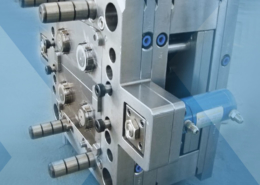
Top 10 Additive Manufacturing And 3D Printing Stock to Watch (September
Author:gly Date: 2024-09-30
Sabic fully supports its new PP compound portfolio with extensive expertise in foamed part design, development, and processing, as well as predictive engineering. For instance, the company can provide guidance on the selection of the appropriate chemical blowing agent for each grade. Sabic’s technical team will collaborate with customers to achieve desired aesthetics at the lowest possible part weight.
While almost all respondents described the expected benefits of 3D printing, the most frequent benefit discussed was faster part delivery timelines.
Prototyping remains the primary application of 3D printing, according to a survey of decision makers who oversee 3D printing within their organizations.
Issues with the cost and availability of materials are extremely prevalent, noted by 85% of decision makers, increasing 31% from 2021.
74% of survey participants printed at least 10,000 parts last year, while 36% polled printed up to 100,000 parts in that same timeframe.
Prototyping is also widely recognized as the area most benefited by additive manufacturing (selected by 96% of respondents), followed by design (52%) and small-scale production (27%).
Almost all respondents (96%) said their organization would want to use metal additive materials if certified versions were available at a reasonable cost, followed closely by plastics/polymers (88%).
Finished inner tailgate trim part made with Sabic PPc F9005 grade through foam injection molding. The molded part features fixations, ribs, honeycomb, doghouse, domes, holes, textures, and excellent aesthetics. Sabic’s PP compound has high flow, can decrease sink marks, and reduces weight by up to 30%.
Another consideration is the foaming process, which can use chemical or physical agents. The new Sabic PP compounds are good candidates for use with chemical blowing agents, which are typically preferred for visible foamed parts. These agents are introduced to the molding machine in the form of a masterbatch, along with the plastic pellets, and activated during the melt phase to release gases for foaming.
Unlike standard FIM materials, which typically exhibit surface defects, the new advanced PP compounds feature uniformly high surface quality similar to solid injection molded parts. Compared with solid components, foamed parts made with Sabic PP compounds offer significant weight savings that can help cut emissions. According to a cradle-to-grave life-cycle assessment study (pending third-party review), the advanced materials can help OEMs lower carbon dioxide (CO2) emissions by as much as 15%.
Sabic has introduced a specialized portfolio of Sabic PP compounds for foam injection molding (FIM). New mineral-reinforced Sabic PPc F9005, PPc F9007, and PPc F9015 grades can help deliver attractive aesthetics for visible automotive interior parts with complex geometries, such as door panels and trim, seat and trunk cladding, A/B/C/D pillar covers, and center consoles.
While participants aren’t as bullish on overall 3D printing industry growth, they are expecting larger growth in the use of 3D printing for production parts or goods in the next three to five years.
Core-back molding, which requires part redesign and new tooling, can lower weight by as much as 30%. Both Sabic PPc 9005 and PPc 9015 grades are formulated for core-back molding and deliver medium stiffness and impact.
Previously, the FIM process was essentially limited to non-visible parts, restricting its usefulness in automotive applications. Foaming can underperform in surface aesthetics — silver streaking, swirl lines and dimples are common defects. Sabic PP compounds for foamed interior parts deliver low-gloss textured (grained) surfaces with uniformly high quality and eliminate streaking and swirling. Talc filler in these grades acts as a nucleator that promotes the generation of finer bubbles, which contribute to a consistent surface appearance. For enhanced aesthetics, these grades are currently available in selected automotive interior colors. Custom coloring is also available.
To drive future developments in polymer foams, Sabic operates a Foam Innovation Center in the Netherlands. This center, which is equipped with foam process capabilities as well as analytical equipment, enables the company to develop new foam solutions and technology innovations and collaborate with customers.
More than half of those surveyed (55%) say that their company’s top leadership recognizes additive manufacturing as a strategic capability.
The choice between the short-shot and core-back techniques, with their different tooling requirements, also helps to determine whether FIM with Sabic PP compounds is cost neutral or delivers cost savings. Additional cost savings are possible through cycle time reductions from flow improvements inherent in FIM.
96% of participants use in-house 3D printing, but outsourcing is still typical, especially with additive networks and contract manufacturers.
Prototyping remains the predominant use of additive manufacturing, according to a survey of 200 mid- to senior-level decision makers who oversee additive manufacturing within their organizations. While the survey commissioned by design engineering, manufacturing, and supply chain services company Jabil revealed that a majority of respondents continue to use the technology for prototyping purposes, it also showed consistent growth since 2017 in the use of 3D printing for production parts, bridge production, and jigs, fixtures, and tooling.
Stephen has been with PlasticsToday and its preceding publications Modern Plastics and Injection Molding since 1992, throughout this time based in the Asia Pacific region, including stints in Japan, Australia, and his current location Singapore. His current beat focuses on automotive. Stephen is an avid folding bicycle rider, often taking his bike on overseas business trips, and is a proud dachshund owner.
Seven in 10 decision makers expect moderate growth of 3D printing for their company in the next two to five years; this contrasts with “significant” growth reported in previous surveys.
Short-shot molding, which uses the same tooling as an injection molded part, can reduce weight by up to 10%. Sabic PPc 9007 is formulated for short-shot FIM and low-impact applications.
“The automotive industry continues to look for new weight-out strategies that can advance energy efficiency and sustainability goals,” said Sabic’s Abdullah Al-Otaibi, General Manager, ETP & Market Solutions. “Although foam injection molding produces desirable lightweight parts, manufacturers have been forced to sacrifice aesthetics . . . until now. We applied our extensive expertise in foaming technology to develop these new compounds to help resolve the issue of surface quality and open new application opportunities for foamed parts.”
GETTING A QUOTE WITH LK-MOULD IS FREE AND SIMPLE.
FIND MORE OF OUR SERVICES:
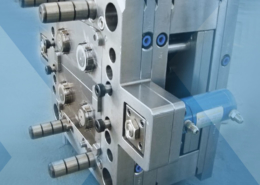
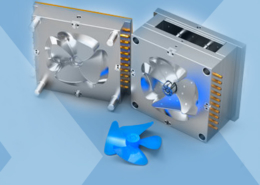
Plastic Molding

Rapid Prototyping
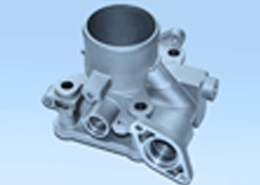
Pressure Die Casting
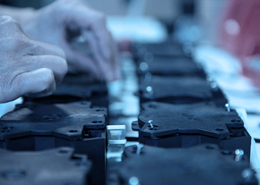
Parts Assembly
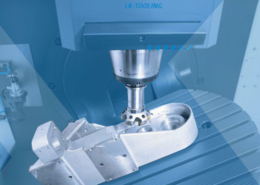