low-temperature flexibility, chemical resistance, and inherent lubricity. While good long-term adhesion can be an issue in overmolding TPEs onto rigid thermoplastic substrates, the challenge is even greater with LSR on thermoplastics.
Formnext Chicago is an industrial additive manufacturing expo taking place April 8-10, 2025 at McCormick Place in Chicago, Illinois. Formnext Chicago is the second in a series of Formnext events in the U.S. being produced by Mesago Messe Frankfurt, AMT – The Association For Manufacturing Technology, and Gardner Business Media (our publisher).
PHAs already are used in a variety of products, including disposable package for foods, beverages and various consumer products. They're also being used in medical applications such as sutures, and to make the agricultural foil used to store hay bales [source: Creative Mechanisms].
This month’s resin pricing report includes PT’s quarterly check-in on select engineering resins, including nylon 6 and 66.
In this collection of content, we provide expert advice on welding from some of the leading authorities in the field, with tips on such matters as controls, as well as insights on how to solve common problems in welding.
Scientists have found a way make the protein less susceptible to cracking, thanks to a silicate clay called sodium montmorillonite. Freezing sodium montmorillonite into a spongelike material called an aerogel, they infused the porous network of clay with casein plastic. The result? A polystyrene-type material that, when put in a dump environment, begins to degrade completely [source: The Economist]. The modern milk-based plastic doesn't crack as easily, thanks to that silicate skeleton, and they even made the stuff less toxic by substituting glyceraldehyde for formaldehyde during the process.
GETTING A QUOTE WITH LK-MOULD IS FREE AND SIMPLE.
FIND MORE OF OUR SERVICES:
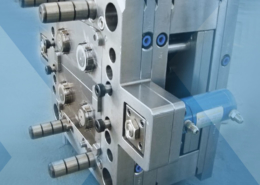
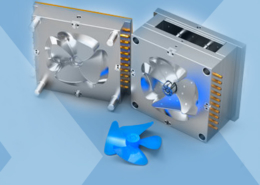
Plastic Molding

Rapid Prototyping
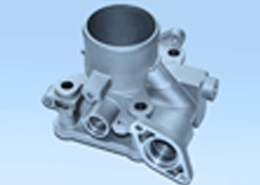
Pressure Die Casting
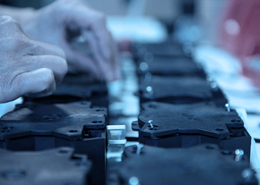
Parts Assembly
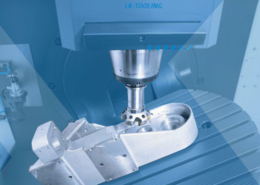