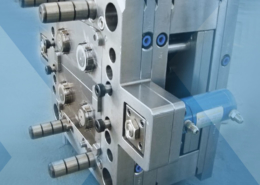
Two-Shot Molding: The Advantages, Considerations and Real-World Applications - i
Author:gly Date: 2024-09-30
MGS Mfg Group, headquartered in Germantown, WI, has been operating in Mexico for six years. MGS Plastics Chihuahua S.A. de C.V. has benefitted from the exploding growth of automotive OEMs in that region, expanding several times since MGS bought an existing, 20-press molding operation in 2008, adding to the overall square footage and increasing the number and range of the injection molding machines. Within the first two years, MGS added two 770-
ton presses, and today MGS Plastics Chihuahua has a total of 48 presses ranging from 50 to 770 tons. MGS Plastics Chihuahua also integrated the company's Universal Multishot Systems portable injection units and rotary platens to enable two-component molding. The company has since added continuous extrusion shuttle blowmolding capabilities. Today, MGS Plastics Chihuahua operates three 40,000-sq-ft production facilities and a 50,000-sq-ft warehouse with offices that total 135,000 sq-ft.
Global Precious Metals E-Waste Recovery Market Size, Share, and COVID-19 Impact Analysis, By Metal (Gold, Silver, and Others), By Source (Household Appliances, IT & Telecommunication, Consumer Electronics, and Others), and By Region (North America, Europe, Asia-Pacific, Latin America, Middle East, and Africa), Analysis and Forecast 2023 – 2033
MGS Plastics Chihuahua has obtained numerous certifications that include ISO 9001:2008, ISO/TS 16949- 2009 and ISO 14001:2004. Other investments include installation of new manufacturing systems and equipment, and personnel training, all of which has paid off in existing-customer retention and significant growth in new customer acquisitions.
As Mexico's automotive and aerospace industries continue to see rapid growth, suppliers are encouraged to locate plants near these OEM and Tier 1 facilities to help reduce cost and time. Many OEMs have been manufacturing in Mexico for decades, bringing in parts and components from suppliers in the United States and Canada. That is primarily because there has been a reluctance on the part of smaller, Tier 2 suppliers, such as molders and moldmakers, to site manufacturing plants in Mexico. But those who have gone there are seeing their growth pace in line with their customers.
Browse key industry insights spread across 240 pages with 110 Market data tables and figures & charts from the report on the "Global Medical Injection Molding Market Size, Share, and COVID-19 Impact Analysis, By Product (Medical Equipment Components, Consumables, Patient Aids, Orthopedics Instruments, Dental Products, and Others), By System (Hot Runner, Cold Runner), By Material (Plastics, Metals, and Others), and By Region (North America, Europe, Asia-Pacific, Latin America, Middle East, and Africa), Analysis and Forecast 2023 – 2033."
Global Carpet Tape Market Size, Share, and COVID-19 Impact Analysis, By Adhesive Type (Rubber-based Carpet Tape and Acrylic-based Carpet Tape), By Application (Carpet Installation, Rug Binding, Temporary Floor Covering, and Others), By End-Users (Residential and Commercial), and By Region (North America, Europe, Asia-Pacific, Latin America, Middle East, and Africa), Analysis and Forecast 2023 – 2033
GW Plastics has been in business 
since 1955. Headquartered in Bethel, VT, the company made the move to put molding in Queretaro, Mexico 
in 2006, a site that was strategically located to serve its customers throughout Mexico, according to Justino Barrientos, Mexico sales manager for GW. "Following our customers and expanding our footprint in Queretaro meant greater opportunities for us as a supplier," Barrientos said. "The cities on the border were our first targets, but it was not as centrally located, so we went to central Mexico instead. It's strategically located and allows us to reach most 
of the primary automotive facilities within three hours. For JIT automotive programs, it's ideal. Being close to our customers is key."
Supply chain concerns, JIT deliveries for critical components, and local problem solving is driving vehicle manufacturers to want their suppliers close-even building "supplier parks" to make relocation easy for smaller Tier 2 companies. Long-distance shipping can be fraught with problems.
According to Marcel Alvarez, director of sales for Mexico, when MGS acquired the facility in 2008, the customer base was primarily electronics, industrial, and appliance OEMs, with very little automotive. "In less than six years, revenues have increased from an average of $500,000 per month to the current $2.5 million per month, with the automotive industry responsible for approximately 40% of those sales," Alvarez told PlasticsToday. "Automotive is the fastest growing industry of our interests in Mexico." Sales for fiscal 2013 totaled $26.9 million.
The hot runner segment dominated the market with the largest market share of the medical injection molding market during the projected timeframe. Based on the system, the medical injection molding market is divided into hot runner and cold runner. Among these, the hot runner segment dominated the market with the largest market share of the medical injection molding market during the projected timeframe. Hot runner systems are becoming increasingly essential due to their many advantages, including reduced pressure and a shorter cycle time. As the molten mixture must be forced into the mold cavity, waste can be eliminated because runners are not needed, larger parts can be produced at a higher volume, and part consistency and quality are all enhanced.
As Mexico's automotive and aerospace industries continue to see rapid growth, suppliers are encouraged to locate plants near these OEM and Tier 1 facilities to help reduce cost and time. Many OEMs have been manufacturing in Mexico for decades, bringing in parts and components 
from suppliers in the United States and Canada. That is primarily because there has been a reluctance on the part of smaller, Tier 2 suppliers, such as molders and moldmakers, to site manufacturing plants in Mexico. But those who have gone there are seeing their growth pace in line with their customers.
MGS's Alvarez agrees. "The delivery expectations and quality standards of the auto industry are high, so it is imperative that the production team is well trained and supported," he said. "Our Chihuahua team has responded successfully. On April 8 of 2014, the employees of MGS Chihuahua received the Delphi Automotive 2013 Pinnacle Award for Supplier Excellence. Delphi is a long-time MGS customer, going back well before the Mexico acquisition. Their production management and quality teams worked very closely with ours to develop the systems and procedures needed by Delphi."
GW's Barientos sees close proximity to the automotive companies as
 one more advantage over some of the European Tier 1 or Tier 2 suppliers. "The automotive companies have very challenging [delivery] targets, and moving parts from Europe means they bring all these parts in by ship and rail every day," Barrientos explained. "If something goes wrong or if a shipment needs to be replaced, then you are talking about air-freighting parts," he says. Everyone strives for perfection, Barrientos adds, "but sometimes that is
 not the case, so it's ideal to be close to the customer so that if something goes wrong, we can ship parts in a few hours by truck."
While Mexico may be considered
 a low-cost location, suppliers like GW have to have high-tech, state-of-the-
art plants to meet the requirements of today's automotive OEMs. The 51,500 sq-ft plant is ISO 14001 and ISO/TS 16949 certified. Today, with 20 injection molding presses ranging from 50 to 650 tons, GW Queretaro serves some 
of the major global automotive Tier 1 suppliers that deliver final assemblies to OEMs including Honda, BMW, Audi, GM, Ford, Chrysler, VW, and more. "All these OEMs are expanding and opening new operations, and the Tier 1 suppliers are following them. We work with the Tier 1 [suppliers] to accommodate this increased business," said Barrientos. "We are growing organically and taking advantage of the location-investing in additional capacity to face these challenges."
Asia Pacific is expected to hold the largest share of the medical injection molding market over the forecast period.Asia Pacific is expected to hold the largest share of the medical injection molding market over the forecast period. The region's expanding population and rising healthcare demands are driving the need for cutting-edge medical devices and components, which is promoting the use of injection molding technology. The growing prevalence of chronic illnesses combined with the healthcare industry's requirement for accurate and cost-effective manufacturing procedures is fueling the market's growth. Additionally, the availability of skilled labor and advancements in injection molding technologies in countries like China and India have contributed to the region's status as the center for the manufacture of medical devices.
North America is predicted to grow at the fastest pace in the medical injection molding market during the projected timeframe. There is a well-established healthcare infrastructure and an enormous demand for medical devices and equipment. Furthermore, the growing prevalence of chronic illnesses and an aging population are driving the growth of the medical injection molding market in this area. One of the key factors affecting the North American sector is the rising per capita healthcare spending in the US on health insurance. This is expected to contribute to an increase in the demand for generic medications and medical supplies.
As a testament to just how fast the automotive manufacturing industry
 has expanded in Mexico, in the last two years, MGS has been visited by automotive companies from Germany, Italy, Japan, Australia, South America, and the United States as they prepare for new platforms for their respective vehicle OEMs. "Several key prospective customers are currently discussing production opportunities for our facility," stated Alvarez. "MGS is also developing strategic alliances within our automotive customer base, and I can only see this trend increasing, as new announcements are made of new assembly plants moving into Mexico."
The medical equipment components segment is expected to grow at the highest CAGR growth of the medical injection molding market during the projected timeframe. Based on the product, the medical injection molding market is divided into medical equipment components, consumables, patient aids, orthopedics instruments, dental products, and others. Among these, the medical equipment components segment is expected to grow at the highest CAGR growth of the medical injection molding market during the projected timeframe. The medical equipment manufacturing business is experiencing a growing demand for medical injection molding due to several significant factors. Recently, complicated medical devices have grown increasingly essential as the healthcare industry develops, and injection molding offers a highly accurate and efficient manufacturing method for fulfilling these needs.
As Mexico's automotive and aerospace industries continue to see rapid growth, suppliers are encouraged to locate plants near these OEM and Tier 1 facilities to help reduce cost and time. Many OEMs have been manufacturing in Mexico for decades, bringing in parts and components from suppliers in the United States and Canada. That is primarily because there has been a reluctance on the part of smaller, Tier 2 suppliers, such as molders and moldmakers, to site manufacturing plants in Mexico. But those who have gone there are seeing their growth pace in line with their customers.
Because of the tremendous growth of the automotive industry in Mexico - both among OEMs and Tier 1 suppliers - GW and MGS sited their respective plants in strategic locations.
Barrientos commented that GW Queretaro is "at the top of the supplier pyramid" for its technical capabilities, which include the ability to mold complex, tight-tolerance, functional parts and to provide overmolding and a variety of secondary operations, specifically assembly. "We're looking forward to expanding our assembly capabilities to grow our business scope," added Barrientos. "The types of parts we supply include automotive electronics, electrical drives, panel systems, and other tight-tolerance components. We have many years of experience in manufacturing these parts."
Global PFAS Filtration Market Size, Share, and COVID-19 Impact Analysis, By Technology (Reverse Osmosis, Ion Exchange Resins, Granular Activated Carbon Filters, and Others), By End-User (Commercial, Industrial, Municipal, and Others), and By Region (North America, Europe, Asia-Pacific, Latin America, Middle East, and Africa), Analysis and Forecast 2023 – 2033
Spherical Insights & Consulting is a market research and consulting firm which provides actionable market research study, quantitative forecasting and trends analysis provides forward-looking insight especially designed for decision makers and aids ROI.
Market SegmentThis study forecasts revenue at global, regional, and country levels from 2020 to 2033. Spherical Insights has segmented the medical injection molding market based on the below-mentioned segments:
A device that uses the injection molding process to make plastic products is called an injection molding machine, additionally referred to as an injection press. The primary components are the clamping unit and the injection unit. During the injection molding manufacturing process, molten material is injected into a mold to form a product. Although a wide variety of materials can be injected, the most common ones are elastomers, glass, confections, metals (die casting is the process utilized for this), thermoplastic, and thermoset polymers. One of the primary factors driving the market for medical injection molding machines is material selection. Wearable technology and prosthetic surfaces help with the usage of polyethylene due to its high molecular weight, robustness, attractiveness, and relative smoothness. Furthermore, the high initial tooling and machinery costs related to medical injection molding machines may prevent the organization from expanding. Developing a plastic injection facility requires substantial initial expenses, which can keep small and medium-sized companies from entering the market.
Until she retired in September 2021, Clare Goldsberry reported on the plastics industry for more than 30 years. In addition to the 10,000+ articles she has written, by her own estimation, she is the author of several books, including The Business of Injection Molding: How to succeed as a custom molder and Purchasing Injection Molds: A buyers guide. Goldsberry is a member of the Plastics Pioneers Association. She reflected on her long career in "Time to Say Good-Bye."
The plastics segment is anticipated to hold the largest market share of the medical injection molding market during the projected timeframe. Based on the material, the medical injection molding market is divided into plastics, metals, and others. Among these, the plastics segment is anticipated to hold the largest market share of the medical injection molding market during the projected timeframe. Plastic injection molding is currently used to build complex designs for medical devices. Plastic medical injection molding is an essential component of the healthcare industry due to its unparalleled precision, versatility, and affordability in producing a broad range of medical devices and components.
Global Sustainable Aluminum Market Size, Share, and COVID-19 Impact Analysis, By Product (Sheet, Plate, Cast Products, Extrusion, and Others), By Processing Method (Rolling, Extruding, Casting, Forging, Drawn, and Others), By End-Use (Construction, Transportation (Aerospace, Automotive, and Marine), Packaging (Food & Beverages, Cosmetics, and Others), Electrical, Consumer Durables, Machinery & Equipment, and Others), and By Region (North America, Europe, Asia-Pacific, Latin America, Middle East, and Africa), Analysis and Forecast 2023 - 2033
The report offers the appropriate analysis of the key organizations/companies involved within the global market along with a comparative evaluation primarily based on their product offering, business overviews, geographic presence, enterprise strategies, segment market share, and SWOT analysis. The report also provides an elaborative analysis focusing on the current news and developments of the companies, which includes product development, innovations, joint ventures, partnerships, mergers & acquisitions, strategic alliances, and others. This allows for the evaluation of the overall competition within the market. Major vendors in the medical injection molding market include the Rodon Group, Currier Plastics, Inc., D&M Plastics, LLC, Molded Rubber & Plastic Corporation, Metro Mold & Design, ARBURG GmbH, BOLE Machinery, Biomerics, Rutland Plastic, Sumitomo Chemical Co., Ltd., Evco Plastics, C&J Industries, Hillenbrand Inc., Tessy Plastics., and Others.
Which is catering to different industry such as financial sectors, industrial sectors, government organizations, universities, non-profits and corporations. The company's mission is to work with businesses to achieve business objectives and maintain strategic improvements.
New York, United States , July 10, 2024 (GLOBE NEWSWIRE) -- The Global Medical Injection Molding Market Size is to Grow from USD 21.54 Billion in 2023 to USD 36.43 Billion by 2033, at a Compound Annual Growth Rate (CAGR) of 5.40% during the projected period.
GETTING A QUOTE WITH LK-MOULD IS FREE AND SIMPLE.
FIND MORE OF OUR SERVICES:
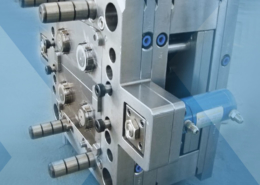
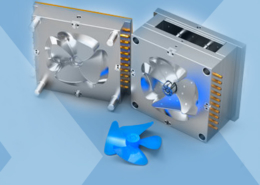
Plastic Molding

Rapid Prototyping
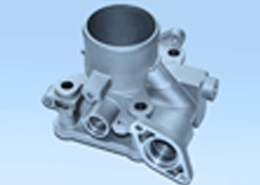
Pressure Die Casting
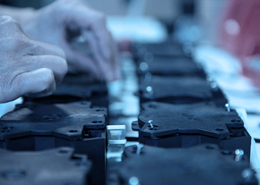
Parts Assembly
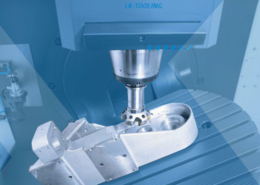